At two recent events, I was asked questions about aluminum conductors leading me to believe that an update to an article written for IAEI News a decade ago would be timely. The first was a meeting with a large corporate customer, and the second was a conference for home inspectors. I found that many of the same questions are being asked now that were being asked ten years ago. Is maintenance required? Are aluminum branch circuit conductors available? Is it safe for homes? Is it reliable for cyclical loads? What are the differences in installing aluminum and copper conductors? Let’s tackle these by answering some of the most common questions first.
How should aluminum conductors be terminated?
If you’ve been in the electrical industry awhile, you are aware that the overwhelming majority of circuit breakers and lugs in panelboards are listed for use with aluminum conductors. In fact, the most common lug found in a panelboard is made of aluminum, and is marked for termination with either copper or aluminum conductors. This has been true for decades, which means that we have decades of evidence that aluminum connections are reliable and stable. Typically, failures are seen when the connection was improperly made during installation, a fault event occurs, a system is seriously overloaded, or a well-intentioned but misinformed person attempts to “maintain” the connections by repeatedly tightening them over time.
Much of our electrical equipment is rated for use with aluminum, but there are a few exceptions. Since conductor manufacturers typically do not make 10 and 12 AWG aluminum conductors, there is no call for device manufacturers to list 15- and 20-amp receptacles or switches for use with aluminum conductors. For those items, you will find very limited selections, primarily intended for use in homes that were built more than 40 years ago. When you look at higher rated receptacles, 30 amps or more, they are typically listed to accept copper or aluminum. Aluminum conductors are frequently used in residential construction for larger electric appliances like ranges, dryers, air conditioners, etc. My home in Nevada is twenty years old and has aluminum branch circuit wiring to the wall oven and two air conditioners.
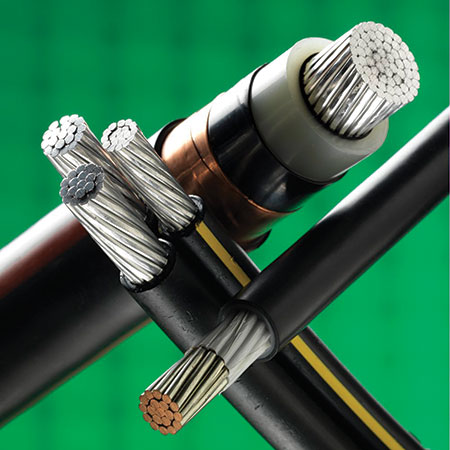
Other common uses are for feeders and service-entrance conductors. Most homes have aluminum conductors for the service entrance, either insulated conductors in a raceway or directly buried, or in a cable like Type SE. Aluminum alloy conductors have also been used in commercial and multi-family residential feeder installations for decades. One of the most visible changes in the use of aluminum conductors in the last two decades is their increasing use as feeders for high-rise buildings, hospitals, hotels, stadiums, and (more recently) data centers and manufacturing facilities. Many of these feeders are installed in circuits with high current loads, cyclical loads and continuous loads.
The key to terminating aluminum conductors is to follow the listing and labeling of the equipment, just like for every other component we install in our electrical system. Verify that the termination is listed or identified for use with aluminum conductors, and follow the connector or equipment manufacturer’s instructions. A quick review of the installation requirements will show that copper and aluminum alloy conductors are installed in the same manner: use the right connector and torque to the right value (or use the recommended crimp tool and method). Oxide inhibitor may be required for either aluminum or copper, and commonly is required for both where it is mentioned by the manufacturer.
What kind of aluminum is allowed by the NEC?
Since 1987, the National Electrical Code (NEC) has specifically required electrical grade AA-8000 series for a number of insulated conductors and cables. In the 2014 NEC, section 310.106(B) now lists the following types: RHH, RHW, XHHW, THW, THHW, THWN, THHN, service-entrance Type SE Style U and Style R. These all require flame-retardant insulation, since they are allowed to be installed in buildings. One notable omission from this list is USE (and USE-2). This type, when it is the only marking on the conductor, is prohibited from being installed in buildings, as it is not required to be flame-retardant nor to use AA-8000 series conductors. There is an insulated conductor commonly produced that has multiple type markings: USE-2/RHH/RHW-2. This type is allowed for direct burial and for installation in raceways inside buildings; it is required to have AA-8000 series aluminum alloy conductor since it bears the RHH and RHW-2 markings.
In some ways, the NEC was slow to catch up to industry practice. UL standards have required the use of electrical grade AA-8000 series conductors since the early 1970s (commonly quoted as being published in 1972). Some manufacturers began using AA-8000 series conductors even prior to that required date. Connector manufacturing standards were not far behind; most were updated in the late 1970s or early 1980s. Connector manufacturers still use the utility style aluminum (referred to as AA-1350 or EC grade) to test new connectors based on “worst-case” conditions. EC grade aluminum has lower endurance fatigue and higher creep rates, which means that the use of AA-8000 series conductors results in more reliable terminations under equal installation conditions.
What kind of maintenance do aluminum alloy conductor connections require?
Aluminum alloy connections require the exact same maintenance as copper conductors. If you are tightening your set-screw connections for either copper or aluminum on a regular basis, there is a good chance that you are damaging the conductor, the connection and/or the equipment. Many failures have been caused due to incorrect maintenance procedures and “re-torquing” conductors. Connectors manufactured in accordance with UL standards are intended to be tightened to a recommended value and then operate undisturbed for many years. Manufacturers go to great lengths to design connectors that have a long life and do not require re-tightening.
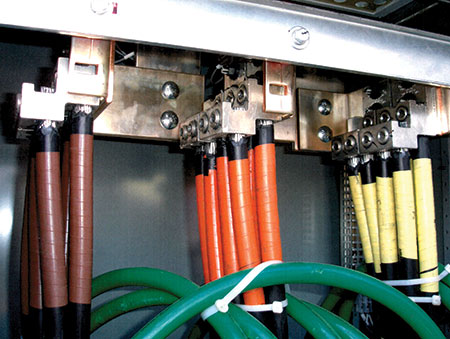
Does that mean a connection can never come loose? No, but what it does mean is that loose connections are a sign of some other condition that must be corrected. Was the connection improperly installed to begin with? Then it must be remade properly. Is one of the phases overloaded? You will need to re-distribute the load and then remake that connection. Did you experience a fault condition or ongoing vibration that is causing a mechanical failure of your connections? The root cause needs to be found and corrected before re-making that connection. Simply putting a wrench on a connection once a year doesn’t solve the problem, and it may accelerate the failure.
Since loose connections lead to excessive heat at the connection point, maintenance for connections could include visual inspection and thermal scanning. These methods can detect a problem, and investigation can help determine the root cause of the overheating. All inspections should be done in a safe manner using appropriate work practices. Adequate personal protective equipment must be worn if the inspection is performed while the equipment is energized.
Are there places I can’t use aluminum alloy conductors?
Yes. One instance is where a connection or termination is not listed for aluminum conductors. Listing for use with aluminum conductors is usually a choice made by the equipment manufacturer, and can vary from one manufacturer to another. Another is where the NEC prohibits its use. The NEC prohibits the use of bare aluminum conductors directly buried or terminated within 18 inches of bare earth when used for equipment grounding conductors or grounding electrode conductors. The oxide layer on aluminum conductors provides an excellent protection against corrosion, but it requires oxygen to repair any damage to the thin oxide layer, and it is vulnerable to the soil conditions found in many locations.
That brings us to a broader question: does aluminum corrode more easily or quickly than other metals? To answer that, I’ll draw from the work of my colleague from Canada, Alex Mak:
“Only beryllium, potassium, sodium and magnesium are more thermodynamically reactive than aluminum. However, a signature property of aluminum is its tendency to form a strongly bonded passivating oxide film on its surface. For this reason, it offers excellent resistance to corrosion and provides years of maintenance-free service in natural atmospheres. At an ambient temperature of 25 degrees C, the normal surface film formation is only about 2-50nm thick. If damaged—by a fresh abrasion for example—this corrosion-protective film re-forms immediately in most environments and ensures continued protection. As a result, aluminum and its alloys are used in a wide range of applications that include buildings, power lines, large ship superstructures, truck transports, railroad and subway cars, water pipelines, beverage containers (soft drink and beer cans), and chemical industry tanks, piping, barges, reaction vessels, and distillation columns. In applications where exposure to the elements—particularly water—is a factor, you can be sure you will find aluminum being used. For an excellent example of aluminum’s time-proven resistance to corrosion at work in the electrical industry, look no further than bare aluminum transmission conductors, which have been hard at work and resisting corrosion now for over 100 years.”
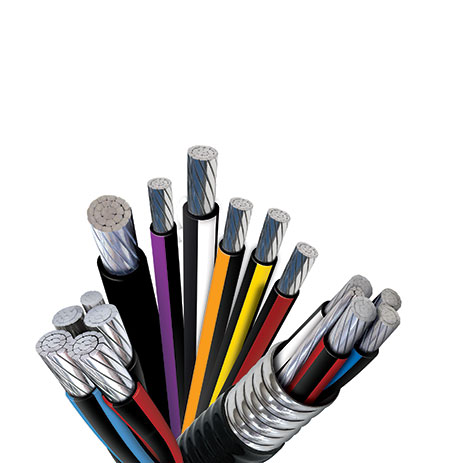
(Emphasis mine, extracted from “Corrosion of Steel, Aluminum and Copper in Electrical Applications” by Alex Mak, P. Eng., Senior Field Applications Engineer, General Cable)
The greatest corrosion risk for any metal used in the electrical industry is installation in contact with other metals, which is why we have limitations on and installation rules for installing dissimilar metals in contact with each other.
Does the oxide layer on aluminum prevent good connections?
The short answer is no. The oxide layer on aluminum is exceedingly thin, and the mechanical force of making a set-screw or compression type termination easily breaks through the brittle layer of aluminum oxide. Once the oxide layer is broken in the termination process, it does not re-form since the connector and the conductor are in intimate contact. Additionally, the voltages used in our distribution system (typically 120 volts to 480 volts) are sufficient to overcome the insulating property of naturally occurring aluminum oxide.
So why would we ever wire brush and use oxide inhibitor? While neither may be required or even necessary for many connections, you can think of it as an insurance policy for connections (both copper and aluminum). Oxide and other contaminants can affect the number of contact spots formed during the initial process of connection. The number of contact spots is the primary determinant in the contact resistance of the connection; the more contact spots, the lower the contact resistance, and the better the connection. Aluminum oxide is a very thin insulating layer, and copper oxide is a typically thin semiconducting layer. Neither is advantageous in making the best initial connection, and wire brushing can remove some of the existing oxide layer. This is particularly important for copper and aluminum conductors that have been exposed to humid or corrosive atmospheres, high temperatures, or a long service life. While both copper and aluminum oxide layers will re-form immediately after wire brushing, the thickness is limited by the short amount of exposure time before application of oxide inhibitor. The oxide inhibitor will then prevent the thickening of oxygen-dependent corrosion layers, and it will prevent any electrolyte (like humid air or salt mist) from being present in the connection area and setting up a galvanic corrosion reaction over the life of the connection.
Aren’t there studies out there showing that aluminum conductors fail even on listed connections?
Our society loves studies. I would bet that there is study published somewhere “proving” that we love a good study. And yes, there are certain studies published by special interests that seek to create doubt about the reliability of listed aluminum connections. I can only speak from my experience and conversations, and to my knowledge those studies are not considered credible by the manufacturers of listed aluminum conductors or connectors. The studies do not re-create actual installation conditions, and in fact, specifically ignore installation rules that have been known and followed for many decades. Millions of real-world connections that have operated successfully for decades are far more compelling evidence of the reliability of aluminum conductors and connectors.
Summing it all up
When making a choice between copper and aluminum conductors, reliability is not one of the deciding factors. Engineers, owners and installers are charged with making the choice based on the listing of equipment, any unusual circumstances present at the site, and the available budget. Inspectors are looking for a few key items, including: is the connection listed or identified for the conductor metal, and are there any NEC installation rules that must be taken into account? For the vast majority of locations, either copper or aluminum alloy conductors are equally acceptable, and in certain circumstances, even utility grade aluminum is acceptable per the NEC. In some corrosive locations, aluminum performs better and in others copper performs better, but you have to do the research when the question arises. The best part of this for designers, installers and owners is that there are multiple options, and the industry is not limited to a single conductor metal, insulation type or installation method.
Find Us on Socials