When you think about technology leaps, ground-fault circuit interrupters (GFCIs) and arc-fault circuit interrupters (AFCIs) come to my mind as those two that have been and continue to be technologies that are an important part of an overall change in our electrical industry. Today, we’ll look at the journey that AFCIs have taken as our industry works to make an impact on electrical fires due to arcing and sparking.
The Beginning
The story of AFCIs began in the early 1990s. As with other industry changing technology introductions, the journey begins quietly with the collecting of data to document a problem. Sometimes the data collection begins because of a personal tragedy, because an industry or company recognizes a hazard exists, or due to the pressures of litigation.
Debates at NEC Code Making Panel (CMP) meetings during the 1993 and 1996 code cycles on both code making panel (CMP) 10 and CMP-2 began the AFCI journey. The Electronic Industries Association (EIA) was the first organization to gain traction when they submitted a public input that sought to address this identified problem of electrically caused fires. While UL studied the abilities of the molded case circuit breaker (MCCB), the Consumer Products Safety Commission (CPSC) collected fire data. Information was brought forth in both areas as discussions continued in various forums to address an electrical fire problem. The EIA proposal during the 1996 NEC code cycle sought to solve the issue of electrical arcing by a requirement for MCCBs to have “. . . specified instantaneous trip characteristics to mitigate the effects of arcing faults.” And so, the technology journey to detect harmful arcing and sparking began.
MCCB performance was being questioned as fire statistics and demonstrated lack of reaction to arcing (https://youtu.be/zdrFke7YOjk) seemed to indicate that these devices were not doing their job. It seemed quite logical that the solution was to lower the instantaneous trip of the MCCB. The EIA and others drove research and study in this area, but it was realized that lowering the instantaneous trip low enough to address arcing and sparking would result in unwanted tripping issues due to inrush currents and other application related conditions. This apparent solution would not be feasible. The CMP-2 panel statement associated with a rejected proposal from the 1996 NEC code cycle provides some insight as to where the electrical industry was with regard to this situation back in the mid 90’s.
“The overcurrent protection presently required by Article 210 and specified in Article 240 properly addresses overcurrents in branch circuits as defined in Article 100. The substantiation supplied with the proposal is insufficient to show that the lowering of instantaneous trip levels in circuit breakers will adequately address fires due to low level arcing faults in damaged appliance and extension cords. A more complete analysis of actual cord problems and alternate solutions such as other cord constructions, supplemental overcurrent protection, and electronic sensing is needed.”
At this point, circuit breaker manufacturers where hard at work on two fronts. Defend their MCCB product offering and determine how to address the problem raised. Engineers behind the products had to develop a solution. A new product was about to be born.
The Branch/Feeder AFCI
It was October of 1997 that the first commercially available AFCI was introduced. This electronic solution was soon to be listed to a new UL 1699 standard and intended to be installed at the origin of a branch circuit or feeder, such as at a panelboard and intended to provide protection of the branch circuit wiring, feeder wiring, or both, against unwanted effects of arcing.
The branch/feeder type AFCI was designed to pass tests that would protect installed Type NM-B cable wiring from 5 ampere and 75 ampere arcs that the industry would soon call “series arcs” and “parallel arcs” respectively. A “series” arc is basically an arcing event between two opposite polarities and a “parallel” arcing even is an arcing event at a break in a conductor. These devices employed ground fault protection of equipment (GFPE) technology with pickup values anywhere from 30 mA and not exceeding 100 mA depending upon the brand. GFPE was used to pass performance test requirements to detect a 5-ampere series arc in Type NM-B cable. The construction of Type NM-B cable is such that the hot and neutral conductors are separated by a bare copper equipment grounding conductor (EGC). A 5-ampere series arc in this conductor will propagate to the EGC and GFPE detects and clears it quickly. Series arc detection with this product is not afforded to connected two wire cords because of the lack of an EGC. An important detail that will be important later.
The 1999 NEC code cycle saw proposals to provide AFCI protection for all 15- and 20- ampere branch circuits. Through the proposal and comment phase of that cycle, CMP-2 heard debate about this new technology that would reduce the incidents of electrical fires. Although it began with all 15- and 20-ampere branch circuits being protected, CMP-2 would set that as an ultimate goal but began with a limited introduction for dwelling unit branch circuits providing power to bedroom receptacle outlets. This would give this new technology a chance for a gradual introduction. An enforcement date was established of January 1, 2002, and the journey of AFCIs to protect all 15A and 20A circuits began.
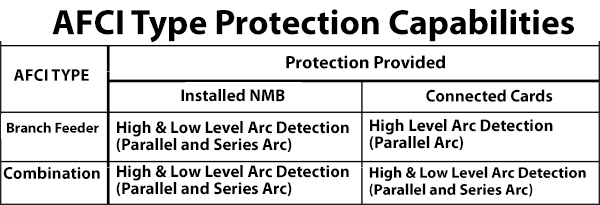
Desire for complete protection
The industry wasn’t satisfied with the branch feeder type AFCI because it didn’t afford complete protection of all installed wire and connected cords. This desire drove a shift in AFCI technology during the 2005 NEC cycle. Debates and discussions raised concerns that not all conductors are protected by the branch/feeder type AFCI. The industry demanded that connected cords be afforded the same level of protection as installed wiring. A new AFCI solution was soon to be born.
Commercially introduced in 2006, the “combination” type AFCI (UL Category Code AWAH) was added to the basket of AFCI solutions. A “combination” AFCI device provides both series and parallel arcing protection at both high and low levels. In true AFCI fashion, this introduction didn’t come without controversy and debate. This time there were debates between manufacturers of branch/feeder type AFCIs. Not all manufacturers had a combination type AFCI ready for the market. If the NEC would mandate this new technology, manufacturers would have to step up yet again to meet the new requirements.
The combination type AFCI is listed to UL 1699 and complies with the requirements for both branch/feeder and outlet circuit AFCIs. These devices are intended to provide protection of downstream branch circuit wiring and cord sets and power-supply cords. NEC 2005 modified the language of 210.12 and would no longer permit the use of the branch/feeder type AFCIs. January 1, 2008 was established as the date the industry would transition to the new combination type AFCI. The desire for complete protection prevailed at the code making panel as the journey of AFCIs continued to protect installed wire and connected cords. Manufacturers were again under pressure and hard at work to bring a complete offering to the market.
The terms “series arcs” and “parallel arcs” began to grace the lips of many in the industry as they tried to convey these latest NEC changes. Many describe the branch/feeder type AFCI as offering parallel arc detection, and the combination type AFCIs as offering parallel and series arc detection. This is an inaccurate simplistic description. The differences between the branch/feeder AFCI and the combination type AFCI are shown in Table 1.
The additional protection of the combination type AFCI is series arc protection of connected cords. CMP-2 has and continues the AFCI journey to ensure protection of all 15- and 20-ampere circuits including connected cords.
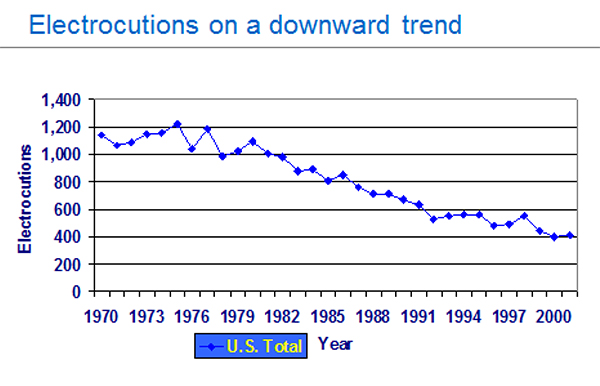
Existing Homes and the OBC AFCI
The housing inventory up to 2002 when AFCIs were first required by the NEC was more than 108 million homes. None of these homes were afforded arcing fault protection. A number that will make impacting fire statistics a long journey for AFCIs. The electrical fire statistics that have driven the need for AFCI technology is based not only on a percentage of the more than one million homes that are built each year but also on all of those existing homes that continue to age. Since the beginning of the AFCI journey, wiring device manufacturers had been working to determine how they too could help fight the battle against electrical fires. NEC 2011 was destined to not only increase the coverage of AFCI protection for new construction but also lay a foundation to address the existing housing stock. By 2011 there are now more than 115 million new homes standing, and only those new homes built to the latest NEC up to this point will have the fortune of AFCI protection and then only for those circuits that supply bedroom outlets.
NEC 2011 saw actions from both CMP-2 and CMP-18 that moved the ball forward with regard to AFCI protection. CMP-2 expanded AFCI protection to a laundry list of rooms in the home and added provisions for modifications of wiring in existing homes. CMP-18 added a receptacle replacement requirement to Article 408 [408.4(D)]. Wiring device manufacturers finally saw their opportunity to bring a solution to the market in the form of an AFCI receptacle. A new AFCI solution would soon be born.
The outlet branch circuit (OBC) AFCI (UL Category code AWBZ) was commercially introduced in 2013. This device is intended to be installed at a branch circuit outlet, such as at an outlet box. It is intended to provide protection of cord sets and power-supply cords connected to it (when provided with receptacle outlets) against the unwanted effects of arcing. This device may also provide feed-through protection of installed Type NM-B cable and cord sets and power-supply cords connected to downstream receptacles.
With the introduction of the OBC AFCI and new code changes, existing homes have yet another viable solution to help with reducing incidents of electrical fires. One of the largest concerns that CMP-2 struggled with in regard to existing dwelling units was the fact that the AFCI technology, like GFCI technology, is unforgiving when it comes to finding wiring problems. These solutions will find damaged conductors due to staples driven too hard, rodents who had extreme appetites, HVAC and plumbers who were a little over zealous with metal ductwork and hot flames. CMP-2 did not want to cause a home owner to decide to not upgrade their service because of all the wiring problems in the home that would have to be addressed for the AFCIs to permit power to flow. Relief was provided in the language included in the NEC to address these concerns.
Expanding Options
During the 2014 NEC cycle, the topic of AFCIs did not disappoint when it came to controversy. The discussion on the table was options. At this point in time the AFCI basket includes branch/feeder type and combination type AFCI circuit breakers and OBC AFCI receptacles. CMP-2 began a journey to explore how the OBC AFCI could be leveraged more in new home construction. Public inputs and debate ended with a restructuring of 210.12 and a few more options were added with restrictions. You see, the OBC AFCI is not able to provide complete protection of the entire branch circuit as it has limitations with regard to seeing behind it to detect arcing in the home run circuit. CMP-2 members continued to stress that protection for the entire branch circuit and connected cords should not be compromised. Use of the OBC AFCI in new construction was permitted, but it came with provisions to ensure an equivalent level of protection afforded by the combination type AFCI circuit breaker.
The CMP-2 technical review of reports and data settled on the fact that both the MCCB and the OBC AFCI had to work together to provide the complete protection that they have expected and required since the beginning of this AFCI journey. Manufacturers got to work yet again to bring a new solution to the market. Another new product was about to be born.
The new system-combination type AFCI (UL Category code AWDT) was introduced into the market in January 2018. This solution is the latest in the basket of solutions available for arc detection. Per the UL guide card, “. . . System-combination arc-fault circuit protection is a system consisting of a certified outlet branch-circuit AFCI installed at the first outlet of a branch circuit in combination with a specified certified molded-case circuit breaker installed as the branch-circuit overcurrent protective device. The system-combination is intended to provide protection of the branch-circuit wiring, feeder wiring, or both, and cord sets, and power-supply cords connected to receptacles against the unwanted effects of arcing. The certified outlet branch-circuit AFCI with its specified certified molded-case circuit breaker is packaged together as a certified system-combination arc-fault circuit protection system.”
As the NEC 2020 process unfolds, more AFCI solutions than ever are available in multiple packages from multiple manufacturers. Circuit breaker and receptacle solutions are readily available on the market to take a bite out of the electrical fire situation in both new and existing homes.
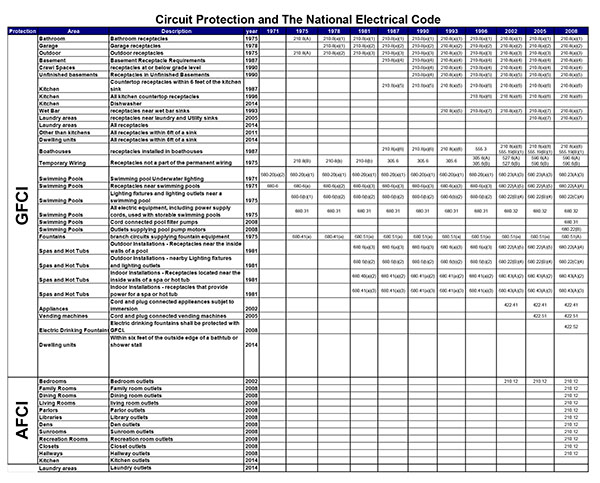
The unwanted trip
Both GFCIs and AFCIs are unforgiving technologies that have had their days of unwanted tripping. It has taken many years for our society to realize that when a GFCI trips, it probably means something is wrong. Since GFCIs have hit the market, appliance standards have changed placing a maximum leakage current limit on these listed solutions. The electrical contractor, inspector, and manufacturer work closely with each other to work through applications where tripping is occurring. AFCIs are on a similar path.
NEMA has established resources for anyone working with AFCIs. (www. afcisafety. org) NEMA manufacturers, UL and other industry partners all work together as our technologies change in our industry. Industry partners working together have changed UL standards associated with treadmills and created many educational resources.
Unfortunately, the moment an AFCI trips, many want to blame the messenger. More often than not, a tripping AFCI is an indication of a problem. Below is a 5-part series of a documented case of AFCI nuisance tripping. This video series tells the story of one homeowner who would not do what too many told him to do and replace his AFCIs with standard MCCBs.
Part 1, The Situation:
https://youtu.be/fO5ulBRdVb8
Part 2, The Problem:
https://youtu.be/97mgZw-ZrDY
Part 3, Searching for Help: https://youtu.be/XBqm3TTVPlA
Part 4, Troubleshooting: https://youtu.be/VLOgTrSM3XE
Part 5, Lessons Learned: https://youtu.be/iirOIwePOYA
Working with new technologies being introduced into the electrical industry takes team work between manufacturers, contractors, inspectors and listing agencies. The solution to any unwanted tripping event is not just in the lap of one individual. We all must do our part.
Team work
GFCIs and AFCIs are both “players” on a team. The entire team must do their job to win the game. Believe it or not, you and I are also on that team. A good look at the history of GFCIs, which have been around since the 70’s, can help us understand this. A review of the statistics of shock presents an interesting insight to not only GFCIs but also AFCIs.
Figure 1 and Table 2 are a result of my work on NFPA 73 to help identify when GFCI protection was added at the various locations within the power distribution system. That was to help inspectors who are looking at older homes. My gut reaction was that this shows the story of how GFCIs reduce electrocutions. That was until I dug deeper into understanding how our electrical industry changed over those years.
In the 50s and 60s, the Black and Decker catalogs of hand tools showed pictures of tools that are all metal. (Reference Figure 2)
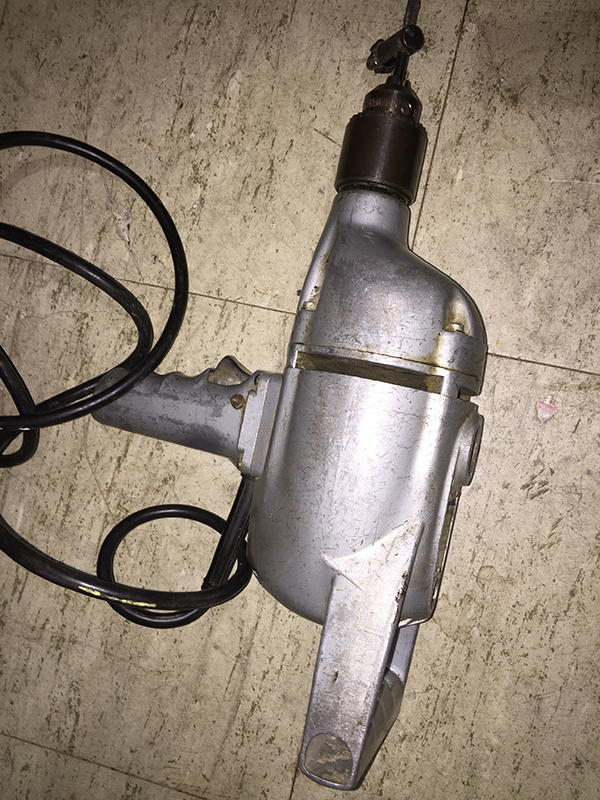
I can remember working with my uncle’s drill and having to wiggle the cord to get it to work. Every now and then I had to drop it because of the jolt I received. We would all watch when some new family member came to help and grabbed that drill. We chuckled when they dropped it in pain. Looking back now, it’s not so funny when aware of the statistics and the potential of that situation. Over the years, standards for these products changed. As I walk through supply house tool displays, I can’t find electric hand tools that are not either all plastic or at least plastic where you’ll have your hands.
Our industry has changed since the late 1970s. We not only have appliances built to more strict standards, and protection devices to detect arcing and sparking as well as lethal leakage currents, we also have an educated work force and general public awareness of the hazards of electricity. We have tamper-resistant receptacles, GFCIs, AFCIs, double insulated tools and appliances, leakage current detectors in cords, hair dryers that know when they are dropped in water and shut off. Everything around us has changed and together these statistics are impacted. Our televisions went from consoles with tubes to flat screens that mount on the wall like a picture. Lights turn on and off by themselves when we walk into a room. Change is happening, and we as an industry must adapt. Think about the manufacturer of incandescent bulbs. Energy codes have made those bulbs obsolete. The flat screen TV said goodbye to console television sets. Those changes impacted manufacturers and those who work on that equipment as well. You may have been an ace at vacuum tubes, but had to learn what a motherboard is. Change brought the ability to differentiate oneself from others in a market very resistant to new things and new ways of doing business.
Closing Paragraph
I continue to stress that there is little to no reason why anyone should die in their home due to the use of electricity. We are on a journey to safer installations. GFCIs and AFCIs are only a part of a bigger picture that will eventually have a huge impact on lives saved. Fire statistics have and continue to be debated since the original data used to show an electrical fire problem exists. Any time you hear discussions of statistics, especially fire statistics, you must think of the bigger picture. In the world of the GFCI, many deaths have been prevented by other changes in the industry outside of the presence of the GFCI. Tools, appliances, and other equipment standards have also made a difference. When it comes to AFCIs, the fact remains that there are more than 117 million homes standing– the majority of which are not afforded AFCI protection. Until the number of new circuits begin to outnumber the number of unprotected circuits in homes, impact to fire statistics will be hard to determine.
The NEMA site www.afcisafety.org provides examples of found electrical problems. Evidence of these products doing their job is clear. Evidence of electrical wiring issues causing fires and taking lives is also, unfortunately, all too clear.
No one will ever know exactly how many lives have been saved by GFCIs and AFCIs. We can only do our part to help increase the safe usage of this thing we call electricity.
Find Us on Socials