In the product safety profession, we consider the six hazards: shock, energy, fire, injury, chemical and radiation. Of these six hazards, shock is the most common, the most deadly, and the most difficult to prevent. Energy can melt a bracelet or ring, but does not generally cause the heart to stop. To a great degree, fire can be extinguished or avoided by leaving the area quickly, and mechanical product injuries are less common and not as often fatal. Chemical and radiation hazards are less common still, and have available more countermeasures for remedies and treatment. Shock is the invisible enemy, the deadly surprise waiting for the unprepared and the unprotected.
As inspectors in the testing laboratory, we have the opportunity to prevent the risk of shock and electrocution while a product is still in the design stages. We often evaluate prototypes that have never been used by the public, or have not been widely sold and distributed. There is a great deal of attention given to examining the many ways a person can be exposed to shock hazards, including the use of accessibility probes and instruments to accurately determine the measurements of electrical spacing between live parts. The use and intended environment are also important considerations. If the construction of the product looks correct, then the evaluation turns to the testing phase, where normal and abnormal conditions are tested. These tests are designed to be repeatable, and become the part of record by which the products are regularly examined in unannounced factory inspections throughout the year. These audits continue for the life of the product, or until it is redesigned. Many times, the evaluation and testing uncovers design errors. This could be evidence that the designers weren’t aware of the requirements in the safety standards or misinterpreted the standard. Eventually, the problems are corrected, and the manufacturer is able to apply the label. This is the most reliable and practical way to protect the public and the workplace from electrical product hazards.
For field inspectors, it’s a different world. Many times, we are called to sites where things have been done incorrectly, and there are claims of ignorance of workplace laws, and arguments without foundation or logic. Sound familiar? There is a great deal of speculation about our work, and sometimes suspicion. We often have to explain patiently that we are trying to keep people from getting shocked or electrocuted, and that electricity is invisible and dangerous. We also often hear the argument that if a product is built with all certified components, then it should be safe and acceptable. This argument is absolutely false. Any certified component can be installed improperly, allowing the probability of one of the above-mentioned hazards to realize (evidence provided below).
In the end, we take some satisfaction in the fact that lives and businesses have been saved. The experiences we share amongst each other serve to continually remind us that our work is important. We can sleep better at night knowing we may have saved one life.
In the last few years, we’ve been able to easily share photos of what we’re seeing on these jobsites, and the results are always a source of amazement, even to veterans of the field. Most of the pictures in this article are from my personal projects, some others are from projects assigned to other members of our field team. None of these photos have been retouched or altered in any way, except for the removal of manufacturer information in one instance. In most cases, the manufacturer of the equipment is not shown. In all examples, the actual owner or site address is not revealed.
Restaurant and Food Preparation
Tortilla Machine
[See Photos 2-5]
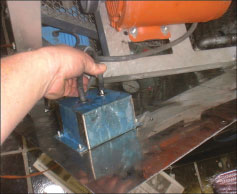
Photo 2. The cable has no markings, and there is no reliable strain relief. If the cable got caught on something, there would be an exposed live conductor.
Photo 3. Notice that the main ground was connected to an attachment screw and came loose when the cover was opened. This represents a likelihood that it would not be reattached. Also, when closing the cover, the conductors could easily become pinched by the sharp sheet metal edges
Photo 4. Mixing unit: Not only is the ground wire cut off, but the switch is non-certified (not even a CE mark), and the motor has no overload protection (UL Recognized motor, but not thermally protected).
Photo 5. Again, no strain relief, and an unmarked jacketed cable. This was a new piece of equipment, with many electrical construction problems and non-certified components.
Industrial Panels and Machinery
Bottling Plant
[See Photos 6-8]
Photo 6. Overview of a small water bottling plant, which, as you can imagine, is a wet location.
Photo 7. This control panel didn’t look too bad from the outside, but inside the rust and deterioration were obvious. Notice the new stainless steel framework it is attached to. There were other panels in similar condition.
Photo 8. Rust is a great conductor. When we reported to the inspector that this installation represented an immediate hazard, the engineering firm that designed the system and specified the materials demanded proof to back up the statement. When we sent them the photos, they were silent. Unfortunately, we were not able to complete the evaluation, (the customer never rescheduled a reinspection), and notified the AHJ that we were no longer involved in this project. We can only hope that the panels were replaced with listed panels (in this case, it would be difficult to imagine them being repaired).
Foreign Machinery
[See Photos 9-11]
Photo 9. This is new equipment, with a nice paint job, imported from mainland China.
Photo 10. Nice looking panel, right? On closer inspection, several things were discovered: 1) incorrect use of supplementary protectors (in place of fuses or UL 489 circuit breakers); 2) unmarked conductors (non-certified wiring) from this part of the world often means very little copper and sometimes toxic metals in the conductors and toxic plastics in the jacketing. Also, this equipment has unevaluated components such as 480 V filters and 120 V power supplies, controllers, fans, serve motors, terminal blocks and more.
Photo 11. Another section of the cabinet shows a non-certified outlet strip and non-certified controller. This system was under consideration for purchase by a major aircraft manufacturer. After the distributor of the system would or could not reply to the electrical construction and component issues, the aircraft manufacturer decided not to purchase the system.
Homemade Equipment
[See photos 12-13]
Photo 12. Sometimes it is obvious that the manufacturer of a system did not have a copy of the product standard. It’s hard to start over in some of these situations. The list of corrections went on and on, and they simply had to be done. In this case, the builder had to hire a licensed electrician that was also a qualified control panel builder.
Photo 13. One of the problems with this equipment was its obvious unsuitability for an outdoor installation, and the potential damage to the conductors from the sharp edges of the enclosure. Additionally, this was built to supply power to and control a remediation system (classified location)
Other Industrial Machinery
[See photos 14-16]
Photo 14. This piece of equipment didn’t look bad from the outside, and seemed to be operating normally. A look at the inside shows several obvious shortcomings. The motor does not appear to be suited for the environment, is poorly connected (see the taped cable and exposed conductors), the power cord arrangement and the proximity of hoses carrying fluid could cause a disaster under a single-fault condition (i.e., if fluid leaked into the plug configuration/motor).
Photo 15. This view shows that the plug arrangement is not even mounted, just hanging near the side of the enclosure. A closer look at the motor connection shows the exposed conductors, damaged jacket, and deterioration of the motor.
Photo 16. This final view shows a compromised junction/switch box and cut wiring.
Medical Equipment
Hair Restoration Laser
[See photos 17-20]
Photo 17. This was a new piece of equipment, purchased by a doctor. The medical facility has hospital grade receptacles, and this system requires the patient to sit under the laser, with a gel applied to the head.
Photo 18. The power supplies provided were not certified for medical use, and the system failed the leakage current limits (it tested at over twice the limit allowed). Although the laser is low-power, the issue with this type of equipment is that in a fault condition, the patient could be in direct contact with high leakage current if the equipment ground was lost (from UL 60601 requirements)
Photo 19. One of the required changes was the use of medical class power supplies, shown here after the modification.
Photo 20. In addition to the use of a non-medical power strip (no hospital grade cord), stability was accomplished by putting weights in the bottom of the enclosure. Without these weights, the unit would fall over if bumped against. (These items were also corrected for the final inspection). The doctor did not really understand what the problem was, and just wanted to use the equipment. When we explained to him that he should consider that this might unintentionally do harm to his patient, he eventually convinced the manufacturer to cooperate. He also said that he had three other clinics in another state with the same devices. It was recommended that he have the same modifications for his other locations.
Laboratory Equipment
[See photos 21-23]
Photo 21. If a certified component ends up looking like this, it is often because it was used in the wrong environment. Some components are not certified for extremely humid, wet/splash, or corrosive chemical atmospheres.
Photo 22. On the left of the chemical tank is a non-evaluated submersible heating element. In the center, you can see exposed conductors and disconnected wiring, motor, in the wet/splash environment.
Photo 23. The (non-certified) heating element in the laboratory-plating tank had already begun to burn the tank material.
Hazardous Location
[See photos 24-26]
Photo 24. This equipment is not suitable for a Class I, Division 2 area. The disconnect is for ordinary location, and the control panel design and components are not suitable for the potentially explosive atmosphere (hydrogen fuel equipment).
Photo 25. Many times, a permit is not pulled when a facility or equipment owner adds new machinery. In this case, we were called to evaluate equipment using flammable solvents, Class I, Division 2. This existing panel and fan were covered in residue from these materials. The piece of equipment we evaluated was right next to this installation.
Photo 26. Square D makes some great products. The equipment owner or installation designer had this equipment installed where it was never intended to be; however, in a Class I, Division 1 environment. Also, no grounding conductor was pulled.
Graphic Arts Equipment
[See photos 27-31]
Photo 27. Printing can be a messy business, but the mess should be limited to the floor or the outside of the equipment. These components and conductors were not meant for this kind of environment.
Photo 28. Certified components sometimes fail because they are incorrectly installed or inadequately protected. Sometimes they’re used in the wrong environment for the component design.
Photo 29. If an E-stop is placed in a location where it can be repeatedly bumped and activated, it is the wrong E-stop. These devices are also made in a configuration that prevents accidental engagement.
Photo 30. It’s likely that this was never properly connected. The attempt to repair it failed.
Photo 31. Live parts should never be accessible to a human hand or object. This is a product design mistake and an installation problem.
Listed Products Installed Incorrectly
[See photos 32-34]
Photo 32. You can be sure the installation instructions did not include an outdoor location, or the ground being added as an afterthought. Listed and otherwise certified products have specific conditions for use, which are often ignored.
Photo 33. This is a listed control panel, evidently installed in an unsuitable environment.
Photo 34. Certified components installed in a haphazard fashion. There’s a good reason why certified wireways require the covers to be attached. Also, there were no fuse values on the equipment or schematics, no warning to replace with the same type and rating of fuse, and no electrical hazard warning on the panel door. The door could be opened without the use of a tool while the circuits are energized.
A Glimpse Inside
Photo 35. This is what our installations and products might look like without the NEC and the product standards (not one of our photos).
There are many reputable and competent manufacturers. Most of them get their products certified by product safety experts. Manufacturers simply cannot be implicitly trusted to get it right. Too many corners will be cut. There are too many ways to get it wrong. [See photo 35]
The next time someone suggests that testing lab field evaluations are an inconvenience or unnecessary, show them this article. The next time someone tells you their equipment doesn’t need to be certified because it has all certified components, please, show them this article. IAEI News is available online, and it will be easy to send a link to this article. In case someone doesn’t know it, or wants to look it up, Federal OSHA law requiring electrical equipment to be approved by a nationally recognized testing laboratory is 29CFR 1910.303(a). Requiring a workplace or equipment owner to have the equipment inspected protects them and their employees from needless risk and cost, and it gives the local inspector confidence that he or she has signed their name to an installation that has a defined level of safety. Testing lab inspectors should be in the testing lab certifying products before they reach the market or the workplace, but until equipment manufacturers realize the advantages of having a listed product, we will have to be in the field, on the front lines in the fight to protect the public from electrical product hazards.
Find Us on Socials