This is the second in a series of five articles detailing significant changes approved by the Technical Committee for the 2018 Canadian Electrical Code Part I (CE Code). The final meeting for 2018 CE Code changes took place in June 2017. It should be noted that the 2018 CE Code was published by CSA Group on January 1, 2018, and the information provided in this article is based solely on the consolidated memorandum of revisions to the CE Code, published by CSA Group after the June meeting.
Note to reader: The figures and tables retain the numbers they have in the code, so they will not be re-numbered in sequence (1, 2, 3, 4 …) in this article.
Section 10 — Grounding and bonding of the CE Code has undergone a complete rewrite. As I am sure you will see, René Leduc, Chair of the Section 10 subcommittee, and the rest of the subcommittee have done a tremendous job resulting in a completely reorganized Section 10 that has been reduced in size by deleting duplication, and re-arranged as shown below that will be easier for code users to navigate. The first thing you will notice is that the subsections have been reordered and reduced as follows;
10-000 Scope, Object, and Special terminology
10-100 Grounding – General
10-200 Solidly grounded systems
10-300 Impedance grounded systems
10-400 Ungrounded systems
10-500 Bonding general
10-600 Bonding
10-700 Equipotential bonding
This new order follows a logical sequence that aligns with how electrical equipment is installed. First is to ground the electrical system, second is to ensure that the electrical equipment is connected to a bonding conductor and third is to provide equipotential bonding of non-electrical equipment. This order is also reflected in the new Scope for Section 10 that simply reads:
“This Section applies to
(a) grounding
(i) solidly grounded systems;
(ii) impedance grounded systems; and
(iii) equipment for ungrounded systems;
(b) bonding; and
(c) equipotential bonding.”
Section 10 is the only section in the CE Code (in addition to Section 0) that has an object statement. The Object of Section 10 has been expanded to provide more detail indicating that the intent of grounding and bonding in Section 10 is to minimize the likelihood and severity of electric shock by establishing equipotentiality between exposed non-current-carrying conductive surfaces and nearby surfaces of the earth, and to prevent damage to property during a fault event.
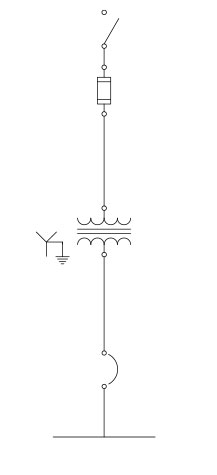
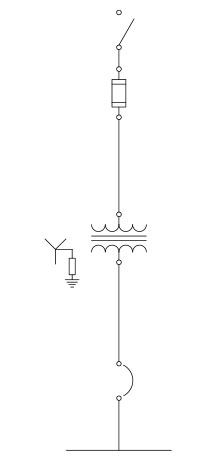
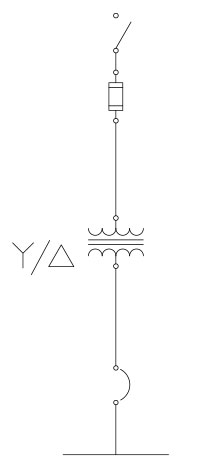
Unlike previous editions of the CE Code, Section 10 now has special terminology (unique for the application of this Section) with the following definitions:
“Equipotentiality — the state in which conductive parts are at a substantially equal electric potential.” Examples of non-electrical equipment that require equipotential bonding are metal water piping systems, metal waste water piping systems, metal gas piping systems, raised conductive flooring, and metal towers and station structures of passenger ropeways.
“Grounded conductor — the conductor of an electrical system that is intentionally grounded.” The grounded conductor is also known as the identified conductor and the neutral (or midpoint) conductor for 3 and 4-wire systems.
“Impedance grounded system — an electrical system where a point (normally the midpoint or neutral) is connected through an impedance device to
(a) an impedance system bonding jumper; and
(b) a grounding electrode, or to a conductive body that extends the ground connection, by a grounding conductor.” The impedance grounded system was referred to in the 2015 CE Code as “installation of neutral grounding devices.” In the 2018 CE Code the term “neutral grounding device” has been substituted to “impedance grounding device.” These devices are certified to CSA Standard C22.2 No. 295-15 Neutral Grounding Devices.
“Impedance system bonding jumper — a connection between the grounded side of an impedance grounding device and the non-current-carrying conductive parts of the electrical system.” In previous codes, this conductor was considered as a bond conductor.
“Separately derived system — An electrical system, the circuit conductors of which have no direct connection to circuit conductors of a supply authority system other than those established by grounding and bonding connections.” Three examples of separately derived systems are: the secondary of a two-winding transformer, the output of a power supply, and the output of a generator that does not have the neutral directly connected to a consumer’s service neutral (grounded conductor). A generator with the neutral directly connected to the neutral of a consumer’s service (without the neutral switched in a transfer switch) is not considered a separately derived system.
“Solidly grounded system — an electrical system where a point, without inserting an impedance grounding device, is connected to
(a) a system bonding jumper; and
(b) a grounding electrode, or to a conductive body that extends the ground connection, by a grounding conductor.” This definition also lines up with the requirements in existing Rule 2-104(2) to have slash rated equipment (600Y/347V) to be connected to a circuit of a solidly grounded system.
“System bonding jumper — a connection between the system grounded point and the non-current-carrying conductive parts of the electrical system to establish a solidly grounded system.” The system bonding jumper (in my opinion the most important component of an electrical installation) is also commonly known as the “bonding screw” of service equipment, or the conductor installed at a transformer secondary between the neutral and the transformer enclosure or bonding bus.
“Ungrounded system — an electrical system where no point of that system is intentionally grounded.” Ungrounded systems were recognised and referenced in the previous codes but not defined. We now have a clear definition where needed.
The first change to installation requirements in Section 10 is in Rule 10-116 for the installation of the grounding conductors. The previous requirement for the grounding conductor to be “without joint or splice throughout its length” has been deleted. The new Subrule (1) only requires the grounding conductor to be electrically continuous throughout its length, this will now allow splicing in a grounding conductor.
In Subsection 10-200 the requirement for grounding of ac and dc systems has been clarified by requiring all ac and dc systems to be solidly grounded, ungrounded, or impedance grounded. Both ac and dc extra low voltage systems are not required to be grounded with the following exceptions:
a) extra low voltage ac systems that are run overhead,
b) extra low voltage systems that are supplied by a transformer with a primary voltage of more than 150 volts-to-ground, and
c) extra low voltage systems that are supplied by a transformer that is fed from an ungrounded system.
The third change will have the biggest code impact on installations in Section 10. Rule 10-210 covering the grounding connections for solidly grounded ac systems supplied by a supply authority will now limit the number of connections between the grounded conductor and the non-current-carrying conductive parts of electrical equipment to ONE only – on both the supply and load sides of a service box. The previous CE Codes only limited the number of connections between the grounded conductor and the non-current-carrying conductive parts of electrical equipment to one on the load side of the service box. This will require bonding between the meter mounting device and the service box for ALL installations as the identified conductor of a solidly grounded system can only be grounded and bonded to the enclosure in one location.
This also means that the system grounding at a second building fed from main service which receives supply from a solidly grounded system, would no longer be permitted for any type of building, not just buildings housing livestock. It should be noted that with the exception of extra low voltage, ALL feeders and branch circuits from one building to another will be required to include a bonding conductor to be used as the bonding means for the distribution equipment at the other building.
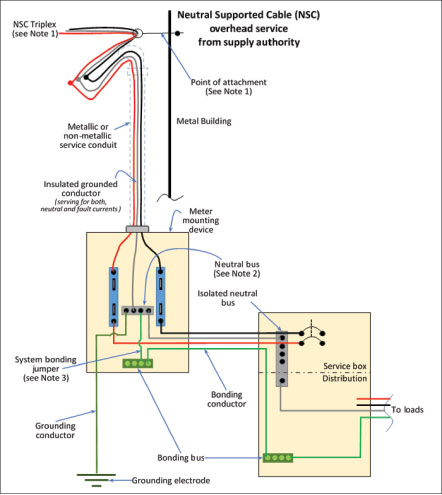
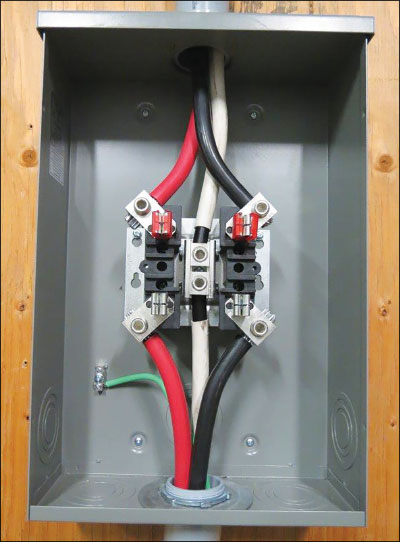
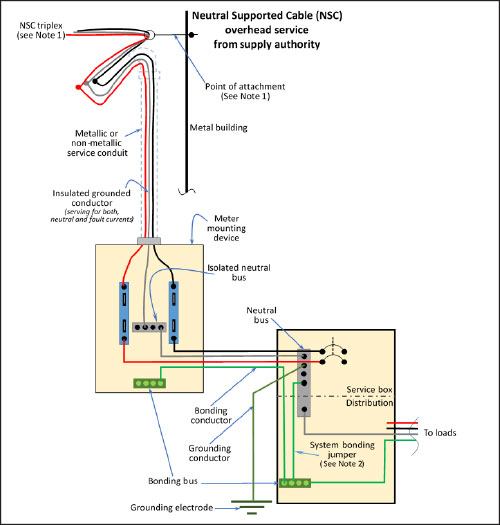
Rule 10-212 covers grounding connections for a solidly grounded separately derived system (with no direct connection to the circuit phase or neutral conductors of a supply authority system). Let’s start with Subrule (2); this subrule allows a separately derived ac system operating at 750 V or less to be grounded by the system bonding jumper only, when connected to the primary supply bonding conduactor. This new subrule deletes the previous 19-year-old requirement for a grounding electrode connection for a “different system” source rated in excess of 1000 VA [2015 CE Code Rule 10-206(3)]. Other than allowed in Subrule (2), Subrule (1) requires the grounded conductor of a solidly grounded separately derived system to have a connection to a ground electrode and a system bond jumper to connect the grounded conductor (neutral) to the equipment bonding terminal. The grounding electrode conductor and the system bond jumper are mandated by Subrule (1) to be at the source (output of the separately derived system), at the first switch controlling the separately derived system, or at a common tie point where more than one separately derived system terminates.
As an example, a permanently installed 600Y/347 3-phase 4-wire generator with a bond jumper installed between the generator neutral conductor and the generator bonding, will require a grounding conductor connection from the generator neutral and a grounding electrode, and either the neutral is not distributed, or the neutral is connected to distribution by use of a 4-pole transfer device.
Rule 10-400 details the next change; this harmonizes the requirements for ground indication and visible or audible alarms for both ac and dc ungrounded systems.
The next significant change can be found in Rule 10-606(2). This subrule does not permit reducing washers to be used as part of a bonding path. This will require the use of a bonding bushing to maintain the bonding connection between a raceway of cable connector and an enclosure.
Two new Subrules (5) and (6) have been added in Rule 10-612 that will require switches that are provided with a bonding terminal to have a bonding conductor installed between the device box and the bonding terminal on the device.
The size of bonding conductors and system bonding jumpers are now covered in Rule 10-614. The first main change here is the replacement of Tables 16A and 16B from the 2015 CE Code with a single Table 16. The bonding conductor is now sized based on either the ampere rating or setting of the overcurrent device, or the allowable ampacity of the largest ungrounded conductor or group of conductors.
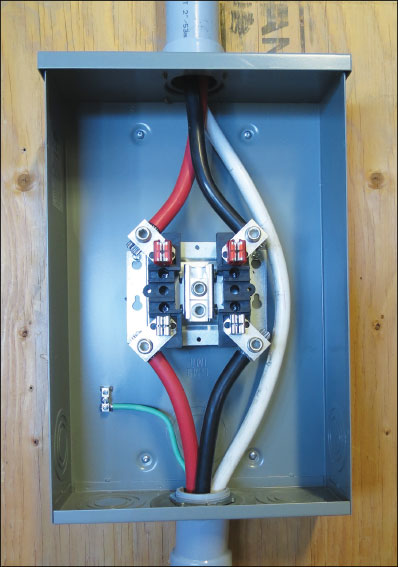
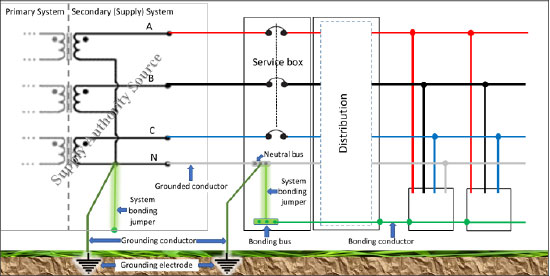
Subrule (1) requires a field installed system bond jumper (the conductor between the neutral and the enclosure bonding) to be sized using Table 16 and the ampere rating or setting of the overcurrent device protecting the ungrounded conductors. To illustrate an example, let’s look at the size of the field installed system bonding jumper for a 50kVA single phase transformer with a 600V primary and a 120/240V secondary. As indicated in an Appendix B note, the primary overcurrent protection and the ratio between the transformer primary and secondary voltage is used to determine the size of a field installed system bond jumper.
The first step is to determine the size of the overcurrent protection. Based on Rule 26-256, Subrules (1) and (3) allow the primary overcurrent protection to be 125% (or the next higher standard rating), and Subrule (2) allows the primary overcurrent protection to be set at not more than 300% with 125% overcurrent protection on the secondary. This would allow a 125 A primary circuit breaker (50,000/600 = 83.3 x 1.25 = 104.2 → 125A) or a 250 A primary circuit breaker with a secondary overcurrent device set not exceeding 125% (50,000/600 = 83.3 x 3 = 250 → 250 A).
The next step is to look at the ratio between the primary and secondary voltage. The ratio is 2.5 (600/240 = 2.5) This ratio is then applied to the primary overcurrent protection options. For this we will use three options: 100 A, 125 A, and 250 A. If a 100 A primary circuit breaker is used, the ratio would result in an ampacity of 250 A that would be used with Table 16. The 125 A primary circuit breaker would result in 312.5 A (125 x 2.5 =312.5) to be used and a 250 A primary circuit breaker would result in 625 A (250 x 2.5 – 625). When these ampacities are applied to Table 16, the field installed system bond jumper would be #4 AWG copper for the installation with the 100 A primary circuit breaker, #3 AWG copper for the 125 A primary circuit breaker, and 1/0 for the installation with the 250 A primary circuit breaker. As you can see, the size of a transformer primary overcurrent protective device can have a significant impact on the size of the field installed system bonding jumper.
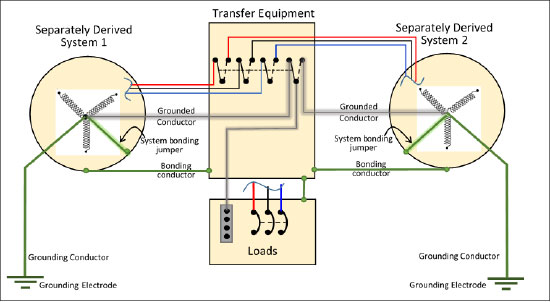
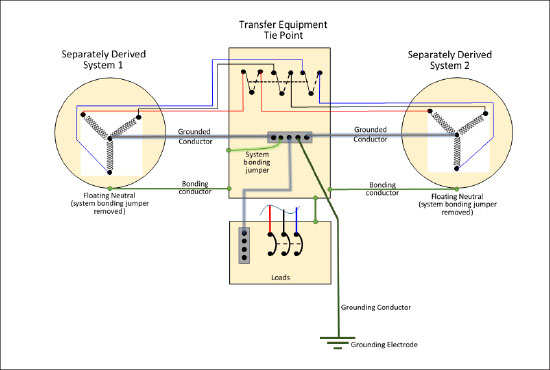
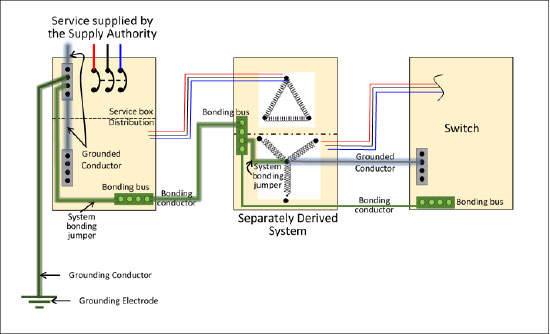
Subrule (2) requires the bonding conductor at service equipment (between the meter mounting device and the service box) to be based on the allowable ampacity of the largest ungrounded consumer’s service conductor. In this example, we will look at a 400 A consumer’s service with 600 kcmil copper insulated with a 75˚C allowable ampacity based on Table 2 of 420 A. The installation required allowable ampacity is used when the insulated ungrounded conductors have an insulation rating higher than the maximum termination temperature used to determine the allowable ampacity. As the allowable ampacity of the insulated conductor is above 400 A, the 500 A row in Table 16 is used to establish the bond conductor size of #2 AWG copper.
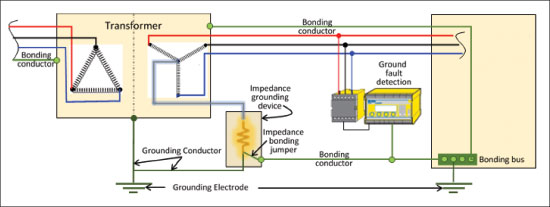
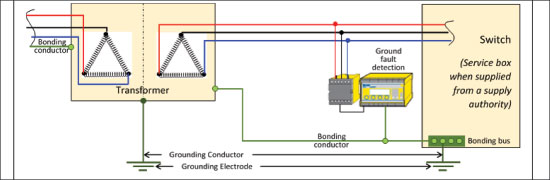
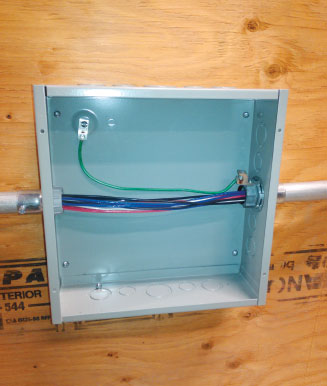
Subrule (3) provides details on where the first two columns of new Table 16 are used and mandates that for other than service equipment, field installed bond conductors are to be sized based on the rating or setting of the circuit overcurrent protection; or where circuit conductors are increased in size to compensate for voltage drop, the size of the bonding conductors are to be sized based on the allowable ampacity of the largest ungrounded conductor.
One of the main reasons for the new Table 16 was to address installations with parallel circuit conductors. Subrule (4) allows the size of bonding conductors selected in accordance with Subrule (3) to be divided by the number of groups of parallel conductors.
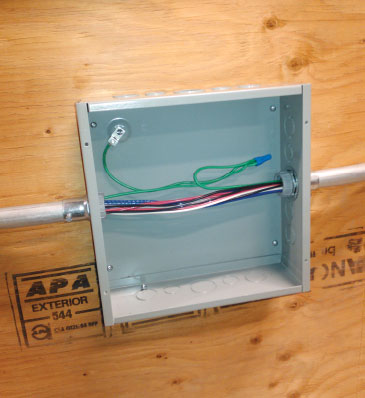
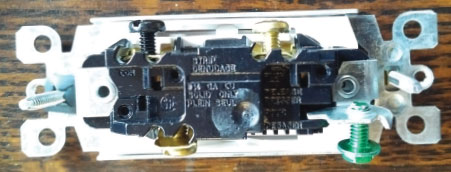
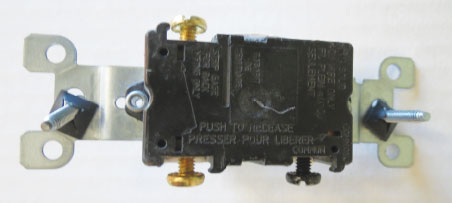
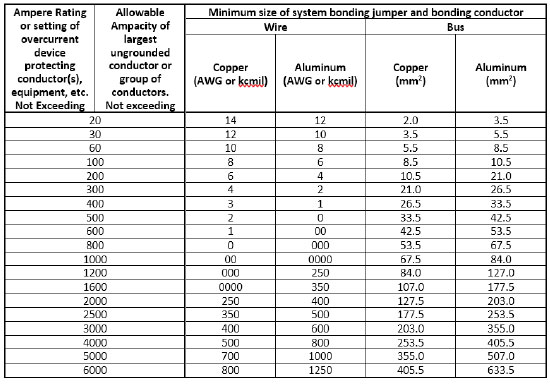
Other than the system bonding jumper, Subrule (5) allows bond conductors to be not larger that the current-carrying conductors.
Subrule (6) allows electrical metallic tubing and rigid metal conduit to be used as a bonding conductor, and Subrule (7) considers the bonding conductor that is an integral part of a cable as meeting the bonding requirements of Rule 10-614.
As an example, let’s look at the required size of a bonding conductor for a motor branch circuit installed in PVC conduit for a 25 HP 575 V motor with a full load current of 27 A and a KVA Code of G. Based on CE Code Rule 28-106, the minimum size of a 75˚C copper motor branch circuit conductor is #10 AWG. Based on CE Code Rule 28-200, the maximum time delay fuse is 45 A and the maximum non-time delay fuse is 80 A. Based on Table 16, the size of the copper bonding conductor for the motor branch circuit with the 45 A time delay fuse is a #10 AWG, and the size of the copper bonding conductor for the motor branch circuit with the 80 A time delay fuse is a #8 AWG. As the size of the bonding conductor is not required to be larger than the circuit conductors in accordance with Subrule (5), the bonding conductor need not be larger than #10 AWG. If the PVC conduit was replaced with a Tech 90 Cable with #10 AWG copper circuit conductors, the copper bonding conductor of #12 AWG that is integral with the cable will be acceptable based on Subrule (7).
The next article will cover CE Code changes for Sections 12 to 24.
The figures were used with the permission of Canadian Standards Association, (operating as “CSA Group”), 178 Rexdale Blvd., Toronto, ON, M9W 1R3, material is reproduced from CSA Group’s standard CSA C22.1-15 – Canadian Electrical Code, Part I (23rd edition), safety standard for electrical installations – Consolidated Memorandum of Revisions to the 2015 (23rd) edition. This material is not the complete and official position of CSA Group on the referenced subject, which is represented solely by the Standard in its entirety. While use of the material has been authorized, CSA Group is not responsible for the manner in which the data is presented, nor for any representations and interpretations. No further reproduction is permitted. For more information or to purchase standard(s) from CSA Group, please visit http://shop.csa.ca/ or call 1-800-463-6727.”
Find Us on Socials