Those installing and inspecting electrical installations according to the provisions of the National Electrical Code might wonder from time to time how important are these rules? When discussions turn to, “You are overreacting to these small discrepancies!” or “What are the fire or shock hazards associated with this violation?” it is sometimes difficult to know what effect the violation might have on the overall safety of the facility. If installations comply, there are no shock and fire war stories and it might be easy to become complacent. Another reality is that NEC requirements not only minimize immediate shock and fire hazards associated with a new electrical installation but also provide safe failure of a system after installation. If properly installed, some protective device should turn power off before the installation becomes a shock or fire hazard.
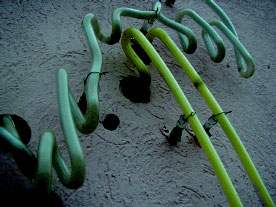
Photo 2. Shows what could be seen from the outside of the shopping center facade
This article will look at an installation that was installed in the mid-1990s without a permit, without an inspection, and without any consideration of the NEC requirements in place at that time. For the local fire department, the installation became a real war story on November 12, 2000, at 9:50 p.m. Fortunately, customers in other tenant spaces at the shopping center saw the smoke, called 911, and the fire station was only 1/2 mile from the scene. The fire was contained to a small area and there were no injuries. An inspection of the installation site and damage to the structure revealed some interesting possibilities and opportunities for problems with the installation. Information provided to the media indicated a ground fault in the store’s sign was the cause.
As can be seen in photo 1, electrical systems installed improperly are fire hazards. Not visible in the picture are the remains of a metal enclosed electrode receptacle. Considering the installation, the cause of the fire appears to be a ground fault that originated in the receptacle. The remaining field-installed skeleton tubing also revealed obvious problems. Photo 2 shows what could be seen from the outside of the shopping center facade.
Photo 3. Flexible metal conduit that was found near the burned area in the attic
The NEC and UL 48 Standard for Electric Signs both require the electrode receptacle to be closed by a cap or during the 1996 NEC code cycle sealed with silicon or a cap. This requirement minimizes the entrance of water, bugs, dirt, or other debris that contaminates the receptacle and leads to tracking and eventual short circuiting. At the same time, the mounting of the receptacles would not allow water that entered to run back out. Although no conclusive fire investigation determined that this condition affected the insulation of the sign conductors and caused an arcing ground fault in the receptacle, that possibility exists.
A look in the attic of the facade revealed additional code violations and other possibilities for a ground fault within an electrode receptacle. There were other violations; however, the flexible metal conduit shown in photo 3 was located near the most burned area in the attic, indicating that the ground fault occurred in the receptacle or the end of the conduit as it terminated to the receptacle.
Photo 4. Shows a typical view of the secondary, high voltage wiring
The GTO cable insulation burned off and the flexible metal conduit had obviously been very hot. Other possibilities that were not accessible for a full inspection would include the termination of the GTO cable in the electrode receptacle. Instructions on the receptacle are specific about the length of cable insulation that is to be stripped, the procedure for installing the button and spring including button placement in the receptacle, and the installation of the strain relief. These electrode receptacles require a pull point or pull box to allow proper termination of the high voltage secondary conductors. Mistakes in those procedures could result in a potential for arcing inside the metal housing. The fact that the installation operated six to eight years without problems lessens the likelihood that the cable was stripped back too far. If that were the case, the ground-fault condition would probably have occurred earlier. Photo 4 shows a typical view of the secondary, high voltage wiring. This shows additional violations and possibilities for a ground fault and cable failure in the flexible metal conduit or the electrode enclosure.
As can be seen in photo 4, flexible conduit is not secured to the structure at all. This would be a violation of the supporting requirements for flexible metal conduit located in Article 350. After several years, the weight of the conduit and wire along with any additional stress caused by settling of the building or maintenance personnel walking and crawling through the space could have placed enough strain on the terminations to reduce the spacings required in the electrode receptacles to prevent arcing. With no boxes provided, it is hard to imagine how the GTO cable could have been installed on both ends with no place to push the slack in cable needed to make the terminations. This probably resulted in less than ideal spacings from the beginning. A closer look at the picture reveals that the flexible metal conduit is 3/8 inch. Articles 600 and 350 of the 1993, 1996, and 1999 NEC, do not include provisions to use flexible metal conduit smaller than 1/2 inch. During the time that this installation was completed, UL Standard 48 may have permitted 3/8 flexible metal conduit to be used with listed signs. Industry discussions on this topic indicate that the use of 3/8″ flexible metal conduit can increase the presence of capacitive coupling and corona because there is obviously less air space between the GTO cable and the grounded conduit wall than provided with larger conduit sizes. This increased capacitive coupling increases the leakage current to ground, and increased corona produces more ozone, which degrades the insulating properties of the GTO cable insulation.
Photo 5. Another issue that is obvious in photo 5 is that grounding requirements were not met.
Another issue that is obvious in photo 5 is that grounding requirements were not met. Many isolated sections of ungrounded flexible metal conduit go from one metal enclosed electrode assembly to another. The 1993 NEC, in Section 600-36(c), required secondary conductors for outline lighting and skeleton-type signs to be enclosed in grounded metal raceways. A fine print note (FPN) to Section 600-31(a) Wiring Methods, refers to Section 600-5 that makes a general reference to Article 250. It also included an exception allowing isolated noncurrent-carrying metal parts of outline lighting to be bonded with a No. 14 conductor and grounded in accordance with Article 250. In 1996, that bonding conductor size was changed to No. 12. When considering the purpose of grounding noncurrent-carrying metal parts coupled with the fact that there was no overcurrent device on the secondary of the transformer and then taking into consideration that the secondary current limitations for the transformer was limited to 60 milliamperes in 1993 and 300 milliamperes in 1996, it is obvious that overcurrent devices are not going to open in a ground-fault condition in the neon secondary circuit. At the voltage levels used for this application, equalizing potential of all the metal parts is important to minimize arcing. Providing a low impedance path for fault current to return to the source is also important to minimize current flow through damp combustible materials that could become a real fire hazard. Another issue that could be discussed is the use of the 3/8 flexible metal conduit as a bonding means from the transformer enclosure to the first metal enclosed electrode assembly. One thing that is probably not debatable is the termination of the flexible metal conduit to the transformer enclosure in photo 6. The fittings used in this installation at the terminations of the flexible metal conduit do not appear to be suitable for bonding.
Photo 6. One thing that is probably not debatable is the termination of the flexible metal conduit to the transformer enclosure
Other issues that are shown in the pictures of the transformer enclosures include: transformers were not fastened to the enclosures, enclosures were not fastened to the structure, spacings from secondary terminals do not seem to comply, bends in the GTO cable seem severe, covers were not installed on enclosures. Although these items did not appear to cause this fire, any one of them could have become the source of a fire, given the right set of circumstances.
One last issue to consider is the current requirement for secondary-circuit ground-fault protection (SCGFP). This type of protection was not available or required during the 1993 NEC cycle. This installation should have never been energized. However, in those areas where there is no adoption, enforcement, or adherence to the NEC, the secondary-circuit ground-fault protection would provide a level of protection for the public and property from these types of installations. These installations are still required to comply with the NEC.
One of the most important lessons that can be learned by this small fire is that violations of the NEC may exist in many installations. When those areas are identified, it is important to realize that the NEC was developed by the entire electrical industry, viewing the requirements from a variety of perspectives. It is important also to remember that the purpose of the NEC as stated in Section 90-1(a) is “the practical safeguarding of persons and property from hazards arising from the use of electricity.”1 Therefore, it is important not to become complacent. If that happens, with installers or inspectors, those many small discrepancies can manifest into much larger hazards for persons and properties.
1 NFPA 70, National Electrical Code1999 Edition (Quincy, MA: National Fire Protection Association, Inc., 1998, p. 70-17.
Find Us on Socials