Electrical safety requirements have often been described as a three-legged stool: (1) electrical installation codes, (2) electrical equipment maintenance standards, and (3) safety-related work practice standards. All three legs are equally important if the stool is to serve as a level, stable seating platform. All three are necessary to help ensure the reliability of electrical distribution systems and the safety of persons that operate and work on them. It is no surprise, therefore, that these codes and standards cross-reference each other. For example, the U.S. National Electrical Code cross-references NFPA 70E, Electrical Safety in the Workplace Standard in Article 110.16, and the Canadian Electrical Code cross-references the CSA Z462, Workplace Electrical Safety Standard in Rules 2-304 and 2-306.
NFPA 70E and CSA Z462 are, for the most part, developed in parallel and are technically aligned. This article will focus on four inter-related safety-related work practice requirements found in both documents: an electrical safety policy, risk assessment, human performance, and job safety planning and briefing.
by Daniel Roberts
Electrical Safety Policy
New to the 2021 editions of NFPA 70E and CSA Z462 is the requirement that an employer should create, document, and implement a policy for when electrical conductors and circuit parts must be placed in an electrically safe work condition. This condition is defined as “a state in which an electrical conductor or circuit part has been disconnected from energized parts, locked out in accordance with established standards, tested to verify the absence of voltage, and, if necessary, temporarily grounded for personnel protection.”[1] [2] The objective of such a policy is to provide a consistent understanding and expectation at all levels in an organization regarding when electrical equipment is to be placed in an electrically safe work condition.
The importance of an electrical safety policy cannot be understated. Rather than create and implement a policy, some employers rely on the electrical worker to make the decision to lockout equipment before beginning work. The mistaken belief is that these workers are aware of the statutory (i.e., legal) requirements and are sufficiently knowledgeable to uniformly make the correct decision every time. In reality, the decision will vary based on a range of human performance factors that include age, experience, workplace stressors, and workplace culture.
Other employers rely on a “NO LIVE WORK” policy. This is unrealistic. Electrical workers know that there are some tasks, for example, diagnostic testing and troubleshooting, that often cannot be performed when electrical conductors and circuit parts are in an electrically safe work condition. Verifying the absence of voltage during a lockout procedure is also “live work.” A “NO LIVE WORK” policy provides no organizational guidance regarding when electrical equipment is to be placed in an electrically safe work condition. Rather, it results in confusion between worker and supervisory or managerial levels. The electrical worker is left in a position where they must make the decision, which will be based on unreliable human performance factors.
The employer’s electrical safety policy must be clear and unambiguous. It should require that electrical conductors and circuit parts be placed in an electrically safe work condition before workers begin work involving an electrical hazard unless the task to be performed is not practicable in such a condition. Tasks that are not practicable would be limited to troubleshooting of control circuits, testing, and diagnostics that cannot be performed if electrical conductors and circuit parts are placed in an electrically safe work condition. The policy should expressly prohibit tasks such as installation, maintenance, modifications, or repairs on energized equipment.
Risk Assessment
The focus in the 2015 editions of NFPA 70E and CSA Z462 changed from “hazard analysis” to “risk assessment.” An employer must have a risk assessment procedure to be used before work is started to identify hazards, assess risk, and implement risk control according to the hierarchy of risk control methods. This shift was influenced by risk assessment terminology and methodology found in standards such as ISO 31000:2009 Risk management — Principles and guidelines, ISO Guide 51 Safety aspects — Guidelines for their inclusion in standards, ANSI Z10-2012 Occupational Health and Safety Management Systems, and CSA Z1002-12 (R2017), Occupational Health and Safety – Hazard identification and elimination and risk assessment and control.
As can be seen from the diversity of the referenced standards, risk assessment applies in many spheres of activity. Annex F of both NFPA 70E and CSA Z462 provides a generic overview of risk assessment and risk control and then explains how this applies to occupational health and safety, and specifically, to workplace electrical safety. Risk assessment involves:
- Hazard identification: Find, list, and characterize hazards (i.e., sources with the potential to cause harm)
- Risk analysis: A level of risk is established by combining:
- an estimation of the likelihood that harm might result from a hazard
- an estimation of the potential severity of that harm
- Risk evaluation: The level of risk is evaluated to determine if the objective of freedom from harm can reasonably be met by the risk control that is in place or if further risk control is required
Risk assessment can be hazard-based, task-based, or a combination of the two. An activity where the hazard-based approach is typically used is the workplace safety inspection. An activity where a combination of the two methods might be used is during the design or re-design of a product, service, or process. The risk assessment procedure that NFPA 70E and CSA Z462 require a worker to use is the task-based approach. This concept will be discussed in the Job Safety Planning and Briefing section of this article.
Risk assessment tends to be a subjective exercise, particularly the risk analysis, estimation, and evaluation steps. To reduce subjectivity, Annex F advocates a binary approach to risk estimation and evaluation whereby there are only two choices for the likelihood of occurrence and two for the severity of the outcome. The choices are based on higher-order risk control methods that do not rely on human performance factors such as skill, awareness, or alertness. This approach is based on the Haddon injury causation model [3]. Mr. Haddon proposed that all injuries are causally in one of two groups: (1) deprive the body of needed energy (e.g., oxygen); or (2) deliver to the body amounts of energy (e.g., electric current) that exceed the corresponding local or whole-body injury threshold. Applying the latter:
- The likelihood of contact with energy is either possible or improbable based on whether the source is guarded or unguarded. Whether the source is guarded or unguarded is based on the requirements of a code, standard, or law such as enclosure ingress guarding requirements published in NEMA or IEC standards.
- The severity of harm is either negligible or severe based on whether the threshold of energy that could be delivered to the body is equal to or greater than that specified in a code, standard, or law. An example is the shock hazard voltage thresholds found in NFPA 70E (equal to or greater than 50 V) and CSA Z462 (greater than 30 Vac or 60 Vdc).
When a “possible” level of likelihood is combined with a “severe” level of severity, the result is a “high” level of risk (see Figure 1), which must be reduced by applying the hierarchy of risk controls.
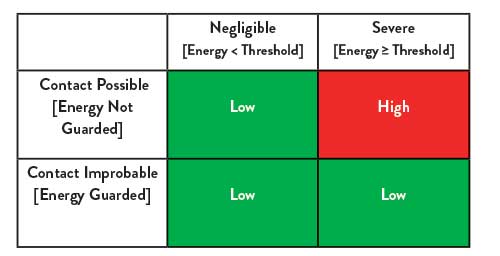
The purpose of specifying and adhering to a hierarchy of risk control methods is to identify the most effective individual method or combination of methods to reduce the risk associated with each hazard or hazardous situation. Each risk control method is considered less effective and reliable than the one before it. Annex F lists the hierarchy of six control methods specified in NFPA 70E and CSA Z462 and provides examples of each. It should be noted that some standards such as ISO 45001:2018 Occupational health and safety management systems — Requirements with guidance for use, list only five risk control methods; Awareness and Administrative controls are referred to collectively as Administrative controls.
- Elimination – conductors and circuit parts are in an electrically safe working condition
- Substitution – use of 24 V A.C. or V DC rather than 120 V control circuitry
- Engineering controls – Guard energized electrical conductors and circuit parts to reduce the likelihood of electrical contact or the occurrence of arcing faults
- Awareness – signs alerting of the potential presence of hazards
- Administrative controls – procedures, job planning, and briefing tools
- Personal Protective Equipment (PPE) – shock and arc flash PPE
Human Performance
NFPA 70E and CSA Z462 require the employer’s risk assessment procedure to “address the potential for human error and its negative consequences on people, processes, the work environment, and equipment relative to the electrical hazards in the workplace.” The method by which “human error and its negative consequences” are addressed is called human performance. This concept was introduced to CSA Z462 in the 2015 edition and to NFPA 70E in the 2018 edition. NPFA 70E and CSA Z462 Informative Annexes Q and U, respectively, elaborate extensively on the concept of human performance and how it can be applied to workplace electrical safety.
- First developed in high-risk industries such as nuclear and aerospace, human performance seeks to reduce workplace incidents by:
- Acknowledging that people are fallible – we all make mistakes
- Identifying and managing, or preventing situations in which error is more likely
- Influencing individual performance through organizational processes and values
- Encouraging and reinforcing high levels of performance through feedback and modeling from leaders, peers, and subordinates
- Applying lessons learned (i.e., continuous improvement).
Risk assessment and human performance are linked: risk assessment is a decision-making method, and human performance is rooted in the psychology of decision-making. There are two mental processes by which we make decisions and carry out activities – the automatic process and the controlled process [4].
The automatic process is the default decision-making process – it is intuitive, quick, and easy. This process is at work when we execute tasks that can be done without conscious thought. Examples include tying our shoes or typing without looking at the keyboard (i.e., “touch-typing”). The following are some of the inherent biases of the automatic process that could affect workplace safety:
- It underestimates the likelihood of occurrence and significantly underestimates the severity of the outcome.
- It focuses on existing evidence and ignores absent evidence (a concept known as “What You See Is All There Is”).
- It neglects ambiguity and suppresses doubt.
In human performance language, the automatic process is referred to as the “skill-based mode” of task execution. Performing tasks in the skill-based human performance mode place a relatively low demand on attentional resources. This can result in inattention, a perceived reduction in risk, or both. When an incident investigation report concludes that an injury occurred due to “worker inattention,” it misses the point: We are incapable of 100% focus 100% of the time.
The controlled process is governed by conscious thought; it is slow and requires purposeful effort. It is NOT the default decision-making process. In human performance language, this is referred to as the “knowledge-based mode” of task execution. This mode is used when no skill or rule is readily identifiable. The individual relies on their understanding and knowledge of the situation and related scientific principles and fundamental theory to develop an appropriate response. Common errors that occur when operating in knowledge-based mode include an inaccurate mental picture of the work situation, poor decision making during high stress, the tendency to use only readily available information to evaluate the situation and to become enmeshed in one aspect of the problem to the exclusion of all other considerations. This mode is not ideal in safety-critical situations where a decision cannot be reversed, and the consequence is severe.
There is a third human performance mode known as the “rule-based mode” of task execution. This mode involves applying memorized or written rules to execute tasks when the work situation is covered by training or a procedure. The rules may have been learned through interaction at the workplace, formal training, or by working with experienced workers. Executing tasks in the rule-based mode requires more attentional resources than the skill-based mode. An individual functioning in the rule-based mode will usually react in a predictable manner. According to human performance theory psychologist James Reason, rule-based is the most desirable human performance mode in those safety-critical situations where a decision cannot be reversed, and the consequence is severe [5].
Since we do not naturally gravitate toward rule-based mode, there are human performance tools that facilitate the execution of safety-critical tasks in this mode. Some common examples of human performance tools include the pilot’s pre-flight checklist, patient identification wristbands (the next time you are in a hospital, take note of how frequently medical staff checks a patient’s wristband to verify a patient’s identity), three-way communication (an information exchange confirmation feedback technique), and alerting or blocking techniques such as barricades or barriers.
Job Safety Planning and Briefing
The job safety planning and briefing requirements of NFPA 70E and CSA Z462 bring together risk assessment and human performance.
Job safety planning is a task-based risk assessment. The job is defined and broken down into individual tasks, hazard(s) are identified for each task, the risk associated with each hazard is analyzed, estimated, and evaluated, and risk control is selected and implemented. This logical sequence is followed in the prescriptive job safety planning and briefing requirements of NFPA 70E and CSA Z462. Before beginning work that involves an electrical hazard, a job safety plan must:
- Be completed by a qualified person
- Be documented and include the following information:
- A description of the job and the individual tasks
- Identification of the electrical hazards associated with each task
- A shock risk assessment for tasks involving a shock hazard
- An arc flash risk assessment for tasks involving an arc flash hazard
- Work procedures involved, special precautions, and energy source controls
The worker in charge is required to conduct a job briefing of the job safety plan with all the workers involved. If during the course of work, changes occur to the scope of work that might affect the safety of workers, then the job safety plan must be revised accordingly, and additional job briefings are required to be held.
Examples of human performance tools used for job safety include:
- Job safety planning and briefing checklists and forms
- Requesting feedback from workers during a job briefing
- A post-job review to identify opportunities for improvement
- Temporary barricades or barriers that provide awareness or prevent access
Conclusion
The four interrelated safety-related work practice requirements of NFPA 70E and CSA Z462 that were discussed in this article are supplemented by many other safety-related work practice requirements. These include but are not limited to electrical safety training requirements, work practice audit requirements, shock and arc flash boundary and PPE requirements, lockout requirements, and the steps to help create an electrically safe work condition. Although these are U.S. and Canadian standards, respectively, they are widely used in Central and South America and are referenced in guidelines and standards found in Australia and South Africa. Electrical inspectors are in a unique position to promote the use of these two standards as routine practices for workplace electrical safety.
References
[1] CSA Z462:21, Workplace electrical safety
[2] NFPA 70E Electrical Safety in the Workplace
[3] Haddon, William Jr.; A Note Concerning Accident Theory and Research with Special Reference to Motor Vehicle Accident; Annals of the New York Academy of Sciences; 1963, Vol 107; p. 635-646
[4] Kahneman, Daniel; Thinking, Fast and Slow; 2011
[5] Reason, James. Managing the Risks of Organizational Accidents, 1998
This article was provided by the Canadian Standards Association (CSA Group). The author, Daniel Roberts, is Chair of the CSA Z462 Technical Committee, a voting member of the Canadian Electrical Code Technical Committee, Past Chair of the IEEE IAS Electrical Safety Committee, and author of several peer-reviewed and published papers on risk assessment, human performance, and safety management systems.
Copyright © CSA Group. All Rights Reserved.
Find Us on Socials