A formal plan review process and plan reviewers are not found in numerous smaller jurisdictions due to budget constraints and the perceived lack of need for such activities. This is probably an acceptable situation where routine inspections involve residential electrical systems and the smaller commercial systems. Those electrical systems have remained essentially unchanged for decades with the exception, of course, of equipment such as arc-fault circuit interrupters and ground-fault circuit interrupters and the like. The load center that I installed in 1960 in the home I grew up in is nearly identical to the load center I installed in my retirement home in 2010. Yes, each edition of the National Electrical Code (NEC) provides changes in the requirements for residential and commercial electrical installations, but the equipment is very similar from year-to-year and the methods of installing that equipment are very familiar to the electricians and inspectors. The electrical contractors are familiar with the equipment and installation procedures and although there are differences from installation to installation, there are many similarities. Mistakes in the installation occasionally get made and are found by the inspectors, corrected and are not made in future installations, hopefully, by the same contractor.
However, we now have the ubiquitous photovoltaic (PV) power system springing up in numerous neighborhoods on residences and commercial buildings throughout the country. The photovoltaic (PV) industry is dynamic and fast changing. New PV modules are being released on a monthly basis and each new module has a different size and different ratings. New inverters and other equipment are also coming to market with significant frequency. Although the equipment is connected with the conductors and uses overcurrent devices that we are familiar with, the outdoor environment and the rapidly changing equipment generally point to the need of some sort of plan review process to ensure that the somewhat unique PV Code requirements are being met.
Most inspectors would agree that an unfamiliar installation, a new contractor, and unfamiliar equipment as well as new and slightly different code requirements dictate that a longer-than-usual inspection may be required. In fact, it is difficult when inspecting the typical PV system as installed in the field to fully ascertain that all the code requirements have been met. The modules are fastened to the roof and the rating labels cannot be seen so the ratings for open-circuit voltage (Voc), short-circuit current (Isc), and maximum protective overcurrent device cannot be verified (photo 1). The wiring is typically behind the modules or in conduit and the markings on the conductors in many cases cannot be verified and, like the module labels, some of the equipment such as combiners is not readily accessible (photo 2).
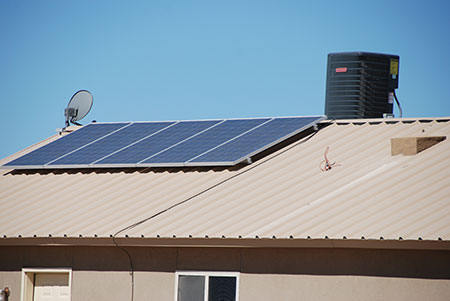
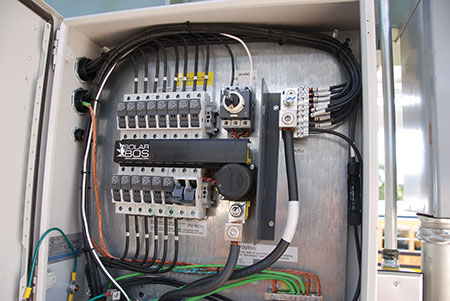
Even without a formal plan review process or dedicated plan reviewers, it would behoove the typical inspector to spend a few minutes in the office with the permit application and the plans, which will be described shortly, and verify that, at least, on paper the proposed PV system meets code requirements.
The Plan
Of course, in order to do a plan review there must be a plan. Many jurisdictions do residential electrical permitting across the counter with no substantial, detailed plans required for the electrical system. A form is filled out, the fee is paid, and the permit is issued. At some point, an inspection is requested and the inspector makes the inspection and either approves or disapproves the installation. While this works for normal residential and some small commercial electrical installations where the equipment and Code requirements are fairly well standardized, it is probably not the best option for PV installations, as noted above, where the equipment and the installation techniques are changing frequently.
Some jurisdictions are adopting an expedited PV permitting process for PV systems under 10 KW. This expedited permitting process usually includes a diagram and other information and is, in some cases, based on the process described on the SolarABC’s website. That expedited permitting report can be found at: http://www.solarabcs.org/about/publications/reports/expedited-permit/index.html.
The following paragraphs contain some suggestions that I have found useful when performing a plan review to determine if the basic design of the PV system meets minimum code requirements. Figure 1 shows a three-line diagram of a small PV system with a single string of modules as an example.
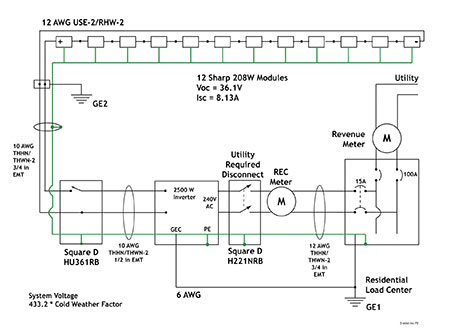
Diagram and Other Information
This diagram should be accompanied by several additional pieces of information. An installation instruction manual for the PV module should be included along with a specification sheet for the module since frequently the specifications are not contained in the instruction manual. An installation instruction manual for the utility-interactive inverter should also be included along with an instruction manual for any dc combiner, where such a combiner is used to combine source circuits. Cut sheets should be provided to show the ratings of all disconnects and overcurrent protective devices used in the system. Information should be provided on the ratings of any existing electrical equipment such as load centers that the PV system will be connected to or that PV ac currents may pass through all the way from the PV inverter output to the service entrance conductors.
Module Grounding
Starting with the PV module, a grounding detail that is going to be used to ground the module frames should be provided on or with the diagram, and this grounding detail should be consistent with the grounding instructions provided in the module instruction manual. If the module is not grounded in a manner consistent with the module instruction manual, the listing on the module will be invalid. And, of course, since the NEC requires that the module be certified/listed [690.4(D)], then the installation of an unlisted module no longer meets NEC requirements. A frequent problem in this area is the use of some sort of a grounding device that does not use the marked grounding holes shown in the module instruction manual and the instruction manual makes no mention of grounding the module at positions other than the marked grounding holes.
Module Mounting
In a similar manner, a mounting detail for the PV module should be included with the diagram. This mounting detail should be consistent with the mounting instructions for the PV module. Again, if the module is not mounted according to the module instructions, the listing is invalid and the module installation does not comply with the requirements of the NEC. The use of a mounting device that has top clips to mount the modules has become common recently (photo 3). The module instruction manual must show the use and location of top clips for mounting the module if this mounting system is to be acceptable and the installation to remain code-compliant. This alternate mounting system will be in addition to the normal mounting holes that are drilled in the back frame of the module that are normally used for mounting. See “Perspectives on PV” in the September–October 2012 issue of the IAEI News for details on module mounting and grounding.
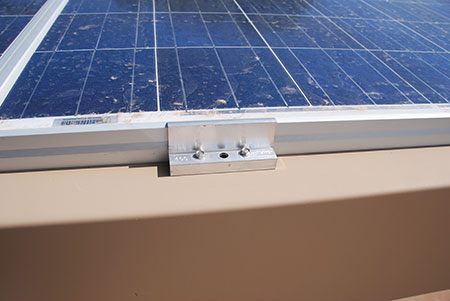
Racking Systems
Underwriters Laboratories (UL) Outline of Investigation 2703 details a list of performance requirements for PV racking and mounting systems. Although the Code does not require racking or mounting systems to be certified/listed, a racking system that complies with this Outline of Investigation will ensure that the racking system is structurally robust and that the racking system can be used as an equipment grounding conductor. The certification/listing of the racking system to UL 2703 does not, however, automatically guarantee that the racking system and its module mounting and module grounding provisions meet code requirements. At this time, both the racking system instructions and the module instructions must indicate that these two devices have been evaluated together as a system in order to ensure that the mounting of the module to the racking system and the grounding of the module to the racking system comply with all provisions of both standards and, therefore, will meet the requirements of the NEC. See the “Perspectives on PV” in March–April 2014 issue of the IAEI News article for more details on modules and racking.
Cold-Weather, Open-Circuit Voltage
The diagram should show the number of PV modules connected in series for each string. The specification sheet for the modules should show the open-circuit voltage (Voc) at standard test conditions (STC) and the plans should show a calculation using the expected lowest temperature at the installation site to calculate, along with the module temperature coefficient, a value of the highest open-circuit voltage from the string under open-circuit conditions at the coldest expected temperature. See “Perspectives on PV” the January–February 2009 issue of the IAEI News for more details on this calculation. This open-circuit voltage in cold weather should be lower than the maximum voltage of any equipment connected to the modules including the modules themselves, the dc source and dc output circuit conductors, ratings of any switchgear and overcurrent protective devices, and the maximum dc voltage input of the inverter. This equation, and the numbers that went into it, can be shown as a single line of numbers and an equation on the diagram.
Conductor Conditions of Use
The conductors from the PV modules to the inverter will pass through several different areas on or in the building; each area will have a different set of conditions of use. At some places, they may be in free air behind the modules in the shade or in sunlight. See photo 4. At other locations, they may be in conduit. In some locations, the conduit will be in sunlight close to the roof and at other locations the conduit may be significantly above the roof but still in sunlight and frequently the conduits will be in shade on the roof. Usually, at some point, the conduit will be inside conditioned space as it is routed to the inverter. The diagram should be annotated to show these different conditions of use and the temperatures and spacings from the roof expected in each segment of the conductor run. Of course, the worst-case conditions of use will be applied to determine the conductor size. It should be noted that, in some installations, the conductor size for the field-installed conductors may exceed the size of the conductors attached to the modules themselves because the conditions of use for the field-installed conductors and conduit in sunlight may be more severe than those associated with the conductors attached to the modules which are typically in free air. An ampacity calculation showing the conditions of use and the required conductor size should be shown for each separate condition of use or at least the worst-case conductor size and that calculation should be shown (310.15).
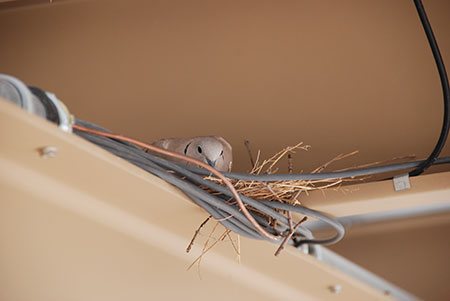
At the DC PV Disconnect and the Inverter
The inverter instruction manual should be consulted to determine whether the inverter is to be used with a grounded or ungrounded PV array. An inverter designed for use with a grounded PV array would be called an isolated inverter. The term isolated comes from the fact that an internal transformer isolates the ac circuits from the dc circuits (including the grounded conductors) in the inverter. A non-isolated (transformerless) inverter would require the use of an ungrounded PV array.
A grounded PV array that uses an isolated inverter must have only the ungrounded PV dc source (or dc output) circuit conductor switched through the disconnect. The actual connection to ground of one of the PV circuit conductors (either the positive or negative depending on the PV module grounding requirements) will be done inside of the inverter by the required NEC Section 690.5 ground-fault protection device built into the inverter. If the PV system has an ungrounded PV array, the inverter will be a non-isolated inverter and both positive and negative conductors of the PV array output must go through the disconnect and be switched.
The system that uses a grounded PV array and the isolated inverter must show (on the diagram) a dc grounding-electrode conductor routed from the inverter to the first panelboard or load center which has a grounding busbar with a grounding electrode conductor routed to a grounding electrode. NEC Section 690.47(C) shows the various ways that the dc PV grounding electrode conductor may be routed and connected.
Inverter AC Output Circuit
The conductor from the inverter output to the first overcurrent device must meet the requirements of NEC Section 690.8 for size. And, the overcurrent device itself should be rated according to the requirements of Sections 690.8 and 690.9 of the NEC. The conductor sizes for the ac output circuit of the inverter including any conductor downstream of the inverter after the first overcurrent device that may carry both inverter output current and utility current must comply with NEC Section 705.12(D). Someplace in the permitting package, the calculation should be shown for each circuit involved all the way back to the service-entrance equipment. Backfed circuit breakers in each panelboard or load center that will handle PV current should be marked on the diagram showing their correct location, which in most cases will be at the opposite end of the busbar from the main breaker or main lugs for that panelboard. The “Perspectives on PV” article in the January–February 2013 issue of the IAEI News deals with load-side PV connections to the utility under the 2011 NEC and the January–February 2014 article covers the load-side connections under the 2014 NEC. The November–December 2013 article deals with supply-side connections.
The Inspection
With the some of the Code requirements verified during plan review, the field inspection will usually go much smoother. Code requirements that are found not to be met on paper may be flagged for the installer, and they should be corrected before taking valuable time going to the site and attempting to ensure that everything meets Code by a visual inspection of the installation. I have reviewed several hundred plans for PV systems over the last 24 years (5 kW to 4 MW) and note that many systems fail to meet all NEC requirements on paper. The systems that do comply with the NEC requirements are usually plans from PV installers/systems integrators that have been in business a number of years and have been installing similar systems over that period.
Summary
PV installations differ from normal residential electrical installations in that the equipment is rapidly changing in form, fit, and function and the NEC requirements for these installations are somewhat different and are constantly evolving. Detailed plans are required to fully evaluate code-compliance and these plans are best evaluated prior to the field inspection. Time spent in the office reviewing a good, detailed PV plan submitted as part of the permit application will allow the AHJ to be more efficient and more effective. A checklist showing NEC requirements for the installation of PV systems may be downloaded from the author’s web site below.
For More Information
The author has retired from the Southwest Technology Development Institute at New Mexico State University, but is devoting about 25% of his time to PV activities in order to keep involved in writing these “Perspectives on PV’ articles in the IAEI News and to stay active in the NEC and UL Standards development. Seven to eight hour presentations are still available on PV and the Code and they cover 2008–2014 NEC requirements. He can be reached at: e-mail: jwiles@nmsu.edu, phone: 575-646-6105
The Southwest Technology Development Institute web site maintains a PV Systems Inspector/Installer Checklist and all copies of the previous “Perspectives on PV” articles for easy downloading. A color copy of the latest version (1.93) of the 150-page, Photovoltaic Power Systems and the 2005 National Electrical Code: Suggested Practices, written by the author, may be downloaded from this web site: http://www.nmsu.edu/~tdi/Photovoltaics/Codes-Stds/Codes-Stds.html .
Find Us on Socials