Whether an industrial application, a commercial space, a residential build, or a retrofit, there is inevitably a choice to be made when it comes to a building project’s wiring system—hardwiring or modular wiring? Is it more advantageous to “pipe-and-wire” your project or will you be better off with a “plug-and-play” solution?
While every project will have its own needs, goals, and challenges, recent updates to modular connectors have elevated them to the superior choice when it comes to ease of installation, system flexibility, cost of installation and maintenance, and safety. Connectors of today are more reliable than ever, are available with multiple connection options, and are designed to withstand prolonged environmental stressors—all reasons that more of today’s electrical engineers are relying on modular connector systems to deliver exceptional performance while reducing cost and upkeep.
Material and installation costs continue to rise. Skilled labor remains a challenge. Modular wiring systems—preassembled connection solutions designed to simplify the wiring process—are an effective way for contractors to address both of these issues, ensure an exceptional finished product, and maintain their profitability. Modular wiring systems benefit building owners and management as well, reducing their project costs, time and money spent on building maintenance, and total cost of ownership.
What is modular wiring?
With a modular wiring system, electrical components are connected using what are known as plug-and-play modules and connectors. Unlike traditional wiring, modular connections can be easily snapped together, creating dramatic reductions in installation time and helping prevent the chance of faulty wiring. Modular wiring can also be used to create complete prefabricated wiring systems that arrive onsite predesigned, preassembled, and ready to go—ideal for both new construction jobs and renovations.
In recent years, modular connectors have undergone a number of advances that have made them easier to use, increased their stability and reliability, and made them more versatile. As modular systems have become more readily adapted and the demand for them has increased, manufacturers have begun producing connectors in a wider range of options and at a higher level of quality. Today’s modular connector lineup includes connectors designed for an array of specific installation and system applications; a variety of termination, voltage, and transmission options; and a long list of innovative new features, including easy-lock termination, quick-click assemblies, and twist-top locking systems. On the durability front, modular connectors are available that can withstand extreme vibration and temperature fluctuations and prevent ingress of dust and precipitation.
What is hardwiring?
In hardwired (pipe-and-wire) systems, electrical components are connected using permanent wiring and fixed connections (in contrast to modular wiring, which uses temporary and/or plug-in connections that can be connected and disconnected at any time). Hardwiring typically involves the installation of permanent wiring systems that connect any and all electrical components (outlets, switches, fixtures, devices) and run through walls, ceilings, and floors. Delivering a fixed, integrated electrical infrastructure, hardwiring provides a safe, reliable, consistent electrical supply in commercial, industrial, and residential structures.
What are the biggest advantages of modular wiring vs. hardwiring?
More and more property owners, construction managers, and electrical engineers are specifying connector-based electrical assemblies vs. point-to-point wiring for both new construction projects and renovation jobs. Due in large part to the high quality and versatility of today’s newest modular connection options, this shift away from traditional hardwiring is helping to lower costs, increase system flexibility, reduce installation time and effort, deliver significant tax benefits, ensure adherence to safety and performance standards, and provide a safe overall installation process.
- Modular Wiring is More Cost-Effective
As modular wiring can be installed much faster than hardwiring, it is inherently more cost-effective because project timelines are shorter and labor costs are reduced. Additionally, a large portion of modular wiring installation can be completed without an electrician-based crew. Skilled electricians are still required to supervise final wiring and perform system checks, but general labor can be used to plug system connectors together (repetitive wiring tasks) based on system plans and easy-to-follow project instructions.
A modular wiring system may cost more upfront than hardwiring, but this monetary difference is quickly recovered by more expedient onsite installation times, lower labor costs, and less chance for error due to the simplicity of modular connectors. In the end, modular connectors save both time and money, especially when the entire cost of a hardwired system is considered. Unlike modular wiring, where most costs occur on the front end in the form of material purchase and comparatively inexpensive labor, hardwiring may also incur ongoing expenses due to wiring errors or expensive system repair. Modular wiring is also dramatically more cost-efficient if a renovation or property move is needed in the future.
- Modular Wiring is More Flexible
Modular wiring is designed with adaptability in mind—plug-and-play connection components can be easily reconfigured or added at any stage in the construction process. In addition, modular connectors can be manufactured to the exact needs of the project at hand. Connectors are available in a range of shapes and sizes, can be specified in metal and plastic, and can be ordered with a variety of termination options. Connector units are also available in specialized designs, including tight-fit styles. Modular wiring connectors are fully scalable and fully customizable based on the project needs at hand.
Buildings of all sizes and with all types of layouts can benefit from modular wiring. If certain rooms and floors are standardized, wiring connectors can also be standardized. If a variety of electrical systems share the same setup (i.e., building management/service systems, HVAC systems, power and lighting systems), connector systems can be standardized per system as well.
Modular wiring components also provide greater flexibility than hardwiring systems when it comes to the future of a building. If a room or floor layout is changed, new time and money does not have to be spent on rewiring—plug-and-play connectors make it easy to disconnect, swap out, reconfigure, and reconnect your system components based on the current usage needs of the building.
- Modular Wiring is Easier to Install
Modular wiring systems are made up of preassembled components that are quickly and easily connected onsite. Installation is easier, faster, and much less complex when compared with traditional hardwiring. Many modular systems also include installation blueprints, making the installation process even simpler.
Plug-and-play connectors are also designed to eliminate the wiring and connectivity issues that may come with a hardwired system. As cables are wired directly into the components, connecting and disconnecting is extremely easy, and connectors can even be keyed to ensure that they can only be connected to their proper counterpart. Installation times, performance issues, and man hours are all reduced, and troubleshooting becomes much easier with the use of far simpler components compared to a hardwired system needed to achieve the same output.
- Modular Wiring Delivers More Tax Benefits
Because modular wiring is portable and can be classified as property, it can provide accelerated deprecation that may lead to tax savings for the building owner. Building owners can also benefit from potential tax savings on future remodeling projects as there will not be a need for new wiring to be installed during new construction. Modular wiring systems can be moved and reused, allowing them to be easily reconfigured as part of a building renovation or expansion.
- Modular Wiring is Safer
Modular wiring systems are designed with safety as a top priority. They are much easier to work with than traditional hardwiring systems, reducing the risk of onsite accident or injury. The safety standards associated with their installation are also easier to initiate, implement, and keep consistent from worker to worker—there should be no deviation in safety protocols between different experience levels, skillsets, or assignments. Today’s modular wiring components are also designed with a long list of safety features, including standardized designs and connections, built-in insulation, and fault protection, delivering even more confidence in their use.
Modular wiring components additionally provide the ability to safely swap out devices while the power stays on. This is convenient for facilities of all types but especially beneficial in scenarios where power needs to be on 24-7, including healthcare, transportation, hospitality, and judicial facilities.
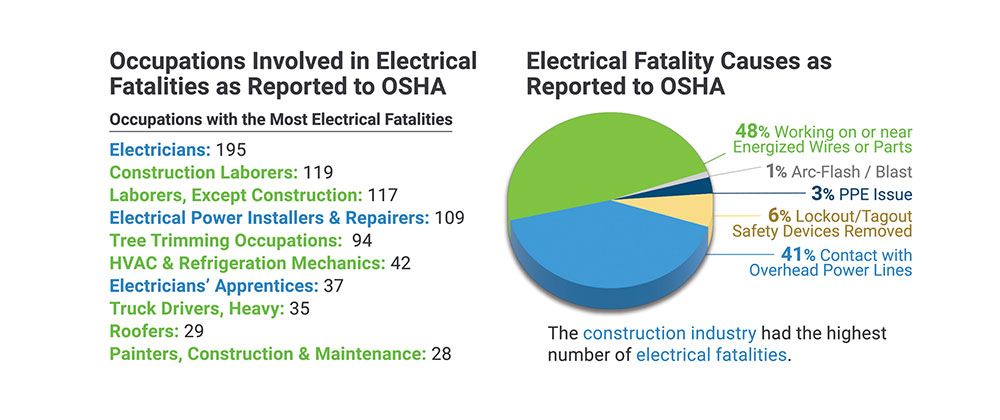
Built-In Advantages
While hardwiring may still be beneficial in some cases, modular wiring offers distinct advantages for today’s new construction, renovations, and retrofits. Unlike traditional wiring, modular wiring is based on preassembled components that easily snap together, making the entire electrical install process cheaper, faster, easier, and more reliable. Because modular connectors are so easy to use, the actual wiring installation needed onsite is dramatically reduced, and the majority of connectivity tasks can be handled confidently by standard crew members. Prewired modular components provide a simple, convenient, performance-based means of wiring buildings of all sizes while accommodating any number of layout or end-use demands.
Today’s modular wiring solutions provide an array of built-in advantages for contractors, engineers, and project planners, as well as long-term benefits for facility owners and managers. The reusable and reconfigurable nature of modular wiring also makes additions and setup adjustments much easier and much faster than with traditional hardwiring. Some of today’s most in-demand prewired modular devices include modular lighting systems (open ceiling, suspended ceiling, warehouse), plug-and-play power components (distribution modules, power cables, building interfaces), prefabricated assemblies (fully engineered systems, load centers, basic assemblies, quick-connect devices, cable-ready devices, main terminal boxes, custom whips), raised floor wiring (open office, floor boxes, underfloor power, underfloor PDU, underfloor zone wiring), zone networking (consolidation point), access floor boxes (high-capacity, low-profile, round), and accessibility products (slot link, station link).
Find Us on Socials