Selecting materials for electrical installations in environments that are or could be corrosive can be challenging. There is abundant information about corrosion available online by doing an Internet search, and we all know that everything on the Internet is true! The quantity of information and explanations can certainly be overwhelming. Considerations of initial cost, life expectancy, ease of installation, future use, and other factors are involved when designing electrical installations. This article provides more details in a simplistic form to help you make those decisions.
“Corrosion is a natural process that converts a refined metal into a more chemically-stable form such as oxide, hydroxide, or sulfide. It is the gradual destruction of materials by chemical and/or electrochemical reaction with their environment.” — Wikipedia
“Galvanic corrosion is an electrochemical process in which one metal corrodes preferentially when it is in electrical contact with another, in the presence of an electrolyte. A similar galvanic reaction is exploited in primary cells to generate a useful electrical voltage to portable power devices.” — Wikipedia
Steel is an alloy made primarily from iron along with other alloying metals to give it more favorable mechanical and corrosion resistance properties. As noted in the corrosion definition provided, the chemical/electrochemical reaction of the steel, and the environment it is in, causes the degradation of the iron within the steel into iron oxide (rust). Interestingly, the steel seems to be trying to revert back to its natural composition as iron ore. That is why steel products are often coated with other materials to provide protection from corrosion. Steel products are often coated with less reactive materials (such as zinc, plastic polymers, etc.) or refined into special alloys (such as stainless steel) to help reduce or prevent the rate of corrosion.
Corrosion Protection
A general requirement for the protection of electrical products against corrosion and deterioration is in 300.6 of the National Electrical Code®(NEC®). Essentially, all equipment must be suitable for the environment where it will be installed. Ferrous equipment must have an approved corrosion-resistant coating, as stated in NEC 300.6(A). The zinc coating (galvanized) typically applied by manufacturers of steel conduit and electrical metallic tubing (EMT) accomplishes this requirement. Raceways that are threaded anywhere other than where the product is listed (field-cut threads) must be coated with an approved electrically conductive corrosion-resistant coating where corrosion protection is necessary. There is an exception for stainless-steel equipment not requiring a protective coating because it is inherently corrosion resistant.
Ferrous equipment installed in concrete, or in direct contact with the earth, or in severely corrosive environments must also be suitable for that environment. The manufacturers’ zinc coating is typically acceptable for that purpose. If additional protection is required, PVC-coated raceways are available, as well as a variety of supplemental corrosion protection techniques. Aluminum equipment in contact with concrete or the earth does require supplementary corrosion protection, as stated in NEC 300.6(B). Deterioration of non-metallic materials is also possible and can be a concern in some environments, such as areas with solvents.
NEC Sections 342.10 for intermediate metal conduit (IMC), 344.10 for rigid metal conduit (RMC), and 358.10 for electrical metallic tubing (EMT) allow galvanized steel in concrete, in direct contact with the earth and severely corrosive environments. These products have safely been used for many years in those environments.
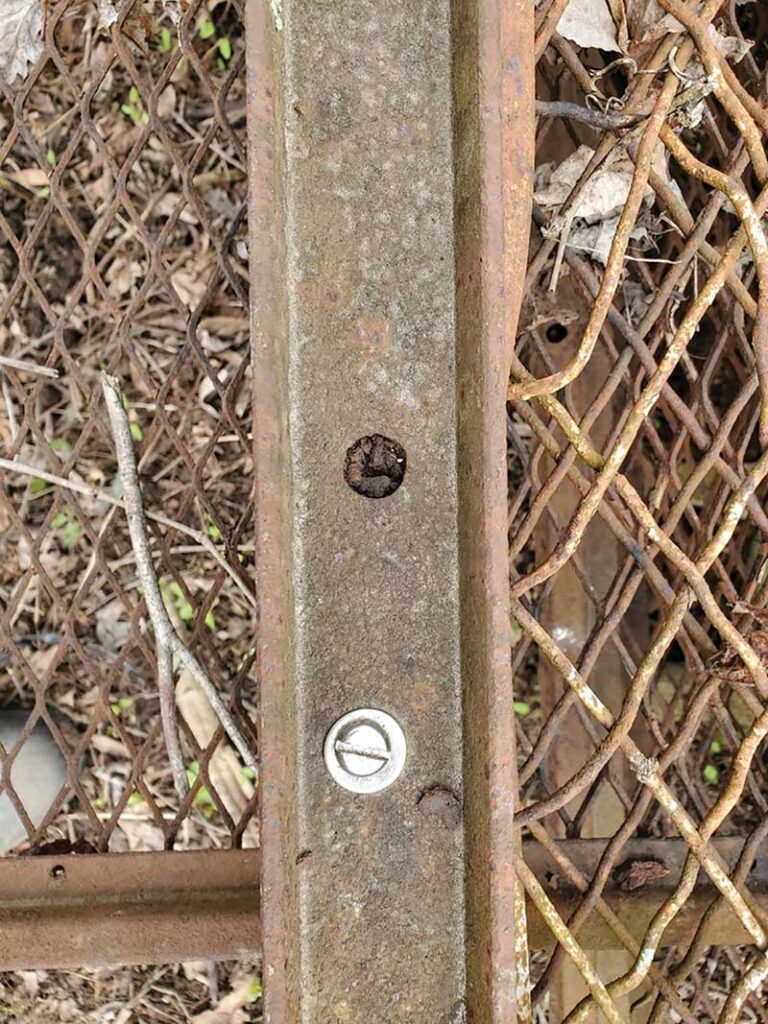
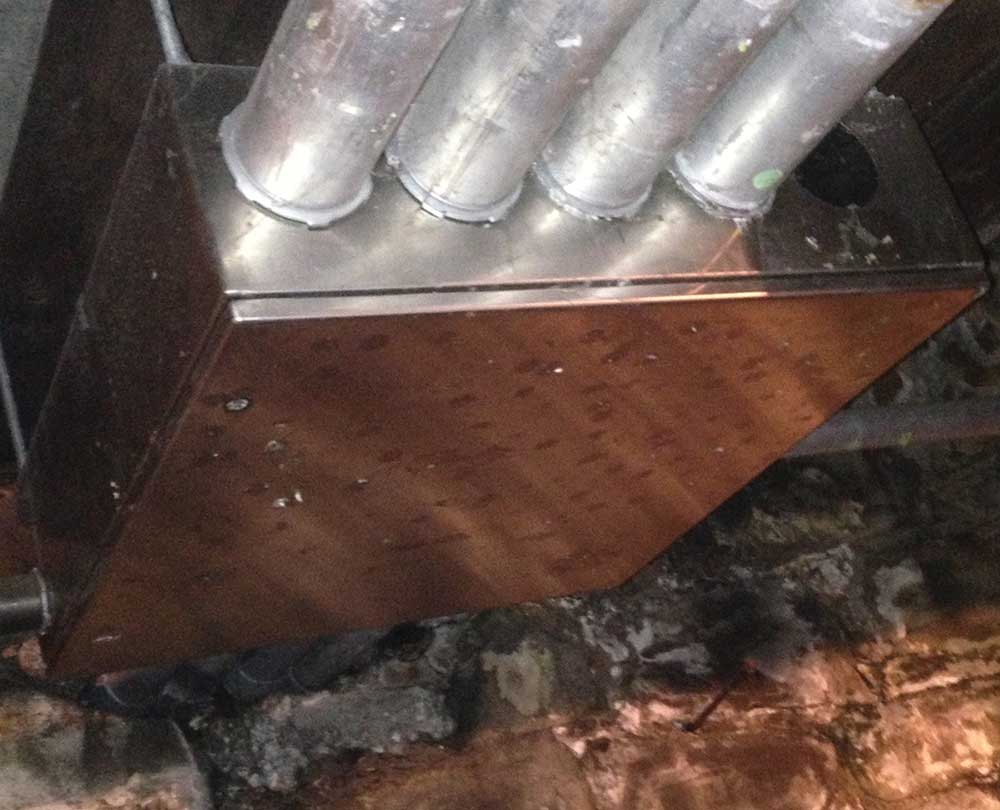
The soil type also influences the degree of corrosion. Lower-resistivity soils are more corrosive than ones with higher resistivity and are often dealt with at a local level.
UL Product iQ contains the following Guide Information for Rigid Ferrous Metal Conduit under UL® Category (CCN) DYIX and is available at: https://iq.ulprospector.com/en/profile?e=207305
“Galvanized rigid steel conduit installed in concrete does not require supplementary corrosion protection.
Galvanized rigid steel conduit installed in contact with soil does not generally require supplementary corrosion protection.
In the absence of specific local experience, soils producing severe corrosive effects are generally characterized by low resistivity (less than 2000 ohm-centimeters).
Wherever ferrous metal conduit runs directly from concrete encasement to soil burial, severe corrosive effects are likely to occur on the metal in contact with the soil.
Conduit that is provided with a metallic or nonmetallic coating, or a combination of both, has been investigated for resistance to atmospheric corrosion. Nonmetallic outer coatings that are part of the required resistance to corrosion have been additionally investigated for resistance to the effects of sunlight.
Rigid metal conduit with or without a nonmetallic coating has not been investigated for severely corrosive conditions.”
UL Product iQ contains the following Guide Information for Electrical Metallic Tubing under UL Category (CCN) FJMX and is available at: https://iq.ulprospector.com/en/profile?e=207693
“Galvanized or stainless steel EMT installed in concrete on grade or above generally requires no supplementary corrosion protection. Galvanized steel EMT in concrete slab below grade level may require supplementary corrosion protection.
In general, galvanized steel EMT in contact with soil requires supplementary corrosion protection. Where galvanized steel EMT without supplementary corrosion protection extends directly from concrete encasement to soil burial, severe corrosive effects are likely to occur on the metal in contact with the soil.
Galvanized or stainless steel EMT that is provided with a metallic or nonmetallic coating, or a combination of both, has been investigated for resistance to atmospheric corrosion. Nonmetallic outer coatings that are part of the required resistance to corrosion have been additionally investigated for resistance to the effects of sunlight.
Galvanized steel EMT with or without a nonmetallic coating has not been investigated for severely corrosive conditions.
Aluminum EMT used in concrete or in contact with soil requires supplementary corrosion protection.”
Although not specifically addressed in the NEC, the point where a wiring method emerges from concrete or grade is also a location that is often subject to more rapid corrosion. Products are available such as tapes, sleeves, or wraps that can be used at those points for additional protection.
Notice in photo 1 that the stainless-steel screw is not corroded, but the steel frame is.
Dissimilar Metals
As noted in the galvanic corrosion definition provided, if different metals are in electrical contact with each other, and an electrolyte is present, one metal can corrode faster or more than the other. The electrolyte contains conductive substances, such as minerals in the water, which allow ions (electrically charged atoms) to cause movement of material from one metal to another. The amounts and types of metals change the effect.
Different materials and alloys can have different electrochemical properties. More noble metals (cathodic) are those that are resistant to corrosion. The potential difference (voltage) between different materials creates current through the electrolyte. This current causes corrosion of the less noble metal (anode). The relationship of nobilities is called the Galvanic Series. The amount of each type of material in contact also affects corrosion. See figure 1 for the galvanic series of metals in saltwater.
NEC Sections 342.14 for intermediate metal conduit (IMC), 344.14 for rigid metal conduit (RMC), and 358.14 for electrical metallic tubing (EMT) have requirements for dissimilar metals. Never installing different metals in electrical contact with each other might be ideal, but that is not always practicable. The second sentence of those sections allows stainless-steel fittings and stainless-steel enclosures to be used with galvanized steel raceways where not subject to severe corrosive influences. The reason that stainless-steel fittings, couplings, and enclosures are allowed to make the transition, but their galvanized counterparts are not, is because of their position in the Galvanic Series (anodic/cathodic chart). The closer an alloy is to the cathodic end of the table, the less likely it is to corrode. The process of being a cathode and receiving electrons protects the alloy from corrosion, while the process of creating electrons (anode) opens an alloy up to corrosion.
Since stainless steel is closer to the cathodic end of the table than galvanized steel, it becomes the cathode, and the galvanized steel becomes the anode. As the anode, the galvanized steel becomes the sacrificial material in the galvanic corrosion/reaction process. The smaller the surface of the galvanized product compared to the stainless product connected to it, the faster the corrosion will occur. Therefore, if you have a galvanized coupling making the transition from stainless steel to galvanized steel in a wet location, that coupling will become the sacrificial object in the corrosion process and could corrode much more quickly than originally anticipated. Now, if you use a stainless-steel coupling in the same scenario, it becomes the cathode, so the galvanized conduit becomes the anode and sacrificial object — but since the galvanized conduit’s surface area is so much greater than the stainless steel coupling’s surface area, the galvanic reaction will have minimal effect on the original life span expectations of the conduit.
Changes have been made to these sections in recent editions of the NEC to provide more detail about reducing galvanic action. Varying interpretations of what is meant have resulted based on the revised wording. Keeping in mind the concept of galvanic corrosion and the amounts of material while applying all of the requirements in Sections 342.14, 344.14, and 358.14 will help with understanding.
Stainless-steel conduit has been used at various industrial facilities such as in hazardous (classified) locations at chemical plants and refineries for many years. Because of the additional cost of stainless steel, transitions are made to galvanized steel conduit outside of the severely corrosive environment. Stainless couplings or fittings used to make the transition are acceptable based on the second sentence of Sections 342.14, 344.14, and 358.14.
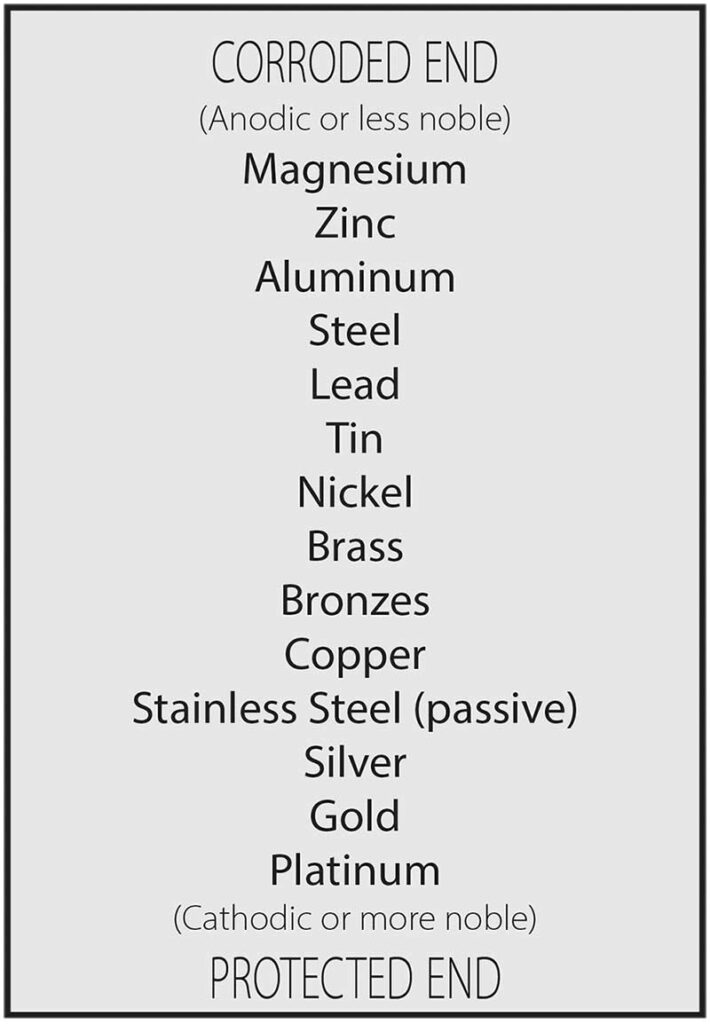
Summary
Steel conduit and electrical metallic tubing (EMT) have been safely used for many years in various environments. Consider the materials available and the environment during the design to help ensure that their safe use continues.
For more information, see the Steel Tube Institute’s Guidelines for Installing Steel Conduit / Tubing and ANSI® / NECA® 101 Standard for Installing Steel Conduits (Rigid, IMC, EMT at https://steeltubeinstitute.org/ or https://www.neca-neis.org/
Find Us on Socials