I. INTRODUCTION
In general, power quality is a critical factor in the performance, efficiency, and safety of electrical systems. Therefore, conducting power quality (PQ) studies is vital to ensure optimal operation and prevent potential issues. While many papers focus on specific power quality problems such as voltage sags/dips, swells, harmonics, transients, and unbalance, this paper aims to provide a comprehensive understanding of power quality studies, specifically in the context of commercial buildings. Its goal is to assist decision-makers in identifying potential power quality issues and implementing effective solutions. Emphasis is placed on understanding the client’s requirements, site conditions, testing plans, and adherence to industry standards to achieve reliable and accurate results.
Although there are no international standards mandating power quality studies for building electrical systems, several organizations have published guidelines and standards related to power quality, including the IEEE [1-5][33], IEC [6-10], ANSI [11-13], and NEMA [14-15]. Adhering to these guidelines and standards helps ensure that the electrical system meets accepted power quality and reliability levels. Additionally, certain industries or applications may have specific regulatory requirements for power quality studies due to the potentially serious damage caused by power problems.
Numerous incidents resulting from inadequate maintenance and improper power quality studies have been documented over the years. Examples include the Bellagio Hotel fire in Las Vegas in 2019 [16], the Trump Tower fire in New York City in 2018 [17], the office tower fire in Calgary in 2017 [18], the MGM Grand fire in Las Vegas in 1980 [19], and the One Meridian Plaza fire in Philadelphia in 1991 [20], and the list goes on.
Overall, this article highlights the importance of PQ studies with a focus on commercial buildings, provides guidance on how to prepare properly, and emphasizes the significant impact that power problems can have on safety and infrastructure. Several convincing arguments to persuade conducting a PQ study on-site, including cost savings (See Figure 1), enhance equipment reliability, code compliance, ensuring safety, maintaining reputation, future-proofing (Predictive maintenance umbrella), environmental sustainability, and operational efficiency. For instance, a study can uncover issues such as poor power factors leading to higher energy bills, frequent equipment failures due to voltage sags and surges, or ground faults posing safety hazards to building occupants and maintenance personnel.
![Figure 1. Cost of having PQ issues for different industrial sectors [32]](https://iaeimagazine.org/wp-content/uploads/2023/09/2023-04-abdera-fig1.jpg)
As an example of how PQ studies can save costs; the study can easily evaluate the power factor (PF) of a building (efficiency of electrical power usage). Mathematically PF can be given as:
PF = Real power (kW) / Apparent power (kVA)(1)
Suppose a commercial building has a total connected load of 500 kW and a power factor of 0.8. Add-ing that fact that the utility usually charges for both real power (kW) and apparent power (kVA). Now, for simplicity, let us assume the cost is $0.12 per kWh for real power and $0.08 per kVA for apparent power.
To calculate the actual power consumption, we can use Equation 1 above and use the given power factor of 0.8, to calculate the apparent power as follows:
500 kW / 0.8 = 625 kVA.
Now, let us determine the energy consumption and cost for both real power and apparent power:
– Energy consumption and cost for real power (kW):
Energy (kWh) = Real Power (kW) × Time (hrs)
Energy (kWh) = 500 kW × 1,000 hrs (for example)
Energy (kWh) = 500,000 kWh
Cost for real power = Energy (kWh) × Cost per kWh = 500,000 kWh × $0.12/kWh = 60 k$
– Energy consumption and cost for apparent power (kVA):
Energy (kVAh) = Apparent Power (kVA) × Time (hrs)
Energy (kVAh) = 625 kVA × 1,000 hrs (for example)
Energy (kVAh) = 625,000 kVAh
Cost for apparent power = Energy (kVAh) × Cost per kVAh = 625,000 kVAh × $0.08/kVAh = 50 k$
In this example, due to the lower power factor of 0.8, the energy billing based on apparent power results in a higher cost of 50 k$ compared to the billing based on real power, which costs 60 k$.
By conducting a power quality study, experts can identify a low power factor and recommend solutions such as power factor correction capacitors to improve the power factor. Improving the power factor to a desired value, typically close to unity “1.0”, can reduce the apparent power and lower energy bills.
Figure 2 illustrates other common scenarios in which power quality (PQ) studies should be considered represented as a percentage of likelihood to happen. These scenarios range from frequent electrical disturbances or power outages that disrupt critical equipment and processes to the use of sensitive electronic devices such as medical or manufacturing equipment that require a reliable and consistent power supply. Other situations that necessitate PQ studies include being connected to an electrical grid with a history of poor PQ, which may involve voltage sags, swells, transients, or harmonics. PQ studies may also be required after a significant renovation or expansion that alters the electrical load profile, ensuring that the existing electrical infrastructure can support the new load. Lastly, being in an area susceptible to PQ problems, such as experiencing high levels of electromagnetic interference (EMI) from neighboring industrial facilities or being prone to lightning strikes, may also warrant PQ studies.
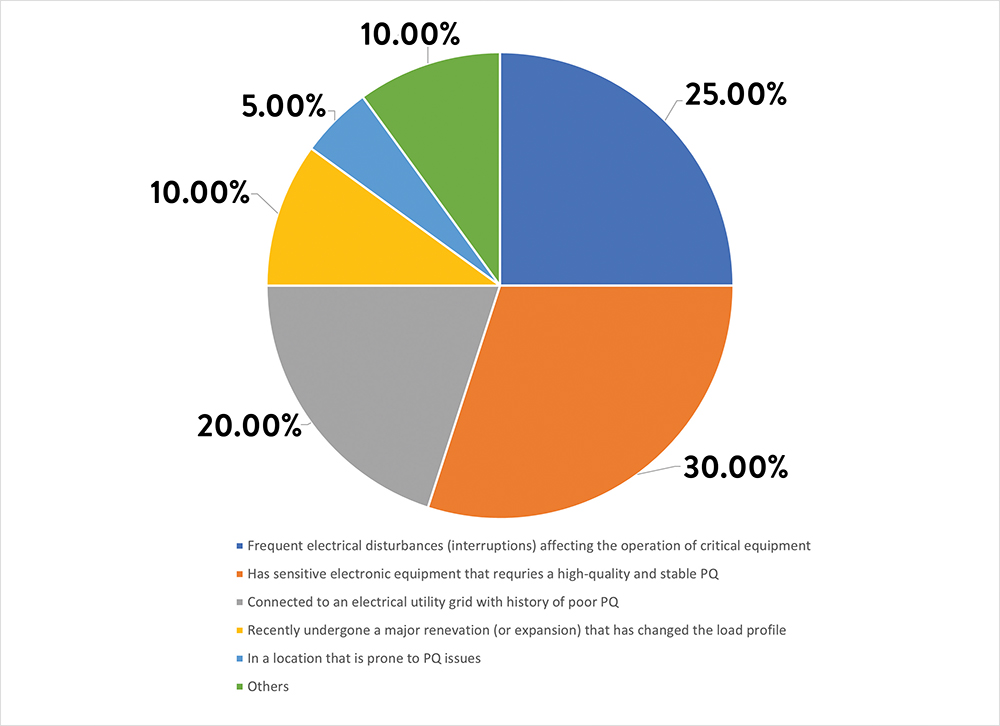
Considering the factors that cause power interruptions or disturbances in an electrical system is crucial to prevent future occurrences and ensure the reliability and safety of the electrical system. Weather events, equipment failures, overloading, power grid issues, human error, animals, and malicious acts are some of the issues that can affect any building that relies on a stable and reliable electrical supply, including hospitals, data centers, manufacturing facilities, office buildings, and residential buildings.
Power quality studies involve measuring and analyzing various electrical parameters, such as voltage, current, power factor, harmonics, and transients, to identify potential issues and recommend solutions to improve the quality of the power supply. Identifying the cause of power interruptions or disturbances is important to ensure the reliability and safety of the electrical system, and PQ studies provide valuable insights to decision-makers in identifying potential power quality issues and implementing effective solutions.
Figure 3 below shows a case of damage that could have been prevented if a proper PQ study had been conducted. In addition, Figure 4 displays samples of damages happening to capacitors sampled from different industrial sites. Note that, capacitors can become damaged due to harmonic resonance when the harmonic frequency coincides with the natural frequency of the capacitor and the power system (resonant overvoltage), where the voltage across the capacitor becomes significantly higher than expected, leading to excessive current flow through the capacitor. This can cause the capacitor to overheat and fail, resulting in power quality problems such as voltage distortion, flicker, and reduced power factor. In severe cases, overcurrent can also cause damage to other equipment connected to the same electrical system. Harmonic resonance is more likely to occur in systems with high levels of harmonic distortion and in cases when capacitors are used for power factor correction or voltage regulation.
![Figure 3. Likelihood of PQ Consequences [21]](https://iaeimagazine.org/wp-content/uploads/2023/09/2023-04-abdera-fig3.jpg)
Another good point to mention here is that conducting a power quality study not only helps identify existing problems but also plays a crucial role in enabling predictive maintenance practices. By analyzing the power quality data and recommendations provided by the study, building managers can proactively address potential issues and implement measures that enhance the reliability and safety of the electrical system. Through the adoption of predictive maintenance strategies, such as installing capacitors, voltage regulators, or surge protectors as suggested by the study, a building can significantly improve equipment reliability, reduce maintenance costs, prevent potential penalties or fines, enhance its reputation, prepare for future growth or changes, minimize its environmental impact, and optimize operational efficiency. Therefore, conducting a power quality study becomes an essential step in identifying potential issues and leveraging predictive maintenance to prevent significant damage to the electrical system, ensuring its long-term health and performance, as will be discussed in the next few sections.
![Figure 4. Capacitor Damage Due to Harmonics Resonance [22][34]](https://iaeimagazine.org/wp-content/uploads/2023/09/2023-04-abdera-fig4.jpg)
III. PQ AND SITE READINESS
As has been discussed, PQ studies can provide extended benefits for preventive maintenance, optimization, compliance, insurance, and future planning. However, before scheduling a study, certain steps should be followed to ensure both accurate and effective results. (Gantt chart in Figure 5)
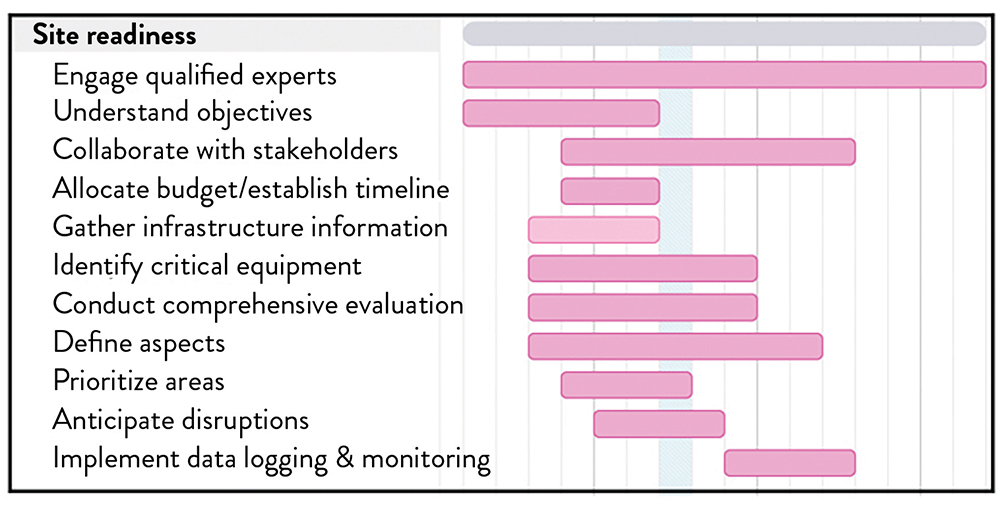
The first step is to clearly understand the objectives of the study and define specific aspects of power quality to be assessed, such as voltage fluctuations, harmonics, flicker, or interruptions. Furthermore, it is important to identify critical equipment and systems within the building that are sensitive to power quality issues. This step could be very sensitive in some facilities such as data centers, medical equipment, and manufacturing machinery. By prioritizing some of the areas on-site, building managers can focus their efforts on ensuring the reliability and performance of crucial systems.
Following that, building managers should have access to relevant and updated power infrastructure information. This includes electrical drawings, single-line diagrams, and equipment specifications, which aid in understanding the electrical distribution system and identifying potential areas of concern. Collaboration with key stakeholders is essential, involving maintenance personnel, electrical engineers, and relevant staff members. Their insights and expertise contribute to a comprehensive understanding of the building’s electrical system and help identify specific areas that require closer examination.
In some cases, implementing a data logging and monitoring system is crucial for collecting real-time power quality data. This involves installing power quality meters at strategic locations within the building to capture relevant parameters. Building managers should also anticipate potential interruptions or disruptions to normal building operations during the study. Note that proper coordination with occupants and careful planning minimize any inconvenience or impact on critical activities.
In addition, engaging qualified experts, such as professional licensed consultants (Ex: Professional engineers), is highly recommended. These professionals bring their experience and specialized equipment to conduct a thorough assessment, ensuring accurate measurements and detailed analysis. Adequate budget allocation and establishing a realistic timeline are important aspects of the preparation process. Sufficient resources and time should be dedicated to conducting a comprehensive study, allowing for in-depth evaluation and effective implementation of solutions.
By addressing these major points, building managers can ensure their building is well-prepared for a power quality study. This enables a thorough assessment of power quality issues and empowers them to implement appropriate measures to improve power reliability and system performance.
It is also important to mention that while gathering site information, the scope here should investigate site maintenance, electric code violations, and equipment status. Different factors such as dirty electrical connections, loose or corroded wires, malfunctioning equipment, or inadequate grounding can significantly contribute to power quality issues. For instance, a loose or corroded wire can lead to an increase in electrical resistance, resulting in voltage drops and sag that have the potential to cause equipment malfunction or failure. Similarly, the presence of dirty electrical connections can introduce increased resistance, leading to voltage fluctuations and power quality concerns like flicker. Therefore, regular maintenance practices such as cleaning, tightening, and inspecting electrical equipment play a crucial role in preventing these types of issues and ensuring the safe and efficient operation of electrical systems. See Figure 6.
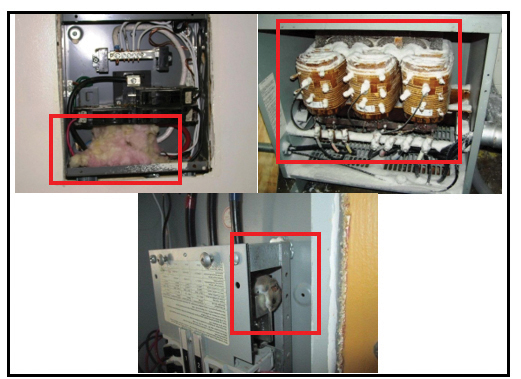
In addition, incorporating data analysis and predictive maintenance techniques within the scope of the study enhances the effectiveness of maintenance practices. By collecting and analyzing relevant data on power quality parameters like voltage variations and harmonics, commercial buildings can gain valuable insights into their electrical systems. This enables early detection of faults and facilitates prioritized maintenance based on equipment condition and criticality, thereby minimizing down-time and extending the lifespan of equipment. As a rule of thumb, it is always recommended to conduct periodic power quality studies to have enough data history to identify any future power quality issues and ensure the reliability and safety of the electrical system, with the frequency varying depending on the building’s specific needs and requirements.
Moreover, analyzing energy usage patterns and power quality data offers opportunities for energy efficiency improvements and enables power factor correction. The integration of real-time monitoring and remote diagnostics into building management systems empowers facility managers to remotely identify power quality issues, prioritize responses, and conduct troubleshooting, ensuring uninterrupted performance and enhancing operational efficiency. Therefore, by combining comprehensive maintenance practices with data analysis and predictive maintenance techniques, commercial buildings can effectively manage power quality, mitigate potential issues, and promote system reliability while reducing the risk of equipment failure, downtime, and costly repairs.
Furthermore, a measurement plan should be developed at an early stage, which involves identifying the measurement locations, determining the type and duration of measurements required, selecting appropriate equipment, and developing a measurement schedule. In addition, this step includes installing measurement equipment and configuring them correctly.
III. PERFORMING THE STUDY
When conducting a power quality study, different meters should be placed at specific locations to provide a comprehensive assessment of the quality of the power being delivered throughout the building or facility (Figure 7). Note that these locations have a direct effect on the accuracy of the study. As a rule of thumb, the meter should be placed as close to the source of the power quality issues as possible, typically near the main switchboard or distribution panel. This is because power quality issues can be caused by various factors, such as the incoming power supply, equipment connected to the electrical system, or the electrical wiring itself. Placing the meter close to the source of the issue helps save enormous time and money when identifying the cause of the issue and taking appropriate corrective actions. Another important note: Meters should be placed in locations that are considered easily accessible (time and space) and safe for the technician to install and operate. Other possible locations may include the main incoming power, load-side distribution panels, sensitive equipment, grounding systems, and harmonic filters.
![Figure 7. Placing meters on specific locations enhance PQ accuracy [23]](https://iaeimagazine.org/wp-content/uploads/2023/09/2023-04-abdera-fig7.jpg)
Note that for some buildings, these measurement points (locations and the number of points) will be more specific. As an example, in a hospital setting, meters should be placed at the main incoming power, emergency power supply system, patient care areas, imaging equipment, and grounding system.
An important point here is that several common misjudged points can occur when conducting PQ studies on commercial buildings, including:
- Inadequate scope: Failing to properly define the scope of the study, which can result in missing critical electrical systems or equipment that may be contributing to power quality issues or focusing on some equipment without a proper site scan: such as focusing only on transformers. Transformers are an important piece of equipment to consider when conducting a power quality study, as they can be a significant source of voltage distortion and other power quality issues, such as being sensitive to voltage sags/swells, and can be negatively affected by excessive harmonic distortion. However, transformers are not necessarily the only or most important piece of equipment to monitor when conducting a power quality study. Other key pieces of equipment to monitor will depend on the specific application and the potential sources of power quality issues. The chart in Figure 8 shows other equipment onsite that can cause PQ issues. For example, in hospitals and medical centers, any critical medical equipment such as CT scanners, MRI machines, and life support systems should be a higher priority than monitoring transformers, as these pieces of equipment are essential to patient care and can be particularly sensitive to power quality problems. Therefore, when determining which pieces of equipment to monitor during a power quality study, it is important to consider the specific application and the potential impact of power quality issues on critical equipment and systems.
- Insufficient data collection: Collecting inadequate or incomplete data, such as failing to capture all necessary electrical parameters, not recording data for a long enough period, or using inappropriate measuring devices. Note that the duration of a power quality study should be long enough to capture a representative sample of the electrical system performance, with a duration of 24 hrs being sufficient for a basic power quality assessment of a small building or facility. The recording period may need to be longer for equipment that operates intermittently or with variable loads. It is important to carefully plan the measurement strategy and ensure that data is collected consistently over time.
- Improper data analysis: Misinterpreting or misanalyzing the collected data, which can lead to incorrect identification of power quality issues or improper recommendations for solutions.
- Overlooking root causes: Focusing on treating symptoms rather than addressing the underlying root causes of power quality issues, such as not considering upstream sources of disturbances or failing to investigate equipment failures.
- Inadequate communication: Failing to communicate the findings and recommendations of the power quality study effectively to building owners or facility managers, which can lead to misunderstandings, delayed action, or ineffective solutions.
- Poor implementation: Implementing solutions improperly or inadequately, such as not verifying that proposed solutions have been effectively implemented, or not conducting regular maintenance and monitoring of the electrical system to ensure continued power quality and reliability.
As a general rule, the equipment types to be monitored in a power quality (PQ) study will depend on the application and potential sources of power quality issues. Typically, critical equipment, sensitive equipment, power distribution equipment, motor-driven equipment, and lighting and HVAC equipment are commonly monitored, listed in order of importance. However, the specific equipment types to be monitored will vary based on the unique characteristics of each facility.
Similarly, the prioritization of power distribution equipment during a power quality study will depend on the specific characteristics of the facility and potential sources of power quality issues.
It is worth mentioning that there may be differing opinions in certain industries regarding PQ metering on three-phase and single-phase equipment. The importance of both types depends mainly on the specific application and could extend to the type of disturbances being studied. Three-phase equipment is more commonly used in industrial and commercial settings, while single-phase equipment is prevalent in residential settings. For example, in an industrial setting more three-phase equipment will be presented than in a residential setting.
VI. AFTER THE STUDY
After conducting a PQ study, it is crucial to carefully review the results and list of recommendations. If any issues were identified, appropriate steps should be taken to address them. Recommendations may include adding specific equipment or parts to the main electrical system to improve the performance for example (such as PF correction equipment, surge protectors, or voltage regulators); implementing a monitoring program using permanent or portable power quality monitoring equipment; and/ or scheduling periodic re-evaluations of the building’s power quality.
Furthermore, integrating power quality considerations into the building’s overall maintenance and energy management plans is also important. This involves conducting regular inspections and maintenance of electrical equipment, implementing energy efficiency measures to reduce the load on electrical systems, and continuously monitoring power quality to optimize efficiency and reliability.
PQ studies can provide valuable insights into equipment health by measuring electrical parameters and comparing them to the manufacturer’s specifications or industry standards. In addition to physical measurements like temperature and vibration, power quality studies provide information on parameters such as voltage and current levels, harmonic distortion, and power factor (PF), which can impact equipment health. Identifying any issues through the power quality study allows for the prioritization of maintenance and repair activities, ensuring optimal performance and reliability of electrical equipment.
Note that, during a power quality study, there are no universally fixed optimum values for all parameters. The relevant values will depend on the type of equipment being monitored, operating conditions, and applicable industry standards or regulations. Key electrical parameters typically measured in power quality studies include voltage levels and stability, harmonic distortion, power factor, temperature, and current levels. The specific optimum values for these parameters will vary based on the equipment being monitored and the applicable industry standards or regulations.
Finally, at the end of the study, a detailed report with a list of recommendations derived from the analysis is presented. After reviewing and accepting the recommendations, the suggested solutions are implemented and verified. By following this systematic approach, power quality studies provide essential insights and actionable recommendations to enhance power quality, mitigate issues, and maintain reliable electrical systems in buildings and facilities.
V. IMPROVING PQ RESULTS
The focus so far has been on site preparation and budgeting for a PQ study. In this section, let’s explore some of the methods to improve study results and enhance electrical system reliability using predictive maintenance principles and theory. Here are some suggestions:
- Conduct a power quality assessment following relevant standards such as IEEE 1159 [1] and IEC 61000-4-30 [24], which may involve measuring voltage, current, power, and power factor using instruments such as power analyzers (meters) and oscilloscopes.
- Before conducting a study, electrical equipment in the building may need to be prepared to ensure that it is in good working condition. This could involve multiple Preventative/Preventive maintenance tasks, such as equipment cleaning, calibration, tightening connections, replacing worn-out parts, and equipment testing.
- Enhance the building’s electrical system (if needed): Assess the capacity of the electrical system and consider upgrading it with additional transformers, switchgear, and relevant equipment. This may entail conducting load flow and short circuit analyses using software like SKM PowerTools, EasyPower, and others [25-27].
- Evaluate the impact of the new loads on the power factor (PF) and take steps to improve it, if necessary, which involves calculating the power factor using the formula. [2] [28].
- Mitigate the effects of harmonics on the electrical system by installing harmonic filters and other equipment if needed. This step can involve calculating the total harmonic distortion (THD). [2][8].
- Perform arc flash analysis before the PQ study: Arc flash analysis helps to determine the level of personal protective equipment (PPE) required for workers and it helps point out some of the unpredictable problems that the system might have. [27][29-31]
VI. BAD PRACTICES TO AVOID
In this section, the discussion aims to shed some light on examples of bad practices that should be avoided when conducting PQ studies or any power study. For simplicity, these examples are divided into three main categories:
a. Mistakes when Pricing PQ studies:
When pricing a power quality study, some practices can lead to underestimating the costs and time needed for project completion. One mistake is disregarding the complexity of the study, as not all power quality studies are equal in complexity. Some may be more intricate than others. Additionally, overlooking the study’s scope can result in unexpected additional work, leading to higher costs. It is crucial to include all necessary equipment and resources, such as power quality analyzers and expert personnel, for analyzing and interpreting the results. Failure to do so can result in incomplete or inaccurate findings, which can be costly to rectify. Lastly, neglecting to consider the location and accessibility of the site can impact the study’s cost, as it may require travel expenses or specialized equipment for site access.
b. Mistakes when planning PQ studies:
Planning a power quality study requires careful consideration of various factors, including a clear understanding of the client’s needs and expectations. Moreover, insufficient knowledge of the electrical system and specific power quality issues, lack of well-defined objectives and criteria, omission of relevant equipment and loads, and inadequate consideration of safety and access requirements for in-stalling meters and other equipment can impede the study. Furthermore, relying on an outdated Single Line Diagram (SLD) may result in incomplete or inaccurate results. It is crucial to utilize reliable and up-to-date equipment during the study to ensure precise outcomes. Lastly, having a comprehensive testing plan is essential to gather all necessary data for accurately analyzing the power quality of the electrical system. Failing to establish a testing plan can lead to incomplete or inaccurate results.
c. Mistakes when conducting PQ studies:
Not following industry standards, such as the IEEE and IEC standards mentioned earlier, can result in inaccurate or incomplete results. Proper data analysis is vital to ensure accurate outcomes, and failure to do so can lead to incorrect conclusions and recommendations. It is also essential to consider all potential sources of power quality issues, including external factors like lightning strikes. Neglecting to consider all possible sources may lead to incomplete or inaccurate results. Additionally, effectively communicating the power quality study findings and recommendations to the client is crucial to ensure their understanding. Failure to do so can result in misunderstandings and incorrect actions taken by the client. It is important to note that power quality studies are complex and require careful consideration and planning for success.
Furthermore, there are other examples of bad practices to avoid. These include improper placement of equipment and meters, such as choosing locations that do not represent the overall system or fail to capture critical loads or circuits. Placing meters in areas susceptible to electromagnetic interference, using inadequate or poorly calibrated equipment, and improper grounding of equipment and meters are also bad practices. Inaccurate data collection can result from failure to capture data over a sufficient period, inadequate documentation, neglecting issues requiring specialized measurement techniques, and insufficient attention to data quality control.
In sizing channels, CTs (Current Transformers), and other equipment used for measuring power quality parameters, it is crucial to avoid using incorrectly sized CTs for the load they monitor (Selecting the correct CT size based on the actual load and cable being monitored, rather than compensating for smaller cables with oversized CTs), failing to account for potential overloads or transient conditions, installing CTs in locations prone to electrical noise interference, using measurement equipment not rated for expected operating conditions, improper calibration and testing of equipment, using equipment with insufficient resolution or bandwidth, and inadequate documentation of equipment and settings.
![Figure 8. Equipment that should be tested while performing a PQ study [21]](https://iaeimagazine.org/wp-content/uploads/2023/09/2023-04-abdera-fig8.jpg)
VII. CASE STUDY
Consider a hypothetical scenario where a building manager intends to conduct a PQ study for a commercial facility with a moderate number of electrical equipment on-site (2000 buses). The purpose of the study is to implement a proactive and predictive maintenance approach. In this example, it is assumed that no visible problems are observed on-site. The objective is to determine the potential impact of the factors discussed earlier on the total cost of the study. Table 1 below illustrates these parameters:
In addition to these parameters, in some cases, adding appropriate maintenance into the pricing equation for a power quality study can be challenging, as it depends on the specific maintenance requirements of the building’s electrical equipment. However, in general, the following are the main maintenance categories that apply to the majority of PQ study budgets:
- Equipment preparation
- Preventative maintenance
- Post-study maintenance
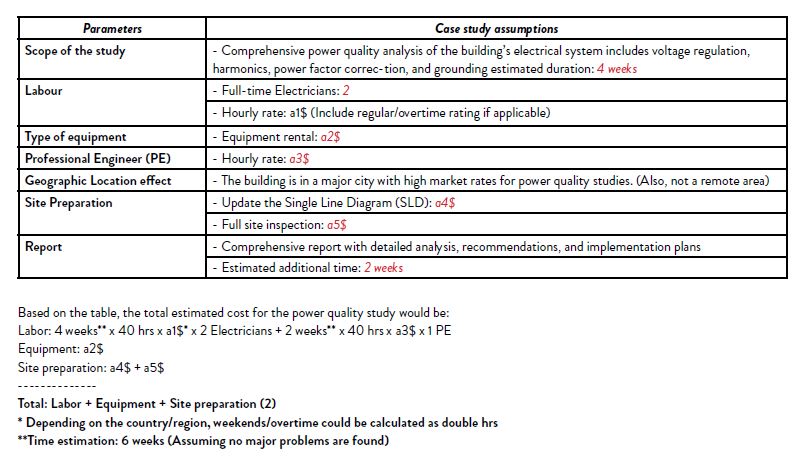
VII. CONCLUSIONS
The previous sections have highlighted the crucial role of power quality (PQ) studies in ensuring the safe and efficient operation of electrical systems. Proper planning and preparation are vital to fully leverage the benefits of these studies, including identifying potential risks and challenges, and developing effective mitigation strategies. It is evident from the discussion how PQ studies offer valuable insights for equipment selection, maintenance, and system upgrades, thereby minimizing the risk of power outages and equipment damage (under the umbrella of predictive maintenance). On the other hand, neglecting a thorough assessment can result in unnoticed problems, equipment failures, safety hazards, and costly repairs. Furthermore, prioritizing planning and adhering to international standards are key factors in the success of power quality studies. They provide a roadmap for maintaining on-site electrical systems that are safe, efficient, and reliable.
REFERENCES
[1]. IEEE 1159, “Recommended Practice for Monitoring Electric Power Quality”, 2019.
[2]. IEEE 519, “Recommended Practice and Requirements for Harmonic Control in Electrical Power Systems”, 2014.
[3]. IEEE 1453, “Guide for Application of Power Electronics for Power Quality Improvement on Distribution Systems Rated 1 kV to 38 kV”, 2022.
[4]. IEEE 242, “IEEE Recommended Practice for Protection and Coordination of Industrial and Commercial Power Systems”, 2001.
[5]. IEEE 50160, “Revision of European Standard EN 50160 on power quality: Reasons and solutions”, 2010.
[6]. IEC61000-2-2, “Electromagnetic Compatibility (EMC) – Part 2-2: Environment – Compatibility Levels for Low-Frequency Conducted Disturbances and Signaling in Public Power Supply Systems”, 2002.
[7]. IEC61000-2-4, “Electromagnetic Compatibility (EMC) – Part 2-4: Environment – Compatibility Levels in Industrial Plants for Low-Frequency Conducted Disturbances”, 2002.
[8]. IEC61000-3-2, “Electromagnetic Compatibility (EMC) – Part 3-2: Limits – Limits for Harmonic Current Emissions (Equipment Input Current ≤ 16 A per Phase)”, 2002.
[9]. IEC61000-4-11, “Electromagnetic Compatibility (EMC) – Part 4-11: Testing and Measurement Techniques – Voltage Dips, Short Interruptions, and Voltage Variations Immunity Tests”, 2002.
[10]. IEC61000-4-13, “Electromagnetic Compatibility (EMC) – Part 4-13: Testing and Measurement Techniques – Harmonics and interharmonics Including Mains Signaling at a.c. Power Port, Low-Frequency Immunity Test”, 2002.
[11]. ANSI C84.1, “Electric Power Systems and Equipment – Voltage Ratings (60 Hz)”, 2020.
[12]. ANSI C84.2, “Electrical Power Systems and Equipment – American National Standard for Electric Power Systems and Equipment – Voltage Ratings (60 Hz) – Safety Standard for Portable General-Purpose Transformers”, 2020.
[13]. ANSI C84.7, “American National Standard for Electric Power Systems and Equipment – Voltage Ratings (60 Hz) – Preferred Ratings, Related Voltage Ratings, and Electrical Characteristics for Three-Phase Electric Power Systems”, 2020.
[14]. NEMA MG 1, “Motors and Generators”, 2022.
[15]. NEMA AB 1, “Molded-Case Circuit Breakers, Molded Case Switches, and Circuit-Breaker Enclosures”, 2002.
[16]. https://www.dailymail.co.uk/news/article-8395563/Blaze-breaks-near-Bellagio-Hotel-Las-Vegas-just-two-days-casinos-reopened.html (accessed: May, 18, 2023).
[17]. https://www.cnn.com/2018/04/07/us/trump-tower-fire/index.html(accessed: May,18, 2023).
[18]. https://calgary.ctvnews.ca/three-alarm-fire-leads-to-evacuation-of-northeast-calgary-building-1.3697666 (accessed May. 18, 2023).
[19]. https://en.wikipedia.org/wiki/MGM_Grand_fire (accessed May. 18, 2023).
[20]. https://www.firerescue1.com/firefighting-history/articles/one-meridian-plaza-3-firefighters-killed-during-unimaginable-blaze-vOsQ4mBwJMLDxiH4/ (accessed May. 18, 2023).
[21]. S. Bhattacharyya, J. M. A., Myrzik, & W. L. Kling, “Consequences of poor power quality-an overview”, IEEE: 42nd International Universities Power Engineering Conference, pp. 651-656, 2007.
[22]. https://voltage-disturbance.com/power-quality/harmonic-resonance-in-power-systems/ (accessed Jan. 23, 2023)
[23]. https://www.fluke.com/en-us/learn/blog/power-quality/a-fresh-look-at-power-quality-basics (accessed Jan. 23, 2023)
[24]. IEC 61000-4-30, “Class A—Power quality monitor: Development and performance analysis”, 2015.
[25]. IEC 60364, “Low-voltage electrical installations”, 2005.
[26]. IEEE 1547, “IEEE Standard for Interconnection and Interoperability of Distributed Energy Resources with Associated Electric Power Systems Interfaces”, 2018.
[27]. NFPA 70, “National Electrical Code (NEC)”, 2023.
[28]. IEC 61000-3-6, “Electromagnetic compatibility (EMC). Limits. Assessment of emission limits for the connection of distorting installations to MV, HV, and EHV power systems”, 2008.
[29]. IEEE 1584, “IEEE Guide for Performing Arc-Flash Hazard Calculations”, 2018.
[30]. IEC 60909, “Short-circuit currents in three-phase a.c. systems – Part 0: Calculation of currents”, 2016.
[31]. CSA Z462, “Workplace electrical safety”, 2021.
[32]. A. Sharma, B. S. Rajpurohit, and S. N. Singh, “A review on the economics of power quality: Impact, assessment and mitigation”, Renewable and Sustainable Energy Reviews vol.88, pp.363-372, 2018.
[33]. IEEE 141, “Recommended Practice for Electric Power Distribution for Industrial Plants”, 1993.
[34]. Park, et al. “A fault analysis of DC electric arc furnaces with SVC harmonic filters in a mini-mill plant” Electric power systems research, pp.807-814, 2010.
Find Us on Socials