Electrical systems and equipment are grounded to achieve a greater level of safety from electrical hazards to persons and property. Article 250 of the NEC provides the minimum requirements for grounding and bonding electrical systems and equipment. NEC-2008 has incorporated revisions related to electrical grounding and bonding terminology that results in improved clarity and usability of the rules containing such terms. This article reviews a few of the revisions and provides a more specific review of what equipment grounding is intended to accomplish.
Photo 1. The Earth
Figure 1. Bonding establishes continuity and conductivity
Common Language of Communication
To understand the requirements adequately one should always be familiar with defined terms related to the subject matter. The way the defined terms are used within theCodeprovides users with improved understanding of how the rules apply to installations and systems. It’s all about developing and maintaining a common language of communication; in other words, using the grounding and bonding terms that are defined in theNECfor improved accuracy in their application.
NEC Defined Terms Simplified
Connected to establish electrical continuity and conductivity (see figure 1).
Ground.The earth (see photo 1).
Grounded (Grounding).Connected (connecting) to ground or to some conductive body that extends the ground connection (see figure 2).
Grounding Conductor, Equipment (EGC).The conductive path installed to connect normally non-current-carrying metal parts of equipment together and to the system grounded conductor or to the grounding electrode conductor, or both (see figure 3).
Figure 2. Grounding means “connected to ground or a conductive body that extends the ground connection.”
Figure 3. Equipment grounding conductor performs grounding, bonding, and serves as the effective ground-fault current path
Effective Ground-Fault Current Path.
An intentionally constructed, low-impedance electrically conductive path designed and intended to carry current under ground-fault conditions from the point of a ground fault on a wiring system to the electrical supply source and that facilitates the operation of the overcurrent protective device or ground-fault detectors on high-impedance grounded systems (see figure 4).
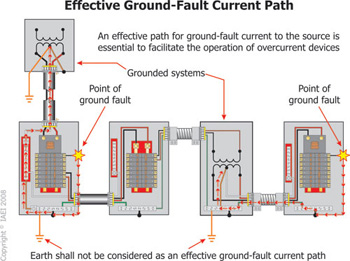
Equipment Grounding and Bonding
Section 250.4(A)(2) provides a clear explanation of why electrical equipment is grounded. This performance language indicates that when equipment is grounded (connected to ground) it limits the voltage to ground on these conductive materials. The process of grounding electrical equipment results in the conductive parts being connected to ground in a manner that maintains the conductive object at or close to earth potential in normal operation and during abnormal events such as ground faults. Section 250.4(A)(3) explains why electrically conductive materials and other equipment are bonded, or connected to establish electrical continuity and conductivity between them. From a performance standpoint, bonding not only establishes electrical continuity and conductivity for ground-fault current paths that facilitate overcurrent device operation, but also minimizes differences of potential between conductive parts, such as is required for equipotential bonding grids for aquatic environments covered in Article 680.
What Equipment Grounding Conductors Accomplish
Equipment grounding conductors essentially perform three basic functions. This component of the grounding and bonding scheme in the electrical system is a multitasking conductor. Let’s review the three performance aspects of equipment grounding conductors.
The first task accomplished by the equipment grounding conductor is establishing a conductive connection to ground (the earth) for the electrically conductive parts of equipment. The process of equipment grounding by use of the equipment grounding conductor electrically connects the conductive parts of equipment to the earth and attempts to hold these conductive parts at or as close to ground potential as possible during normal operation. This helps minimize the possibilities of electrical shock for persons that come in contact with this equipment.
Figure 5. Functions of the equipment grounding conductor
The second task performed by the equipment grounding conductor is bonding. It is clear within the definition ofgrounding conductor, equipment (EGC) that bonding is a performance characteristic of this safety circuit. The text of the definition includes the words “connect” and “together” clarifying within the definition that bond is accomplished by the equipment grounding conductor. The new fine print note following the definition of grounding conductor, equipment (EGC) indicates that the EGC performs bonding. An example of the bonding performed by the EGC is where two luminaires are connected together using a section of electrical metallic tubing. Even though the electrical metallic tubing is a qualifying equipment grounding conductor in accordance with 250.118(4), it also performs the function of bonding these two pieces of equipment together.
The third task performed by the equipment grounding conductor is that it serves as an effective ground-fault current path to facilitate overcurrent device operation in the event of a ground-fault condition in the system (see figure 5).
Photo 2. Raceway-type equipment grounding conductor electrical metal tubing
So with this understanding of the performance requirements of the equipment grounding conductor, one can clearly understand its importance in the electrical safety circuit installation. Electrical safety circuits are the grounding and bonding circuits that are constructed for electrical systems including those required for services, feeders, and branch circuits, as well as separately derived electrical systems. These performance requirements are the same for systems rated at 600 volts or less and those systems and installations over 600 volts.
Types of Equipment Grounding Conductors
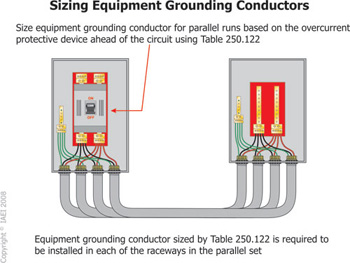
Figure 6. Sizing equipment grounding conductors based on the rating of the overcurrent protective device using Table 250.122
Sizing Equipment Grounding Conductors
It is important to understand that the sizing criteria provided in Table 250.122 is only the minimum and the actual size of an equipment grounding conductor may need to be larger than those table values to ensure effective performance of the equipment grounding conductor during ground-fault events. The note at the bottom of the table is a mandatory note, not a fine print note, and it references the performance criteria in 250.4 that must be met for safety. A common installation condition that often warrants an increase in the minimum size of equipment grounding conductor is where the ungrounded phase conductors of a feeder or branch circuit have to be adjusted in size for managing the effects of voltage drop in the design. Another condition that might require increases in size of equipment grounding conductors is where there are high amounts of available short-circuit current supplying the facility. The concern here is that the equipment grounding conductors have adequate capacity to conduct safely any fault current likely to be imposed on it.
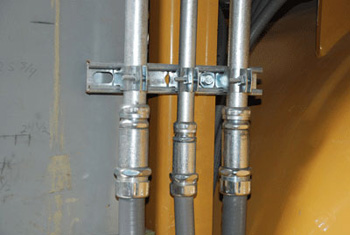
Good Workmanship
These items all have a bearing on the performance of the effective ground-fault current path during a ground-fault event. The National Electrical Contractors Association (NECA) publishes a family of ANSI-accredited standards that provide electrical workers with additional details and information about what constitutes good workmanship in electrical contracting. These publications are made available to the entire electrical industry as a concentrated effort to promote a more uniform and consistent approach to quality and integrity of electrical installations. This family of standards is titled the National Electrical Installation Standards (NEIS).
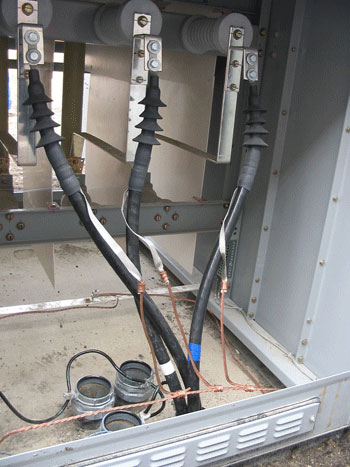
Effective Ground-Fault Current Path
- The path should be electrically continuous.
- The path should have adequate capacity.
- The path should have low impedance.
These three tasks are required of any effective ground-fault current path that is installed with feeders or branch circuits. TheCoderequires the effective ground-fault current path to be electrically continuous. For wire-type equipment grounding conductors to be electrically continuous, they must be connected to enclosures using one of the methods specified in 250.8. Where the equipment grounding conductor is a conduit, tubing, or other raceway, the fittings (locknuts, couplings, connectors, etc.) are key to meeting the electrically continuous requirement.
For effective ground-fault current paths to have adequate capacity, they must be sized to meet the minimum requirements in theNEC. Wire-type equipment grounding conductors must be sized according to the minimum values in 250.122, but may be required to be sized larger to ensure adequate capacity.
Figure 7. Equipment grounding conductors are required to be run with circuit conductors
The effective ground-fault current path must also be of the lowest possible impedance. TheCodeincludes requirements for the equipment grounding conductors to be routed with the circuit conductors to maintain low impedance values in normal operation and when functioning in ground-fault conditions. Sections 300.3(B) and 250.134(B) generally require equipment grounding conductors to be run with the circuit conductors (see figure 7).
Equipment Grounding Over 600 Volts
The grounding and bonding requirements for systems and circuits over 600 volts are provided in Part X of Article 250. Section 250.180 clearly indicates that for high-voltage systems that are grounded, the requirements in all parts of Article 250 apply in addition to any provisions that may modify or supplement those general requirements as provided in 250.182 through 250.190. Essentially, this means that where equipment grounding conductors are required for feeders or branch circuits over 600 volts, the sizing requirements for such equipment grounding conductors are the same. If a 200-ampere, 12,470-volt feeder is installed in PVC conduit from point A to point B, it should include an equipment grounding conductor sized in accordance with the rules in 250.122. The minimum size required is not smaller than 6 AWG copper for this particular installation.
Photo 6. Cable shields are required to be grounded in accordance with 310.6
Remember that equipment grounding is required for all fixed, portable, and mobile equipment and associated fence structures, housings, electrical enclosures, and supporting structures. Section 250.190 requires an equipment grounding conductor with a minimum size not smaller than 6 AWG copper or 4 AWG aluminum. It is important to note that medium and high voltage cable shielding is typically not suitable for use as an equipment grounding conductor for these circuits. This shielding is required for draining excess capacitance and electrostatic fields present where these cables terminate. This is accomplished by the use of an appropriately installed shielding conductor (either a ribbon tape or concentric stranding) that connects the cable shields to the grounding electrode, the grounding bus in equipment, or to a grounding electrode conductor [SeeNEC310.6 for additional information on connections of cable shields] (see photos 5 and 6).
Figure 7
Summary
Equipment grounding is essential for safety in electrical systems operating at 600 volts or less and for those operating at over 600 volts. Although the requirements vary slightly for both systems, the performance objectives of equipment grounding are the same. This article provided a basic overview of equipment grounding requirements in theNECand reviewed what grounding equipment is intended to accomplish from a performance standpoint. The equipment grounding conductor is a safety circuit that is intentionally constructed when installing feeders or branch circuits. The equipment grounding conductor and the process of equipment grounding results in a safety circuit that performs three critical tasks while providing safety for the electrical installation. The process provides a path to ground (earth) for electrical equipment required to be grounded. The process of grounding through branch circuits and feeders includes installing an equipment grounding conductor that also performs bonding functions as indicated in the revised definition of this term, and the third critical function of the equipment grounding conductor and the process of equipment grounding is that it serves as an effective ground-fault current path that is electrically continuous, with ample capacity, and of the lowest possible and practical impedance. For more detailed information about electrical grounding and bonding see the 10th edition of IAEI’s Soares Book on Grounding and Bonding available in the spring of 2008.
Find Us on Socials