From time to time, a request is made, typically by an installing electrical contractor, to label some or all the components of a modular wiring system with the circuit ID before shipping to the job site. The request for circuit ID typically applies to home run cable conductors, power distribution modules (PDM), and access floor boxes (AFB). Although circuit ID labeling may be standard practice for conventional “pipe & wire” electrical installations, modular plug-n-play wiring systems can be more beneficial over the practice of pre-labeling system components with circuit IDs before they are shipped to and installed at a job site. Modular wiring systems are covered in NEC Article 604, Manufactured Wiring Systems. There are primarily three reasons manufacturers advocates against pre-labeling system components with the to-be-installed circuit IDs. Pre-labeled components:
- increase installation time and complexity by untold orders of magnitude;
- increase system management challenges; and
- decrease system safety.
Increased Installation Time And Complexity
On a typical system installation with unlabeled system components, the electrical installation crew simply places all system components as they are shown on the system layout drawings provided by the manufacturer. For instance, in a relatively small project of 100 workstations, the installation crew would place the 100 AFBs and perhaps 10 PDMs at their designated locations as shown on the layout drawings, interconnect the components with the appropriate length plug-n-play whips as designated on the layout drawings, and tie the home run cables’ conductors, by phase, into electrical panels and the installation is essentially done.
Nearly all of the simplicity and labor savings designed into the plug-n-play installation described above do not apply with a pre-labeled system. Now, instead of simply placing 100 AFBs at any of the 100 designated locations of the layout drawings, the electrical installation crew must search through all 100-floor boxes to find the one specific floor box that has the correct circuit ID label that matches the circuit designation recorded on the layout drawings for a specific AFB location. This same tedious and error-prone process is then repeated another 99 times, just to place the pre-labeled floor boxes in their proper locations. Repeat this process again for the ten PDMs. Finally, instead of simply tying the conductors of the home run cables to the appropriate breaker panel by phase, the electrician must find and land every uniquely labeled phase conductor to its designated breaker location in the panel. Now, imagine the multiplied time wasted, installer frustration, and potential for error on a project of 300 or 500 or more workstations.
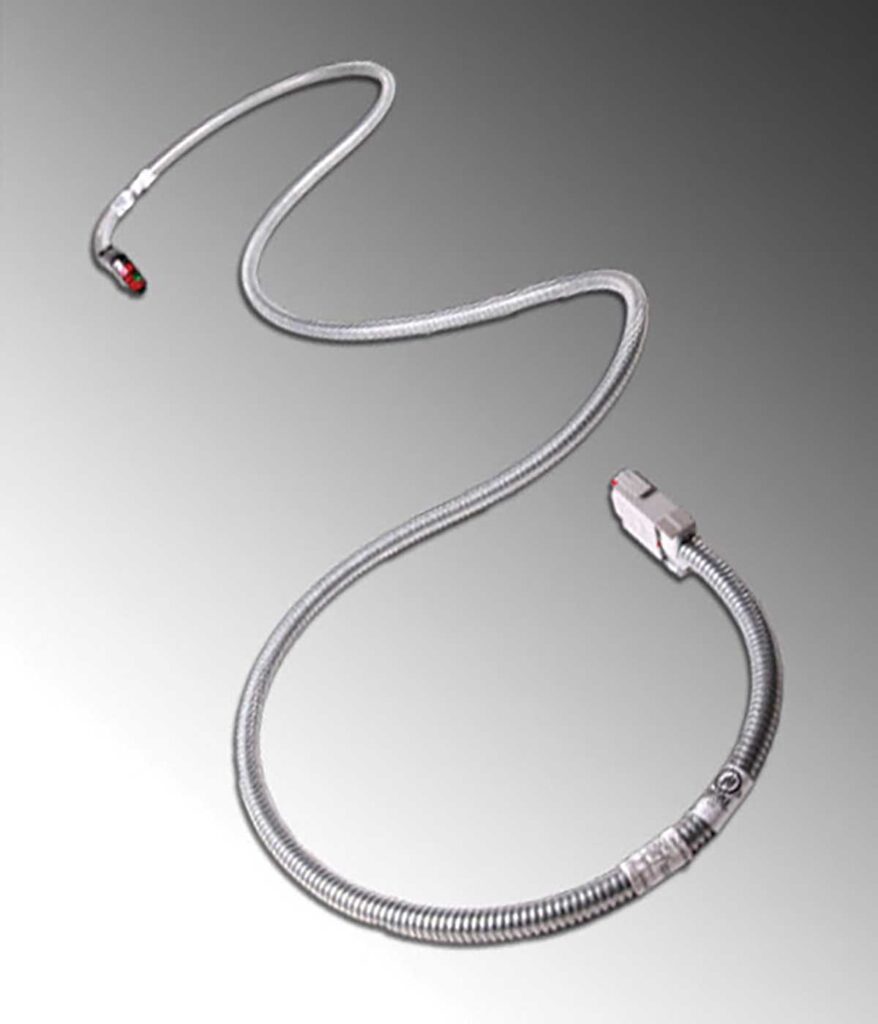
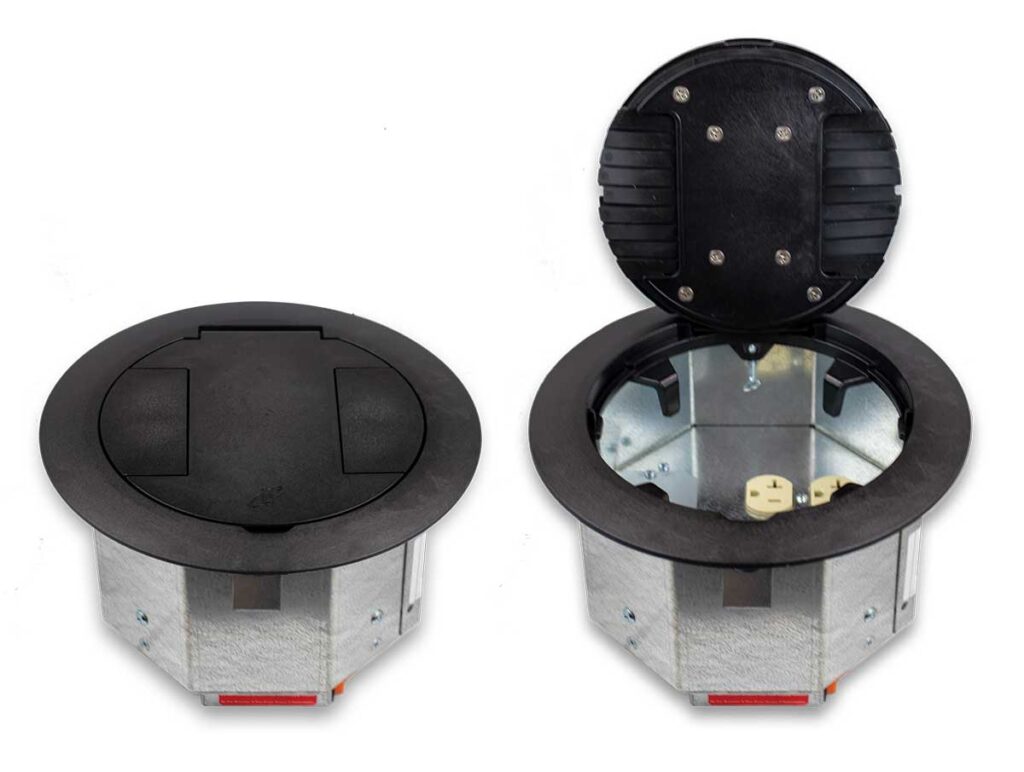
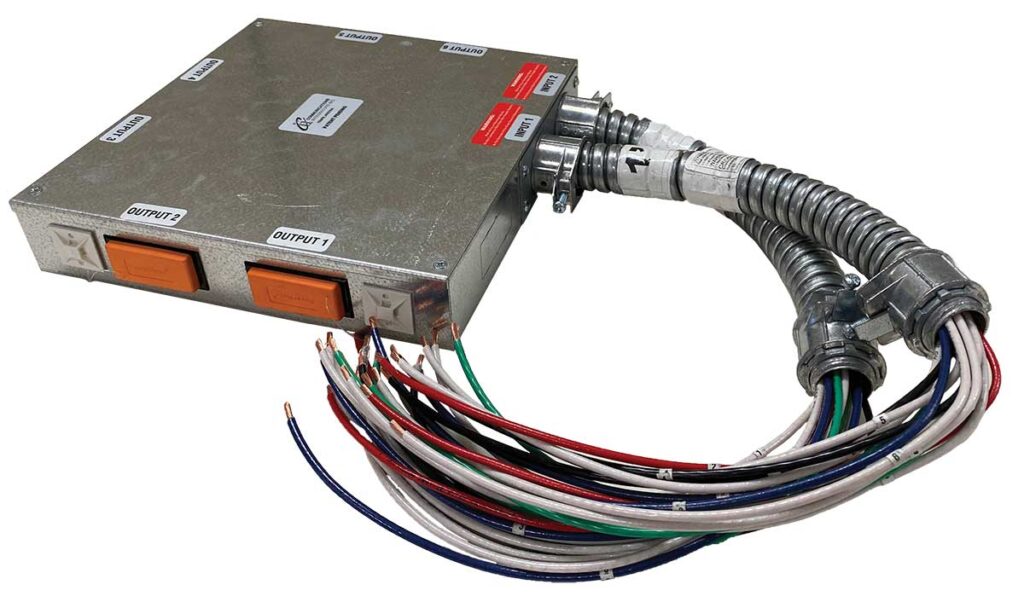
Increased System Management Challenges
A modular wiring system is designed and built to facilitate the easy relocation of the system components, minimizing the impact of the work environment churn on the business. In the event the components of the modular wiring system have been labeled with the as-installed circuit IDs, any and every relocation of these components (the AFBs in particular) will necessitate their re-labeling with their new circuit IDs.
The most typical relocation would involve moving an access floor box, and possibly its associated jumper cable, from its original PDM port to a vacant port of a different PDM, or even to a different port of the same PDM. This would then require re-labeling the relocated access floor box with a new circuit ID, given the different circuit(s) to which it would then be connected through its new PDM port location.
The task of correctly identifying circuit IDs is complicated when AFBs of different wiring configurations are employed on a project. It is not unusual for a project to have two or sometimes three different wiring configurations of access floor boxes, meaning that AFB “A” would be wired so that its outlet picked up circuits 1 & 3 from a PDM port, while AFB “B” is internally wired to pick up circuits 2 & 4, and so on. It’s not hard to imagine the difficulty in keeping all the varieties of possible circuit IDs straight after just a few rounds of office churn. An access floor box having an incorrect circuit ID presents a real maintenance safety hazard.
Decreased System Safety
If just one of these relabeling tasks is not 100% accurate, then over time and multiple relocations, this one mistake can very easily snowball, creating a system with many multiple components labeled with the wrong circuit ID.
A mislabeled component within a wiring system creates a substantial risk of bodily injury to anyone making changes to or working on the system. Although it is perfectly safe to relocate system components while the system is energized and under load, there is still a substantial risk to a technician who, at some point in the future may take it upon him or herself to open an access floor box while performing some sort of troubleshooting or maintenance task. Relying on incorrect circuit ID labeling for circuit identification, a technician may believe he or she has shut power off to a device when in fact, they have not, placing that technician at risk of receiving substantial injury, or worse.
Find Us on Socials