Back to the Future
In Part One of copper-clad aluminum (Cu-Clad or CCA) building wire for Branch Circuit Wiring (BCBW), which was published in the September/October 2016 issue of IAEI Magazine, I dealt with the history, reference standards, and the macro-economic climate that brought about the emergence of core-metal CCA as an electrical conductor (Cu-Clad).
To quickly recap, CCA has underpinned the world’s cable TV (CATV) business for decades as one of its primary conductor materials, as it is heavily used in trunk and distribution cables for data.
In the world of electrical power, CCA is the third of only three industrial metals referenced by the NEC as acceptable for use as the core-metal conductor in residential branch circuit conductor applications. The three metals are copper, aluminum and copper-clad aluminum (CCA), also known by the acronym Cu-Clad when applied to an electrical conductor. Over its entire life-cycle, Cu-Clad has seen very limited installation in only a handful of US municipalities from 1972 – 1980. Since 1980, Cu-Clad has been absent from the US market.
Much of the standardization work on CCA by ASTM, the NEC, and UL was set in place by 1972 — almost a full decade after fire-hazard issues began arising with solid utility-grade (1350) aluminum branch circuit building wire (BCBW). Solid aluminum BCBW is currently banned by most municipalities nationwide for residential use, but not so with Cu-Clad building wire. To prevent another “aluminum” building wire debacle, UL extensively tested and vetted Cu-Clad BCBW using heat-cycling circuit testing methods borrowed from BICC to guarantee safe connections to standard copper-only wiring devices before it was allowed to enter the market. The standard UL test method, UL486C, is the modern incarnation of this early testing. Cu-Clad is covered by ASTM B-566 as a manufactured core-metal material; by UL83, UL44, UL719, and UL1581 as an insulated power conductor; and by the NEC Article 310.01–100 as a component of an electrical circuit.
Whereas the use of solid aluminum for residential branch circuit wiring has been summarily banned by most US municipalities since 1970, notwithstanding, just as with copper, Cu-Clad (a little-known fact) is widely accepted by most municipalities for use in residential branch circuits.
Nevertheless, due to the lack of presence of Cu-Clad in the field as BCBW, there remains a minority of municipalities that bunch Cu-Clad along with solid aluminum BCBW; and, therefore, keep it from being utilized in their jurisdictions. This error is understandable given the economics of copper that have dictated the limited usage of Cu-Clad BCBW over the last five decades. In the economy of cheap copper from 1980–2005, Cu-Clad discontinued to be a viable economic alternative. This reality ceased all production, marketing and educational campaigns. Albeit still alive and found within the 2017 NEC code, Cu-Clad has been in the midst of a multi-decade hibernation period. Officials have simply lacked exposure to it, and thus have had little basis to make an informed judgment about its safety.
The sample size of Cu-Clad wired homes is only some hundred thousand residential units nationwide, unlike the tens of millions of residences currently wired with copper BCBW. The track records for copper and solid utility grade aluminum BCBW are both clear and well-documented, but not so with Cu-Clad BCBW. But a sampling of a hundred thousand is more than large enough to draw conclusions regarding its safety.
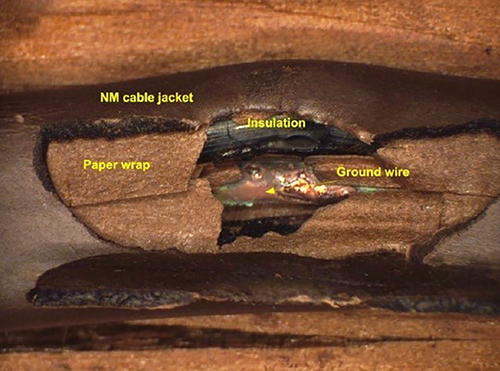
The reality is that CCA as a conductor material has proven to be remarkably well-suited for use as a residential building wire, and arguably the best core metal for the job of the three permissible metals in code. CCA is thermally stable (like copper), 2.7X lighter than copper, pliable, twistable, strong (like copper), and UL-compliant with all copper-only connection devices, more electrically efficient than copper when sized to NEC recommendations (less voltage drop), significantly more economical per foot than solid copper at modern commodity pricing levels and, perhaps the most endearing advantage to the residential builder, theft resistant.
Ninety-nine-point nine percent of recyclers will not accept CCA core wire if they know what it is. When sized correctly in the circuit, a Cu-Clad conductor runs 4% more efficiently (less heat loss) when set against the NEC recommended copper equivalent, which translates into significant energy conservation over the life of the circuit.
Next to solid aluminum building wire, which is susceptible to galvanic corrosion and brittleness in the circuit when mistakenly paired with copper-only devices, both potentially lethal conditions, Cu-Clad conductors are neither. CCA is not susceptible to galvanic corrosion because of its thick copper hide, and is remarkably pliable, strong and twistable as a result of the pressure bond manufacturing process of mechanical cladding.
The following pages will discuss aspects of Cu-Clad residential branch circuit building wire in depth. It will identify the causes of failure in BCBW in general, as well as what manufacturers have done over the years to make their CCA core-metal wire safe for residential electrical conductors. You will gain insight into a few of the communities where Cu-Clad BCBW is currently in use, how to identify it in the circuit, and how the wire has held up over time. You will learn of its safety record, and see evidence that Cu-Clad residential BCBW is forgiving of poor workmanship, perhaps even more so than solid copper BCBW. You will also learn that existing installations using Cu-Clad BCBW are able to connect and terminate using today’s standard, residential-grade wiring devices meant to be used with solid copper wire. Finally, with the help of an industry-leading metallurgical lab, you will gain insight into the quality level of Cu-Clad BCBW by reviewing various test results from wire samples after having been in live circuits for nearly ½ century.
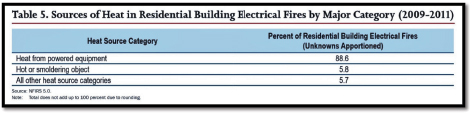
The Factors that Cause BCBW Conductors to Fail
According to the U.S. Fire Administration, only 6.3% of all residential fires in 2014 were caused by malfunctioning electrical systems a/o equipment. In other words, slightly more than nine out of every ten residential fires are caused by factors other than electrical issues, which goes against common intuition. Cooking remains the root cause of one out of every two house fires in the United States.
Much progress has been made over the many decades to reduce the risk of using electricity in the home. Further, an abundance of excellent research has been conducted over the last 25 years by officials and industry experts aiming to decrease property loss and the number of deaths caused by electrical fires in homes. In this endeavor, the residential, electrical branch-circuit wiring system has been an area of keen study. According to the National Fire Protection Association (NFPA), “there are nearly 26,000 residential electrical fires each year. In the vast majority of cases (nearly 85%) residential electrical fires occur in one- and/or two-family dwellings, as opposed to apartments and condominiums. In nearly 30% of these cases, the (BCBW) insulation is the first material to ignite, which is first among all the other combustible component materials of the study.”
Further, it was found that electrical wiring was involved in nearly 22% of the cases of electrical fires.
It is with good reason, therefore, that BCBW should be under the microscope. The hope when undertaking these types of investigations is to trace out the root causes of failure to prevent losses in the field. It should be emphasized that solid copper has been the only core-metal material utilized for residential BCBW in the USA since 1980, so all the modern testing and resulting data on the subject reflects the use of copper as the core-metal conductor rather than the two other options. Modern research demonstrates that even solid copper wire can yield problems. Given that solid aluminum is already off the table as a viable alternative, the relevant question becomes, does CCA perform better than solid copper in branch circuit building wire? Has Cu-Clad BCBW been wrongly accused (bundled with solid wire aluminum) by the industry due to a paucity of information and study on the subject? Below is an image of solid Copper NM cable as a result of testing at UL during its research for its ground-breaking report, “Influence of Damage and Degradation on Breakdown Voltage of NM Cables.”
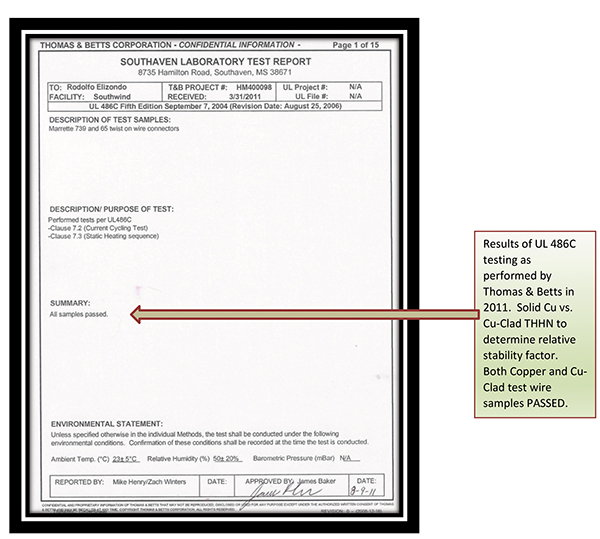
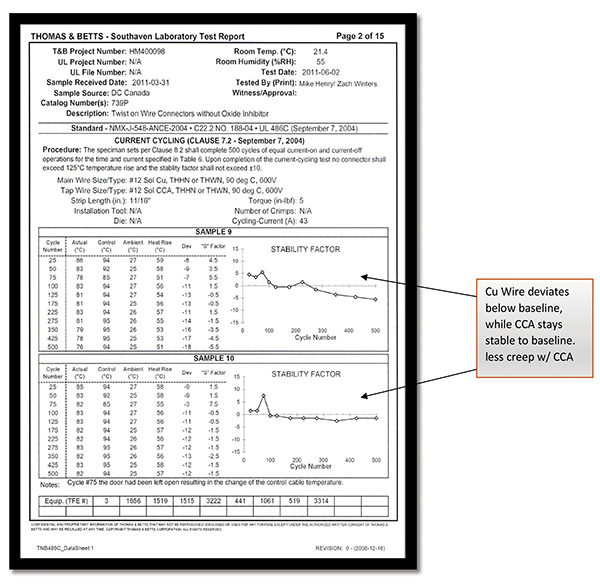
Enemy Number One: Arc-Faulting
Electrical arc-faulting caused by failures in branch-circuit wiring systems has been identified by researchers as a (if not “the”) primary culprit in residential electrical fires. According to the NFPA document, Topical Fire Report Series. Volume 14, Issue 13 / March 2014. Residential Building Electrical Fires (2009 – 2011), “the ‘heat from powered equipment’ category accounted for the majority (89 percent) of all electrical fires, and within this category, electrical arcing accounted for 82 percent of the incidents.”
Arc-faulting is a complex phenomenon, the origin of which is many: core-metal thermal creep contributing to the loosening of connections and terminations; galvanic corrosion of the core-metal creating hot spots and loosening at the point of termination; physical damage to the conductor; poor workmanship during installation; overloading of the circuit coupled with a faulty breaker; faulty electrical devices, as well as faulty insulation of the conductor. In judging which core-metal of a power conductor is superior to the other, the problems caused by poor workmanship, faulty electrical devices, faulty wire insulation, overloaded circuits and conductor damage have no bearing. Issues arising from these factors will occur regardless of the core-metal type. To measure core-metal performance, only thermal creep and galvanic corrosion are therefore applicable.
The Role of Creep in Arc-Faulting
In an attempt to standardize conductor products so that they may combat the deleterious effects of arc-faulting, UL and other accrediting agencies have developed testing standards to identify points of potential failure. UL, for example, developed UL 486C for this purpose. UL 486C was designed to measure thermal stability in conductor core-metal to avoid thermal creep, the primary factor thought to be responsible for arc-faulting at points of termination/connection. The test is rigorous. It purposely puts higher-than-permitted-by-code voltage through each test-sample conductor, in periods of on–off power over 500 cycles. The test takes months to complete. The aim of UL 486C is to locate the stress points in the test samples under the worst conditions that a real-world installation could possibly afford.
In 2011, Thomas & Betts, a world-leading producer of electrical connectors and devices, tested the thermal stability of 12 AWG CCA vs 12 AWG Cu as per UL 486C in their internal laboratory in South Haven, MS. The Cu-Clad samples were supplied by COPPERWELD Bimetallics and Condusal, SA. Note that all Cu-Clad wire samples passed this rigorous test, and performed similarly to solid copper wire. This gives credence to the idea that a CCA core metal does not create a higher probability of creep within an electrical branch circuit. The creep characteristics of CCA are in the same league as that of solid copper, if not better, as a result of its engineering and manufacture. Additionally, one company, for example, uses grade 8000 series aluminum for the core of their CCA material. Grade 8000 series aluminum was developed in 1968 to have the same thermal characteristics as solid copper, and to prevent it from relaxing at the points of termination.
When judging the results of this particular test, it can be argued that Cu-Clad performed better in thermal stability than even solid copper after 500 hours of cycle testing. The Cu-Clad wire stayed closer to the baseline temperature over 500 cycles than did the solid copper wire in the same test, which trended below the baseline temperature. Temperature change (either above or below the base-line) indicates the degree of mechanical change in the core metal. Below is the result of testing a solid 12 Cu wire against a 12 CCA wire.
Galvanic Corrosion Can Also Cause Arc-Faulting
Galvanic Corrosion should also be carefully considered when choosing a core-metal for BCBW. All metals have an electro-magnetic potential. When dissimilar metals come into contact with each other within an environment (medium) conducive to ionic locomotion (a humid or high-saline environment accelerates the galvanic corrosion of dissimilar metals, for example), the less noble metal will begin to surrender its mass to the more noble metal. Ions of the less noble metal will begin to migrate from their grain-matrix towards that of the more noble metals surrounding it. Further, when less noble metals corrode, they form primary oxides that act as insulators, making the corroded wire hotter when in the circuit and compounding the problem. This was the case in the 1960s when solid aluminum BCBW was connected to Copper-Only devices in residential branch circuits.
Aluminum is less noble than copper, brass, and steel; therefore, the aluminum wire surrendered its mass (via ion locomotion, i.e., galvanic corrosion) to the electro-plated steel screws and brass-coated steel contact plates of the copper-only devices to which it was connected. The loss of mass in the aluminum wire caused wire embrittlement and loosening at the points of termination, and the precipitant oxide crust on the surfaces of the metals caused overheating of the already compromised core-wire (having lost a portion of its mass). This resulted in arc-faulting and overheating, yielding to device melting, carbonized path condition, and ultimately house fires.
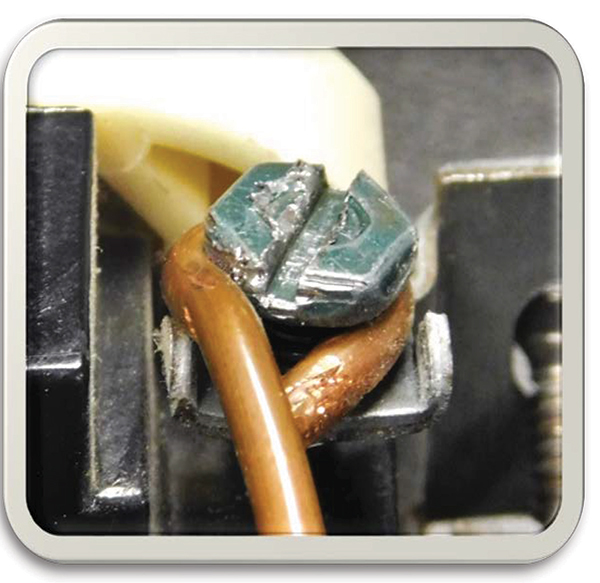
Galvanic corrosion does not occur with a Cu-Clad wire when connected to a brass electroplated steel screw / brass-steel plate contact system of a “copper wire only” electrical wiring device. This fact is well documented. The thick copper “hide” of Cu-Clad wire allows for a stable connection of similar metals within a circuit designed for copper-only wire. Galvanic corrosion simply cannot occur when two similar metals with similar electro-magnetic potentials are connected to each other. The mass of the wire stays put.
With the introduction of arc-fault circuit interrupters (AFCI) in the 1990s, the industry has installed another layer of safety against arc-faulting in branch circuits. AFCIs are by no means perfect, but their positive effects are undeniable. New residential construction is required by the NEC to install AFCIs in bedrooms. This could help explain the downward trend in electrical fires in the country today.
To date, there’s not been one claim against Cu-Clad BCBW for increasing the probability of electrical fires over either of the other two core-metal conductors allowed by the NEC, despite the existence of a large statistical sampling. Since its reintroduction in 2006, there has not been a claim against Cu-Clad BCBW from abroad.
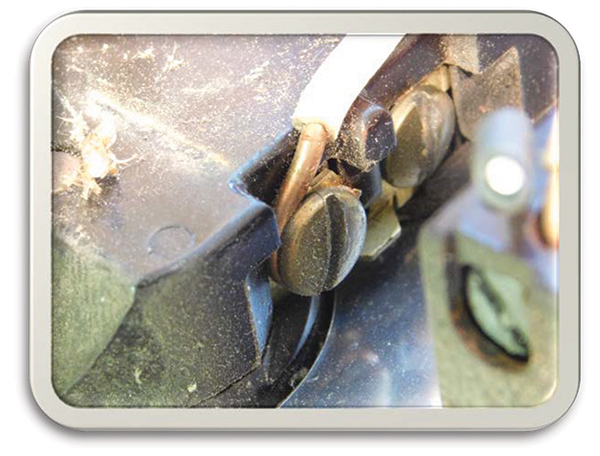
Further, there have never been any damning statements against Cu-Clad BCBW by industry watch-dogs like those made against solid aluminum BCBW by the US Consumer Products Safety Commission. Nor was there ever an Ad-Hoc Committee organized by UL to usher out Cu-Clad BCBW from the market, like there was with solid aluminum BCBW from 1968 to 1974. To the contrary, the record clearly shows that UL assisted in the introduction of Cu-Clad BCBW into code because it tested so well.
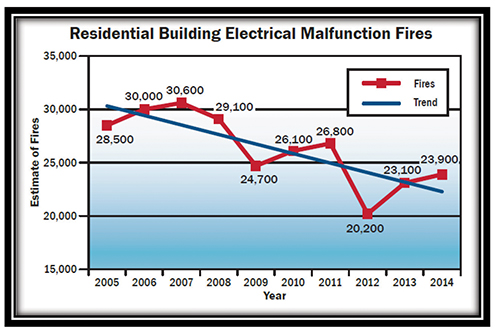
Finally, according to Mr. Dustin Fox, the current sitting chairman of the ASTM Main Committee for Electrical Conductors, B01, “There has never been any documented incidents of catastrophic failures in any system that was specifically related to the use of CCA. In my 20 years of experience in working in the wire and cable industry, I have seen CCA used in multiple power applications with great success as a safe and reliable conductor. My experience and statements are only related to good quality solid-clad CCA that has a verified metallurgical bond and is compliant to ASTM B566.”
Notwithstanding, to further verify the safety and reliability of Cu-Clad BCBW within the residences and communities in which it is currently installed, the May-June installment of this article offers inspection results from homes wired with it. Also, it offers direct testimony from residents of homes and neighborhoods where it is currently in use, as well as official fire data and statements, where available, for these communities.
Find Us on Socials