It has been a while since we followed Senior Electrical Inspector Kate in her daily activities of inspecting photovoltaic (PV) systems. Kate works in a county in the Southwestern United States which has been impacted by COVID-19 like all other areas of the country. And a nearby large city has been a hotspot for COVID-19 infections and hospitalizations. To further complicate her life, the local jurisdiction has funding limitations, making it difficult to hire the necessary number of qualified electrical inspectors. And, as PV system module prices decrease, larger and more complex residential PV systems are being installed, which usually require a supply-side connection. These systems require additional attention during plan review and inspection.
The Basics
Dealing with COVID 19. In the very early days of the pandemic, the County Building Official called a meeting of all of his inspectors to discuss what actions they could take to ensure the safety of not only the inspectors but also any PV system installers or owners that they might come in contact with. They developed a plan that included several early decisions, which have resulted in no positive tests for COVID-19 in their organization. Here are some of the things that were adopted.
Even before the governor issued a state-wide mandate for wearing masks when outdoors or in the presence of others, they adopted a 100% mask requirement. The Building Official obtained a continuing quantity of NIOSH 95 masks, which are about as good as it gets for commercially available products. Each inspector was given several masks, and spare masks were readily available in the office and in each of the work cars and trucks.
Hand sanitizing dispensers were installed and kept filled at the entry points to the building, at each desk in the office, and in each work vehicle. Also, sanitizing wipes were readily available in the office at each desk and kept in each work vehicle to wipe down the vehicle controls and the tools used during the inspections. The use of gloves was encouraged when making inspections, and face shields were provided but were optional for those wearing glasses. For those situations requiring manual dexterity in close quarters with equipment that may not have been disinfected, the Building Official had also provided vinyl or close-fitting nitrile gloves. Kate, who wears glasses, also opted to use a face shield when out of the vehicle performing on-site inspections.
The custodial office staff thoroughly disinfected the offices and restrooms nightly. The staff was encouraged to keep desks clear of needless clutter and disinfect computer keyboards and touch screens, cell phones, telephone handsets, keypads, and handles on frequently used file cabinets throughout the working day. Yes, file cabinets. Unfortunately, the office had not fully adopted a paperless electronic filing system, but the pandemic had them headed that way.
A contactless permitting system was adopted where all required application forms, required technical manuals and diagrams, and fees were submitted electronically.
The Continuing Funding Shortages. Although the County Commission had authorized the Building Official to have five senior electrical inspectors and an equal number of junior electrical inspectors, the two different positions’ salaries were insufficient to attract and retain qualified persons. Kate is one of only two senior electrical inspectors, and there are no junior electrical inspectors. The salaries paid by larger cities in the state and in nearby states made it extremely difficult to attract qualified electrical inspectors.
With at least five PV system installers in the county, the number of pending permit applications for PV inspections exceeded 200, and people were getting a little upset at the long delay in getting their PV systems inspected. Payments for the installed PV systems were due, but these installed systems had not been turned on due to a lack of inspections. In many cases, renewable energy credits (RECs) from the local utilities were not being accrued. The situation was becoming somewhat dire. The Building Official was receiving angry calls, and some suggested that lawsuits may be pending if the inspection backlog was not cleared.
To deal with this situation, the Building Official decided to implement a type of virtual inspection system for PV systems. This plan involved giving some very basic training on inspecting PV systems to county building inspectors and Fire Department inspectors. The author made two eight-hour presentations, one on basic electricity and PV concepts, equipment, and fundamentals and a second one on the details of the National Electrical Code (NEC) requirements for residential PV systems. A checklist was also presented and discussed. The State Electrical Inspection Bureau approved this training and the overall plan. The new PV inspectors also had to pass a state-required, abbreviated test on the various requirements for residential PV systems in the NEC in the state electrical code.
The second part of the plan was that Kate and the other senior electrical inspector would remain in the office and were supplied with large 27-inch computer monitors, a smaller monitor, and computers with full Internet access and cellular network interconnectivity (see photo 1). The dual monitor setup allowed the various codes, standards, and installer diagrams to be displayed on the smaller monitor, while the larger monitor could be used to examine the pictures being sent from the inspection site. After reviewing the PV system plans in the office and talking with the plan reviewer, the new PV inspectors went to the various sites. They walked through their checklist using smartphones to communicate with the senior electrical inspectors and transmit real-time pictures and videos of the equipment in the systems they were inspecting. Questions and answers could be posed in real-time, and decisions made on whether the observed PV system installation passed various code requirements.
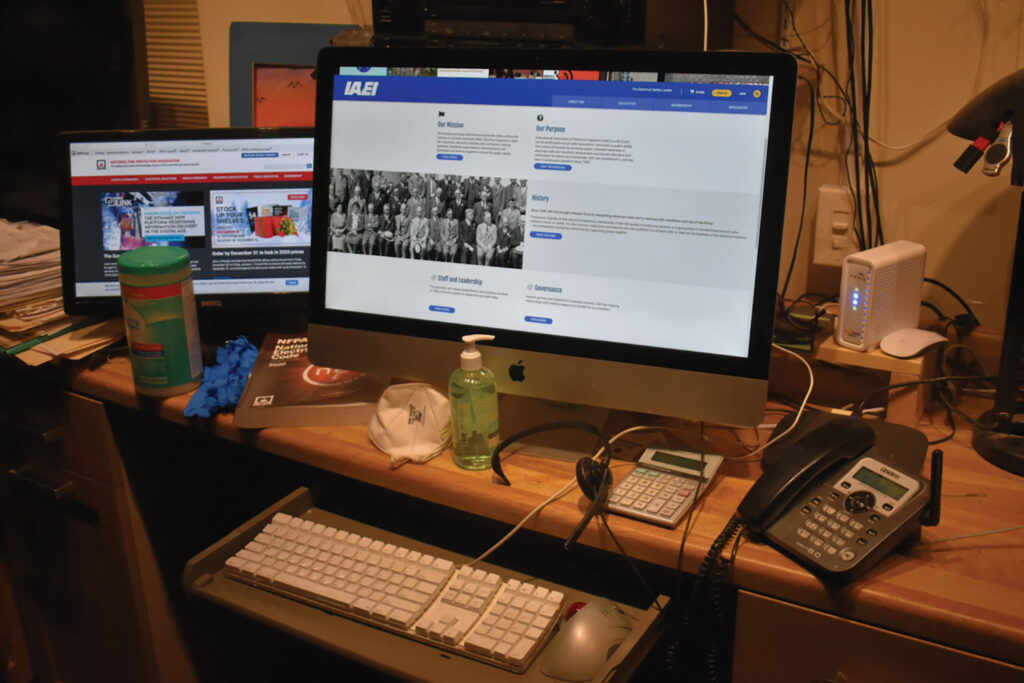
The new PV inspectors went to the sites in teams of two. Since Kate and the other senior electrical inspector did not have to travel from site to site, they could be in an almost continuous inspection mode as they switched from one new inspection team to another with no travel time. This increased the productivity of the office considerably and allowed the large number of delayed inspections to be reduced significantly.
Another activity initiated by the Building Official, with state approval and with the concurrence of his senior electrical inspectors, involved the use of a PV installer inspection system. PV installers who had been working in the county for at least five years installing PV systems of all sizes and who had a nearly perfect permitting, plan reviewing, and inspection record were allowed to participate in the virtual PV inspection activity. These installations had to pass the normal plan review, and after that, the installer used the County-supplied PV Installation Checklist to walk through the system with a smartphone. The senior electrical inspectors watching the walkthrough on their office displays, evaluated the quality of the PV system installation, asked questions, and required close-ups of certain equipment and installation techniques like PV module mounting and grounding.

In many cases, these virtual inspections allowed the senior electrical inspectors to see close-up details on the installation like module mounting and grounding that were difficult to see on an installed PV array. In all cases, the senior electrical inspectors have real-time electronic access to all of the detailed information submitted with the permit application and could compare the system as installed with the approved plans.
At the start of the virtual inspections, Kate or the other Senior electrical inspector went with the new PV inspectors on each inspection to continue their on-the-job training. This was particularly true with systems employing supply-side connections. As the new PV inspectors became more familiar with the inspection requirements, the bugs worked out of the system, and the utility technicians became familiar with the procedures being used, most of the inspections were done virtually.
Of course, new houses and commercial buildings were being constructed. These projects also required electrical inspections that Kate and the other senior electrical inspector managed to keep up with while reducing the PV inspection backlog.
Larger PV System Required Supply-Side Connections. Most of the numerous smaller one-to-five kW PV systems were being installed in the county as load-side connections (to the main service disconnect). However, the falling cost of PV modules and the reduced cost of PV system installations as new racking systems were developed were leading to the design and installation of larger systems up to about 10 kW on dwellings. To some extent, utility rate structures and available roof sizes dictated this power limit.
Obviously, these new, larger systems required more time to plan review and inspect, but in some jurisdictions, including the state where Kate worked, the supply-side connected systems required two inspections. The utilities would not make the interconnection until the system had passed the County electrical inspection for NEC compliance. However, many systems, including systems using smart inverters, required field adjustments or verification that the factory adjustments met NEC and utility requirements when the inverter was operating.
Kate’s jurisdiction had worked out an agreement with the local utility that coordinated a single visit where the following sequence of events occurred.
The County AHJ arrived and inspected the installed system for Code compliance in the non-operating state. If this inspection was passed, and this put the pressure on the PV installer to do it correctly, then the utility technician turned off the service at the nearest disconnect (usually at the power pole or transformer), allowed the PV installer to make the supply-side connection on the now de-energized service and finally reenergized the service. The County AJH then made the final inspection and observed that the system was operating properly. In most cases, at this time, the utility technician made a general inspection of the ac side of the service up to the main disconnect. If this process did not go smoothly due to noncompliance with some particular Code or utility requirement, additional fees were levied for a second inspection.
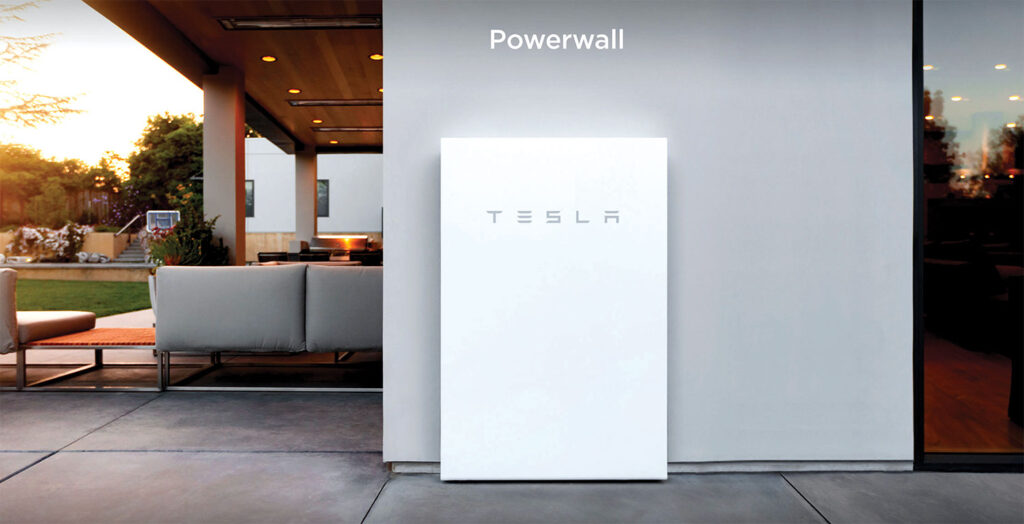
Looking Deeper
Supply-Side Connections. Due to the 20% allowance for back-fed PV currents on load-side (of the service disconnect) connections (20 A on a 100-amp service and 40 A on a 200-amp service), supply-side PV connections are becoming more common to allow installation of the larger PV systems-even on dwellings (photo 2). Section 705.11 (Supply-side Source Connections) was added to the 2020 NEC to provide additional details and clarifications on the requirements for these connections. The following is a summary of some of these requirements.
The sum of the continuous output currents from all power sources connected to a given service shall not exceed the rating of that service. Power sources connected to and controlled by a power control system (PCS) [see 705.13] shall have the controlled output included in this total [705.11 (A)].
In Section 705.11(B), the power source output circuit conductors from the service conductor point of connection to the first overcurrent protective device shall be sized in accordance with 705.28 and in no case size smaller than 6 AWG copper or 4 AWG aluminum. Section 705.28 requires that the conductors be sized based on the larger of the continuous rated output of the power source (called the maximum current) multiplied 125% without adjustments or corrections or be sized with adjustments and correction factors, but not the 125%.
If the power source conductors are connected to a feeder, the ampacity of the conductors shall be based on the overcurrent device protecting the feeder when the calculated conductor size is smaller than the feeder size. The neutral conductor shall have the same size as the ungrounded conductor as calculated above except where the neutral conductor is used only for instrumentation, voltage detection, or phase detection. In those cases, the neutral conductor may be as small as the required equipment grounding conductor. These conductors shall be installed in accordance with 230.30 or 230.43.
Generally, the power source output conductors shall be protected with an overcurrent device rated 125% of the rated current of the power source (705.30). If the power source connection to the service is outside the building, the overcurrent protection shall be located in a readily accessible area outside the building or at the first readily accessible location inside the building where the power source conductors enter the building [705.11 (C)].
Where the power source output conductors are connected to a service inside a building, the following requirements have been established: for dwellings, the OCPD must be installed within 3 m (10 ft) of conductor length, and in other than dwellings, the OCPD must be within 5 m (16.5 ft) of the connection to the service conductors [705.11(C)(1)].
In other than dwellings, cable limiters installed within 5 m (16.5 ft) of conductor length from the point of connection to the service will allow the first OCPD to be located within 20 m (71 ft) of conductor length from the point of connection to the service conductors [705.11(C)(2)].
Power source output conductor connections to the service conductors must be made with connectors or connection methods listed for the service application. Where connections are made inside utility-controlled equipment, utility equipment and procedures may be used. Connections inside listed equipment shall be made using equipment and instructions provided by the equipment manufacturer or shall have a field listing label attached [705.11(D)].
Where the service is solidly grounded wye, rated at 1000 A or more and is over 150 volts to ground, but does not exceed 1000 volts to ground, the power source output circuits shall be protected with ground-fault protection meeting the requirements of 230.95. See 705.11(E). These protection circuits should be installed on the power source output conductors near the point of connection to the service conductors to provide as much protection as possible for the entire length of the power source output conductors and connected equipment.
Battery Backup Systems. PV systems that use partial load or full house battery backup are generally more complex than most other PV systems because they contain power control systems (PCS) and are actually microgrids that have in one form or another microgrid controllers (see photo 3). The installation requirements for these systems are established not only by the Code but by the manufacturer’s detailed installation instructions and diagrams. Kate and the other senior electrical inspector are just getting familiar with these systems themselves, and they have not yet been inspected using the virtual inspection system.
For these systems, one of the senior electrical inspectors accompanies the new PV inspectors for further on-the-job training. Plan review is an increasingly important part of this process where the provided system diagrams are carefully compared to the manufacturer’s required installation diagrams. Due to their complexity, these systems have the potential for many small or large deviations from NEC requirements. While the systems will be covered in some detail in a subsequent article in this series, one area that requires constant attention is that while the requirements of 705.11 apply to the supply-side connection, after the circuits have passed through the first PV system disconnect after the service connection, all downstream circuits from that point to the actual power source, come under 705.12 (load-side connections). In this case, that PV ac disconnect becomes a second main service disconnect.
Summary
In the current pandemic and limited funding environment, Kate and her Building Official have worked together with others in the office to successfully keep the entire office staff healthy while using unique inspection methods to reduce the backlog of permitted and installed, but not yet inspected PV systems. Supply-side connected PV systems require renewed attention due to the more detailed requirements added to the 2020 NEC. The newer and increasingly common battery-backed systems require high levels of attention to the manufacturer’s installation instructions. As Kate always says: “Stay safe and healthy and read those manuals.”
Upcoming Webinar
John Wiles will be making one of his eight-hour presentations on “PV Systems and the NEC” sponsored by the American Solar Energy Society (ASES) in two, four-hour segments on 14 and 15 April 2021.
Log on to the ASES web site at www.ASES.org and then sign up for the Mailing List at the top of the page for further details.
Find Us on Socials