Those who have been following this series of articles for the last year or so may wonder what is involved in designing and installing a code-compliant, durable, reliable, and cost-effective PV system. Utility-interactive photovoltaic (PV) power systems are a mature technology. PV modules have warranties to 25 years and are predicted to produce significant amounts of power for 30 years or more. Inverters have warranties to 10 years and estimated life spans of 15 years or more with even greater longevity predicted in the future. PV systems can be designed and installed following existing guidelines and codes that will achieve long life, durable service, excellent safety, and cost effective power production. However, it is evident that great numbers of systems being installed today will not achieve the art of the possible because of poor design and installation practices. This article will address some of the steps that the PV systems vendor/designer/installer must accomplish to achieve a safe, durable, reliable, and cost-effective system.
Photo 1
The Equipment and the Design
PV systems can be designed and installed in a manner that will yield high levels of performance over the life of the PV modules, which is expected to be more than 30 years. Yes, inverters will have to be repaired or replaced during that time, but advances in inverter designs are driving their lifetimes ever longer. As in other fields, the quality of the products may vary and nearly all manufacturers have production problems from time to time. In most cases, the defective products are repaired or replaced under warranty and the properly designed and installed system will have a long and productive life.
Photo 2
The design of a system involves some complicated steps and details, a few of which have been outlined in previous “Perspectives on PV” articles. A full understanding of how the PV modules respond to the environment is needed. See the “Single Conductor Exposed Cables! Not In My Jurisdiction!” article in the July-August 2004 issue of theIAEI News. The electrical characteristics of the inverter must be matched to the output of the PV array under a wide variety of environmental conditions. The site electrical service must be examined to determine how to best interface the inverter to the utility in a code-compliant manner. See the “Making The Utility Connection” article in the September-October 2005 issue of theIAEI News. A site visit is absolutely necessary before any design can be completed.
The Site Visit
It is imperative that each site be visited to determine a number of critical design parameters. The proposed PV array location must be examined for available space, shading (now and in the future as the trees grow), and orientation (see photo 1). Special tools are available to the PV installer for predicting the impact of shading during each month of the year. Restrictive covenants frequently prohibit the installation of PV arrays on roof planes facing the desired direction. In some extreme cases, these covenants may prohibit any PV system from being installed on the roof. No one wants to cut down the 200-year old oak tree just south of the proposed PV array location. For the common roof-mounted systems, the structure of the roof must be examined not only for attachment methods, but also for structural loading. The location of the existing utility service entrance and the existing load center coupled with the proposed array location will determine where the inverter can be located. All dimensions must be recorded, as they will affect both the mechanical and electrical design. Access to the area where the PV array is to be located must be mapped out.
The Mechanical Design
The geographical location of the PV array will determine the environmental conditions (wind, snow, ice) that will strongly affect the mounting of the PV array. Both the array-to-rack and rack-to-roof or rack-to-ground mounting systems must be addressed in all areas. Structural loading may be positive (dead weight) or negative (wind uplift). High winds, particularly in coastal areas, and earthquakes will significantly impact the mechanical design. Lowered PV output from non-optimum orientations or shading may necessitate larger arrays if a certain output is required. Roofing materials from asphalt shingles, to metal roofs, to tile roofs must be penetrated without damage and then the penetrations effectively sealed against wind and water for the life of the system (see photo 2). Provisions should be made to allow easy removal of the PV array if the roof needs repair at some future date.
Routing of conduits and electrical wiring must be planned in advance. Codes generally require that the power conduits from the PV array remain outside the building shell until a readily accessible disconnect is reached. In some cases, metal conduits are allowed to penetrate the shell before reaching that first disconnect.
Nearly all roof structures in recent yea rs have either been designed by professional engineers (via software used by truss manufacturers) or by the installer strictly complying with the applicable building codes. Attaching any structure to these roofs that would affect either the dead weight or the live load should be preceded by an analysis of the possible effects on the roof.
An iterative process between the mechanical and electrical design is usually required. This is especially true when the site assessment does not permit an optimally sized (smallest) PV array.
The Electrical Design
The desired ac output, the available solar resource, the efficiency of the PV modules, the efficiency of the PV inverter, and the array orientation as well as any shading should be included in designing the system. After the system is sized, application of the requirements in theNational Electrical Code(NEC) and any local codes will determine the balance of systems (BOS) components such as conductor types and sizes, disconnects, and overcurrent protection. To some extent, these items are driven by the installation location (ground or roof) and the design of the inverter (internal disconnects). However, the local electrical inspector may apply local preferences/codes to some of these items. For example, external (rather than internal) disconnects for the inverter and an outside main PV disconnect may be required. Because the rules established by the NEC are numerous and complex, a PV design should only be attempted by someone fully familiar with theCodein the areas of residential and commercial electrical systems.
Coordination and Permitting
After the code-compliant design is completed (both electrical and mechanical), the PV system designer should coordinate with the building officials responsible for permitting and inspecting the system. The PV system design, at this stage, should be presented to the inspectors including as much appropriate documentation as possible. See the “PV Plan Check” article in the March-April 2006 IAEI News. The documentation should include all calculations used to ensure code compliance as well as specifications/cut sheets for each product being used. The inspectors may have their own interpretations of the code requirements of a PV system. Their comments should be integrated into the design, where possible and appropriate, before any hardware is purchased or installed. Conflicts between the requirements of the inspector and the designed system should be resolved at this point. Permits, both electrical and mechanical, should be obtained. In some cases, professional engineering approval must be obtained. Such approvals usually apply to commercial installations and, in some cases, to residential installations where roof loading is questioned.
Installation and Workmanship
PV modules will be generating hazardous amounts of power (voltage and possibly current) for the next 30 years or more even when inverters fail and are not repaired or replaced. These hazardous voltages must be well contained for that time in the face of severe outdoor environmental conditions. Daily sunlight (ultra violet radiation) over long periods of time, coupled with high temperatures (80°C +), make the use of the best materials and installation techniques mandatory. Residential PV installations typically resemble commercial electrical installations (with substantial use of conduit) more than they resemble residential electrical installations. The details of properly installing a high-quality, safe, durable PV system at the nuts-and-bolts level is a task best left to the electrician who has years of practical experience installing (but possibly not designing) electrical power systems (see photo 3).
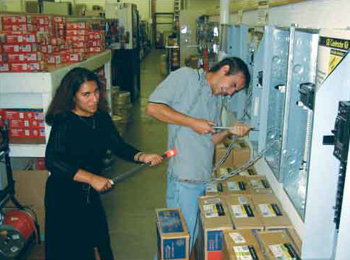
Education, Training, and Experience Are the Keys
There is no “cookbook” for PV system design and installation. While a number of helpful written guides have been developed, none of them are, or can ever be, all inclusive; none of them will be able to teach the hands-on skills required; and none of them can imbue the installer with the years of experience required to learn the tricks of the trade. The needed hands-on details are not usually found in written guides, although some of the do-it-yourself manuals on electrical wiring try to provide instruction in these areas. Hands-on training given by various organizations is important and everyone involved in PV design and installation should avail themselves of every training opportunity. Most PV equipment manufacturers offer short (1–3 day) training sessions for people using their equipment (see photos 4 and 5).
Photo 5
Photo 6
Anyone involved in PV system design and installation must have a personal library (well-read and absorbed). That library should include as a minimum, the latest versions of the following:
- National Electrical Code Handbook
- Local electrical codes
- Factory manuals for all products being installed
- Manuals for related products (each manual has a few unique tips and techniques),
- Guides
– The author’s PV/NEC suggested practices manual
– The North American Board of Certified Energy Practitioners (NABCEP) Study Guide (www.NABCEP.org)
– A set of this IAEI News series of articles, “Perspectives on PV.”
Because most PV systems are more complex than the typical residential electrical system, and the environment is more extreme (roof tops), the experienced electrician has the best experience base for installing these systems. In all cases, no PV installations should be attempted without significant experience in the electrical trades.
The Team
A team consisting of a competent PV systems designer working with an electrician using the best available equipment from the component manufacturers and the best available guidance on PV installations can design and install a safe, durable, and cost-effective PV system. The views and comments of the electrical inspectors (and any other building inspector) should be solicited and followed at the design stage (see photo 6). The system should be installed using only the highest quality balance of systems components with the highest standards of workmanship—typically commercial electrical system levels of craftsmanship. Full compliance with the requirements of theNational Electrical Codeand any local codes is an absolute minimum. The electrical inspector is a key player as that person verifies the safety of the completed installation. Close coordination, even teamwork, among the PV systems designer, the PV installer, and the electrical inspector will be required on nearly every PV installation if the art of the possible is to be achieved.
For Additional Information
If this article has raised questions, do not hesitate to contact the author by phone or e-mail. E-mail: jwiles@nmsu.edu Phone: 505-646-6105
A color copy of the 143-page, 2005 edition of the Photovoltaic Power Systems and the National Electrical Code: Suggested Practices, published by Sandia National Laboratories and written by the author, may be downloaded from this web site: (http://www.nmsu.edu/~tdi/roswell-8opt.pdf.) The Southwest Technology Development Institute web site (http://www.nmsu.edu/~tdi) maintains a PV Systems Inspector/Installer Checklist and all copies of the previous “Perspectives on PV” articles for easy downloading. Copies of “Code Corner” written by the author and published in Home Power Magazine over the last 10 years are also available on this web site.
Proposals for the 2008 NEC that were submitted by the PV Industry Forum may be downloaded from this web site:
http://www.nmsu.edu/~tdi/pdf-resources/2008NECproposals2.pdf
The author makes 6–8 hour presentations on “PV Systems and the NEC” to groups of 40 or more inspectors, electricians, electrical contractors, and PV professionals for a very nominal cost on an as-requested basis. A schedule of future presentations can be found on the SWTDI web site.
Find Us on Socials