With the increase in solar photovoltaic (PV) systems and electric vehicle charging stations, we observe more outdoor electrical equipment than ever before. The expanded use of electric energy storage systems (ESSs) installed outdoors is another example of the need to protect internal equipment from environmental conditions. Due to fire or building code restrictions on locations within or around buildings, some energy storage systems are installed outdoors and away from buildings.
Enclosure types and listings
International Standardization Organization (ISO) rated shipping containers have been used to create walk-in enclosures. These containers, built for extreme weather conditions, normally create the overall environmental protection leaving the ESS to use standard Type 1 or 2 enclosures within the container. Enclosures such as the ISO containers will be addressed in the new National Fire Protection Association (NFPA) 855 Standard that is being developed for the installation practices for ESSs.
The use of enclosures in these industries is a primary example of why environmental considerations must be evaluated. The equipment and wiring associated with these systems is inherently exposed to the outdoor elements. Whether it is extreme temperatures, constant exposure to moisture, or very dry and dusty conditions, the enclosure must provide the necessary protection for what is installed within them.
It is important we have a clear understanding of the basic codes and standards, along with the materials we are installing. The National Electrical Manufacturers Association (NEMA) provides a product standard NEMA 250 Enclosure for Electrical Equipment (1,000 Volts Max) that is harmonized with the UL product Standard UL 50E Enclosures for Electrical Equipment, Environmental Considerations. The two standards compliment the UL product Standard UL 50 Enclosures for Electrical Equipment, Non-Environmental Considerations that addresses other factors that an enclosure should meet, (e.g., grounding, bonding, sharp edges, etc.). The references in the National Electrical Code (NEC) Article 314 that address enclosures do not specifically address listing as a requirement. The requirements of NEC Section 110.28 do require some marking or identification of environmental protection that the enclosure provides.
Most enclosures used in the electrical industry fall under the scope of NEMA 250. Enclosures are designed and tested to meet certain construction requirements for their intended use—to prevent exposure to energized live parts that are installed within the enclosure and to provide protection from physical damage to those same parts. The NEC has a broad definition with how to provide such protection, as in the use of a fence. We will not address fences here, but will address the typical use of enclosures that conductors and equipment are installed within.
The typical junction box used for splices, pulling points, or enclosures with switches and other equipment will be constructed to UL 50, which addresses the construction aspects that are required to protect from exposure from live parts and protection from electrical hazards.
Photo 1: Although this enclosure contains a gasket, the label indicates it is Type 12 and 13, both for indoor use only.
NEMA has developed the Type Rating of Enclosures, which is addressed in NEC Section 110.28. This rating system creates the criteria and testing protocols for applications into specific environments. Section 110.28 states that enclosures that encase equipment, of which the list is comprehensive, must be marked with the Enclosure Type according to the environment in which it is installed. The rating marking is synonymous with a NEMA type, which is used in the field—Type 3R versus NEMA 3R rating, for example.
The type rating is also used in other standards other than the NEC. This includes UL 50E, CSA C22.2 No. 94.2, and NMX-J-235/2-ANCE. The Standardization of Type categories have been harmonized with Canada and Mexico standards, as noted respectively. NEMA 250 (and UL50E) compliment UL50 and address other factors mentioned above.
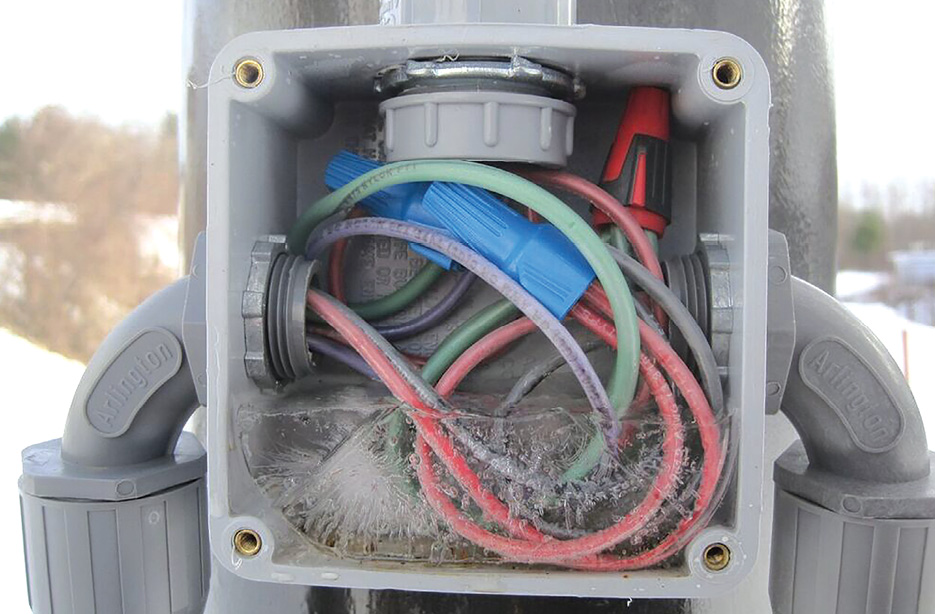
The environments we must consider when protecting electrical equipment—which include power distribution, motor controls, and even the simple splicing of conductors—may be wet (indoor and outdoors), dust laden areas (indoor and outdoor), corrosive areas, or classified (hazardous) locations. All types of enclosures must provide the basic protection within the definition of enclosures in the Code, “to prevent personnel from accidentally contacting energized parts or to protect the equipment from physical damage.” An example of a test of vented enclosures to meet this requirement is a “rod test.” The purpose of this test is to simulate something going into an opening of an enclosure and making contact with live parts. There are test protocols for non-vented and vented enclosures, such as in NEMA Types 1, 2, 3R. The environmental tests include water spray, falling dirt simulations, or testing corrosion resistance.
Application of enclosures and fittings
Now that we’ve had a clear review of enclosure types and listings, the next step is to understand how the application of enclosures and the correct fittings used in the field will maintain the integrity of the type rating, as well as provide effective wiring methods to be used in these environments. After observing hundreds of installation violations over the past several years, the most common, by far, is the misuse of these connectors with outdoor enclosures. NEC Section 110.3(B) reminds us that, “Listed or labeled equipment shall be installed and used in accordance with any instructions included in the listing or labeling.” This simple requirement is truly critical for every component of the installation, no matter how small.
Although less readily available, even individual connectors contain installation instructions and restrictions to their use. With these installations, it can be easy for an electrician not to consider the environmental limitations for even a simple accessory like a reducing washer, knockout seal, gasket, hub, or even a bonding bushing if exposed. Many manufacturers make versions of these products suitable for these environmental conditions, and it is important for electricians to be familiar with and to use these necessary options. Raceways, cables, and conductors that terminate into an enclosure must still maintain the environmental rating the enclosure was initially evaluated for. If a Type 3R is used, then the fittings and wiring methods must also be able to withstand falling rain. Type 3R is typically designed for outdoor safety or transfer switches; therefore, the fitting must be rated as raintight or approved for wet locations. This will ensure the environment will not affect the interior of the enclosure.
Type polyvinyl chloride (PVC) conduit is a common choice for outdoor installations due to its weather-resistant properties, and NEC Article 352 covers its use, installation, and construction specifications. When terminating to an outdoor enclosure, a male adapter and locknut are common practice. But is this enough to maintain the enclosure rating and keep the water out? When we research this application, the manufacturers often inform us that a rubber gasket or other approved means is necessary to maintain the water-resistance of the termination.
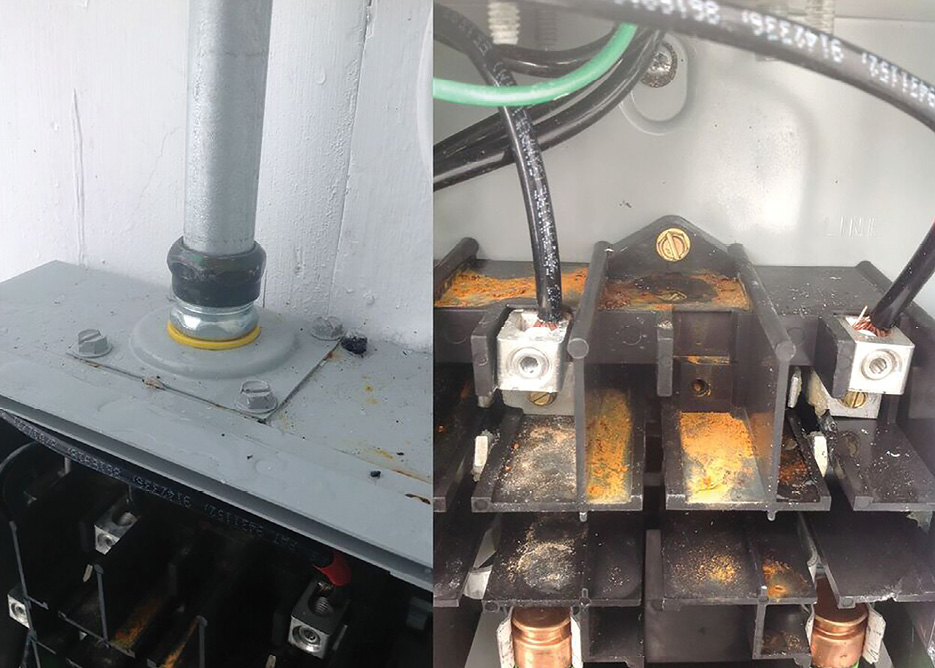
What if the source of the moisture in an enclosure is from a raceway interior that terminates in it? Since 2008, NEC Section 300.9 simply states, “Where raceways are installed in wet locations abovegrade, the interior of these raceways shall be considered to be a wet location. Insulated conductors and cables installed in raceways in wet locations abovegrade shall comply with 310.10(C).” This requirement is often confused with the interior of an outdoor enclosure, although it may seem to share the same airspace.
The enclosures have been evaluated to reduce, minimize, or eliminate the egress of water, dust, sleet, or snow. Although it is common for some outdoor enclosures to be designed with drainage openings at their lowest points, this raises the question whether we can (legally) modify these enclosures with a “weep hole” to allow water to drain, if this option is not provided by the manufacturer. In the 2014 NEC, new language was introduced to Section 314.15 stating “Approved drainage openings … not larger than 6 mm (1⁄4 in.) in diameter shall be permitted to be installed in the field in boxes or conduit bodies listed for use in damp or wet locations. For installation of listed drain fittings, larger openings are permitted to be installed in the field in accordance with manufacturer’s instructions.”
To this day, there remains a question about whether it’s okay to modify these enclosures, but as most experienced electricians will admit, the drainage opening is often the lesser of the two evils when faced with the threat of moisture damage. The new language in the NEC will hopefully assist with any uncertainty about modifying a product in the field and clarify the NEMA standard.
Unlike enclosures, raceway systems are generally closed systems and not always given the chance to drain. This differential of wet/dry is covered by NEC sections 300.5(G) and 300.7. Aboveground sealing of raceways at the enclosures prevents the moisture from moving throughout the electrical system. The raceway may be in full sun, where the enclosure may not be. This represents the temperature change addressed in Section 300.7, and sealing of the raceway with some approved method should be required.
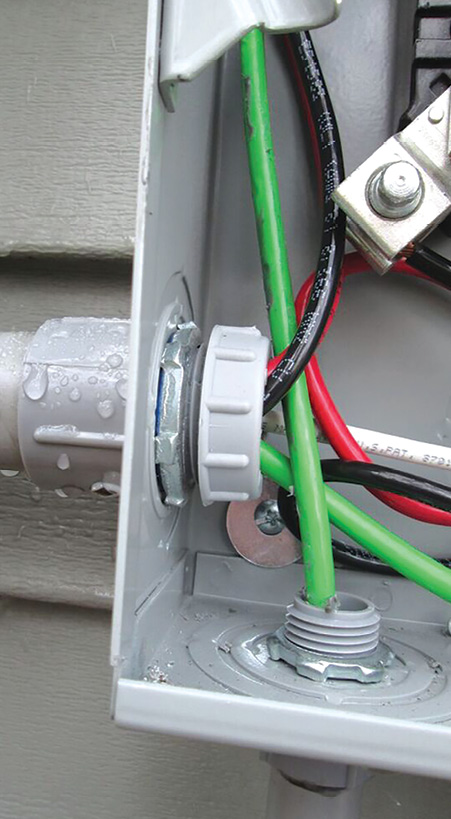
Outdoor-rated nonmetallic enclosures are becoming a popular choice for these applications due to their price, weather resistance, and versatility with locating field-installed connectors. An unfavorable property, however, is that the enclosure walls are often far thicker than those of a metallic enclosure. While it is not often a concern for a nonmetallic raceway termination (such as type PVC conduit and the large amount of threads on a male adapter), it may raise concern when terminating a metal raceway such as electrical metallic tubing (EMT).
Although the connectors often contain a quantity of threads sufficient to properly secure a locknut when terminating to these enclosures, they rarely provide ample threads to add additional hardware. We know NEC Section 250.4 requires these raceways to be bonded, and the preferred bonding method in this application is often by a bonding bushing. When the bonding bushing and locknut will not both fit, unfortunately the locknut doesn’t make the cut. Has bonding bushing to secure the raceway/connector to the enclosure been evaluated for that purpose? An inquiry to one manufacturer indicated that their bonding bushings were not listed to support a raceway. However, they offered at least two potential solutions to address this concern.
A bonding locknut would properly address both problems [if an insulated bushing is not required, per NEC Section 300.4(G)]. Another alternative is a connector designed for this application, which contains additional threads to allow for a means of mechanical support, bonding, and insulating.
Like the ever-changing sustainable energy industry, our wiring methods are also evolving. The increase in outdoor installations opens new opportunities for more innovative products to help solve today’s new challenges. With additional incentives available to support this market, the scrutiny on Code compliance becomes greater than ever before. For the installer, this means understanding the requirements in the NEC, NEMA, and UL Standards, in addition to the appropriate products for these applications.
Proper planning ahead of an installation usually pays dividends and helps to reduce the quantity of “unscheduled maintenance events” in the long term. When in doubt, let the test of time challenge your installation methods. Revisiting an installation long after weather and other environmental conditions have had the opportunity to flex their muscles is one of the best ways to assess your work.
Find Us on Socials