It is essential for safety that jurisdictions establish and maintain an effective code enforcement program. Inspections of installed work provide an opportunity to identify and correct potential hazards, such as shock, electrocution, fire and others, before some catastrophe occurs. Other benefits of code enforcement and building inspections are the positive affects on insurance rates and the reduced number of fires and injuries.
Numerous fires and injuries related to electrical installations or building construction generally indicate a deficiency in the code enforcement program. Unfortunately, people who do not fully understand the hazards of electrical safety often have difficulty comprehending the importance of the inspector’s responsibilities in electrical and building safety and in conformance assessment. For that reason, the importance of proactive electrical safety must be conveyed vigorously and visibly. This article examines electrical inspections and the indispensable role of the inspector. “The practical safeguarding of persons and property from hazards arising from the use of electricity,” as clearly indicated in Section 90.1, is the primary purpose of the National Electrical Code. This concept should always be kept in mind when applying and enforcing the rules contained in the Code. Electrical inspectors know and understand this; it is the driving force of their dedication and commitment to electrical safety.
Photo 1. Typical equipment labels containing applicable information on use
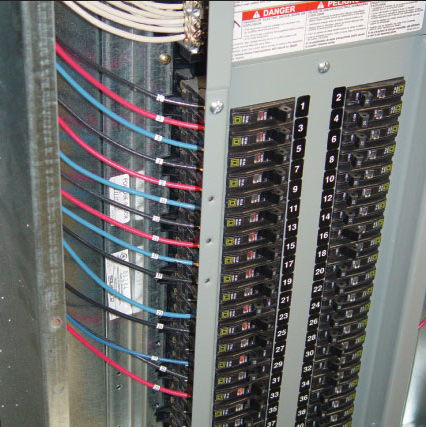
Minimum safety rules are basic
Local jurisdictions commonly amend or modify the minimum international and national standards with local requirements, as deemed necessary. These amendments or modifications usually are more restrictive and are for specific conditions unique to that region or area. One example is local amendments that deal with harsh soil conditions and the negative effects the soil has on electrical equipment in contact with the earth. Another example would be amendments to compensate for the effects of more intense heat or the levels of ultra-violet rays in sunlight on electrical equipment. Various other reasons might necessitate local amendments to the Code. Jurisdictions adopting the NEC into law should exercise careful discretion and consideration before modifying the minimum electrical safety standards.
Electrical inspection checklists offer guidance
Checklists promote consistency and uniformity in the application of the rules and serve as effective training tools for the inspector and installer. Checklists are great starting points but they are generally non-inclusive; each job has a certain amount of uniqueness, which might require diversion from any basic checklist. The best approach is to use the checklists as guides and to treat each installation with individual attention, always remembering that the NEC is the umbrella for any checklist. This means, do not rely on the checklist(s) alone; rely on the Code.
Accurate workmanship is important
Table 1. Ten essential electrical inspections
If a job is worth doing, it is worth doing right. Therefore, all electrical equipment (see definition of equipment) is to be installed in a neat and workmanlike manner, in accordance with Section 110.12. Good electrical work usually looks good as well, and the comfort level of inspectors is generally raised by the quality and appearance of the work. While it is not hard for electrical inspectors to tell if the electrical installer has experience and meets the objectives anticipated in the workmanlike-manner rule, it is also important that the inspector not get too comfortable because the work looks good from outside appearances. An installation can appear neat and workmanlike on the surface but contain serious problems inside. This important consideration will affect the approach of the installer and the electrical inspector.
When applying the general requirements of the NEC, a few of the many essential inspections come to mind (see table 1).
Listing and installation instructions must be enforced
Of first importance is the approval process and how the inspector utilizes listing and the use of listed products as a basis for approvals; this process is a primary contributor to electrical safety. In this process, the inspector verifies that the equipment or material is listed. Listed equipment has been evaluated for electrical safety; generally, the manufacturer provides installation instructions on its use and the limits of its use. Not following the installation instructions is a common violation in the field, yet it is a reasonable Code rule that is easy to comply with and to enforce. It is amazing to witness how many folks still do not follow installation instructions. Section 110.3(B) is clear and offers no exceptions. There are three other critical areas in electrical installations to which the rules in chapter one of the Code apply. They are equipment interrupting ratings covered in Section 110.9; electrical terminations and connections covered in Section 110.14; and adequate working space and dedicated space for electrical equipment covered in 110.26.
Equipment ratings and use
Equipment must have sufficient electrical ratings for the voltage, current, phase and system, etc., and must be applied in systems while not exceeding those limits [see NEC 110.9]. Examine carefully the labels that are required to be on the equipment (see photo 1). There is a plethora of information to be understood from just the equipment labels. An enormous amount of information needs to be included on the labels and it seems to require smaller and smaller print to get it all on the labels. Magnifying glasses and angle mirrors are common tools for inspectors these days to assist with these challenges. Installers should have a good understanding of the markings on equipment as well. Manufacturers of electrical equipment are more than happy to provide additional guidance and information as needed, but one must request the information. It is tough to learn at the end of a red tag or an inspector’s notice of violation in the field.
Electrical terminations and connections
Electrical circuits are only as good as their weakest link. Common points for electrical failures are connections and terminations at equipment and devices such as switches and receptacles (see photo 2). Follow the weakest link theory when installing or inspecting electrical terminals and connections. Be sure that the terminal or connection device is suitable for the use and properly installed. This includes compatibility between conductor materials and the device, proper torque, and ratings, etc. Improper connections and terminations are primary causes of electrical failures and fires.
Working spaces for electrical equipment
Photo 3. Minimum working space is required for electrical equipment
The minimum working spaces required in chapter one for electrical equipment are necessary for ready and safe operation of such equipment (see photo 3). When installing electrical equipment that requires the minimum working and dedicated space, installers should approach the situation as though they might have to service the equipment or work on it in the future. Enough working space to meet the minimum distances provided in Article 110 of the Code is essential for safety, and is a definite electrical inspection must. See 110.26 and 110.32, 110.33, and 110.34 for the minimum distances required for equipment based on applied voltages.
Circuit and disconnecting means identification
Identification of circuits and disconnecting means as to the load served is an essential part of the inspection (see 110.22) and should be approached from the viewpoint of the occupant’s safety. The primary beneficiary of a carefully thought-out circuit directory on a switchboard, panelboard, motor control center, etc., is the occupant or user long after the final inspection and building occupancy is taken. Installers and inspectors sometimes get a bit too casual with circuit identification requirements. Changes in NEC-2008 have added emphasis and requirements to address this issue [see the revisions to Section 408.4].
Protection of persons, equipment, and property
Photo 4. GFCI protection provided to comply with 210.8(A)(1) at a wet bar sink
Chapter two, “Wiring and Protection,” contains hundreds of minimum requirements. The rules for ground-fault circuit interrupters and arc-fault circuit interrupters are located in Article 210. These two forms of protection directly correlate with 90.1 of the Code. The minimum requirements for GFCI and AFCI protection are in the interest of safeguarding persons and property (see photo 4). The inspector should verify that they are installed in locations that require this type of protection [see NEC 210.8 and 210.12].
Location and rating of service equipment
Photo 5. Service equipment and service disconnecting means to be located outside of the building or inside nearest the point of entrance (see 210.70(A)(1))
Requirements for electrical services are provided in Article 230. The number of services to a building or structure and the location of the service disconnecting means are key issues relating to the electrical service (see photo 5). In addition, there are other critical requirements for electrical services, such as equipment rating, size of service conductors, location of the service, overcurrent protection, and so on.
Grounding and bonding
Grounding of the electrical services and systems supplying the premises is another inspection must. The rules for grounding and bonding are provided in Article 250. Developing an understanding of the performance criteria and the purpose of grounding and bonding is essential for the inspector. This information is clearly provided in NEC 250.4. Effective bonding is directly related to the proper operation of overcurrent protective devices. Grounding is essential and plays a slightly different role in minimizing shock hazards and providing a means to keep conductive equipment and enclosures at earth potential, which serves to minimize shock hazards. An additional benefit of grounding is dissipation of lightning or other overvoltage conditions that might be imposed on the electrical system. Grounding and bonding circuits work cooperatively to provide essential safety and functionality of overcurrent protection during ground-fault and short-circuit events.
Overcurrent protection
Photo 6. Overcurrent devices protect the conductors and equipment on the load side of the device (see 240.4 and 240.21)
Compliance with the rules in Article 240 for the protection of electrical equipment and conductors is accomplished by proper application of overcurrent protection (see photo 6). Verification of overcurrent protection types, sizes, and locations is essential for electrical safety. Standard ratings of overcurrent protective devices are provided in Section 240.6. It is important to verify that overcurrent protective devices are applied in circuits within their short-circuit current interrupting ratings in accordance with Section 110.9.
General electrical wiring rules
Article 300 includes requirements for wiring methods for electrical installations. Essentially, these general provisions inform how to install electrical circuits, wiring methods, and equipment. Some electrical inspection essentials in Article 300 include, but are not limited to, installation and grouping of conductors of the same circuit, wiring method burial depths, protection of cables installed in walls, length of conductors in boxes, and number of conductors in boxes and raceways. Be on the lookout for crowding in junction boxes and enclosures, too many wires in raceways, and conductor protection from abrasion where necessary. These situations can lead to excessive heat and failure in time. It is important to verify that whatever wiring method is used for an installation is permitted for that particular use. Each wiring method article generally provides the restrictions on its use under the uses not permitted section (.12) of the respective article.
Conductor and cable current-carrying capacities
Verification of properly sized conductors is another electrical inspection essential. Conductors must be capable of carrying the connected load. The rules for wire sizes are provided in Article 310. Several factors impact the ampacity of conductors and cables in electrical installations: calculated loads; temperature compatibility with connected equipment, especially at terminations as previously discussed; coordination with the overcurrent protection, and compliance with product listings are some essential factors in determination of conductor ampacities.
Photo 7. Multiple NM cables bundled in a manner that requires application of appropriate ampacity correction factors (see 334.80 and 310.15(B)(2)(a))
How the conductors are installed also might require additional consideration. For example, installing conductors in higher ambient temperatures, installing multiple current-carrying conductors or cables together in a manner that they are able to dissipate heat generated by current loading. Watch for the grouping (bundling) of cables and excessive numbers of current-carrying conductors in raceways (see photo 7). Apply the appropriate correction factors and be sure that the conductor is adequate for the load and is properly protected after the correction factors are applied.
Other installations are inspection imperatives such as luminaire installations, motors and air-conditioning equipment installations and special equipment and occupancy installations as provided in chapters five and six of the Code. As previously covered in this article, this list of electrical inspection essentials is not all-inclusive. It is, however, a good starting point that provides some insight into the responsibilities and approach of the electrical inspector in verifying that installations are safe and meet the minimum requirements of the Code. Obviously, all of the Code rules are justified, and we have not visited all rules that might apply to every electrical installation. Each installation warrants its own unique challenges and is the determining factor in which Code rules are applicable.
Electrical inspection is an essential element for electrical safety for persons and property. This article has provided a glimpse of some common areas of concern for inspectors. Inspection is a big responsibility, but it is only a part of the responsibility for safe electrical installations. The primary responsibility for compliance with the Code rests with the installer and owner. The role and responsibility of inspectors is to verify compliance with requirements applicable to those installations and systems. It is equally important that installers of electrical conductors and equipment be clearly and urgently aware of the electrical installations that require most attention in the interest of electrical safety. Where there is any question about minimum requirements of the NEC, or any local code requirements, always consult the authority having jurisdiction in that particular area.
Find Us on Socials