Frequently, people associate an electrical room with Article 110 of the National Electrical Code® (NEC®). More specifically, they associate it with Section 110.26. But is that accurate? The answer would be kind of..
Section 110.26 deals with what it calls working space about electrical equipment, not electrical rooms. After all, these rooms are sometimes used for other mechanical equipment like furnaces or water heaters, which is why they are sometimes referred to as mechanical rooms. The one thing they are not is storage rooms.
The sections within 110.26 are specific to working spaces about electrical equipment that may or may not be within a room. Working space may be in a corridor, basement, exterior, or even a garage. However, the section that could be interpreted to require an electrical room is 110.27, which requires live parts be guarded against accidental contact. One of several methods to accomplish this is by placing electrical equipment in an electrical room or vault. Therefore, most architects design a separate electrical room, or mechanical room, for the main service equipment and mechanical equipment for the building, which is usually less expensive than an electrical vault. In most cases, the room is locked, which helps create a method of control to ensure only qualified persons have access to energized electrical equipment as outlined in 110.26(F).
Contained within the electrical room is the working space about the electrical equipment as described in the 2023 NEC, section 110.26(A). This space consists of several parameters:
- Depth of Working Space is a measurement that considers nominal voltage to ground and if there are grounded parts or exposed live parts across from the equipment. This information lines up with the conditions outlined in Table 110.26(A)(1). To determine this measurement, one must select the condition that applies to the installation. Then measure from exposed parts (soon to be live) or from the face of the enclosure, if live parts are enclosed, extending out the front until the minimum distance within the table is achieved.
- Width of Working Space is a dimension derived from measuring the width across the front of the electrical equipment. This can be taken from center (15 inches in middle of equipment), from left side of equipment or from right side. No matter the amperage the maximum width will be equal to the width of the equipment but will not be less than 30 inches.
- Height of Working Space is measured from grade, floor, or platform to a height of 6.5 feet and is the width of the equipment or at least 30 inches and extends out to the depth of the working space. Other items such as luminaries or sprinkler pipes may be above this space, but not within it.
- Grade, Floor, or Working Platform requires the grade, floor or working platform to be kept clear and that the floor, grade, or working platform be as level and flat as practical for the entire depth and width of the working space for the applicable working space. This is largely because electrical equipment that requires servicing may be in different environments.
Entrance to and Egress from Working Space requires at least one entrance of sufficient area to give access to and egress from the working space. Depending on the size of the equipment (see 110.26(C)(2)), the entrance and egress to/from the working space could be 24 inches wide by 6.5 feet high. Open equipment doors must not impede access to and egress from the required working space. If one or more equipment doors are open and access to and egress from the working space is reduced to less than 24 inches wide and 6.5 feet high, the access is considered impeded.
Most of us have seen electrical equipment located outside of the electrical room. Sometimes a panel is in a corridor of a school or back hall of a store or even outside. Panels located outside of a building may require other means to guard the live parts from accidental contact and to create a compliant working space. No matter where the electrical equipment that may require servicing is located, all of Section 110.26 applies.
So, working space and Section 110.26 must be accounted for by architects and design professionals in the overall layout and installation of electrical equipment to allow for safe access, operation, and maintenance of that equipment.
Electrical room and working space for equipment over 1,000 volts, nominal
Now, we will explore the electrical room and working space for equipment over 1,000 volts, nominal. Does 110.26 still apply to that working space within the electrical room? The answer would be no, because 110.26 is in Part II of Article 110, which covers installations under 1,000 volts, nominal.
The applicable part of 110 is Part III: Over 1,000 Volts, Nominal. Specifically, 110.32, Work Space about Equipment; 110.33, Entrance to Enclosures and Access to Working Space; and 110.34, Work Space and Guarding. Coincidently, these sections have some similarities to 110.26, such as requiring:
- Height for working space of 6.5 feet, measured from floor or platform
- Working space not to be used for storage
- 90-degree opening of equipment doors or hinged panels
- Equipment doors not to impede entrance to and egress from the working space
- Grade, floor, or platform to be as level as practical for the entirety of the working space
- 24-inch wide by 6.5-foot high entrance to and egress from the working space
As you can see, the NEC correlates sections with one another when it makes sense. There are, however, a few differences among these sections, one of which is the width of the working space.
Section 110.26(A)(2) allows a minimum width of 30 inches for working space, while 110.32 allows a minimum width of 36 inches for that same space. Another difference is the depth of the working space. Table 110.26(A) has varying depths from 3 to 5 feet, while Table 110.34(A) has depths ranging from 3 to 12 feet. All these distances are dependent on the specific condition and nominal voltage to ground.
So, for example, for a high-voltage switchgear operating at 13,200 volts to ground, with grounded parts on the opposite side, the depth of working space would be 6 feet, measured from the front of the enclosure or exposed live parts. You will notice that higher voltages and higher hazard conditions require a greater depth of working space for worker safety.
Section 110.27 covers the guarding of live parts under 1,000 volts, which in my previous part could be considered a locked electrical room. For voltages over 1,000 volts, nominal, 110.31, Enclosures for Electrical Installations, would address the electrical room or enclosure for those installations. Some methods of enclosure could be:
- An electrical vault
- Electrical room or closet
- A specific area surrounded by a wall, screen, or fence
These methods are designed and constructed according to the nature and degree of hazard associated with the installation. Additional protective measures are required for installations involving walls, screens, or fences that are used to deter access by unqualified persons. These measures may include additional height or barbed wire. These requirements are different from those found in 110.26 and 110.27.
Typically, the electrical room or vault access doors are locked to prevent access by unqualified persons, or those doors must be under continuous observation. The doors to these areas are required to open in the direction of egress and be equipped with panic hardware or listed fire exit hardware that opens upon simple pressure. For installations over 1,000 volts, nominal, these locked or monitored rooms, enclosures, or vaults must have a warning sign on the door reading, “DANGER – HIGH VOLTAGE – KEEP OUT.” [See Photo 1.]
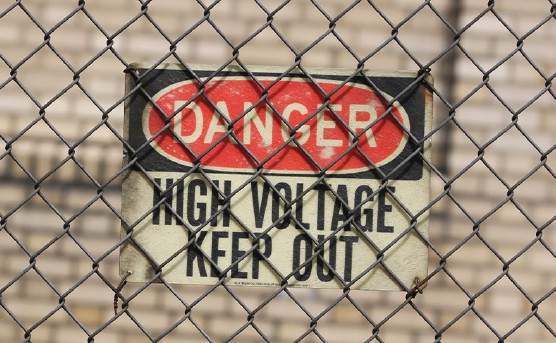
This sign must also comply with the provisions outlined in 110.21(B) around their durability to withstand exposure to the environment and specific marking requirements. Section 110.27(C) also requires a warning sign for installations of 1,000 volts or less, where there are exposed live parts. It must be placed on the door but is only required to be marked to forbid unqualified persons to enter the electrical room or other guarded area. The wording for the warning sign outside of spaces with over 1,000 volts is much stronger because of the potential exposure to high-voltage electrical hazards.
Any exposed live parts adjacent to the electrical room, vault, or enclosure entrance must be suitably guarded. Other exposed parts may require additional means to prevent inadvertent contact with exposed live parts, such as screens, partitions, or fences within the electrical room.
Any exposed live parts above the working space are required to be elevated at the distances found in Table 110.34(E) and have permanent ladders for access according to 110.33(B). These codes around working space and electrical rooms are for the protection of qualified persons who may be working on or in this equipment.
Methods for Guarding Electrical Equipment
Now, we will look at an electrical enclosure, vault, or tunnel that is being used as a method for guarding electrical equipment and see how it affects clearances for working space about electrical equipment.
What is an electrical enclosure?
First, let’s look in Article 100 to see if there is a definition for a vault or tunnel. We find there isn’t one, but we do find a definition for enclosure. Enclosure is defined as “the case, housing of an apparatus, or the fence or walls surrounding an installation to prevent personnel from accidentally contacting energized parts, or to protect the equipment from physical damage.”
So, does this definition cover an electrical room or vault? I think it could, because the vaults are areas typically surrounded by walls and frequently some form of lockable entrance.
Does a vault or enclosure still require working space for electrical equipment? Yes, Parts II and III of Article 110 cover these requirements. For voltages of 50 to 1000 volts, nominal, 110.27(A)(1) would address the use of a room, vault, or similar enclosure that is accessible only to qualified persons, as a means of protection against accidental contact with live parts. For the over 1000 volts, nominal, installations, 110.31(A)—which deals with electrical vaults, including their construction requirements—would apply.
Often, we see vaults being utilized as electrical rooms for installations over 1000 volts versus the under-1000-volt installations. This is in part due to electrical installations using exposed terminations or the use of larger substations and switches, which could increase the risk of accidental contact with live parts, depending on the type of equipment.
Construction of enclosures
Construction of the vault roof and walls must not be made from studs or wall board, but instead from construction materials that will provide adequate structural strength for the conditions and possess at minimum a 3-hour fire rating. This is usually accomplished using materials that are made from or contain concrete, like a masonry block wall with pre-cast concrete planks for the roof and floor, or a complete pre-cast concrete unit. Where the floor is in contact with earth it must not be less than 4-inch-thick concrete. However, where vacant space or stories are below the floor, it may need to be engineered to be able to structurally withstand the loads imposed on the floor.
A vault will normally have access doors as well, which are required to be tight-fitting and have a 3-hour fire rating, unless the vault has an approved fire suppression system installed, in which case the doors can be 1-hour fire rated. These doors must also be lockable, to restrict access to unqualified persons. To allow safe egress in the event of an electrical injury, the doors must be equipped with panic hardware and open 90 degrees in the direction of egress. Don’t forget the signage that must be on the doors (See Part 2 in this blog series for more on signage). Should an electrical catastrophic failure occur, the vault’s robust construction will help mitigate damage to other portions of the building, which could ultimately save lives.
This type of heavy-duty construction requires detailed planning from the electrical contractor and design professional for all electrical equipment locations and the penetrations into the vault from feeders, branch circuits, or raceways that will be connecting to that electrical equipment. These penetrations must not reduce the rating of the vault.
The electrical equipment contained in the vault, such as the switchgear, transformers/substations, and motor control centers (MCC), must meet the working space requirements found in 110.26, 110.32, and 110.34 of the NEC. The applicable NEC section is determined by the highest nominal voltage for the equipment in a particular area, since there may be more than one voltage within a vault. Where high-voltage equipment is contained within the same vault as equipment 1000 volts or less, there may need to be some separation in accordance with 110.34(B). If the separation is accomplished with a fence controlled by locks, then 110.31 would apply. Table 110.31 contains distance values for the required space between the equipment and the separating fence. Note that the fence cannot be within the working space measurements found in Table 110.34(A).
Adding electrical equipment in a vault does not reduce the working space requirements found in 110.26 or 110.34. It just adds some additional items to work around. Whether your electrical equipment is in an electrical room or a vault, you must maintain proper clearances for worker safety.
A great way to learn more about working space about electrical equipment is to register for the NFPA online training series on the 2023 edition of the NEC. Working space about electrical equipment is covered in the General Equipment Installation Practices section of this training. Learn more about this comprehensive, self-paced training.
Important Notice: Any opinion expressed in this column is the personal opinion of the author and does not necessarily represent the official position of NFPA or its Technical Committees. In addition, this piece is neither intended, nor should it be relied upon, to provide professional consultation or services. Images courtesy of NFPA.
Originally posted on NFPA.org Blog.
Part 1: Electrical Room Basics Part 1
Part 2: Electrical Rooms Part 2
Part 3: Electrical Room Basics Part 3
Find Us on Socials