The first question you may be asking yourself is, “How does a code enforcement inspector fit into IAEI?” That is what we will look at in this article.
These inspectors typically respond to complaints from people within their enforcement jurisdiction. They handle weeds, grass, trash and debris, inoperable vehicles, and work being completed without the appropriate permits. But in some jurisdictions, they may also fulfill the needs of on-call responders in cases such as a vehicle into a building.
The Duties:
Upon arriving at the building or residence, the inspector needs to determine if there are any electrical issues. Does the power at the structure need to be de-energized? Is there any water damage to the electrical equipment or systems? Are there other damaged feeders or conductors going to the other unit(s)? Where is the electrical equipment on the premises, and what does it control? And the list goes on.
Some of the things the inspector might encounter on a regular call might include a landlord/owner who has neglected the property. There could be broken or inoperable receptacles or grounded receptacles on non-grounded circuits in the structure. Maybe the main electrical service is severely deteriorated with rust or corrosion. The inspector may not be able to identify the circuits in a panel or switchboard to de-energize a circuit(s) that is posing a hazard. At times the occupant has piled trash and debris in front of the service panel, not allowing access to the equipment. An unqualified person may have worked on the electrical equipment. Items such as multiple conductor terminations at the lugs, non-separated grounds and neutral conductors, improper equipment heights (handles above 6’7”) at the electrical panels. There could also be open splices without boxes. And the list goes on.
This inspector may be assigned a mobile home or RV park to inspect. The inspector could come across exposed non-metallic sheathed cables or conductors. They may encounter broken pedestal equipment or deteriorated power supply cords supplying the mobile home or RV. The power supply cords may have been improperly spliced or the cord caps installed incorrectly. Either the overhead aerial conductors or underground feeders lack ground or bonding conductors due to theft or lack of installation. The access to the electrical overcurrent equipment for the trailer space might be blocked or restricted. There could be outdated meter equipment, incorrect circuit breakers, or other equipment. Someone could have mislabeled electrical equipment. The wooden poles for equipment mounting have deteriorated and are in need of replacement. And do not forget the aluminum wiring factors that may not be installed correctly that could pose a threat of losing connections and or fire. And the list goes on. See figures 1 and 2.
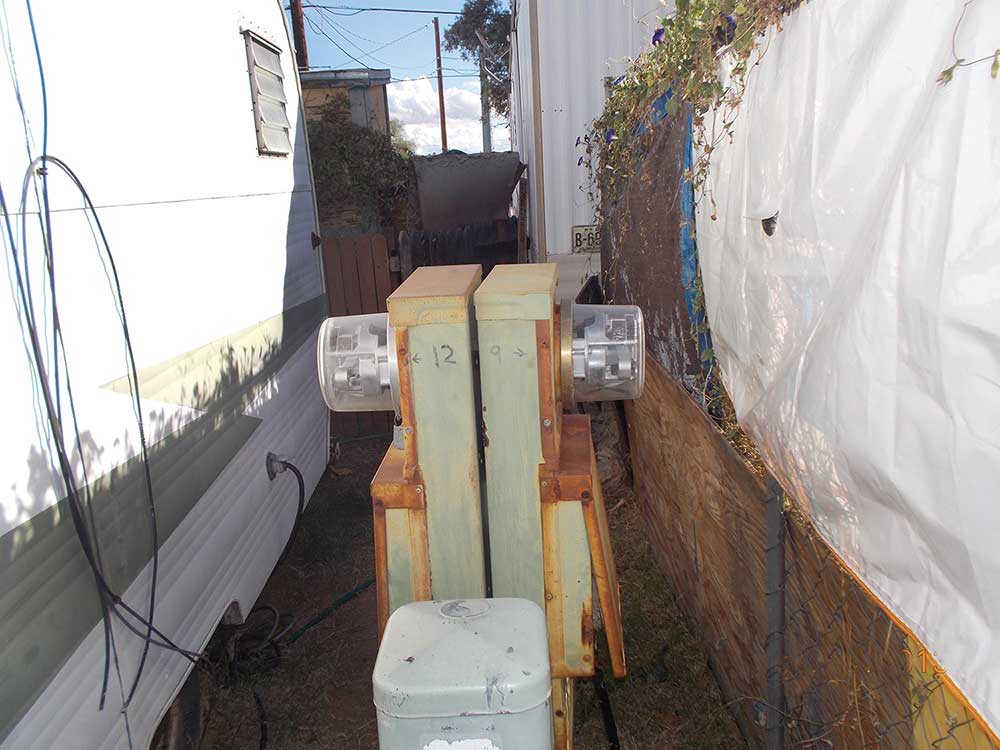
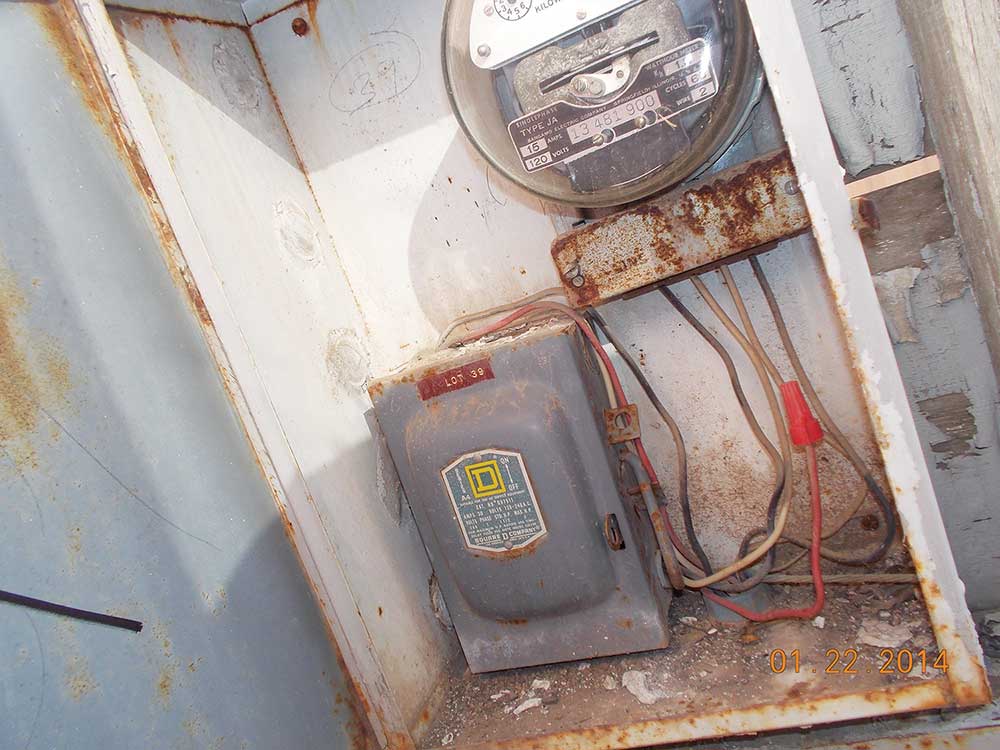
The commercial property that the inspector has been sent to because of a complaint might have violations. An unqualified person has installed some luminaires with two-wire zip cords wired into a box with no connectors and open splices. The raceways are falling out of the wall due to non-support and separating at the connectors or couplings. The grounding electrode conductors have been stolen (again). There is so much dirt, dust, and debris with a build-up of foreign material in the service disconnect that operation is impaired, and fire or fault is inevitable. The cardboard actuating mechanism has deteriorated and is separating, leading to failure. Due to these conditions, the service disconnects will not be operable to de-energize the equipment in a fault condition. The service disconnect is not grouped with the other services for the first responder to quickly disconnect as necessary under an emergency condition. There was no labeling present as to property served (address), to conditions (what is served by the service disconnect), or usage. And the list goes on. See figure 3.
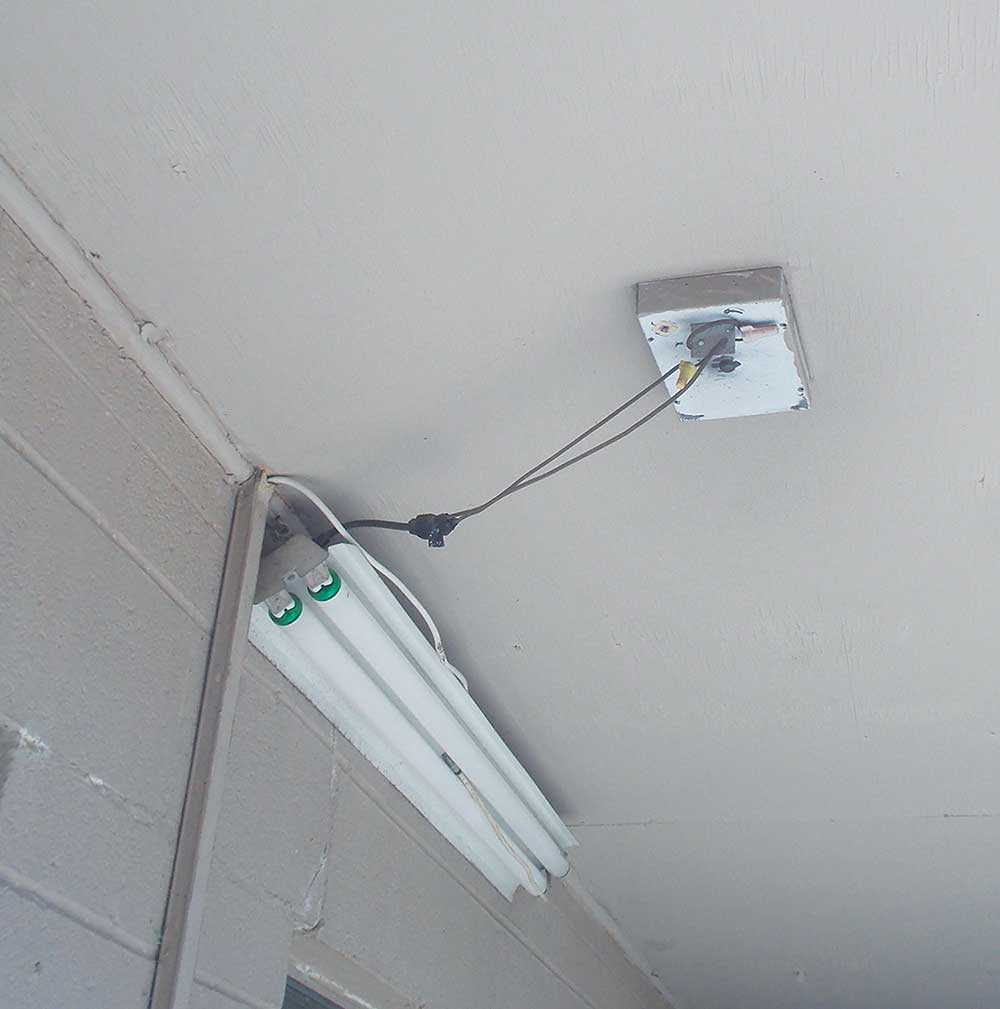
The call comes in for a parking lot light pole that has been hit by a vehicle and damaged. Well, the obvious concern is the exposed conductors, but what about the other light poles that are just missing covers? Maybe we have junction boxes with missing screws for the covers and attached with “magical” duct tape. There are new patches in the parking lot asphalt and no evidence of permits. Are the newly installed underground raceways installed at the right depth as per NEC 300.5? And the list goes on.
How about that nosy neighbor that is looking over the wall into the yard and sees that a very large shed that has been built and wired without a permit. Was the electrical equipment installed as per codes? Does the inspector know what codes may apply to this type of construction? Is the equipment rated for the environment it is being installed in (indoor boxes installed outside)? Have the additional circuit loads been calculated for the electrical service? What special equipment has been installed (dryer, welder, or freezer)? What is the condition of the equipment (new or used)? And the list goes on.
The complaint comes in for a new 9’ wall built without permits. What about the new walk-in freezer installed and hidden behind the new wall? There are used disconnects with holes in the bottom that need to be evaluated and closed. Where did the added sub-panel come from? Have the new loads been calculated to verify if the existing service can handle the added equipment?
Further investigation reveals that the equipment grounding conductors and the neutrals located in the sub-panel are not separated and installed on the same bus bar. Doesn’t that violate NEC 250.24? And the list goes on. See figures 4a and 4b.
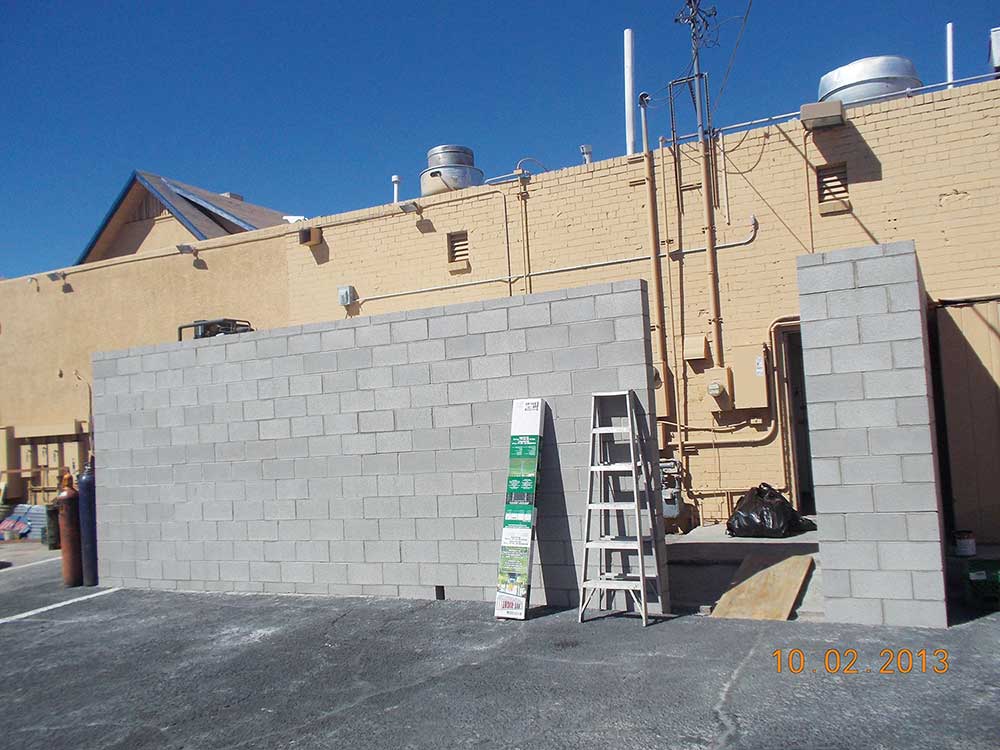
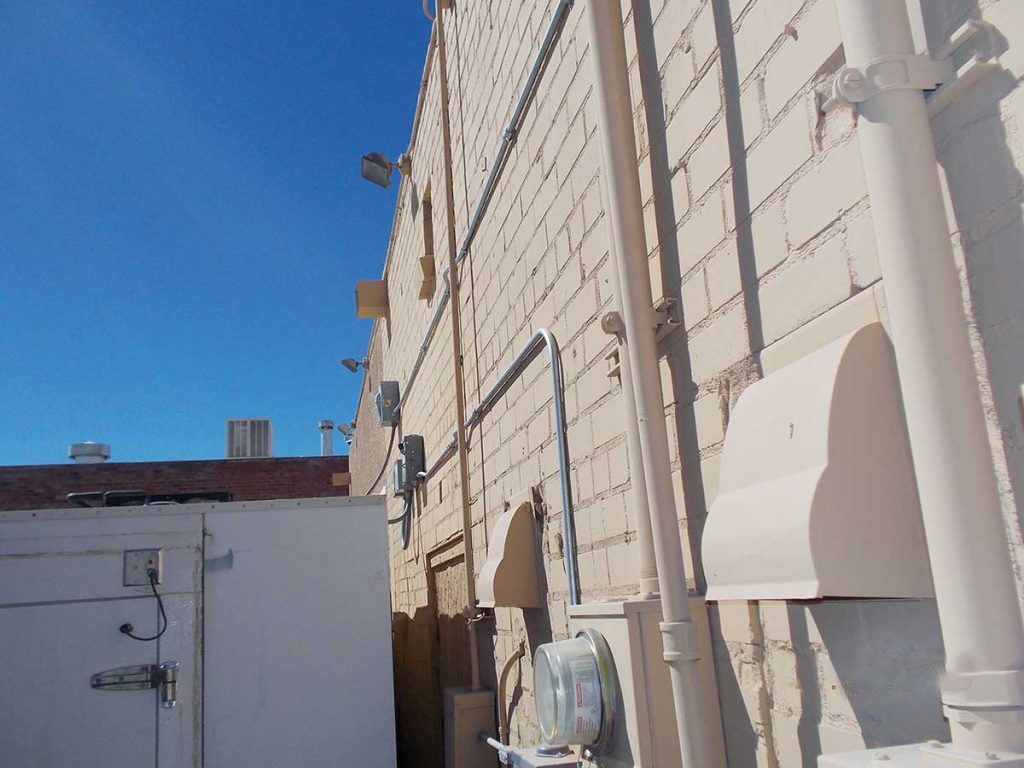
Now the rainy season is upon us, and the roof is leaking. It has been leaking for a while, and the tenants are just now complaining about it. The interior sub-panel shows signs of rust and water damage on the breakers. Is that breaker any good anymore? Will it trip under a fault condition? The feeders to the units are “SE” cable under the foam roof coating with no physical protection. What now? The water heater has an appliance cord used to connect it to the power outlet for a disconnecting means. And the list goes on. See figures 5 and 6.
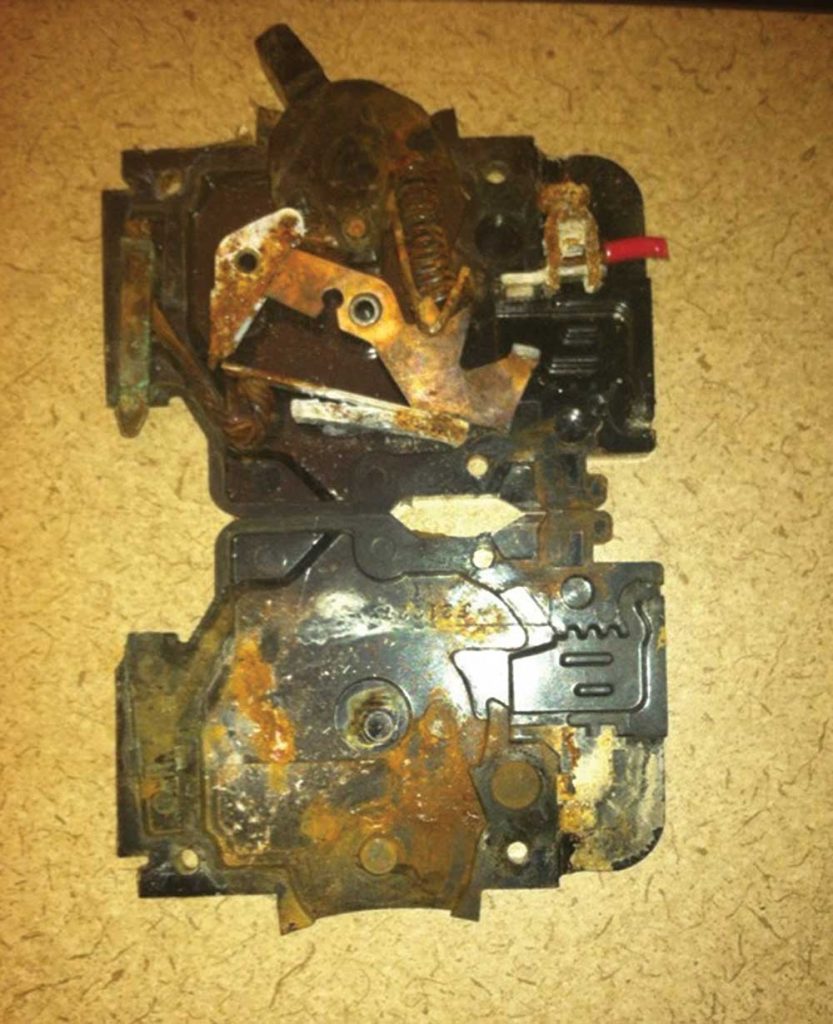
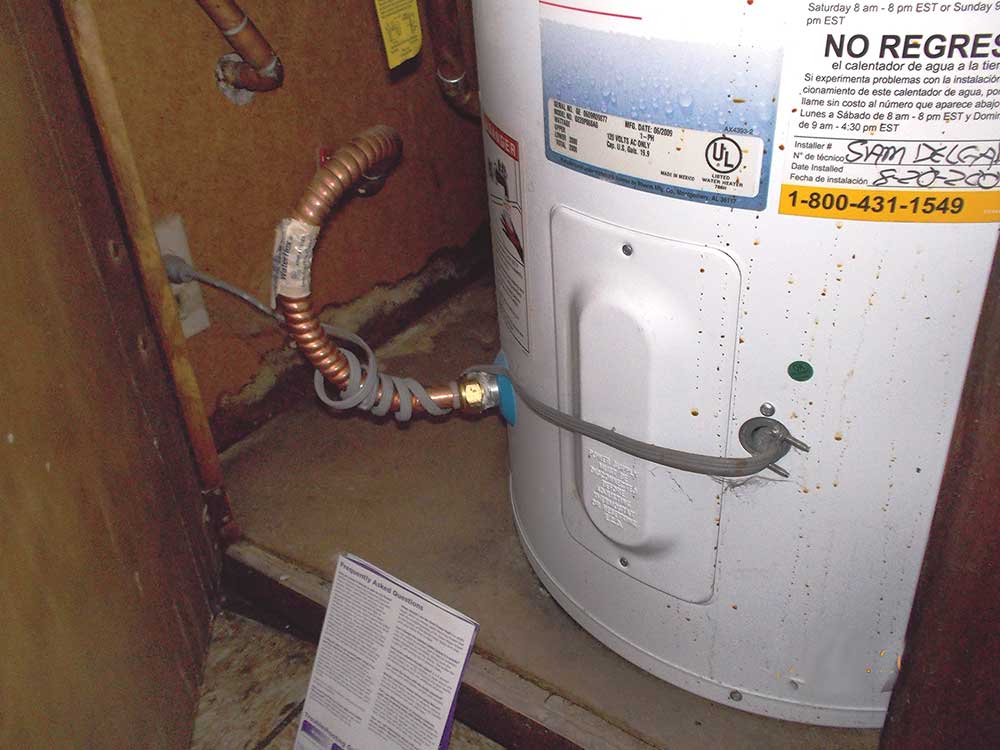
You get called to a triplex multifamily dwelling unit, and upon an investigation of the service, you notice only two electrical meters. Well, that in itself is not a code violation and an issue for the serving utility, but what about the multiple terminations under the load side lug that is listed for only one termination? The service disconnect also has a circuit feeding into the structure and then back out again, passing through to another location for a light. The equipment looks like it was installed in the 1950s or 1960s and shows signs of deterioration. The aerial conductors to the carport are four #12 THHN – three are black, and one is white. What is wrong with this whole picture? And the list goes on. (See figures 7 and 8).
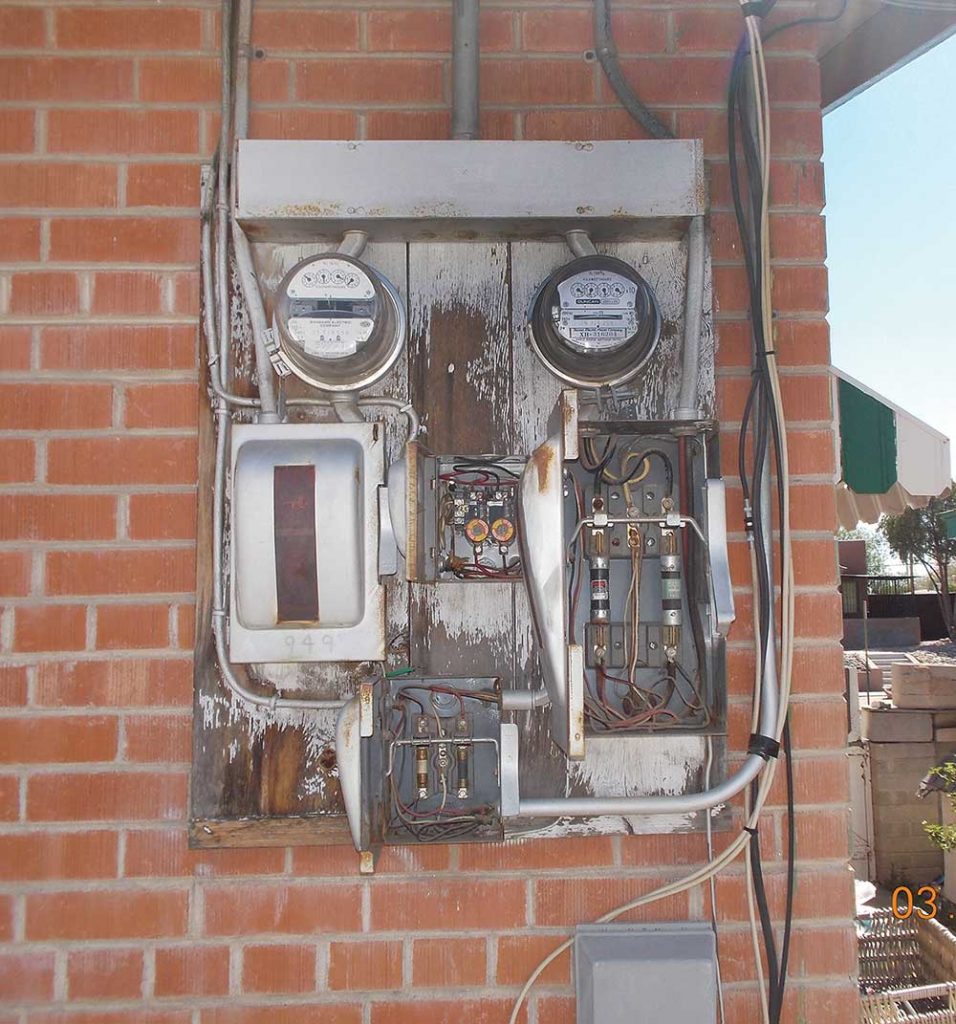
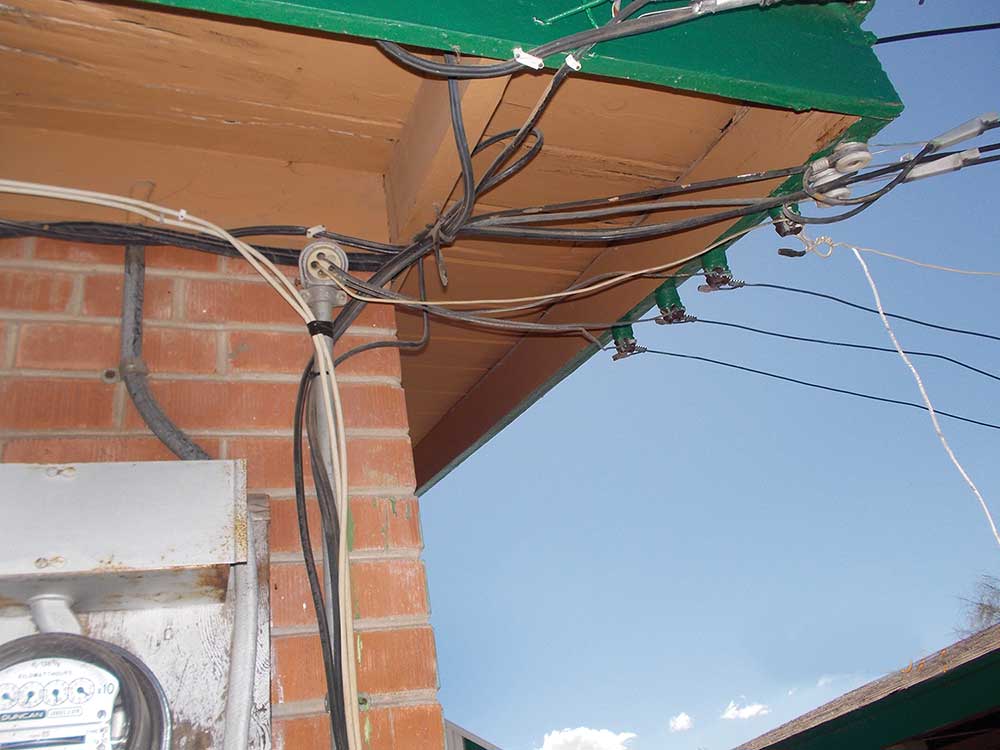
Summary
As you can see, “And the list goes on” is the need for code enforcement inspectors to be involved with IAEI for education training and be respected for the job they do. Also, the need for the knowledge that we can bestow for them is invaluable. These inspectors and their knowledge can also be a valuable part of our committees and boards. We, as IAEI members, need to seek out and include these valuable people to become an active part of our organization. Do you know of any of these individuals that fit what has been described above? Invite them to your IAEI chapter meetings. Inspire them to become members. Embrace them for what they can do for you and your chapter. Let’s show what IAEI can do together. Check with your local jurisdiction for help in finding these new prospective members. These inspectors can be a vital part of the IAEI Family.
Find Us on Socials