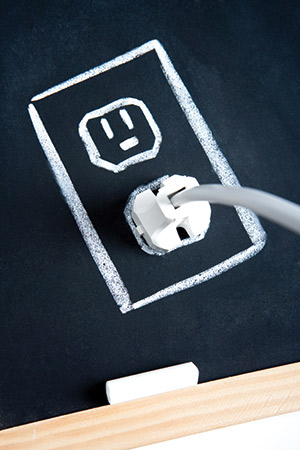
CODES AND STANDARDS
Some people may think the world revolves around codes and standards but the fact is that many products, in addition to revolving around meeting customer wants and needs, do. The following documents are pertinent to our discussion on receptacles:
- UL 498, Attachment Plugs and Receptacles, is the UL document that governs the performance requirements for receptacles and attachment plugs. We’ll talk more about this document later.
- NFPA 70, National Electrical Code, is the installation requirements that include articles and sections with specific requirements for the installation of receptacles.
- CSA C22.2, General use receptacles, attachment plugs, and similar wiring devices, is the Canadian standards document that governs the performance requirements for receptacles and attachment plugs and similar wiring devices for use in Canada.
- Federal Specification WC596, General Specification for Connector, Electrical, Power. This document includes additional MIL Spec references and testing requirements.
NEC 2011 defines a receptacle as a “contact device installed at the outlet for the connection of an attachment plug. A single receptacle is a single contact device with no other contact device on the same yoke. A multiple receptacle is two or more contact devices on the same yoke.” We’ll have to review the parts of a standard receptacle to really understand some of this definition as I’m sure that the reference to yoke above is more than likely not the yoke you had with toast and coffee this morning. Understanding the parts of a receptacle is important as they are referenced in various sections of the Code. The term yoke is one of those that we use frequently but for which there is no formal definition. Rather than assume we all know what a yoke is, let’s define it. In general the yoke, sometimes used interchangeably with the term strap, is a mounting means for a wiring device. The yoke of a receptacle is the frame, the metal portion of the receptacle that is used to mount a device to the outlet box. (Reference figure 1.) While not prevalent, there are non-metallic yokes. The device depicted in figure 1, has two contact devices on a single yoke.
Figure 1
As an example of how important it is to understand the term yoke, let’s look at the language of Section 210.7 of NEC 2011.
“210.7 Multiple Branch Circuits. Where two or more branch circuits supply devices or equipment on the same yoke, a means to simultaneously disconnect the ungrounded conductors supplying those devices shall be provided at the point at which the branch circuits originate.”
For the device in figure 1, only one branch circuit would supply both contact devices without modification as both contact devices are electrically connected. If the tabs on each side of the receptacle are removed from this device, the upper single contact device and lower single contact device are cleanly separated electrically from each other. In this case, you may have two branch circuits supplying this single yoke, with one branch circuit feeding the top single contact device and the other supplying the lower single contact device. Both of these single contact devices share a single yoke. Hence, as per Section 210.7, the two branch-circuit overcurrent devices must have a means to simultaneously disconnect the ungrounded conductors.
Another example of the use of yoke in the Codecan be found in Section 220.14, “Other Loads – All Occupancies,” where the minimum load for each outlet for general-use receptacles and outlets are calculated. Section 220.14(I) Receptacle Outlets states the following:
“(I) Receptacle Outlets. Except as covered in 220.14(J) and (K), receptacle outlets shall be calculated at not less than 180 volt-amperes for each single or for each multiple receptacle on one yoke. A single piece of equipment consisting of a multiple receptacle comprised of four or more receptacles shall be calculated at not less than 90 volt-amperes per receptacle. This provision shall not be applicable to the receptacle outlets specified in 210.11(C)(1) and (C)(2).”
The term yoke is used 20 times in NEC 2011; it is important to understand what a yoke is so as to apply the Codeaccurately.
On the standards front, UL 498 is the standard for receptacles that defines the many performance based tests conducted on these devices. We will explore, at a high level, these tests to which a receptacle must submit.
Standard Receptacle Product Performance Criteria
Product test standards thrive on performance based testing; they seek to create the tests and environments to which the devices will be subjected in their application. Some of the key performance test requirements for receptacles include the following:
- Retention of blades: After ten insertions, not to exceed 40 lb of force, of a standard steel blade plug gauge, the receptacle must be able to hold (retain) a polished steel 2 bladed plug gauge without holes (the grounding blade removed) against a 3 lb force for 1 minute. The receptacle must release a polished steel 3 bladed plug gauge with holes at no more than 15 lb of force.
- Current overload: To pass this test, the same test samples from the previous test are utilized and must not exhibit any electrical or mechanical failure, pitting or burning of the contacts, that would affect the intended function. The test sample device is subjected to 100 insertions & removals of a mating plug making and breaking dc current through a resistive load at 150% of device rating. The blade of the attachment plug is to mate with the contact of the receptacle for not more than 1 second during each cycle.
- Temperature rise: After the previous current overload test, the same samples are subjected to this temperature rise test. Strategically placed thermocouples help to ensure the test subject passes this test which requires that the contact temperature rise of a flush or self-contained receptacle shall not be more than 30°C (54°F) when the receptacle is carrying its maximum rated current.
- Repeat blade retention: For those test samples experiencing the previous temperature rise test, they must additionally pass the Blade Retention test described in item 1 above.
- Resistance to arcing: The outlets that were subjected to the 100 cycles of operation in the Overload Test described in item 2 above must perform acceptably when subjected to an additional 150 cycles of operation under the overload test conditions following the temperature test and the repeated retention of blades test. There is also a dielectric test built into this test; 1500 volts for 1 minute to ensure the integrity of the device.I think it is worth stopping here for a moment to reflect on this specific test as it is a good example of a redundancy that is not unique in this specific UL standard. In this case, the test samples used are not new or fresh out of the box. These samples have experienced an overload test as well as the temperature and repeated retention of blades tests. We’ll see more of this redundancy as we move into the Hospital Grade and other similar products. First, let’s continue looking at what a receptacle must endure as part of this UL standard performance test requirements.
- Terminal strength: The standard 3-prong steel test gauge is inserted 10 times and the maximum insertion force should not exceed 40 lbf. If the receptacle has a breakoff tab, it is removed prior to the conditioning. After conditioning, each terminal is wired with 12 AWG solid copper wire by applying 14 in-lbs of tightening torque. The wire is stripped to the length specified in the manufacturer’s installation instructions. Wire-binding screw terminals are wired by placing the stripped conductor under the screw head and wrapping it ⅔–¾ turn around the screw. Pressure-wire terminals are wired by inserting the stripped conductor into the terminal. The terminal screw is then torqued, loosened and retorqued. Following the last torqueing, each terminal is to be subjected to a straight 20-lbf (89-N) pull applied to each wire for 1 minute perpendicular to the plane of the back cover of the receptacle; the wire shall remain in place. Following this pull, the receptacle must be able to hold (retain) a polished steel 2 bladed plug gauge (without holes in the blades and without ground) against a 3 lb force for 1 minute. The receptacle must release a polished steel 3 bladed plug gauge (with holes in the blades) at no more than 15 lb of force.
- Grounding pin retention: In these tests, the grounding pin is the focus. It is subjected to various situations including a weight of 5 lbs located 6 inches from the outlet face, a 360 degree rotation of a grounding pin during which time the continuity must be maintained. After the receptacle is subjected to these tests, the ground contact must retain a pin being subjected to a 4 oz. and 2 oz. weight depending upon the dimension of the pin.
- Fault current: For this test, the receptacle is subjected to a through fault current of 1,000 amperes downstream of a 15-A or 20-A circuit breaker. After the receptacle experiences this fault current, it must retain its integrity as demonstrated by a continuity check after removing and reinserting the attachment plug.
- Dielectric voltage withstand: For tamper-resistant receptacles, a dielectric test is performed to determine the effectiveness of a device’s insulation. In this case, a potential equal to twice the rated voltage of the receptacle plus 1,000 volts is applied between live parts of opposite polarity and between live parts and grounded or dead metal parts and must not exhibit any arcing or breakdown.
- Mold stress relief: Unwired receptacles are subjected to 70oC for 7 hours and after being allowed to cool, measurements are made where there shall not be any warping, shrinkage or other distortion that results in the device not performing as expected.
- Dielectric voltage withstand (repeated): After the above mold stress relief test, the same test specimens are again subjected to the dielectric voltage withstand tests described above in item 9.
- Assembly security: This test is quite grueling in that the subject receptacle must endure a 50 lb force through extra-long blades inserted into the receptacle and directly on the back of the receptacle.
The above performance tests are just a taste of what a receptacle must pass to obtain the UL label. These tests help ensure the device will safely perform when called upon.
Hospital Grade Product Performance Criteria
In addition to these basic performance tests, UL 498 includes supplements for product requirements addressing other application needs. One such supplement is that for Hospital Grade Devices; supplement SD includes nine additional tests that make hospital grade receptacles what they are. The following additional tests are a taste of what a Hospital Grade receptacle requires:
- Abrupt plug removal: A test plug with brass blades that is attached to a 10 lb weight is inserted into a receptacle. The weight is dropped from 24″ a total of eight times in an effort to abruptly remove the plug from the receptacle. After the eighth removal of the plug, the receptacle shall not experience any breakage that exposes live parts, be able to be mated to a standard plug, retain a 3 lb weight using a standard 2 prong plug (without ground) and retain a 4 oz. undersized ground pin.
- Grounding contact temperature: Using the same devices previously tested above, the acceptability of the grounding path in a receptacle shall be demonstrated by a temperature rise not exceeding 30°C (54°F) when subjected to these tests. The test subjects eight receptacles previously tested to a continuous current of 25 amperes for 1 hour and then 22 amperes until equilibrium is reached after being wired in series through the grounding conductor path.
- Grounding contact resistance: The same devices that experienced the past two tests are again subjected to yet another. This time the resistance between the mated attachment plug grounding terminal and receptacle grounding terminal shall not exceed 0.01 ohms.
- Fault current test: The test subjects that have been previously tested in the above three tests are then subjected to the standard fault current tests. The grounding path must retain its integrity.
- Grounding contact overstress: After an oversized steel pin (0.203 in.) is inserted 20 times into each ground contact, each ground contact must retain a standard sized (0.184 in.) polished steel pin against a 4 oz. force for 1 minute.
- Terminal strength: This is similar to the terminal strength test that is part of the standard receptacle testing criteria except for the fact that the terminals are disassembled, assembled and then torqued three additional times with a maximum tightening torque of 14 lbf-in (1.6 N-m) instead of the standard 14 lbf-in (1.6 N m) for a #8 screw.
- Assembly security: The assembly security test of the standard receptacle which is performed with a 50 lb force is performed with a 100 lb force.
- Impact: Receptacles are installed in a metal outlet box with a metal faceplate with the outlet facing up. Then a 5 lb weight is dropped from a height of 18 inches impacting the center of the receptacle outlet. There shall be no breakage that impairs the function of the receptacles or the insertion of a plug.
- Increased mold stress relief: Unwired receptacles are subjected to 90oC for 7 hours and after being allowed to cool, measurements are made where there shall not be a change in any dimension greater than 10 percent, nor any warping creating an opening greater than 1/32 in. (0.79 mm) in any butt joint forming the enclosure of each receptacle.
These hospital grade receptacles, after passing all of the additional tests, must be marked with the phrase “Hospital Grade” or “Hosp. Grade” and with a green dot.
Fed Spec Product Performance Criteria
Yet another type of device that confuses some when found in the field is the Fed Spec receptacle device. Just as in the Hospital Grade receptacles discussed above, Federal Specifications pile on an additional number of tests to the standard receptacle tests. The following additional 9 tests are a taste of what Federal Specification WC596 requires:
- Gripping – Power Blade – Grounding Blade: In this test, an oversized blade is inserted and removed 20 times into the current-carrying contact (a 0.075 in. thick blade instead of a 0.06 in. thick blade). Then each current-carrying contact must retain a less than standard thickness steel blade secured to a 1.5 lb weight for 1 minute (a 0.055 in. thick steel blade instead of the 0.06 in. thick blade). A similar test is done for the ground blade with modifications.
- Terminal Strength: This test is similar to the Hospital Grade test above. The terminal is tightened 5 times on to a minimum and maximum wire of 14 – 10 AWG and then tested by hanging a 20 lb weight from the wire for 1 minute.
- Overload 200% AC: A plug is inserted and removed from the receptacle 250 times as compared to the 100 times of UL 498, before conducting a 200% rated current test. UL 498 only requires this test to be run at 150% of rated current.
- Temperature Rise: Strategically placed thermocouples help to ensure the test subject passes this test which requires that the contact temperature rise of a flush or self-contained receptacle shall not be more than 30°C (54°F) when the receptacle is carrying 20 amperes for both 15-A and 20-A receptacles.
- Repeat Blade Retention: This repeated blade retention test is performed after the temperature rise test as is done for all receptacles.
- Dielectric Voltage Withstand: A potential equal to twice the rated voltage of the receptacle plus 1,000 volts is applied between live parts of opposite polarity and between live parts and grounded or dead metal parts and must not exhibit any arcing or breakdown.
- Insulation Resistance: The insulation resistance, when measured at various points on the receptacle, shall not be less than 100 megohms.
- Heat Resistance: Unwired receptacles are subjected to 85oC for 2 hours and after being allowed to cool, the device shall show no evidence of mechanical or electrical failure, flow, or critical softening of sealing compounds, or softening or distortion of parts.
- Assembly Security: This test is similar to that which is performed for a Hospital Grade receptacle. The receptacle must endure a 100 lb force through extra-long blades inserted into the receptacle as well as a 50 lb force to the back bridge of the receptacle.
The above should provide some insight to the differences between a standard receptacle, a Hospital Grade receptacle, and a Fed Spec device. The only other type not discussed above that is included in UL 498 Supplement SE and ones you may frequently see are the Weather-Resistant receptacles. These devices must also include corrosion-resistant, cold impact, accelerated aging, and resistance to ultraviolet light characteristics. They are intended to be installed in appropriate enclosures suitable for the application. They are not meant to be installed with direct exposure to water. Just as an example, all wire-binding screws and terminal pressure plates must be copper alloy or stainless steel having a minimum of 16% chromium content. These devices receive special attention to the materials with which they are constructed, as well as some additional tests to temperature cycling, UV light, and more.
RECEPTACLE CONFIGURATIONS, CLASSIFICATIONS, AND GRADES
If you have ever walked down the plug and receptacle aisle of your supply house, you may have left amazed at how many different variations of these devices there are. Plus, there are existing plugs and receptacles that weren’t on those shelves you were looking at. Just as in any product, there are reasons for this variety and there are standards that govern their configuration and application.
A great place to start to understand all of the available configurations is to review NEMA publication WD6, Wiring Devices—Dimensional Specifications. This free download from the www.nema.org website is a great resource to get your arms around the breadth of solutions that are available in the receptacle basket. All of the different NEMA configurations are clearly identified in NEMA WD6, but what is not included is an explanation of where you will typically see each type of configuration. If you are like me, you interface with a very limited range of receptacle types; so in hopes to convey the differences between these configurations, beyond what the NEMA document provides, I’ve assembled Table 1, which focuses only on straight blade available configurations.
The NEMA designations identify the blade configurations for receptacles with each NEMA receptacle configuration having a corresponding plug. The WD6 document includes images of each configuration for your reference. These different blade configurations help ensure the designated loads are only plugged into their designated receptacles. The changes in configurations occur by voltage rating and sometimes by grounding for each of the available ampacity devices. The available configurations for 15-A receptacles, for example, have different receptacle blade configurations for the various voltages including 125-V (grounding and non-grounding); 250-V (grounding and non-grounding); 277-V; 347-V; 3-Phase 250-V; and 125V/250V. Just to reiterate an im-portant fact, the various NEMA configurations ensure that a specific load that requires a specific voltage is not mistakenly plugged into the wrong receptacle. There are also corresponding locking types not discussed here.
The designations do not stop there as in addition to the above NEMA configurations, manufacturers offer different grades of products; some driven by product standards and others driven by market requirements. These grades include but are not limited to the following:
- Standard Grade
- Specification Grade
- Construction Grade
- Hospital Grade
- Industrial Grade – beefy, heavy, meant for use in the plant. Thicker metals
- Commercial Grade
Those grades not governed by the UL standard have qualities that the manufacturer included to meet needs of various target markets. For example, having a strap of brass rather than steel, contacts of a greater thickness for less heat rise, more contact wipes on the blades which gives a better connection are all ways a manufacturer may enhance their product. These go above and beyond the bare minimum product standards.
APPLICATIONS
Just as with any product, these devices too can be applied incorrectly in the field; it’s important to pay attention to where and how these devices are being installed. Care should be taken when landing wires on terminals and when pushing receptacles back into the outlet box. Make sure the environmental condition fits the rating of the device. If you are installing both the plug and receptacle for a specific load, ensure you are paying close attention to all of the code requirements surrounding the installation. The act of cutting off the plug from appliances and installing your own, not only may violate the UL Listing of the product you are modifying, but it also may create an unsafe installation.
REFERENCES
- NEMA WD6, Wiring Devices—Dimensional Specifications, http://www.nema.org/Standards/Pages/Wiring-Devices-Dimensional-Specifications.aspx#download
- NEMA Document, Protection of Receptacle Outlets in Wet Locations According to the National Electrical Code,http://www.nema.org/Standards/Pages/Protection-of-Receptacle-Outlets-in-Wet-Locations-According-to-the-National-Electrical-Code.aspx#download
- NEMA WD1, General Color Requirements for Wiring Devices,http://www.nema.org/Standards/Pages/General-Color-Requirements-for-Wiring-Devices.aspx#download
- “UL Listed Hospital Grade Receptacles, The differences between grades” http://www.ul.com/global/documents/offerings/perspectives/regulators/technical/ul_HospitalGradeReceptacles.pdf
- UL White Book, RTDV, RTRT
PARTING REMARKS
We’ve all interfaced with the standard 15-A and 20-A receptacle. It is indeed one of those devices that is heavily used, sometimes abused, and must perform over and over again safely and reliably. As you can see above, the standard for these devices reflects the awareness of this intended use. Hopefully this discussion has enlightened us all to the world of the incredible receptacle..
As always, keep safety at the top of your list and ensure you and those around you live to see another day.
Find Us on Socials