In the September/October 2020 edition of IAEI News, the Steel Tube Institute gave us an excellent review of corrosion, National Electrical Code® (NEC®) references, and requirements, and methods to mitigate the effects of corrosion. It was noted that galvanic action between dissimilar metals is also corrosion because of a different and more unique set of conditions. In this follow-up article, we will try to answer some common questions, take a closer look at how the manufacturers of steel conduit and tubing address corrosion, and offer additional specific potential solutions to ward off the effects of corrosion. This discussion will focus on rigid metal conduit (RMC), intermediate metal conduit (IMC), and electrical metallic tubing (EMT).
Common Questions:
- “HOW LONG WILL IT LAST?”
- No manufacturer can give a reliable estimate of how long any installation will last. There are simply too many variables, such as:
- How was the product transported, stored, and handled after it left the factory? – – Will the environment be damp, wet, marine, or laden with corrosive vapors?
- How qualified is the installation crew?
- Will it be in contact with soil, rock, or masonry?
If in a trench, what is used as backfill, and is there other debris? - Are there other metal objects in proximity that might contribute to galvanic action?
- No manufacturer can give a reliable estimate of how long any installation will last. There are simply too many variables, such as:
What can be said is that a product that is selected carefully and correctly and is installed per the NEC and manufacturer’s recommendations should give decades of exceptional service.
- “DO I HAVE TO USE SUPPLEMENTARY CORROSION PROTECTION?”
This question was addressed in the previous article. We will expand on some specifics a bit later. - “WHAT HAPPENS IF I INSTALL THIS OUTDOORS, UNDERGROUND OR IN CONCRETE?”
Again, addressed previously. - “CAN I USE STEEL CONDUIT WITH ALUMINUM FITTINGS?”
We will explain in more detail why this isn’t a concern. - “HOW CAN I REDUCE THE CHANCES OF CORROSION?”
There are numerous products and techniques to mitigate the effects of a corrosive or galvanic environment. Keep reading.
Manufacturing to the Standards
It was noted that steel conduit and EMT are provided with a coating of zinc galvanizing for corrosion protection. But why zinc and not some other coating? Zinc provides protection in two ways: It corrodes much slower than steel, and it is sacrificial to steel on the galvanic scale. In addition, zinc provides better environmental protection than paint; it adheres very well to steel, forming a tight bond, and that interface slows potential corrosion. It should be noted that when zinc corrodes, the result is a whitish residue, while steel rust is red. If you find white dust on galvanized products, that indicates that the zinc is doing its job and is protecting the steel beneath.
The UL® standards addressing RMC (UL 6), IMC (UL 1242), and EMT (UL 797) contain requirements for all these products to have corrosion protection as a condition of the listing. (These products are required to be listed per their respective NEC Articles). The standards require that the protective layer of zinc cover completely, adhere firmly at all points, and be smooth and free of blisters and other defects, and they must pass a copper sulfate test called the Preece test. Manufacturers can use any of the primary protective coatings and whatever process they choose (hot-dip galvanizing, in-line galvanizing, electroplating, etc.) as long as the product passes the performance requirements of the standard.

All three UL standards permit the use of alternate corrosion-resistant coatings. An alternate corrosion-resistant coating is defined by UL as a primary coating other than one consisting solely of zinc. As a primary coating, they are required to provide equal or greater protection to the exterior of the conduit/tubing than provided by a coating consisting of zinc only. This is completed by performing a 600-hour salt spray, moist carbon dioxide-sulfur dioxide-air, and ultraviolet light/water tests. Most U.S. manufacturers of EMT and IMC use an alternate corrosion-resistant coating to ensure the best possible corrosion resistance is applied to their products. Typically, an alternate corrosion-resistant coating will consist of at least three layers of protection.
The first layer of protection is usually zinc and is applied directly to the steel, as described earlier in the article. A conversion coating is then applied over that zinc that generally consists of trivalent chromium; the conversion coating is a protective surface created by a chemical reaction between the chromium and the zinc. The third layer is a thin topcoat that is generally a lacquer or some other organic coating that helps with corrosion protection. The organic topcoat is tested for electrical continuity and flexibility and undergoes a flame test. (Organic simply refers to the composition of the coating. It could be a carbon-based chemical compound such as paint, wax, polymer, etc.)
Similarly, organic coatings may be used on the interior of the conduit/tubing in place of a zinc coating and are used by all U.S. manufacturers on EMT and IMC. If an organic coating is used, it must provide the same level of protection as the zinc coating.
Threaded ends of RMC and IMC are provided with corrosion protection from the factory. Since the conversion and top coatings are optional, it would be wise to verify that the product you are installing utilizes these protection techniques to maximize the life of the installation, especially when installed in corrosive environments.
For severe corrosive conditions, the UL standards allow manufacturers to use supplementary coatings. A supplementary coating is a coating in addition to the primary coating; an example would be PVC-coated conduit. It is important to review the markings for supplementary coatings. Manufacturers are required to identify if the corrosion protection properties of the coating have not been investigated.
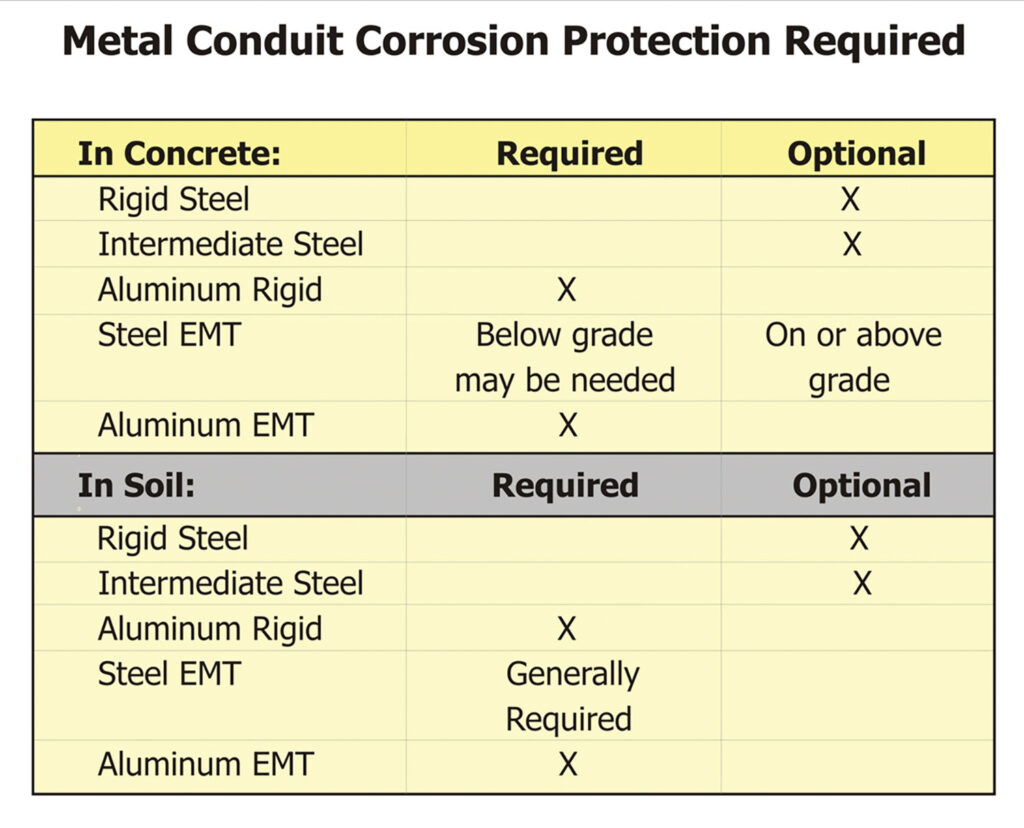
The NEC contains provisions in 342.10(B), 344.10(B)(1), and 358.10(B)(1) requiring approved corrosion protection for these raceways. Per the listing requirements, the raceways are provided with corrosion protection from the factory, so to comply with the basic rule only requires installing a listed product. Of course, “approved” is still the purview of the authority having jurisdiction.
There are locations in the NEC that require supplemental corrosion protection, generally for any aluminum product installed in concrete, in the earth, or in severely corrosive atmospheres. EMT also has requirements for supplemental corrosion protection in 551.80(B) for Recreational Vehicle Sites. In addition to the NEC’s minimum requirements, there are situations where supplemental protection is advisable or recommended by the UL Guide Card for the product. The following matrix offers recommendations:
Providing Supplemental Protection
Where required or desired, the application of supplemental protection should follow recommendations from the manufacturer. Supplemental protection may be provided in a number of ways:
- Paint
- Tape
- Field-applied shrinkable covering
- Factory-applied PVC coating
Paints should be either zinc-rich or be acrylic, urethane, or weather-stable epoxy resins. A tar-based bitumastic coating is also acceptable, but oil-based or alkyd paints are unacceptable. The surface of the conduit or tubing should be prepared prior to the application of any painted-on coating by washing, rinsing, and drying the surface to remove dirt, oils, and other contaminants. It is advisable to wear rubber gloves during this process so as not to re-contaminate the surface with oils normally present on hands. We must emphasize NOT to abrade, scratch, scuff, or media-blast the surface, as this will compromise the factory corrosion protection. Finally, the final coating should be applied and allowed to thoroughly dry or cure.
A primer compatible with the paint or two coats will provide significantly more protection. If you are not using an electrically conductive primer or paint, remember to tape or protect the threads and ends of the conduit or tubing to maintain the required grounding and bonding continuity of the raceway system. Note that this process is important for the long-term sustainability of the coating for additional corrosion protection. Painting for aesthetic purposes in a non-corrosive/climate-controlled environment is less critical. RMC, IMC, and EMT are available in factory colors, which might be more advantageous than painting in the field.
Tapes should be of the high-tack variety, overlap, and completely cover the surface. Depending on the product, a primer might be necessary to obtain the intended adhesion. Standard electrical tape is not intended or adequate for this purpose. There are also shrink-wrap products that will provide an effective barrier against the corrosive environment, both heat activated and systems that do not require heat.
Photo 4a and 4b. Example of a shrink-wrap that does not require heat.
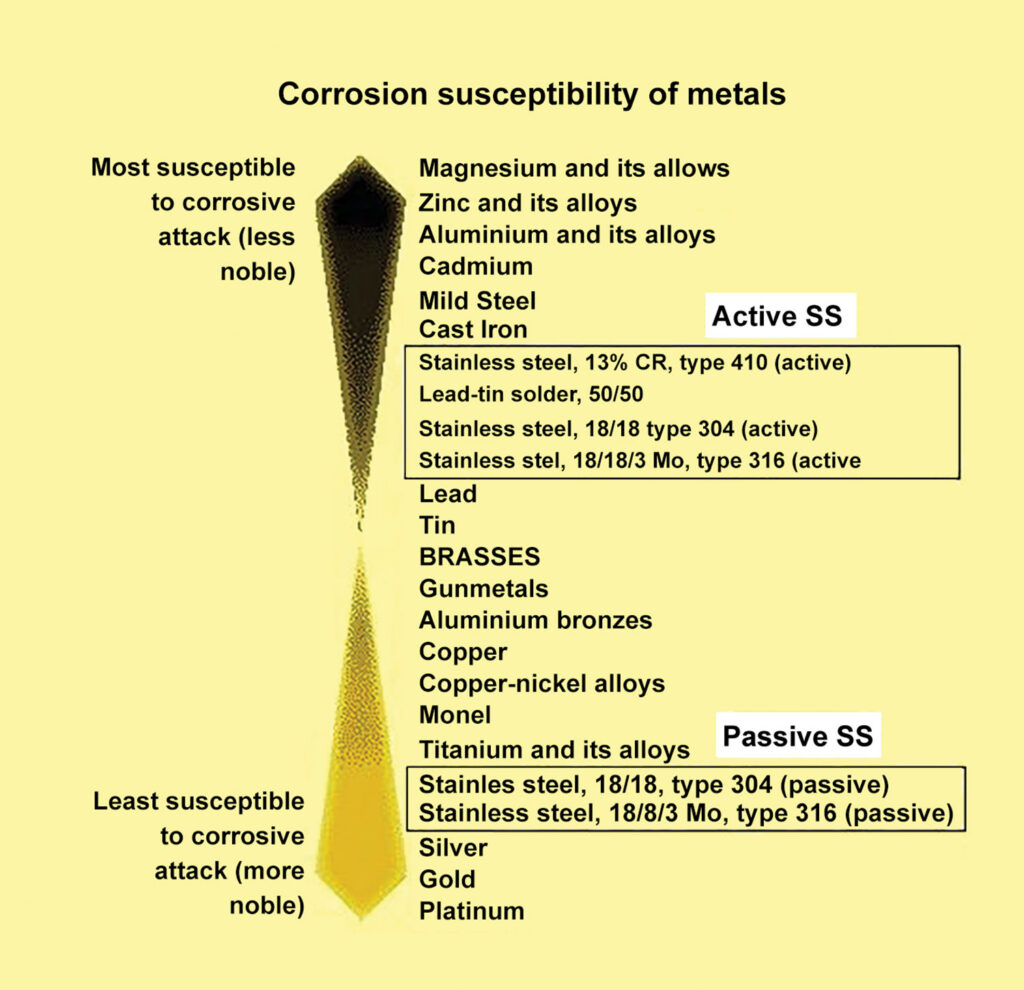
The Dual Personalities of Stainless Steel
Stainless steel (SS) is a material consisting primarily of steel, but with varying amounts of chromium added, along with other materials such as nickel, titanium, molybdenum, nitrogen, etc. These additional elements make stainless steel raceways nonmagnetic, but it is still considered to be a ferrous metal. The amount and mix of chromium and other elements yield different qualities of stainless. For instance, stainless steel Grade 304 is common for automotive and general use, whereas Grade 316 is common for marine and corrosive conditions/applications. Regardless of the final compound, stainless steel offers excellent resistance to corrosion.
The property that makes stainless steel extremely resistant to corrosion is a very thin layer of chromium-rich oxide film that forms on the surface. Although extremely thin, this layer is “self-healing” as long as there is sufficient oxygen present to reform the barrier. Stainless steel in this condition is said to be in a passive state. When there is insufficient oxygen, the stainless steel is said to be in the active state and is much more susceptible to corrosion. The previous article introduced the galvanic scale of metals, itemizing them from anodic to cathodic. Stainless steel is shown in the chart as being highly cathodic; however, note that the chart indicates that the stainless steel is in the passive state. This chart shows the relative resistance to corrosion and galvanic action of stainless steel of varying grades in both the active and passive states. Observe that stainless in the active state is much closer to the anodic end of the scale and is, therefore, more prone to rust and electrolysis.
To further complicate the discussion, the same piece of stainless steel can exist in both states along its length. The active state is likely to exist in oxygen-poor environments such as in stagnant water, non-moving water where the oxygen might be depleted trying to repair the surface film, or an atmosphere containing other compounds that displace the oxygen normally found in the air.
Table 1 shows the relative likelihood of galvanic action between different metals.
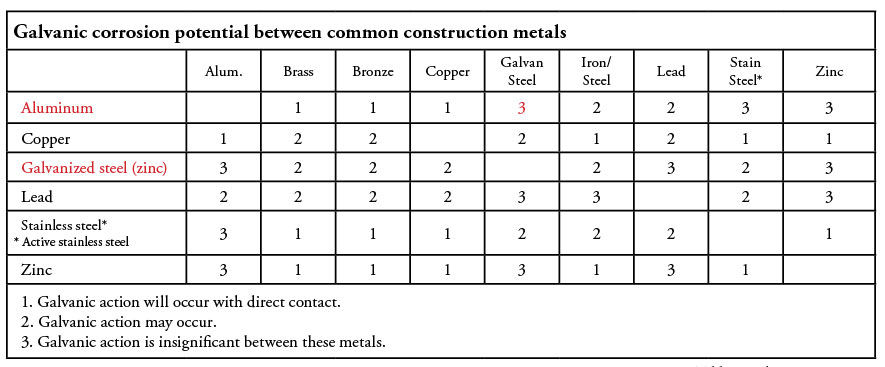
The above matrix might seem contradictory to earlier statements regarding the properties of stainless-steel regarding corrosion potential, but we are looking at two different scenarios: Passive stainless steel has excellent corrosion resistance, but because it is far removed from galvanized steel and aluminum on the nobility scale, there is a high potential for galvanic action. Conversely, active stainless steel is less resistant to corrosion, but because it is fairly close to galvanized steel and aluminum, there is less galvanic action. This concept is the basis for the language in the NEC regarding isolating stainless steel from galvanized boxes and fittings when installed in severely corrosive environments.
Since the NEC has differing requirements for corrosion protection for corrosive environments and severely corrosive environments, it is important to have guidance for these distinctions. In a marine or industrial location, the determination is probably clear, but there are numerous situations where the installation is exposed to seemingly benign compounds. How then do you determine the corrosion potential and need for protection or supplemental protection? The pH of a liquid will be a good indicator of how to design, install, and maintain the electrical installation. It is generally acknowledged that galvanized steel performs well in environments with pH ranging from 4 to 12.5, and aluminum is satisfactory in pH exposure from 4 to 9. Not sure of the pH of a liquid you are working with? Federal law requires that a material safety data sheet (MSDS) be made available for just about every product. This might be obtained from the manufacturer or seller, but a quick internet query is probably the quickest and easiest way to obtain the information.
Lastly, we should talk about repairing damage to the galvanized coating that may occur during transportation, storage, or installation. There are several ways to repair the factory protective coating, including solders, paint, and metalizing. Metalizing is generally a process that is accomplished in a shop and not in the field, so we will not delve into it here. One of the most common sources of damage to the galvanizing protection is the use of pipe wrenches or slip-joint plyers to tighten threaded conduit; the jaws of the tool penetrate the protective covering. Using strap wrenches will reduce the potential for damage during installation.
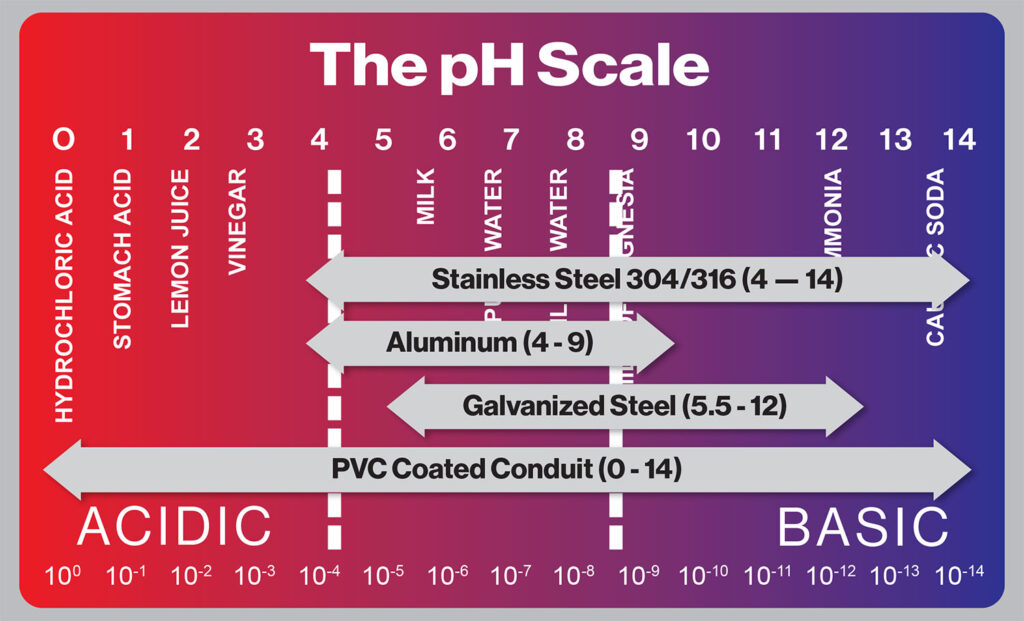
That leaves a couple of practical remedies. ASTM standard A 780-01 , the Standard Practice for Repair of Damaged and Uncoated Areas of Hot-Dip Galvanized Coatings, addresses soldering, paints containing zinc dust, and zinc spray as means of repairing galvanized metal. Soldering is done with a low-melting-point, zinc-rich rod, or powder. By far, the most reasonable means of repairing most damage to galvanized surfaces is with paint. In a wet paint application, there should be a minimal zinc concentration of 65% or above 92% in a dry film. There are several readily available products to satisfy this requirement.
Understanding the causes of corrosion and galvanic action can help you select the right product and installation techniques and determine the need for supplemental corrosion protection. Such a carefully thought-out installation will result in a quality, long-lasting electrical system.
(Please visit steeltubeinstitute.org for additional information to be found in FAQs and Tech Talks and to download installation manuals.)
Find Us on Socials