Many years ago, I accepted a position working on a joint venture called KFM (Kiewit/FCI/Manson) to assist with the construction of a new bridge from Oakland to Yerba Buena Island. When I arrived in San Francisco (SF) and drove to the base of the existing bridge, I soon realized the enormous nature of the task I had accepted. The scope of my work, at the time, was to assist with the temporary power requirements for the project and assist the welding engineers with various foundation elements out in the SF Bay. No direction was provided by the joint venture team. There was no book or manual to read to tell me how to proceed. Moreover, I soon found out fairly quickly that I was the only team member with an electrical background. Now I have a stomachache. Luckily, this was not my first rodeo. I had previous experience with organizing a project and planning for success. With large-scale PV inspections, planning and project management are especially important. As mentioned in my earlier articles last year, you will need a well-seasoned team of inspectors and organized documentation to ensure proper inspections and safe installations that will function for decades with limited maintenance and unscheduled power events.
This article attempts to lay the foundation for properly planning for inspection of a large-scale PV project, developing an inspection team, and communicating with all of the players.
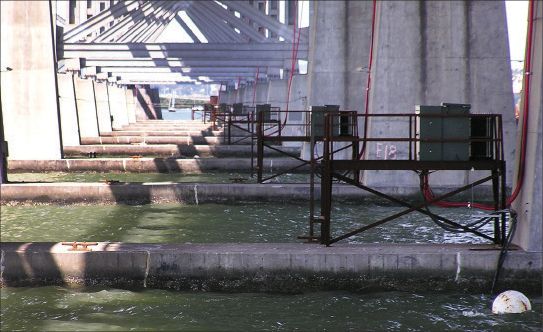
Building & Safety Discussions
During the plan review process, the building official should be communicating with the local inspection team to keep everyone informed as to the progress of the reviews and anticipated start date. If your jurisdiction is subcontracting the inspections, allow sufficient time to provide orientation to the inspection staff and determine the capabilities of the team members. The best inspection team is made up of craft personnel. Electricians will make great electrical inspectors; iron workers, concrete finishers, and welders make great special inspectors and so forth. If your team members are deficient in certain areas, try to pair these individuals up in the field so they can collaborate. Some other things to consider:
- Who will be the lead inspector?
- How many inspectors are needed?
- What’s the duration of the project?
- Will the inspectors be present during normal construction work hours? Or only on site during inspections?
- What codes will be used?
- Who will review the project specifications with the inspection team?
- Are there areas of concern and/or importance?
- How do the inspectors communicate with the plan check engineers?
- What is the involvement of other departments and/or agencies?
- Who has the final say on issues encountered and how is this communicated?
- What type of permits will be issued?
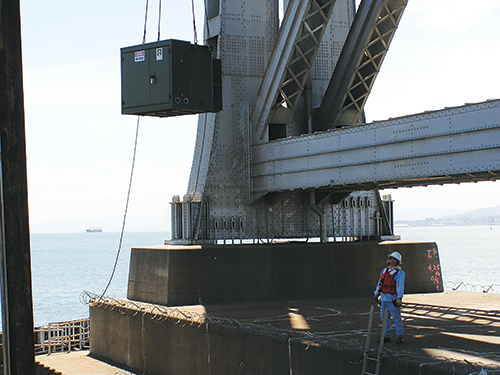
This list is part of what you may need to ask of your team to help develop a plan. I remember my first Large-Scale PV project in 2011. The contractor had already started with construction. I was given a 10- by 20-foot trailer with a gas generator for power and instructions to provide daily/weekly reports of activities. Those were the extent of the instructions and direction given to me. I figured the key to success would be communication, so I engaged with all parties, determined/developed my plan and scope of work to keep the inspections manageable on a daily basis. This type of uninformed start is a reality these days with jurisdictions that may be too busy and/or overwhelmed to plan a project from start to finish. A best practice here is for the inspection team to have self-starters to organize, communicate, and implement an inspection plan.
Alternative Materials & Methods of Construction
Every large-scale PV project I have been involved in required Alternative Materials & Methods of Construction to comply with the IBC. The most common items deal with the steel support structure. Normally the materials are fabricated (welded) and processed (rolled) overseas and do not meet the minimum requirements of Chapter 22, IBC. At one recent project, the contractor opted to send four special inspectors to China to observe the fabrication of the steel and take samples for testing at an approved US lab to confirm compliance with the appropriate ASTM Standard. In most cases, the steel failed to meet the current US ASTM Standard and, on occasion, did not meet the foreign ASTM for the country of origin. Your structural team and the engineer of record (EOR) will need to hammer out these details (hopefully) before the project starts to avoid project delays and/or structural redesigns. As an example, during plan review on one recent project, it was finally revealed that a structural fastener had an automotive ASTM that was not recognized by the IBC. This information was disclosed only after several months of back and forth communication which pushed back the start date of the project but luckily did not affect the completion date. A best practice is honest and open communication at plan review to avoid surprises.
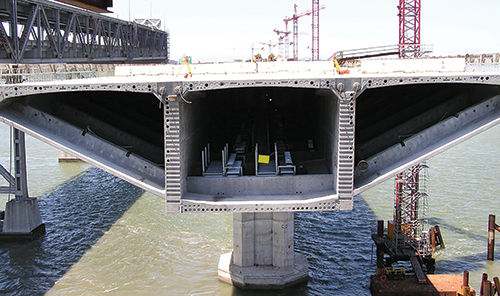
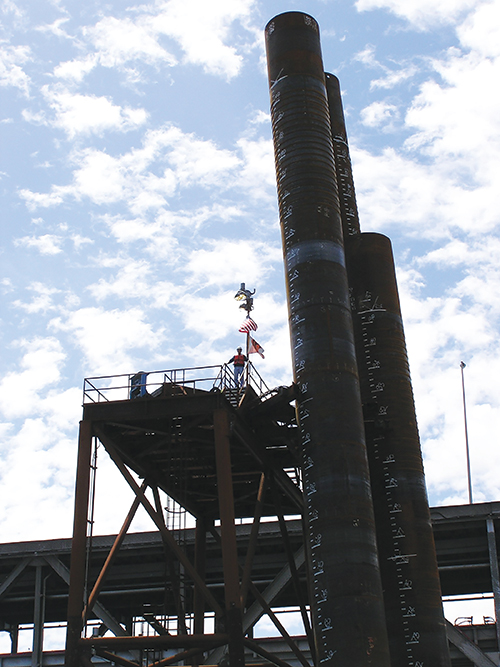
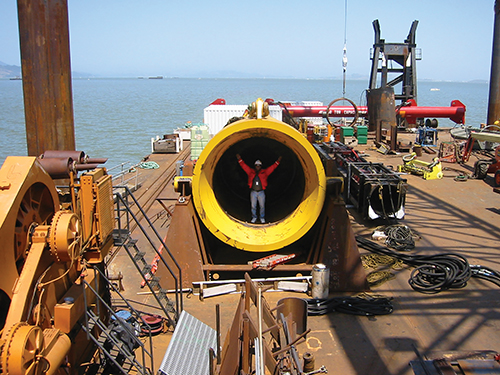
Communication & Documentation
Communication and documentation are crucial to the success of any large project. The standard yellow inspection card used by building departments for documenting normal building construction will not capture all the key aspects of inspection for large-scale PV projects and may require the team to develop their method. Alternatively, some may use a software program that notifies and documents the actions of the inspector. I used two different types of programs, and both were useful for inspections, plan-changes, and special inspection report reviews. If you do not have access to one of these systems, there’s nothing wrong with good old-fashioned daily reports, Excel sheets, Word documents and/or emails. Just keep it organized and simple to follow. As you go along, make improvements that simplify the process and make your methods of communication and documentation more effective.
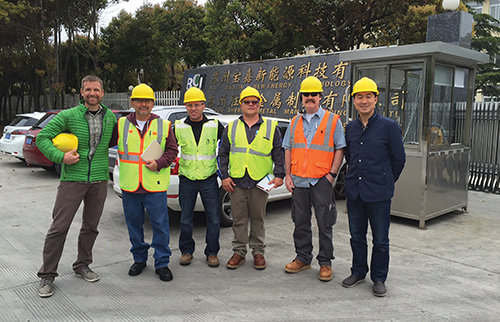
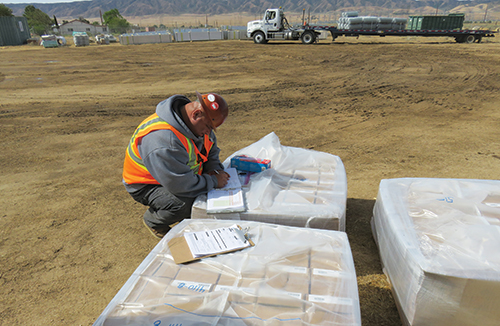
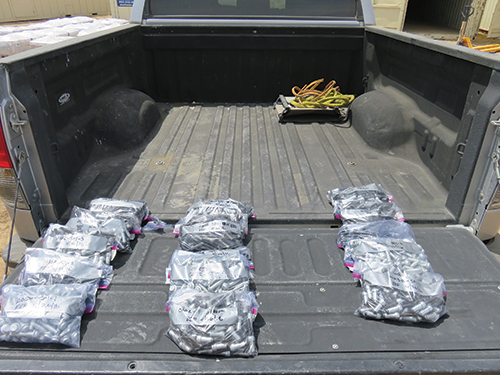
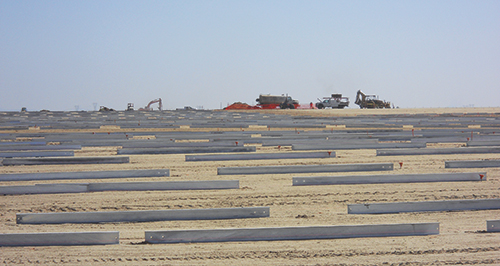
The Kick-Off Meeting
The Kick-Off is usually the first meeting at the site location and is used as a meet-and-greet organized by the project/construction manager (permit holder). This meeting should be attended by all the key personnel responsible for the construction of the project and include:
- Inspector(s)
- Special inspector(s)
- Permit holder(s)
- Installing contractor(s)
- Owner
- Fire Marshal
- Planning Department
- Third-party testing lab (NRTL Field Evaluation)
It is extremely critical that any outstanding issues left over from plan review be discussed and resolved at this stage. Implement written agreements with clear expectations of both the building department and contractor. As an example, if material sampling and testing (steel testing) are behind schedule, or if unqualified materials are arriving to be verified at a later date (additional testing), this is an opportunity to discuss and agree to a process for acceptance. I have had this happen on several occasions where the contractor wishes to install “at risk” to avoid project delays.
At risk meaning the contractor is willing to take the risk (the responsibility) for moving forward with the project while waiting for the results of some form of testing acceptable to the AHJ. The risk can be pretty risky, such as what happens if the test results on the materials fail? What if full material replacement is required? That is a pretty big risk. Hammer out these details before the project begins, you will be thankful later.
The last item on the aforementioned list (third-party test lab) is an important item. I prefer the contractor retain an NRTL before the plan-review process. The reason is, some of the production line witness testing requires several weeks to several months of lead time to properly evaluate and develop electrical field evaluation reports. Remember, some of the unlisted equipment may be manufactured overseas, just like steel fabricators. Moreover, the evaluators (engineers) will need to start their reviews during the manufacturing process and provide traceability to the site (if you are requiring third-party review). Additionally, the inspection team will need to present their inspection plan, so be prepared and ready to answer questions. Keep in mind, flexibility is a must, and modifications to your plan are to be expected based on the pace and complexity of the project. Again, communication is key here.

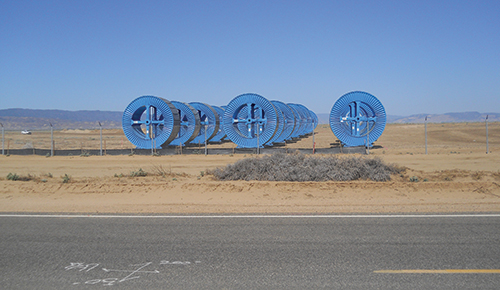
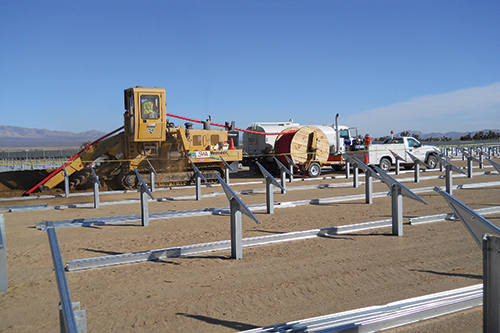
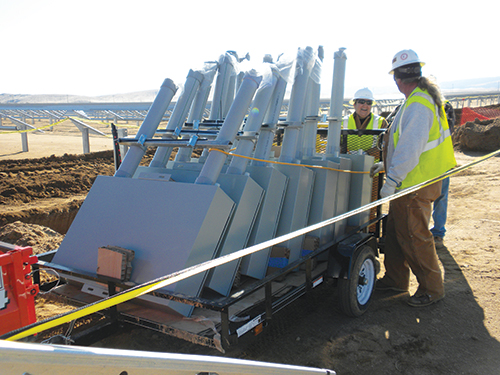
The First Day
Your first day should be spent reviewing all documentation, shop drawings, and project schedules. Hopefully, no additional changes occurred since the kick-off meeting; however, it is expected that plan revisions will occur and that process should have been established during the kick-off meeting. This time is also a chance to collaborate with the special inspectors on-site and to locate the point of contact for inspections. Some questions to ask are:
- Who’s tracking material deliveries and maintaining material documentation?
- Are all special inspectors from one company, and if not, are they collaborating?
- Where’s the laydown area for material deliveries not under the control of the special inspectors? Examples include electrical components and building products.
- Did the fire marshal require accessible roadways and/or available water for emergency vehicles?
- Do I need to attend site safety training to avoid hazards?
- Who’s the emergency contact? Moreover, is it posted at the entrance to the site?
- Do I have contact information, cell numbers?
- Is vehicle traffic controlled and not affecting the public right-of-ways?
This list is just a sampling of what you might think about during your tour of the site. Most likely, the contractor had to meet certain site requirements in order to obtain their construction permits, such as fencing, fire access roads, dust control, stormwater measures and (possibly) Native American or biologist clearances for sensitive areas/protected animal species. A best practice for the first day is to spend a full day or two at the site to get a feel for the project and interact closely with all of the contractors, inspectors and other agencies. Don’t be afraid to ask questions.
Corrections & Deficiencies
The special inspectors will normally identify all deficiencies in their daily reports followed by a weekly/monthly list of outstanding items requiring correction and/or reverification. Your corrections can be either hand-written on your normal red tag notice, or you can use a Word document as a template with the corrections noted with photos. This template allows the document to be emailed to the contractor and the photos help document the deficiency that can be used to develop future best practices. Additionally, the contractor can respond in writing to your notice through email, which provides documentation that your notice was received and reviewed by the engineer of record. If you or the contractor are using a web-based software program, this could eliminate the Word document altogether because all correspondence is captured through the system. There are many ways to do this, just pick one that’s efficient and works for all parties. I have experienced several correction notices requiring several months to years to resolve and having that electronic documentation has certainly saved me.
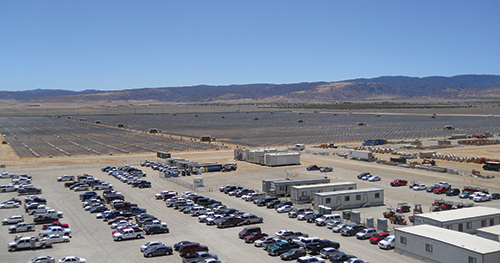
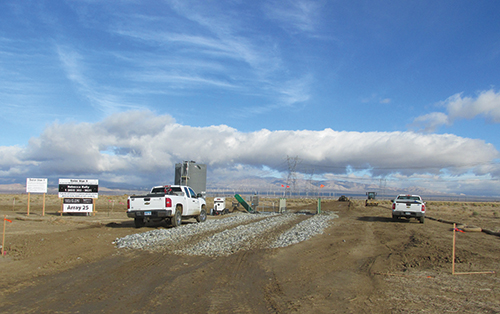
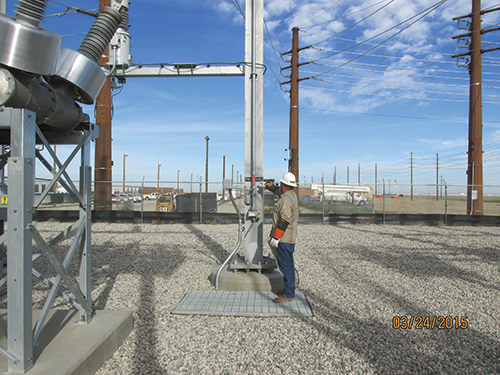
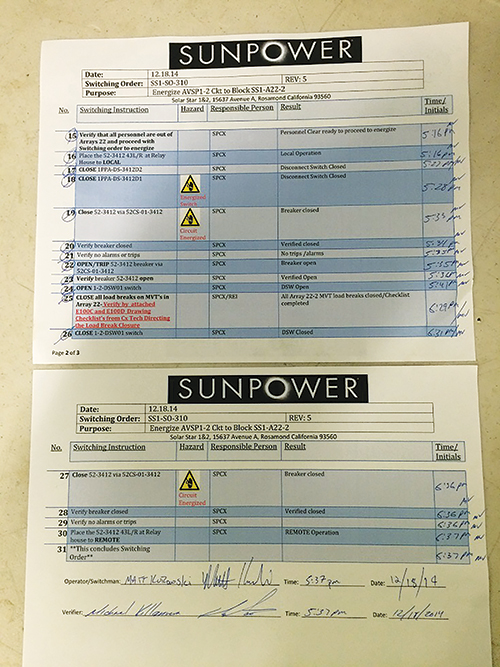
Project Closure
As the project winds down, hopefully, you gathered all your approvals for soils, grading, special inspection, NRTL field evaluations, project deviations, etc., and now you are ready to let them flip the switch. Before allowing this to occur, make sure to require NRTL third-party review of all VLF/ELF testing of cables, transformers, and substation equipment. Also, it is important to be included in the switching procedure review for the site to ensure all qualified personnel are familiar with the scope of work, see photo 18. This procedure is not a code requirement. However, you might be surprised that some don’t know what this process is, and they think it is like a residential system where you actually just flip a switch and walk away.
Summary
Hopefully, this article has given you some ideas on how to start an inspection project and keep it running so that it is planned and managed for a successful outcome. Communication should be open and occur often, and all documentation should be maintained in an organized fashion to ensure you can easily access it whenever needed. Special considerations (such as alternative materials and methods, special inspections, NRTL involvement, etc.) are most effective when addressed before beginning the project. Lastly, putting together a team with the best qualifications, and then appropriately planning their work to match the needs of the project are also important to ensure that inspections are conducted appropriately and timely. Including your inspection team in communications, and following up with them on issues observed in the field will also help to ensure that your inspections are uniform and that codes/standards are applied consistently across the project.
If this article has generated any additional questions and/or comments, please contact the author by phone 619-318-7310 or email at shinspections.inc@cox.net
Find Us on Socials