It’s a warm sunny day, and your facility is at full capacity, with everything humming along just right. Suddenly, the utility power drops out, and everything goes dark. You’re not worried, though, because you have a well-maintained generator that backs up your critical loads. Within seconds, the generator is up and running, and the loads transfer to the backup power.
Since you are conscientious about maintenance, you head out to the generator building to check the load on the generator. All the backed-up loads are up and running, and you want to make sure the generator is not overloaded, especially since it’s a warm day. Expecting to see a high load on the generator, you are surprised to see that the amp draw is less than 30% of the generator capacity. Why is your generator so oversized? Did the engineer who designed the facility get a kickback from the generator supplier for selecting a big and expensive unit?
The good news is there is no conspiracy to make generators bigger and more expensive than they need to be. Instead, there are several reasons that generators do end up being sized larger than what initially seems necessary.
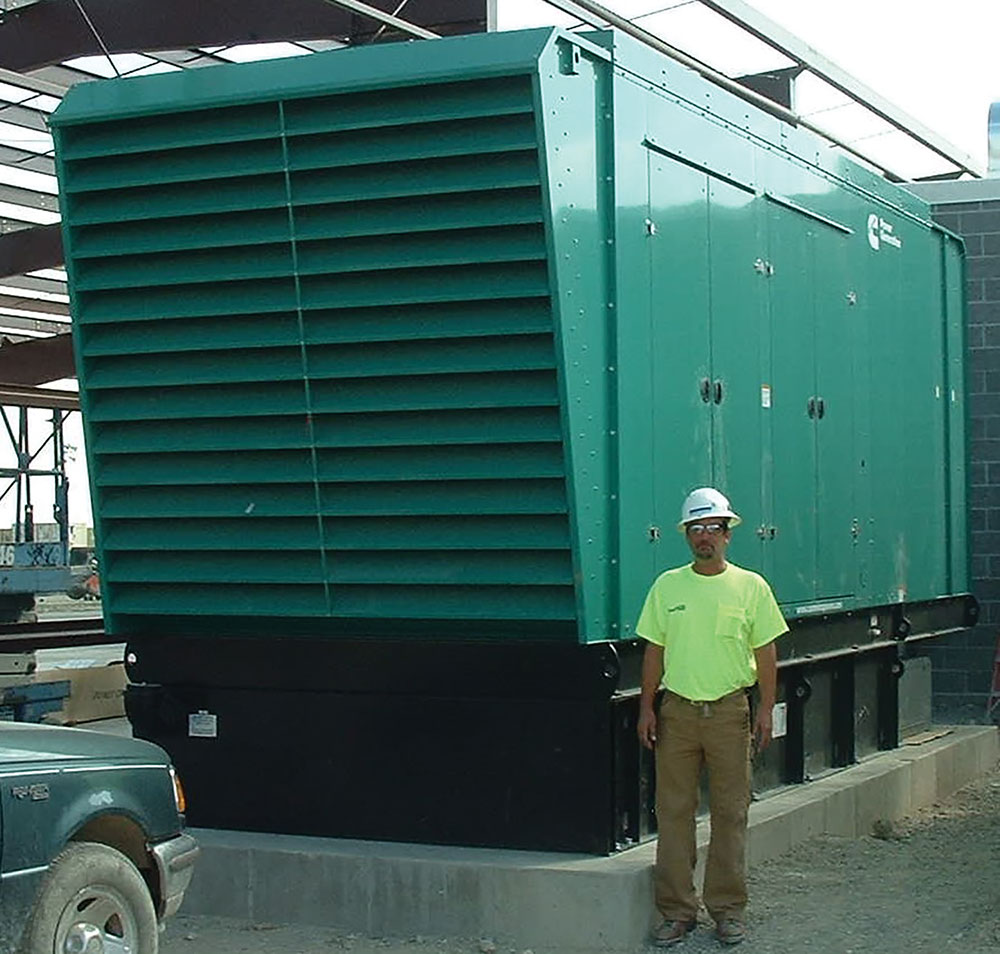
FACTORS IN GENERATOR SIZING
Infinite Bus vs. Finite Engine Capacity
An analogy to help differentiate between the electrical utility grid (an infinite bus) and a generator (a finite bus) is to think about what happens when you toss a baseball-sized rock into a large lake. It makes a splash, but unless the lake is still, it is difficult to follow the water ripples that emanate from the point of impact. In contrast, if you throw the same-sized rock with the same force into your bathtub, the splash and ripples have a noticeable and significant impact on the water and the surrounding area. It is possible that if the rock hits hard enough, it could even dent or damage the bathtub itself.
When something causes a disturbance to the electrical system (or if we continue with the analogy above, makes a splash), like a large motor starting, that disturbance may be noticeable in the nearby vicinity – the lights may instantaneously dim or flicker, but the effect dissipates quickly, and other items in the building will normally not even notice it. On the other hand, starting a large motor that is powered by a generator will certainly be noticed. The engine will lug down, causing the voltage and frequency at the output of the alternator to drop. If the generator is properly sized to accommodate this added load, it will quickly return to normal speed, but if it is undersized, as the voltage and frequency drop, the protective devices on the generator may shut it down. Also, other sensitive electrical loads may be affected by the drop in voltage and frequency.
Motor In-Rush Current
In the previous example, an across-the-line motor starting inrush current was used. Traditionally, the initial inrush current needed to get a motor spinning was about six times its running load current. With today’s more efficient motors, this inrush current can be much higher (as much as 13 times the running load current). This inrush of current to the starting motor creates a significant impact on the generator.
Allowance for Sensitive Equipment
Some equipment, such as Programmable Logic Controllers (PLCs) and other control systems, and even computer power supplies, can be sensitive to voltage and/or frequency dips. Some equipment will shut itself down when the voltage drops below a designated setpoint, and other equipment depends on the consistent 60Hz to regulate pulse timing within the control system. When a generator is sized, these items need to be taken into consideration. The generator also needs to be large enough to start the motors and other large loads in the facility without lugging down so much that the voltage and frequency drop below the tolerable level for this sensitive equipment.
Harmonics in the System
Harmonics, which are multiples of the fundamental 60Hz signal in the electrical system, are introduced any time switched transistors are used to rectify the power for power supplies in computers and other electronic devices, including VFD and UPS units. These cause four major problems:
- In a balanced three-phase system, the neutral current stays near zero because the phase shifts of the three phases add up to zero. However, with the third harmonic (180Hz), they are all in phase and therefore add on the neutral resulting in a high current on the neutral where there should be none. That neutral current travels back to and must be dissipated in the generator.
- Overheating of wires and equipment, including the generator, is often an issue when harmonics are present.
- With the basic sine wave modified by harmonics, the signal’s zero-crossing points can get shifted, which can interfere with the timing functions in electronic systems, including the voltage regulation system of the generator.
- Harmonics can also cause insulation breakdown on motor winding wires. The alternator on a generator is basically an electrical motor that is producing power instead of consuming it. The presence of harmonics in the system will shorten the life of the alternator.
With all these factors, the generator must be bigger to make it less susceptible to harmonics.
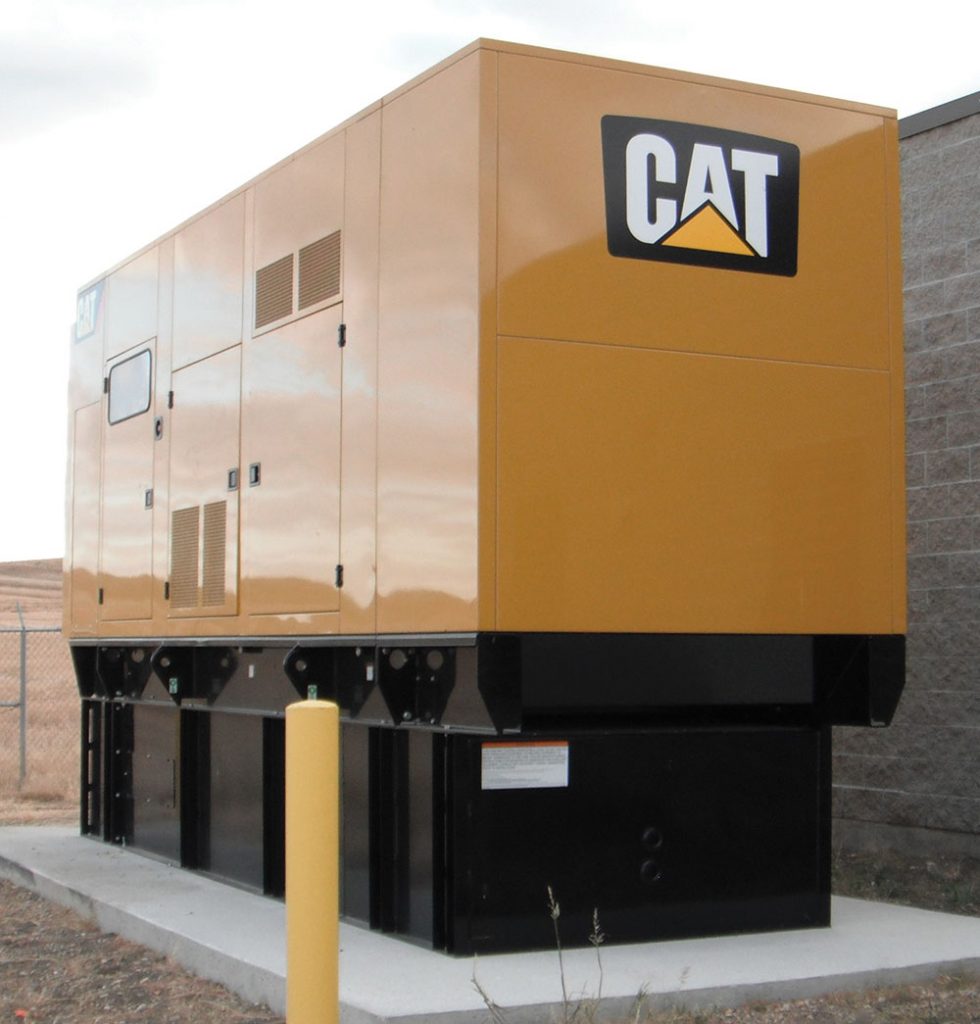
Regenerated Power in the System
When a motor is running and pushing its load, it is using power. When it is spinning because that load is pushing it, it becomes a generator and injects power into the electrical system. This phenomenon is used on electric cars to help put power back into the batteries when the driver hits the breaks. Not only does it slow the vehicle, but it also produces power.
With buildings, this situation is commonly used with the breaking mechanisms in elevators. When this occurs with normal power in the building (infinite bus), the power is easily absorbed by other loads on the system or by the utility’s greater electrical grid. When the regenerated power is applied to a generator-powered system (finite bus), the power needs to go somewhere. If there are not enough other loads on the system, it goes back to the generator.
One way to deal with this is to add a resistive load bank to help absorb the power that’s fed back into the system. Another way to help is by adding additional building load to the generator’s backed-up system. Either way, the generator needs to be upsized to accommodate this regenerative power.
Fire Pump Backup
When fire pumps are required for fire sprinkler protection in a building, the NEC states that “Electrical motor-driven fire pumps shall have a reliable source of power.” NFPA 20 gives some criteria for determining if a utility power source is considered reliable or not. Ultimately it is the Authority Having Jurisdiction’s (AHJ) call as to whether the fire pump needs to be backed up using the generator or not. When it is required, the generator needs to be sized to start and run the fire pump motor, no matter when that power is required. It is important to note that NEC 695.7 requires that there be no more than a 15% voltage dip during fire pump startup. Depending on the type of starter used, this requirement can cause the generator size to grow. Also, this pump will only run during a fire, so normally this headroom in the generator size, while vital, would never need to be used.
Conservative Nature of the NEC
As a young engineer, I was often surprised that utilities would size their transformers significantly smaller than the load I had calculated while following NEC guidelines. When asked, they responded that they used their formulas to determine what power buildings really need. The National Electrical Code is very conservative when it comes to how things must be sized, and they’re right to do so because the last thing we want is a fire caused by an overloaded branch circuit or feed.
Regarding the sizing of generators, the 2017 NEC states, “An emergency system shall have adequate capacity and rating for all loads to be operated simultaneously” [NEC 700.4 & NEC 701.4]. This was problematic when it was clear that some of the backed-up loads would never run simultaneously or when there would clearly be a diversity in the power use of the backed-up loads.
The 2020 NEC now reads, “An emergency (or legally required) system shall have adequate capacity in accordance with Article 220 or by another approved method [NEC 700.4 & NEC 701.4]. Article 220 allows for reasonable (albeit conservative) diversity factors to be applied to the load calculations. (Similar allowances are made for Optional Standby Systems [NEC 702.4].)
It is important to note that the generator sizing is handled a bit differently for health care facilities. In section 517.31(D), it says:
Demand calculations for sizing of the alternate power source(s) shall be based on any of the following:
(1) Prudent demand factors and historical data
(2) Connected load
(3) Feeder calculation procedures described in Article 220
(4) Any combination of the above
The sizing requirements in 700.4 and 701.4 shall not apply to an alternate power source(s).
Also, for Critical Operations Power Systems (COPS), the Code states, “A COPS shall have capacity and rating for all loads to be operated simultaneously for continuous operation with variable load for an unlimited number of hours. . . .” [NEC 708.22].
From these requirements and the conservative nature of the NEC, generators will naturally be oversized to some extent.
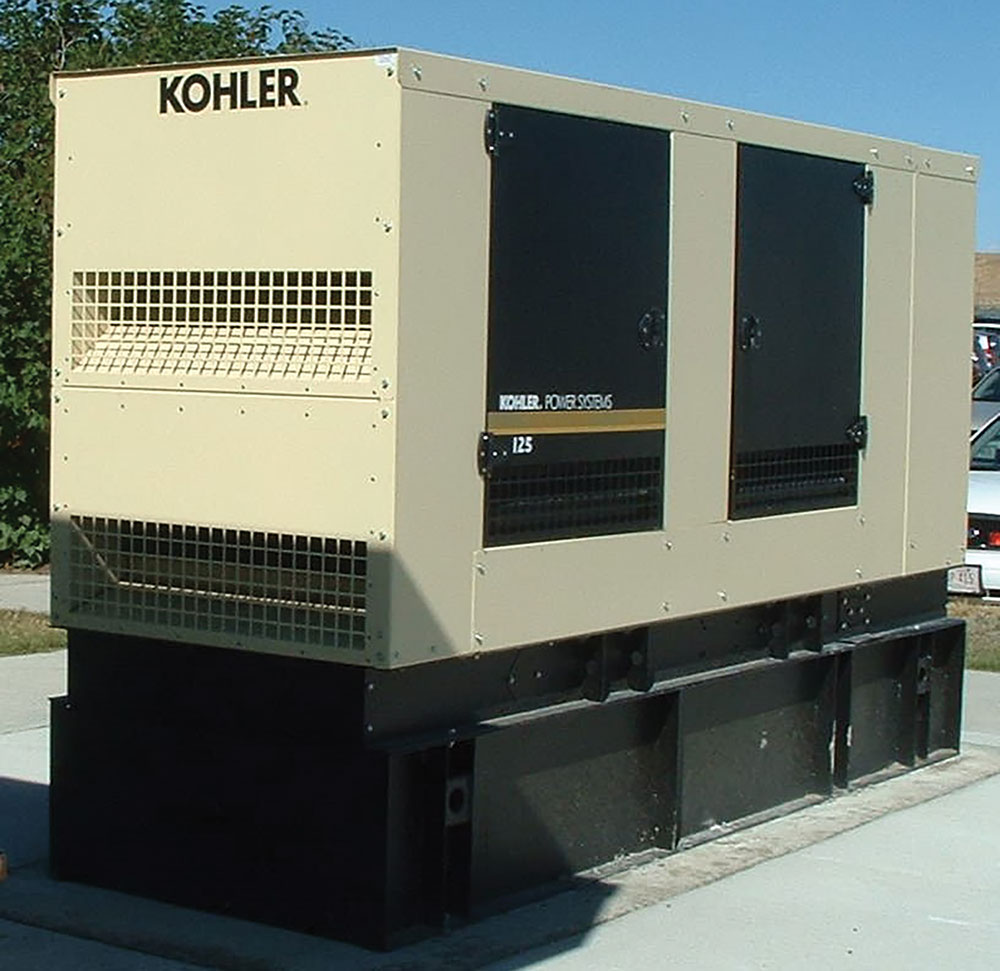
Capacity for Future Expansion
Another thing that makes generators larger is when the design involves making provisions for additional future loads. Unless the future expansion is definite and the future load is known (due to the relationship of calculated load to actual measured load as noted above), it is often wise to wait on future expansions. At the time of the expansion, you can measure the actual load and use the provisions of NEC Section 220.87 to determine the load on the generator. There will usually be plenty of headroom on the generator to accommodate those future expansions.
Loose Specifications
Generators are often specified by electrical engineers who have a good understanding of the electrical aspects of the system but may not be as acquainted with the intricacies of the internal combustion engine. Therefore, when writing the generator specification, there may be some requirements that get left in the spec when they may not be vital, or even appropriate, for the system.
Engine performance is significantly affected by the elevation of the installation, and generators installed at higher elevations need to be derated. Sometimes an engineer will run the sizing program for a specific manufacturer’s generator and use that calculated size in the specification. Within the sizing program, that size will have been derated for the elevation, but when a competitor tries to cross the unit, he assumes that it is the minimum size unit, sees the elevation, and derates his generator, making it that much larger. Keep in mind that not all manufacturers derate their gensets the same and at a particular elevation, and one manufacturer may need to derate while another manufacturer’s base unit may handle that elevation.
Another specified constraint that can oversize the generator is the voltage and frequency dip requirements for sensitive equipment. The specification may say these requirements must be maintained for the entire 100% block load when the loads are scheduled to come on in steps, and the generator will not be hit with the full load all at once.
When large motors in the facility are driving the generator size, it is important to not just assume that those motors are all 100% loaded. Often the actual load factor is around 80%. If this is not considered, the generator will be oversized.
Having addressed the overly conservative nature of the NEC, it is only fair that we mention the overly conservative nature of engineers too. Oftentimes if the implications of a requirement are not completely clear, engineers will choose the safer, more conservative option. This nearly always leads to the use of a larger generator.
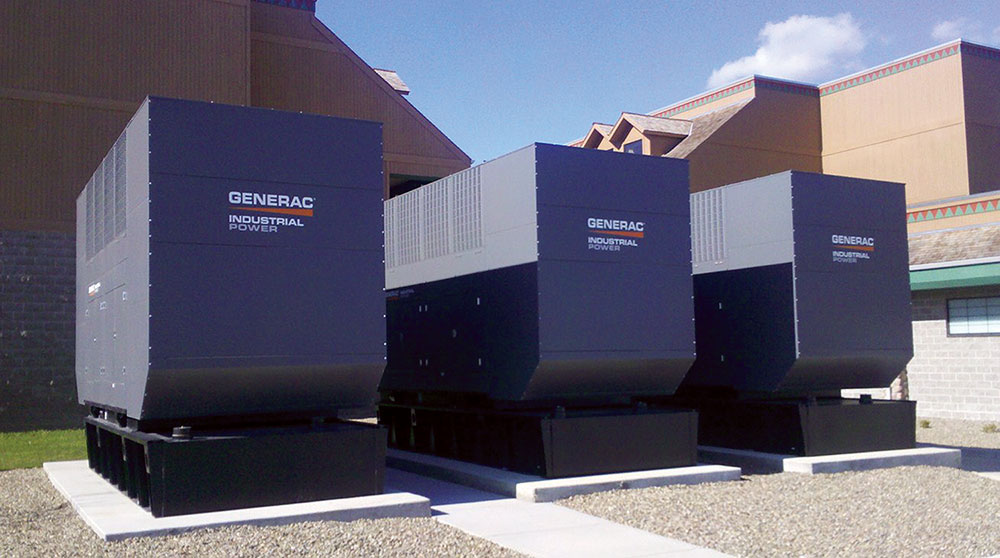
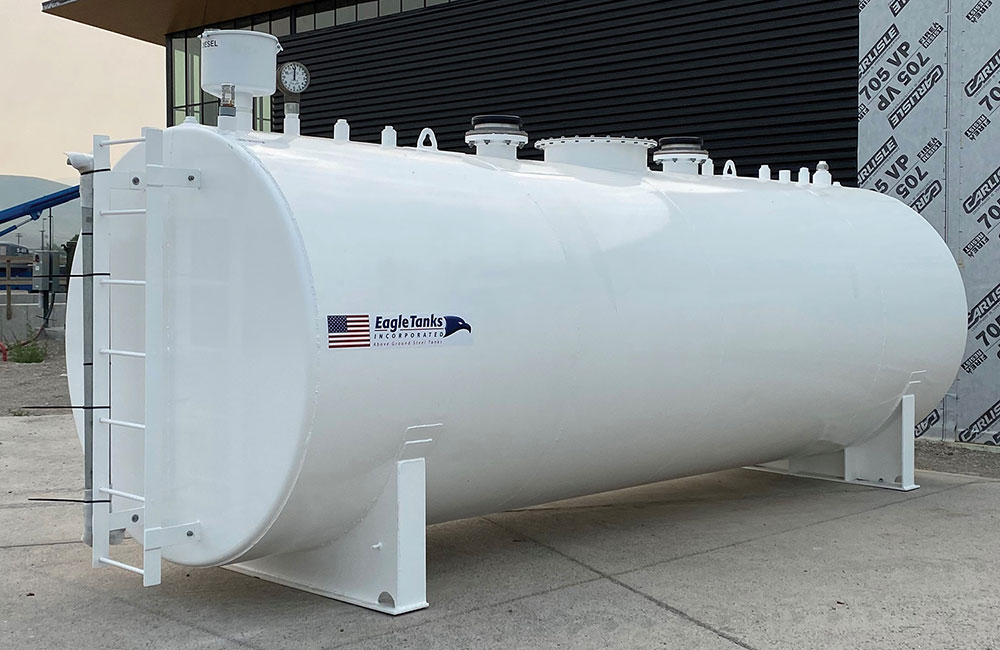
IDEAS FOR SMALLER GENERATOR SIZING
There are some things we can do to reduce the size of generators in our projects.
1. Phased Addition of Large Loads
When a load like a large motor is applied to the generator, the engine tends to lug down while the initial motor inrush is provided. If these motor loads can be staggered, so they don’t all come online at the very same instant, the generator won’t get hit so hard. If you’ve ever rented a second-story apartment and it was time to move out, you’ve experienced the same thing.
Let’s say your roommate was helping you move and was on the balcony tossing books to you one by one, and you were putting each one into your backpack; it would be much easier than trying to catch a box with all the books together. In the end, you carried all the books out to your truck, but you weren’t destroyed by trying to catch a box in one crushing blow.
Similar to this situation where it would be easiest to catch the largest books first before your backpack gets heavy, it is best to start the largest motors first. Working through motor starting scenarios with generator-sizing programs reveals that generators can be sized smaller just by a staggering startup of large motors and starting them first.
As noted above, with across-the-line starters, the motor inrush current is significant. This can be tempered by using soft starters or VFDs to bring the motors up to speed more gradually. Fortunately, VFDs are becoming more and more common as they allow for much greater control of the motor. With VFDs, the harmonic problem is lessened by specifying 12-pulse instead of 6-pulse units or by appropriately applying filters on the input of the unit. Likewise, the alternator on the generator can sometimes be sized up to deal with harmonics without having to enlarge the engine. Additionally, with control schemes in use, delays can be set up to ensure that the large motors are not all trying to start simultaneously once the generator is running.
2. Load Shedding
Often when a generator is installed in a facility, there are requirements for emergency, legally required standby, and optional standby systems. Generally, each of these separate “branches” is given its own transfer switch. The emergency loads need to come on within 10 seconds of a power outage. The legally required standby loads have 60 seconds to come on, and optional standby loads can be delayed or transferred manually. Care needs to be taken with which loads are assigned to which branch of the system. Modern generators can send signals to shed load if they are not able to keep up with the demand. These signals are stepped, and the struggling generator drops off the optional standby branch first, and then the legally required branch leaving the emergency branch on until the generator completely fails.
With these separate transfer switches, the owner also has some ability to shuffle the optional standby system loads the generator will need to supply. Some loads are more or less important based on the season of the year or the current functions within the building, so the owner can decide what can be omitted at any given time. With this capability, the generator can be sized smaller because it will only feed the most essential loads.
The generator can also cause a shunt-trip breaker to drop a less necessary load. This can be used in a smaller facility where the owner wants to back up the entire system. In this scenario, the generator could be sized smaller than needed to match the full calculated load for the entire facility. But it is important to remember that the service entrance transfer switch would need to be sized in accordance with NEC 220 to handle the full load. The generator can then be smaller based on the load shed. As noted above, because of the conservative nature of the NEC, it is possible that once installed and operational, the generator will sufficiently handle the full load, and the shunt-trip breaker will never have to drop out the load.
Kohler is a generator manufacturer with a load control feature built into the transfer switch control that monitors the load. The downstream shunt-trip (or electrically operated breakers) are tripped by a signal from the transfer switch. This is particularly useful for an existing installation in instances where the owner wants to add load to a genset that is already at capacity and is not capable of monitoring or issuing a load shed signal. When electrically operated breakers are used, if the load on the genset drops, the breaker could re-close and re-energize that load.
3. Generator Paralleling
Generator paralleling formerly involved the use of large switchgear with complex synchronizing hardware and motor-driven, mechanically operated breakers to parallel the sources. Because this gear was large and expensive, generator paralleling was a big commitment, and additional space had to be included for any future expansion. Over the past couple of decades, however, paralleling of generators has become much easier and much more common. Large switchgear is no longer necessary, and synchronizing can occur within the generators’ onboard electronic control panels. Planning ahead is still required, but one or two smaller generators with paralleling capability can be installed now. Other units can come online later as the load grows and evolves.
Other advantages to paralleling generators are that, as the load fluctuates, the control system can bring on an additional generator when needed or drop it when not. Then, if the generators are sized so any one of the paralleled units can handle the most critical load, there is greater assurance that load will always have power. Finally, depending on the system and the generator sizes, installing two smaller generators may be more cost-effective than one large one.
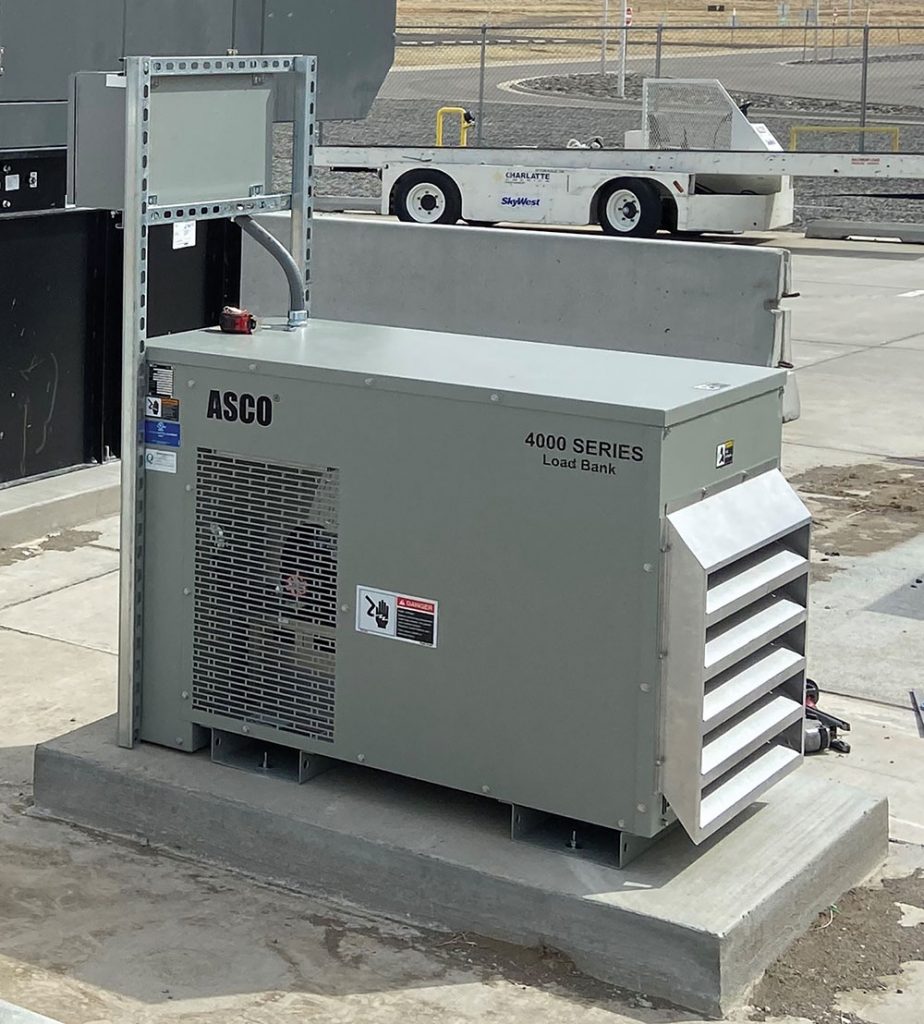
ADVANTAGES OF SMALLER-SIZED GENERATORS
The most obvious advantage of installing a smaller generator is less upfront investment in equipment, sizing for the concrete pad, and housing. Others include less space needed to store fuel and measures needed to prevent wet stacking.
In some cases, based on the reliability of the supply, natural gas can fuel generators. Most often, however, generator fuel needs to be stored on site. The quantity of stored fuel for the system is prescribed in the NFPA 110, based on the availability of fuel for a refill, and must be in accordance with the approval of the AHJ. The smaller the generator, the less fuel it uses, which reduces the need for fuel storage space. Storing too much fuel also becomes problematic because the fuel can get old or contaminated, so the smaller the generator, the better.
It is important to maintain and exercise a generator regularly. It should be run at least once per month, for at least 30 minutes, and with at least 30% load. A generator rep once equated this to having an old pickup truck that you don’t often drive but want to make sure it will start on cold, snowy mornings. You should at least start it up once and a while, then take it out for a quick drive, allowing all the parts to be lubricated and make sure the batteries are well charged. Regularly exercising the generator brings you peace of mind that it will function when needed.
Over time, if the active load on a diesel generator is too low, moisture, carbon, and unburned fuel particles will build up in the exhaust system. This is referred to as wet stacking, which will eventually cause the engine to fail. When the regular load is less than 30% of its capacity, the generator needs to be run annually with a load bank to purge this wet stacking condition. If the diesel generator can be sized small enough, this annual load bank testing can be avoided.
FINAL THOUGHTS
With code requirements and the nature of standby/emergency power needs, your generator will likely still seem oversized when it is being tested or running during a power outage situation. However, by carefully analyzing system loads and code requirements, gross generator oversizing can be avoided.
Find Us on Socials