IAEI has had various requests recently to provide some basic information about the grounding of electric signs and neon lighting installations and to include the bonding requirements. To that end, this article will provide a brief tour through the electrical sign circuit and focus primarily on what is required for adequate grounding of this equipment and how grounding and bonding function together to provide safety for these types of equipment and installations.
It is fairly common knowledge to those in the electrical field that grounding and bonding of electrical equipment is essential for electrical safety as well as a Code requirement. Chapter six of the NEC provides minimum requirements for special equipment. The first article in this chapter is 600, Electric Signs and Outline Lighting, which contains specific rules for this type of equipment that, in some cases, modify or amend the basic requirements set forth in chapters one through four. Otherwise, the basic rules in one through four apply to this equipment, as do the specific requirements of Article 600.
Basic Principles of Grounding and Bonding
Figure 1. Basic concepts of grounding and bonding
To fully understand and apply the related rules, one must grasp an understanding of the two concepts grounding and bonding. Grounding and bonding do not have to be as mysterious or complicated as many make them out to be. Let’s review each of these basic concepts before we look at the Code rules and how they apply to this special equipment. When the word grounding or ground is used one should think of something that is connected to the earth or ground. The word grounded is defined by the Code as “Connected to earth or some conducting body that serves in place of the earth” [NEC Article 100]. The words bonding (bonded) are defined as “The permanent joining of metallic parts to form an electrically conductive path that ensures electrical continuity and the capacity to conduct safely any current likely to be imposed.” So basically bonded means metal parts connected together and grounded means connected to the earth (see figure 1). Both concepts are essential elements and fundamentally important for electrical safety in electric signs and neon installations.
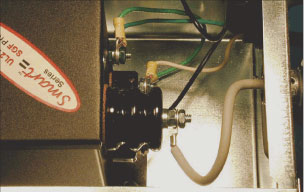
Photo 2. Equipment grounding conductor connected to neon transformer and enclosure
Section 600.7 contains the general requirement for grounding of electric signs and metal equipment of outline lighting systems and indicates generally that metal parts of signs and outline lighting systems must be grounded. The general rules for grounding and bonding are also provided in Article 250. When applying the Code it is generally understood that the rules in chapters 5, 6, and 7 supplement or modify the general rules [NEC 90.3]. So when applying the Code to these installations, if the general rules are not modified in any way by Article 600, then grounding and bonding requirements in Article 250 would apply.
Equipment (electric sign and equipment) Grounding
Figure 2. Equipment grounding conductor connected to the electric sign
The equipment grounding conductor and proper bonding are essential elements for safety in electrical signs and neon installations. Let’s take a closer look at how each of these elements must be applied to electric signs or neon lighting installations. The branch circuit supplying the equipment provides the required equipment grounding conductor for accomplishing the grounding(the connection to the earth). The acceptable equipment grounding conductors are specified in 250.118 and the method of connection to the sign or metal enclosure is provided in 250.120(A) and 250.8. The equipment grounding conductor must be connected to the equipment using methods consistent with 250.8, which excludes the use of sheet metal screws.
Photo 3. Metallic parts shown effectively bonded together
Minimum size of the equipment grounding conductor with the branch circuit must not be less than the sizes in Table 250.122 based on the branch-circuit breaker or fuse rating. The equipment grounding conductor connects the equipment to ground and works to maintain it at or near earth potential (see figure 2). This safety component of the circuit also acts as the silent servant waiting to perform its ever-important function of facilitating the operation of the branch-circuit overcurrent protection in the event of a ground-fault circuit. (Note that the term ground fault is defined in 250.2). Electrical installations for sign circuits and neon installations are not exempt from these basic grounding requirements, and they must be grounded. It is important to note that 250.134(A) specifies in detail the required connections for the equipment grounding conductor. It must be routed with the branch circuit as indicated in 250.134(B) back to the source of a separately derived system or service grounding point. Structural metal frames of buildings are not permitted as the required equipment grounding conductor as clearly indicated in 250.136 and 600.7(E).
Bonding Requirements
Figure 3. Length of secondary circuit limited to 6 m (20 ft) in metal raceway
Bonding basically means connecting metallic parts together. When bonding metal equipment and parts associated with electric signs and neon lighting systems, the primary objective is to establish the bonding in an acceptable manner and connect the parts to the equipment grounding conductor of the branch circuit supplying the sign or neon system. This accomplishes the bonding and grounding for the equipment or system. Proper grounding and bonding of metal enclosures and associated metal parts ensure that these parts remain at earth potential, and minimize differences of potential between metallic parts.
Photo 4. Metal parts bonded together using equipment suitable for the use
High-voltage secondary circuits (GTO in a wiring method that extends from the transformer to the discharge tubing) for neon installations produce various levels of capacitance that is inherent to these secondary circuits and is unavoidable. Capacitance coupling in the neon or cold cathode secondary circuit can actually raise the potential (voltage) on ungrounded metal equipment and metal parts if not bonded together and connected to ground.
The Code allows for listed flexible metal conduit or listed liquidtight flexible metal conduit to be used as a bonding means in total accumulative lengths not exceeding 30 m (100 ft) on the secondary side of the sign transformer or power supply. These flexible metal conduits are suitable as a bonding means in lengths up to 30 m (100 ft) because the current on the secondary side of a neon transformer is in the milliampere range and the bonding provided through the conduit or bonding conductor here is not to clear an overcurrent device on the primary (supply side) of the neon transformer or power supply. One should keep in mind that there is a length limitation on secondary GTO conductors of 6 m (20 ft) when installed in metallic wiring methods and 15 m (50 ft) when installed in nonmetallic wiring methods. This limitation is required to minimize the capacitance effect in the secondary that impacts both the secondary conductors (GTO cable) and the transformer (see figures 3 and 4), [NEC 600.32(J) (1) and (2)].
Figure 4. Length of secondary circuit limited to 15 m (50 ft) in non-metallic raceway
Bonding of electrical equipment and enclosures simply means that the enclosures will be connected together in an appropriate manner to ensure electrical continuity and the capacity to conduct safely any fault current likely to be imposed on those enclosures.
Remember that normal current will always try to return to its source, which is the transformer or power supply secondary. The same is true for any fault current. Any metal parts or components requiring bonding must be bonded back to the source (transformer/and or combination of transformer and enclosure). When a metal conduit is connected to a metal electrical junction box with a proper conduit connector or proper fittings, the two parts are at the same potential because they are bonded together (see figure 5).
Figure 5. Metal parts properly bonded together
When metallic wiring methods are used for secondary circuits and the type of electrode connection to the neon tubing is through an electrode receptacle, particular attention to bonding must be applied. Electrode receptacles (often referred to in the industry as PK housings) provide gaskets that must be installed particularly in wet locations. The installation instructions of listed parts must be followed [NEC 110.3(B)]. Basically, this means that bonding of metallic parts must be assured around any gaskets that cause isolation between the channel letter of a sign and the metallic conduit connect to the electrode receptacle. This happens all too often in the field. One reason it is important to be thorough in the inspection of secondary circuits of neon signs and outline lighting systems (see figures 6 and 7).
Small associated metal parts not exceeding 50 mm (2 in.) in any dimension, and not likely to become energized (such as the metal mounting means for tubing supports), and spaced at least 19 mm (¾ in.) from the neon tubing are not required to be bonded [NEC 600.7(B)]. Where listed liquidtight nonmetallic conduit is used for installing the secondary high-voltage GTO conductors from the transformer or power supply to the neon tubing and where there are associated metal parts that require bonding, a bonding conductor is required to be installed. This bonding conductor is required to be installed separately and to be remotely spaced from the nonmetallic conduit [see 600.7(C)]. The wiring method referred to here is liquidtight flexible metal conduit or rigid nonmetallic conduit.
Stress in the Secondary Circuit
Figure 6. Electrode receptacle establishing bonding connection to metal channel letter by mechanical connection (flanged electrode receptacles are available for this purpose)
Where listed nonmetallic conduit is used to enclose the secondary wiring of a transformer or power supply and a bonding conductor is required, the bonding conductor shall be installed separate and remote from the nonmetallic conduit Bonding conductors are required to be copper and not smaller than 14 AWG. This spacing requirement is established to reduce stresses that might be imposed on the GTO conductor because the magnetic flux lines would no longer be symmetrical around the conductor.
Installation of a bonding conductor or grounded and bonded electrically conductive parts remote from nonmetallic raceways and enclosures that contain high-voltage secondary GTO cables is important to minimize the effects unbalanced
Figure 7. Electrode receptacle with gaskets installed required separate 14 AWG copper bonding conductor to establish bonding connection to metal channel letter
stress on the high-voltage secondary conductor installed in a nonmagnetic wiring method. Two spacing requirements in the Code are intended to deal with this situation [NEC 600.7(C) and 600.32(A) (4)]. When a conductor is carrying AC current, it generates a magnetic field, which surrounds the conductor as the current flows during normal operation. This electromagnetic field produces electromagnetic lines of force.
When the conductor is installed in a metal wiring method, these electro-magnetic lines of force will work to compress into the metal wiring method encircling the secondary conductor because the metal conduit introduces less resistance to the magnetic lines of force than air. Even though the magnetic lines of force (flux) are more concentrated, they are maintained in a more symmetrical fashion around the
Photo 6. Electrode receptacles (flanged and standard types shown)
conductor. This keeps the stress on the conductor more uniform or equal for the most part all around the GTO conductor.
When a current-carrying conductor is installed in a nonmetallic wiring method, for example liquidtight flexible nonmetallic conduit, and a bonding conductor is required to be installed for bonding metal parts associated with the neon sign or neon installation, the magnetic lines of force (flux) will try to compress into the bonding conductor or grounded metal parts on that side of the conductor and remain expanded on the other sides. As the compressed magnetic field flows in this circuit, the current is flowing with this unbalanced magnetic flux from zero to maximum voltage and back to zero with every cycle of AC current flow. The stresses on the secondary GTO conductor are much greater on one side that the other and will continue this unbalanced stress condition, which can cause degradation of the high-voltage secondary conductor insulation in time. By spacing this bonding
Figure 8. Bonding conductor spacing for circuits operating at 100 Hz or less
conductor at least at the minimum required intervals, the amount of unbalanced stresses imposed on the high-voltage secondary conductors will be significantly reduced.
Sections 600.7(C) and 600.32(A)(4) both require a spacing of 38 mm (1½ in.) to be maintained between grounded metal parts or bonding conductors when the secondary circuit operates at 100 Hz or less. When the secondary circuit operates at over 100 Hz, the spacing requirement increases to 45 mm (1¾ in). This conductor is required to be not smaller than 14 AWG (see figures 8 and 9).
Figure 9. Bonding conductor spacing for circuits operating at over 100 Hz
Metal parts of a building or structure are not permitted to be used as a secondary return conductor or equipment grounding conductor [NEC 600.32(A)(5)]. Return secondary leads cannot be connected to the metal parts of a building or structure and used as a return for a mid-point return wired secondary circuit. This is a bad situation that can lead to fire and shock hazards (see photos 7 and 8).
Summary
Proper grounding and bonding is a basic requirement in the NEC and is found in chapter two, which is appropriately titled, Wiring
Photo 7. Violation shows metal parts of a structure being used as a neon secondary (high voltage) return circuit to transformer
and Protection. The NEC provides the minimum requirements for essentially safe electrical installations. That means we must do at least that much. These Code requirements are set forth to protect persons and property from the hazards that arise from the ever-expanding use of electricity. Chapter six of the Code covers special equipment, and electric signs and neon outline lighting systems are covered in chapter six. The requirements in Article 600 often amend or supplement the requirements in chapter two. Following these basic minimum requirements for grounding and bonding of signs and neon lighting installations contributes to the safe use of electricity. We hope that this brief tour through the basic grounding and bonding requirements for this type of equipment is of some help and provides some answers to questions that all too
Photo 8. Violation shows a connection from the last tubing electrode to the metal parts of a structure used as the high-voltage secondary return to the neon transformer
often don’t get asked. More in depth information on this topic can be found in the IAEI book, Neon Lighting. As always, the authority having jurisdiction has the final approving responsibility for these types of special equipment and installation.
Find Us on Socials