Microinverters and AC PV modules are becoming very common in residential and small commercial PV systems. See photos 1 and 2. They have even been used in PV systems rated at 60 kW and above. They have some common features. For example, microinverters and AC PV modules have similar ac output characteristics, connections and code requirements. However, they are different from the typical PV string inverters that use multiple modules connected in series and have dc voltages in the 200–600 volt range. The microinverters and AC PV modules typically operate with just one PV module and the dc voltages are less than 100 volts.
Instructions supplied with these listed products should be followed [NEC110.3(B)]. The suggestions below do not substitute for compliance with theNECor local codes.
Grounding
Both the AC PV module and the microinverter will require equipment-grounding connections where there is any exposed metal in these devices. A grounding electrode conductor (GEC) connection will be required when the microinverter operates the module in a grounded manner.
Equipment/Safety Grounding
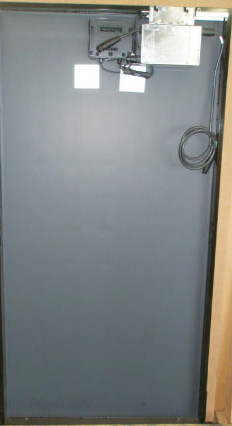
Photo 1. PV microinverter with exposed dc cables and connectors to PV module
The ac output circuit cable of some microinverters and AC PV modules does not have an ac equipment grounding conductor (EGC). This EGC conductor must be started (originated) in the transition box on the roof where each set of inverters has the final factory ac output cable connected to another wiring system. The ac equipment grounding conductor should also be attached to the microinverter enclosure. This ac EGC must be routed all the way back to the service-entrance bonding point as it is in any other ac circuit. There is no requirement that it be unspliced and the size will typically be 14 AWG per Table 250.122.
System/Functional Grounding
True AC PV modules where there are no readily accessible dc conductors or dc disconnect will normally not require a grounding electrode conductor. Since both the requirements in the 2005NEC690.47(C) and the permitted 690.47(C) in the 2008NECare both based on Article 250, the provisions of either editions of the Code appear to be applicable in jurisdictions using either edition. Section 690.47(C) in the 2011NECcombined and clarified 2005 and 2008 code requirements in this area.
Under UL Standard 1741 the microinverter, if it isolates the dc grounded input conductor (assuming a grounded PV module) from the ac output, must have a dc grounding electrode conductor (GEC) running from the grounding electrode terminal on the microinverter case to a dc grounding electrode. If the microinverter operates the PV module as an ungrounded system (neither positive nor negative connected to ground), then no grounding electrode conductor would be required.
Section 690.47(C) in the 2008 NEC permits the use of a combined ac EGC and dc grounding electrode conductor (GEC) from the inverter. The 2011NEChas this requirement in 690.47(C)(3). UL 1741 requires the dc GEC terminal on the outside of the inverter. If this option is elected, then the 8 AWG minimum (250.166) conductor from each inverter must be bonded to the input and output of each metal conduit and metal box that it travels through until it gets to the main grounding bar in the service entrance equipment. The bonding requirement and 8 AWG size would appear to rule out the use of 10-3 with ground type NM cable for the ac output circuit inside the building. The bonding requirement may also be cumbersome to implement multiple times and the routing of this combined conductor may induce lightning surges to enter the main load center and other branch circuits. The permissive method of grounding described in 690.47(C) in the 2008NECmay also be used under the 2005NEC.
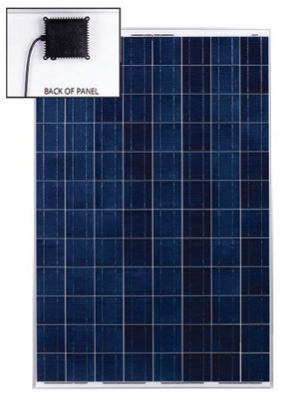
Photo 2. AC PV module. No exposed dc cables or connectors. Courtesy Exeltech.
Alternatively, the permissive grounding method described in the 2005 NEC 690.47 may also be used under the 2008NECas an alternative to the 2008 NEC 690.47. Section 690.47(C) in the 2005NECand 690.47(C) in the 2008 NEC are based on the general requirements of Article 250.
Section 690.47(C) in the 2011 NEC combines and clarifies the grounding methods described in the 2005 and 2008 NEC.
The Exception in 690.47(D) in the 2008 NEC regarding array grounding is not clear. The subject of the section refers to array grounding electrodes. It is not clear if the Exception removes the requirement for an additional array grounding electrode only and leaves the requirement for the array GEC or removes the requirement for both. The intent of the submittal was to use a new array GEC to ground the array to an existing electrode or for a ground-mounted array, to a new grounding electrode at the array location. This would be particularly important in a high lightning area, but that is a performance issue, not a safety issue. This section was not in the 2005 NECand was removed from the 2011 NEC. An auxiliary grounding electrode is always an option under 250.54.
The size of the dc grounding electrode conductor is determined by 250.166, and this section has been clarified in the 2008NEC. In many cases, but not all, a 6 AWG bare copper conductor will meet the requirements. Where a UFER (concrete-encased electrode) is used, a 4 AWG grounding electrode conductor will usually be required. A short 6 AWG conductor may have to be irreversibly spliced to the 4 AWG conductor at each microinverter and connected to the microinverter grounding terminal if the inverter grounding terminal will not accept a 4 AWG conductor directly. An alternative would be to drive a single ground rod six or more feet from the UFER ground, ground the inverters and modules as described below with a 6 AWG bare copper grounding-electrode conductor and then bond the ground rod to the UFER with a 4 AWG bonding jumper (690.47(C)(1) in 2005 and 2011NEC).
The dc grounding electrode conductor may terminate at the service-entrance grounding electrode or at a grounding electrode associated with any subpanel where the inverter dedicated circuits end in backfed breakers under the 2005NEC. Under the 2008NEC, the combined conductor dc GEC/ac EGC can be terminated at the main service grounding bus bar or at any subpanel bus bar that has a grounding electrode attached and where the inverter backfed breaker terminates. The 2011NECallows either location to be used.
Disconnects
The microinverters should be installed in compliance with 690.14(D) of theNEC. As noted in this section, there are requirements for dc and ac disconnects on the roof in this not-readily accessible area, and an additional ac disconnect in a readily accessible location.
The relatively low dc voltage (usually less than 70 volts) and currents (less than 8 amps) may allow the dc connectors on the microinverter inverter to serve as the dc disconnects for servicing the inverter. In a similar manner, the ac connectors on the microinverters and AC PV modules could be used as the maintenance disconnects required by 690.15. Microinverter and AC PV Module manufacturers can have the ac and dc connectors designed and listed with the microinverter or AC PV module as load break rated disconnects and this will allow the use of these connectors to meet Code requirements (690.14, 690.15 and 690.17).
Even with load break rated ac connectors, a transition box is needed to change from the flexible ac output cable to the code-required fixed wiring system that will enter the building. An inexpensive unfused 60-amp 240-volt air conditioning pull out disconnect would serve nicely and is already in a NEMA 3 R enclosure. It will also serve as an ac disconnect that when pulled, will shut down the microinverters or AC PV modules and opening the ac circuit will reduce the dc currents in the microinverter input cables and connectors to very near zero permitting safer opening of the dc disconnects.
Such a disconnect can also be used to meet some AHJ requirements for a non-connector disconnecting means on the roof.
Section 690.14(D)(3) requires an additional disconnect and that disconnect requirement may be met by the backfed breaker in the load center where the load center is positioned to meet the accessibility and location requirements of 690.14(C)(1). Some jurisdictions are requiring that this second ac disconnect be on the outside of the building and any utility-required disconnect on the inverter output circuit would usually meet this requirement.
AC Output Circuits
The output circuit of any utility-interactive inverter up to the first overcurrent protection device (OCPD) is very much like an ac branch circuit. If the utility voltage is removed from this circuit (for any reason), the circuit becomes de-energized (dead) — just like a branch circuit. If there is a line-to-line or line-to-ground fault on this circuit, the OCPD responds in a normal manner to the fault currents generated by the utility. The inverter(s) can generate no more than its rated current per UL Standard 1741 and when the fault occurs, the drop in line voltage will normally cause the inverter to shut down. And when the branch circuit breaker opens in response to the fault, the inverter shuts down.
It would appear that these inverter output circuits could be wired using any Chapter 3 wiring method suitable for the environment (hot, wet and UV outside and hot in attics). Grounding requirements or methods used for microinverters may dictate conductor sizes too large for 10 AWG type NM conductors.
An ac GFCI device should not be used to protect the dedicated circuit to the microinverter or ac PV module even though it is an outside circuit. None of the small GFCI devices (5 ma–30 ma) are designed for back feeding and will be damaged if backfed. In a similar manner, most ac AFCIs have not been evaluated for backfeeding and may be damaged if backfed with the output of a PV inverter.
Combining Multiple Sets of Microinvertersor AC PV Modules
In multiple strings of these inverters, there is no NEC requirement that an ac combining panel (load center) be located on the roof. In fact, most NEMA 3R load centers must be mounted against a surface to keep water from penetrating holes in the back panel and they must be mounted within 30 degrees or vertical. Such a surface may have to be added in order to properly mount a 3R load center on the roof. And then there might be problems meeting 110.26 clearance requirements. A further issue with OCPD on the roof is heating of the device over its rated 40 degrees Celsius operating temperature. Gray load centers in the sun will normally operate 10–20 degrees C hotter than the ambient temperature. This may be difficult to compensate for when considering available equipment, the size of the ac conductors attached to the inverters, and listing restrictions on the inverters. Nevertheless, it is possible to mount an ac load center on the roof with proper solar shielding and use it to combine the outputs of U-I inverters or sets of microinverters.
The rating of any combining panel and the ampacity of conductor from that panel to the backfed breaker in the main load center as well as the rating of the main load center and the backfed breaker must meet 690.64(B)/705.12(D) requirements. This requirement will require a combining panel and conductor with a rating nearly twice sum of all of the 15-amp or 20-amp backfed breakers used for each output. See the 120% allowance in 690.64(B)(2)/705.12(D)(2) and 690.64(B)(7)/705.12(D)(7).
The ac output conductor for a set of inverters must have an ampacity of 125% of the continuous currents for all of the inverters on that circuit. The backfed circuit breaker in the panel must be rated the same and if an odd current rating is determined, the breaker rating should be the next larger size. The breaker must protect the conductor under the conditions of use and the conductor ampacity must be derated for those conditions of use.
The ac output circuit from each set of inverters must have an equipment grounding conductor to facilitate OCPD operation during ac ground faults. Some microinverters have a three-wire output through a four-contact connector. The unused terminal in the connector is reserved for future use. The three active pins in the connector are 240-V L1 and L2, and a neutral. There is no ac equipment grounding conductor. This lack on an equipment grounding conductor in the cable requires that the equipment grounding conductor for the microinverter or ac PV module be an external connection to the inverter case, where the case is metal. This external equipment grounding conductor must be connected to the fixed wiring system (usually, but not always conduit) where that wiring system originates.
Unless the microinverter bracket has been designed and evaluated as a grounding/bonding jumper, grounding the microinverters does not ground the rack or the modules and visa versa.
There is only one ac neutral-to-ground bond in an ac electrical system. That bond is made in the existing service entrance equipment. No additional neutral-to-ground bonds should be made when installing a PV system unless a supply-side service entrance connection is made.
AC PV Module Grounding — A Gray Area
Combinations of PV modules and microinverters combined/assembled in the field or at the dealer or distributor do not meet the intent, definition, or requirements associated with true AC PV Modules as defined in 690.2 and in 690.6. As of early 2012 there is no specific size associated with either microinverters or ac PV modules. The power outputs are increasing with nearly every new product and are now in the 190–220 watt range.
Combinations of a microinverter and a PV module with exposed dc connectors and dc conductors between the PV module and the microinverter are being certified/listed as ac PV modules. Some of these products have instruction manuals that say the microinverter may not be removed from the PV module. Other manuals give specific instructions for removing the microinverter from the PV module for repair. At issue is the definition of an ac PV module as a factory assembled unit and the potential need to meet all dc code requirements for these products with exposed dc connectors and dc conductors. Connectors are subject to loosening or being opened in the field. Connectors and conductors are exposed to environmental degradation, ground faults, and animal damage.
Also at issue in the ac PV module is the microinverter-to-PV module frame bonding when the mechanical/electrical connection is broken in the field. When the microinverter is replaced, how is the bonding connection quality verified and how is the certification/listing maintained without NRTL evaluation?
At some point, these issues will be addressed in UL Standard 1741 and possibly in theNational Electrical Code.
For Additional Information
If this article has raised questions, do not hesitate to contact the author by phone or e-mail. E-mail: jwiles@nmsu.edu Phone: 575-646-6105
See the web site below for a schedule of presentations on PV and the Code.
The Southwest Technology Development Institute web site maintains a PV Systems Inspector/Installer Checklist and all copies of the previous “Perspectives on PV” articles for easy downloading. A color copy of the latest version (1.91) of the 150-page, Photovoltaic Power Systems and the 2005 National Electrical Code: Suggested Practices, written by the author, may be downloaded from this web site: <ahref=”http: www.nmsu.edu=”” ~tdi=”” photovoltaics=”” codes-stds=”” codes-stds.html”=””>http://www.nmsu.edu/~tdi/Photovoltaics/Codes-Stds/Codes-Stds.html
Find Us on Socials