In construction, unanticipated hazards can arise due to changes in project timelines, sequence of events, and the fast pace of some construction projects. Hazard identification and assessment is a crucial part of an effective safety and health program.
One of the “root causes” of construction injuries, illnesses, and incidents is the failure to identify or recognize hazards that are present, or that could have been anticipated. A critical element of any effective safety and health program is a proactive, ongoing process.
Hazard Identification and Assessment
To identify and assess hazards, employers, and workers:
- Collect and review information about the hazards present or likely to be present at the job site.
- Conduct frequent and regular inspections of the job site to identify new or recurring hazards.
- Investigate injuries, illnesses, incidents, and close calls/near misses to identify the underlying hazards, their causes, and safety and health program shortcomings.
- Group similar incidents and identify trends in injuries, illnesses, and hazards reported.
- Consider hazards associated with emergency or nonroutine situations.
- For each hazard identified, determine the severity and likelihood of incidents that could result, and use this information to prioritize corrective actions.
Some hazards, such as housekeeping and tripping hazards, can and should be fixed as they are found. Fixing a hazard on the spot emphasizes the importance of safety and health and takes advantage of a safety leadership opportunity. Fixing other hazards identified using the processes described here will be addressed in the next section, “Hazard Prevention and Control.”
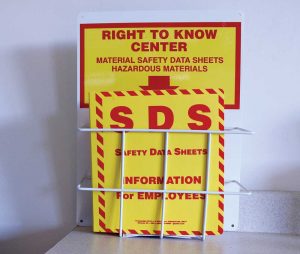
Action Item 1: Collecting existing information about job site hazards
Information on job site hazards may already be available (from both internal and external sources) to employers and workers.
How to accomplish it
- Collect, organize, and review information with workers to determine what types of hazards may be present and which workers may be exposed or potentially exposed.
- Information available may include:
- Equipment and machinery operating
- Safety Data Sheets (SDSs) provided by chemical manufacturers.
- Self-inspection reports and inspection reports from insurance carriers, government agencies, and consultants.
- Records of previous injuries and illnesses, such as OSHA 300 and 301 logs and reports of incident investigations.
- Workers’ compensation records and reports.
- Patterns of frequently occurring injuries and illnesses.
- Exposure monitoring results, industrial hygiene assessments, and medical records (appropriately redacted to ensure patient/worker privacy).
- Existing safety and health programs (hazard communication, confined spaces in construction, respiratory protection, process safety management, personal protective equipment (PPE), etc.).
- Input from workers, including surveys or minutes from safety and health committee meetings.
- Results of job hazard analyses (also known as job safety analyses).
- Information about hazards may be available from outside sources, such as:
- OSHA, National Institute for Occupational Safety and Health (NIOSH), and Centers for Disease Control and Prevention (CDC) websites, publications, and alerts.
- Trade associations.
- Labor unions, state and local occupational safety and health committees/coalitions (“COSH groups”), and worker advocacy groups.
- Safety and health consultants.
Action item 2: Inspect the job site for safety hazards
Hazards can be introduced over time as conditions on the job site change, for example, as the building goes up, equipment or tools become worn, different trades arrive at and depart from the site, and housekeeping practices decline. Setting aside time to frequently and regularly inspect the job site for hazards can help identify shortcomings so that they can be addressed before an incident occurs.
How to accomplish it
- Designate a competent person to conduct frequent and regular inspections of the job sites, materials, and equipment. Have workers on the inspection team and talk to them about hazards that they see or report.
- Plan ahead to anticipate the potential introduction of additional hazards by the next group of trades or sequence of construction activities and to address these additional hazards. For example, ensure that structures can handle any additional anticipated loads.
- Be sure to document inspections so you can later verify that hazardous conditions have been corrected. Take photos or video of problem areas to facilitate on-the-job discussion and brainstorming about how to immediately control them.
- Include all areas and activities in these inspections, such as trenching and excavations, staging areas, layout yards, working at heights, materials storage, heavy equipment maintenance, and the activities of on-site contractors, subcontractors, and temporary workers.
- Regularly inspect both mobile construction equipment (e.g., forklifts, bulldozers, aerial lifts, and cranes) and transportation vehicles (e.g., cars, trucks).
- Create material delivery areas and internal traffic control plans for the construction site and laydown areas.
- Use checklists that highlight things to look for. Typical hazards fall into several major categories, such as those listed below; each workplace will have its own list:
- Slip, trip, and fall hazards
- Electrical hazards
- General housekeeping
- Equipment operation
- Equipment maintenance
- Fire protection
- Work organization and process flow (including staffing and scheduling)
- Work practices
- Ergonomic problems
- Lack of emergency procedures
- Before changing operations, workstations, or workflow; making major organizational changes; or introducing new equipment, materials, or processes, seek the input of workers and evaluate the planned changes for potential hazards and related risks.
Note: Many hazards can be identified using common knowledge and available tools. For example, you can easily identify and correct hazards associated with broken stair rails and frayed electrical cords. Workers can be a very useful internal resource, especially if they are trained in how to identify and assess risks.
Action item 3: Identify health hazards
Identifying workers’ exposure to health hazards is typically more complex and less obvious than identifying physical safety hazards. For example, gases and vapors may be invisible, often have no odor, and may not have an immediately noticeable harmful health effect. Health hazards include chemical hazards (solvents, adhesives, paints, toxic dusts such as lead and silica, etc.), physical hazards (noise, radiation, heat, etc.), biological hazards (infectious diseases), and ergonomic risk factors (heavy lifting, repetitive motions, vibration from operating tools and earthmoving equipment).
How to accomplish it
- Identify chemical hazards—review safety data sheets and product labels to identify chemicals at your job site that have low exposure limits, are highly volatile, or are used in large quantities or in unventilated spaces. Identify activities that may result in skin exposure to chemicals.
- Identify physical hazards—identify any exposures to excessive noise (areas where you must raise your voice to be heard by others), elevated heat (indoor and outdoor), or sources of radiation (radioactive materials, X-rays, or radiofrequency radiation).
- Identify biological hazards—determine whether workers may be exposed to sources of infectious diseases, molds, toxic or poisonous plants, or animal materials (fur or scat) capable of causing allergic reactions or occupational asthma.
- Identify ergonomic risk factors—examine work activities that require heavy lifting, work above shoulder height, repetitive motions, or tasks with significant vibration.
- Conduct quantitative exposure assessments, when possible, using air sampling or direct reading instruments.
- Review OSHA 300 logs to help identify health hazards associated with job site exposures.
Note: Identifying and assessing health hazards may require specialized knowledge. Small businesses can obtain free and confidential occupational safety and health advice services, including help identifying and assessing workplace hazards, through OSHA’s On-site Consultation Program (see www.osha.gov/dcsp/smallbusiness/consult.html).
Action item 4: Conduct incident investigations
Incidents—including injuries, illnesses, close calls/near misses, and reports of other concerns—provide a clear indication of where hazards exist. By thoroughly investigating incidents and reports, you will identify hazards that are likely to cause future harm. The purpose of an investigation must always be to identify the root causes (and there is often more than one) of the incident or concern, in order to prevent future occurrences.
How to accomplish it
- Develop a clear plan and procedure for conducting incident investigations, so that an investigation can begin immediately when an incident occurs. The plan should cover items such as:
- Who will be involved
- Lines of communication
- Materials, equipment, and supplies needed
- Reporting forms and templates
- Train investigative teams on incident investigation techniques, emphasizing objectivity and open-mindedness throughout the investigation process.
- Conduct investigations with a trained team that includes representatives of both management and workers.
- Investigate close calls/near misses.
- Identify and analyze root causes to address underlying program shortcomings that allowed the incidents to happen.
- Communicate the results of the investigation to managers, supervisors, and workers to prevent recurrence.
Note: OSHA has special reporting requirements for work-related incidents that lead to serious injury or a fatality (29 CFR 1904.39). OSHA must be notified within 8 hours of a work-related fatality, and within 24 hours of an amputation, loss of an eye, or inpatient hospitalization.
Note: Effective incident investigations do not stop at identifying a single factor that triggered an incident. They ask the questions “Why?” and “What led to the failure?” For example, if a piece of equipment fails, a good investigation asks: “Why did it fail?” “Was it maintained properly?” “Was it beyond its service life?” and “How could this failure have been prevented?” Similarly, a good incident investigation does not stop when it concludes that a worker made an error. It asks such questions as: “Was the worker provided with appropriate tools and time to do the work?” “Was the worker adequately trained?” and “Was the worker properly supervised?”
Action item 5: Identify hazards associated with emergency and nonroutine situations
Emergencies present hazards that need to be recognized and understood. Nonroutine or infrequent tasks, including mobilization and demobilization of the site, critical lifts with cranes, concrete pours, or setting critical structural members, also present potential hazards. Plans and procedures need to be developed for responding appropriately and safely to hazards associated with foreseeable emergency scenarios and nonroutine situations.
How to accomplish it
- Identify foreseeable emergency scenarios and nonroutine tasks, taking into account the types of material and equipment in use and the location at the worksite. Scenarios such as the following may be foreseeable:
- Structural collapse (i.e., bridges, buildings, trenches, and concrete forms)
- Nonroutine tasks, such as infrequently performed activities (i.e., critical lifts and concrete pours)
- Fires and explosions
- Medical emergencies
- Weather emergencies and natural disasters
- Hazardous material spills
- Startups after planned or unplanned equipment shutdowns
Action item 6: Characterize the nature of identified hazards, identify interim control measures, and prioritize the hazards for control
The next step is to assess and understand the hazards identified and the types of incidents that could result from worker exposure to those hazards. This information can be used to develop interim controls and to prioritize hazards for permanent control (see “Hazard Prevention and Control”).
How to accomplish it
- Evaluate each hazard by considering the severity of potential outcomes, the likelihood that an event or exposure will occur, and the number of workers who might be exposed.
- Use interim control measures to protect workers until more permanent solutions can be implemented.
- Prioritize the hazards so that those presenting the greatest risk are addressed first. Note, however, that employers have an ongoing obligation to control all serious recognized hazards and to protect workers.
Note: “Risk” is the product of hazard and exposure. Thus, risk can be reduced by controlling or eliminating the hazard, or by reducing workers’ exposure to hazards. An assessment of risk helps employers understand hazards in the context of their own workplace, and prioritize hazards for permanent control.
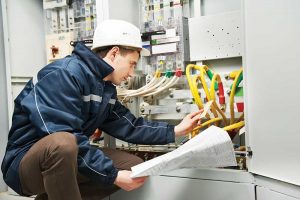
Hazard Prevention and Control
Effective controls protect workers from hazards; help avoid injuries, illnesses, and incidents; minimize or eliminate safety and health risks; and help employers provide workers with safe and healthful working conditions. The processes described in this section will help employers prevent and control hazards identified in the previous section.
TO EFFECTIVELY CONTROL and prevent hazards, employers should:
- Involve workers, who often have the best understanding of the conditions that create hazards and insights into how they can be controlled.
- Identify and evaluate options for controlling hazards, using a “hierarchy of controls.”
- Use a hazard control plan to guide the selection and implementation of controls and implement controls according to the plan.
- Develop plans with measures to protect workers during emergencies and nonroutine activities.
- Evaluate the effectiveness of existing controls to determine whether they continue to provide protection, or whether different controls may be more effective. Review new technologies for their potential to be more protective, more reliable, or less costly.
Action item 1: Identify control options
A wealth of information exists to help employers investigate options for controlling identified hazards. Before selecting any control options, it is essential to solicit workers’ input on their feasibility and effectiveness.
How to accomplish it
- Review sources such as OSHA standards and guidance, industry consensus standards, National Institute for Occupational Health and Safety (NIOSH) publications, manufacturers’ literature, and engineering reports to identify potential control measures. Keep current on relevant information from trade or professional associations.
- Investigate control measures used at other worksites and determine whether they would be effective at your job sites.
- Get input from workers who may be able to suggest and evaluate solutions based on their knowledge of the job site, equipment, and work processes.
- For complex hazards, consult with safety and health experts, including OSHA’s On-site Consultation Program.
Action item 2: Select controls
Employers should select the controls that are the most feasible, effective, and permanent (see Photo 3).
How to accomplish it
- Eliminate or control all serious hazards (hazards that are causing or are likely to cause death or serious physical harm) immediately.
- Use interim controls while you develop and implement longer-term solutions.
- Select controls according to a hierarchy that emphasizes engineering solutions (including elimination or substitution) first, followed by safe work practices, administrative controls, and finally PPE.
- Avoid selecting controls that may directly or indirectly introduce new hazards. Examples include exhausting contaminated air into occupied workspaces or using hearing protection that makes it difficult to hear backup alarms.
- Review and discuss control options with workers to ensure that controls are feasible and effective.
- Use a combination of control options when no single method fully protects workers.
Note: Whenever possible, select equipment, machinery, and materials that are inherently safer based on the application of “Prevention through Design” (PtD) principles. Apply PtD when making your own job site or equipment decisions. For more information, see the link to the NIOSH PtD initiative on the recommended practices Web page.
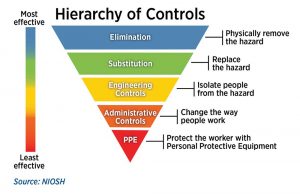
Action item 3: Develop and update a hazard control plan
A hazard control plan describes how the selected controls will be implemented. An effective plan will address serious hazards first. Interim controls may be necessary, but the overall goal is to ensure effective long-term control of hazards. Control plans at a construction site may need to be updated and modified often as the project develops and the site conditions and hazards change.
How to accomplish it
- List the hazards needing controls in order of priority.
- Assign responsibility for installing/implementing the controls to a specific person or persons with the power or ability to implement the controls.
- Establish a target completion date.
- Plan how you will track progress toward completion.
- Plan how you will verify the effectiveness of controls after they are installed or implemented.
Action item 4: Select controls to protect workers during nonroutine tasks and emergencies
A hazard control plan includes provisions to protect workers during nonroutine tasks and foreseeable emergencies, such as falls, cave-ins, fires and explosions, chemical releases, hazardous material spills, infrequent activities, natural and weather disasters, workplace violence, terrorist or criminal attacks, disease outbreaks (e.g., pandemic influenza), and medical emergencies. Nonroutine tasks, or tasks workers don’t normally do, should be approached with particular caution. Prior to initiating such work, review JSAs with the workers involved and notify others about the nature of the work, work schedule, and any necessary precautions.
How to accomplish it
- Develop procedures to control hazards that may arise during nonroutine tasks (e.g., mobilization and demobilization of the site, critical lifts with cranes, concrete pours, or setting critical structural members).
- Develop or modify plans to control hazards that may arise in emergency situations.
- Procure any equipment needed to control emergency-related hazards.
- Assign responsibilities for implementing the emergency plan.
- Conduct emergency drills to ensure that procedures and equipment provide adequate protection during emergency situations.
Note: Depending on your location, type of business, and materials stored or used on site, authorities including local fire and emergency response departments, state agencies, the U.S. Environmental Protection Agency, the Department of Homeland Security, and OSHA may have additional requirements for emergency plans. Ensure that your procedures comply with these requirements.
Action item 5: Implement selected controls on the job site
Once hazard prevention and control measures have been identified, they should be implemented according to the hazard control plan.
How to accomplish it
- Implement hazard control measures according to the priorities established in the hazard control plan.
- When resources are limited, implement measures on a “worst-first” basis, according to the hazard ranking priorities (risk) established during hazard identification and assessment. (Note, however, that regardless of limited resources, employers have an obligation to protect workers from recognized, serious hazards.)
- Promptly implement any measures that are easy and inexpensive—such as general housekeeping, removal of obvious tripping hazards such as electrical cords, and basic lighting—regardless of the level of hazard they involve.
Action item 6: Follow up to confirm that controls are effective
To ensure that control measures are and remain effective, employers should track progress in implementing controls, inspect and evaluate controls once they are installed, and follow routine preventive maintenance practices.
How to accomplish it
Track progress and verify implementation by asking the following questions:
- Have all control measures been implemented according to the hazard control plan?
- Have engineering controls been properly installed and tested?
- Have workers been appropriately trained so that they understand the controls, including how to operate engineering controls, safe work practices, and PPE use requirements?
- Are controls being used correctly and consistently?
- Conduct regular inspections (and industrial hygiene monitoring, if indicated) to confirm that engineering controls are operating as designed.
- Evaluate control measures to determine if they are effective or need to be modified. Involve workers in the evaluation of the controls.
- If controls are not effective, identify, select, and implement further control measures that will provide adequate protection.
- Confirm that work practices, administrative controls, and PPE use policies are being followed.
- Conduct routine preventive maintenance of equipment and controls to help prevent incidents due to equipment failure.
Education and Training
Education and training are important tools for informing workers and managers about hazards and controls so they can work more safely and be more productive. Another role of education and training, however, is to provide workers and managers with a greater understanding of the safety and health program itself, so that they can contribute to its development and implementation.
Education and training provides employers (owners and executives), managers, supervisors, and workers with:
- Knowledge and skills needed to do their work safely and avoid creating hazards that could place themselves or others at risk.
- Awareness and understanding of hazards and how to identify, report, and control them.
- Specialized training, when their work involves unique hazards.
Additional training may be needed depending on the roles assigned to employers or individual managers, supervisors, and workers. For example, employers, managers, and supervisors may need specific training to ensure that they can fulfill their roles in providing leadership, direction, and resources for the safety and health program.
Workers assigned specific roles in the program (e.g., incident investigation team members) may need training to ensure their full participation in those functions.
Effective training and education can be provided outside a formal classroom setting. Peer-to-peer training, on-the-job training, daily toolbox talks, and worksite demonstrations can be effective in conveying safety concepts, ensuring understanding of hazards and their controls, and promoting good work practices.
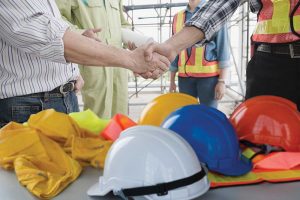
Action item 1: Provide program awareness training
Managers, supervisors, and workers all need to understand the program’s structure, plans, and procedures. Having this knowledge ensures that everyone can fully participate in developing and implementing the program.
How to accomplish it
- Provide training to all managers; supervisors; workers; and contractor, subcontractor, and temporary agency workers on:
- Safety and health policies, goals, and procedures
- Functions of the safety and health program
- Whom to contact with questions or concerns about the program (including contact information)
- How to report hazards, injuries, illnesses, and close calls/near misses
- What to do in an emergency
- The employer’s responsibilities under the program
- Workers’ rights under the OSH Act
- Provide information on the safety and health hazards of the job site and the controls for those hazards.
- Ensure that training is provided in the language(s) and at a literacy level that all workers can understand.
- Emphasize that the program can only work when everyone is involved and feels comfortable discussing concerns; making suggestions; and reporting injuries, incidents, and hazards.
- Confirm, as part of the training, that all workers have the right to report injuries, incidents, hazards, and concerns and to fully participate in the program without fear of retaliation.
Action item 2: Train employers, managers, and supervisors on their roles in the program
Employers, managers, and supervisors are responsible for workers’ safety, yet sometimes have little training on safety-related concepts and techniques. They need specific training that allows them to fulfill their leadership roles in the program.
How to accomplish it
- Reinforce employers, managers, and supervisors’ knowledge of their responsibilities under the OSH Act and the workers’ rights guaranteed by the Act.
- Train employers, managers, and supervisors on procedures for responding to workers’ reports of injuries, illnesses, and incidents, including ways to avoid discouraging reporting.
- Instruct employers, managers, and supervisors on fundamental concepts and techniques for recognizing hazards and methods of controlling them, including the hierarchy of controls (see “Hazard Prevention and Control”).
- Instruct employers, managers, and supervisors on incident investigation techniques, including root cause analysis.
- As a starting point, consider providing the OSHA 30-hour construction safety course, or a similar course.
Action item 3: Train workers on their specific roles in the safety and health program
Additional training may be needed to ensure that workers can incorporate safety and health responsibilities into their daily routines and activities.
How to accomplish it
- Instruct workers on how to report injuries, illnesses, incidents, and concerns. If a computerized reporting system is used, ensure that all employees have the basic computer skills and computer access sufficient to submit an effective report.
- Instruct workers assigned specific roles within the safety and health program on how they should carry out those responsibilities, including:
- Hazard recognition and controls (see Action item 4)
- Participation in incident investigations
- Program evaluation and improvement
- Provide opportunities for workers to ask questions and provide feedback during and after the training.
- As the program evolves, institute a more formal process for determining the training needs of workers responsible for developing, implementing, and maintaining the program.
Action item 4: Train workers on hazard identification and controls
Providing workers with an understanding of hazard recognition and control, and actively involving them in the process, can help to eliminate hazards before an incident occurs. Employers are required to instruct each employee in the recognition and avoidance of unsafe conditions and the regulations applicable to his or her work environment to control or eliminate any hazards or other exposure to illness or injury [29 C.F.R. 1926.21(b)(2)]. As a starting point, employers may consider providing the OSHA 10-hour course for construction or a similar course to be supplemented by orientation training and toolbox talks to cover hazards on each specific site.
How to accomplish it
- Train workers on techniques for identifying hazards, such as job hazard analysis (see OSHA Publication 3071).
- Train workers so they understand and can recognize the hazards they may encounter in their own jobs, as well as more general work-related hazards.
- Instruct workers on concepts and techniques for controlling hazards, including the hierarchy of controls and its importance.
- Train workers on the proper use of work practice and administrative controls.
- Train workers on when and how to wear required PPE.
- Provide additional training, as necessary, when construction progresses. Consider situations such as when new trades and/or equipment arrive at the job site to perform the next phase of the project.
Extracted from OSHA 3886, Recommended Practices for Safety & Health Programs in Construction, October 2016, https://www.osha.gov/safetymanagement.
With the Occupational Safety and Health Act of 1970, Congress created the Occupational Safety and Health Administration (OSHA) to ensure safe and healthful working conditions for working men and women by setting and enforcing standards and by providing training, outreach, education, and assistance. Visit OSHA online at https://www.osha.gov/.
Find Us on Socials