Even as PV sales and installations are booming (especially in states or regions providing financial incentives), PV systems are still relatively rare. While many inspectors have neither seen nor inspected one, some inspectors are inundated with inspection requests for these systems. Some inspectors never want to see or inspect a PV system. The rarity of PV systems does not prepare the typical inspector when he or she comes upon one for the first time. These systems and the equipment used in them are unlike other common electrical power systems.
PV Modules
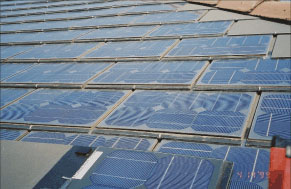
produce electricity when illuminated and the normal cautions associated with any electrical power system should be followed. PV modules come in differing power and voltage ratings. They must be connected in a manner that produces the needed voltage, current, and power since the output of a single module is usually not sufficient.
PV Combiners
PV combiners (PV j-boxes or PV combining enclosures) are common in PV systems operating at dc nominal voltages of 12, 24, and 48 volts and sometimes are used on higher voltage systems (up to 600 volts). In these systems, it is a normal practice to connect modules
Photo 3. PV modules laminated to metal roof
in series (called a source circuit) to get the proper voltage and then connect each series string of modules in parallel through a PV combiner to increase the current to get the desired power level. These combiners will usually contain the overcurrent devices (fuses or circuit breakers) that are required to protect the module interconnecting conductors from fault currents and the individual modules from reverse currents. The reverse currents may originate from parallel-connected strings of modules, from reverse currents from the batteries in a system that has them, or from backfeed currents from a utility-interactive inverter. The ratings of the overcurrent devices must be consistent with the ampacity of the conductors connecting the modules and the maximum series fuse marked on the back of the module. The combiner might be viewed as a branch circuit load center connected in
Photo 4. PV combiner with fuses
reverse acting like a PV source panel. The overcurrent devices in this enclosure are located in the proper place in the PV circuits to meet NEC and UL requirements. Most of these enclosures are white since they may be exposed to sunlight and white minimizes the internal temperature rise (see photos 4 and 5). Inspectors should check for screw-cover enclosures and warning labels if the combiner contains circuit breakers or fuses and has internal, exposed, energized terminals. Several units have been listed with no external labels warning that there are no user serviceable parts inside. UL Standard 1741 will be changed to reflect the requirement for such warning labels because there are internal, exposed busbars in these units that pose shock hazards. It may seem strange, but these enclosures containing normally user-serviceable
Photos 5. PV combiner with circuit breakers
items like fuses and circuit breakers are not required to have a dead-front interior panel.
Charge Controllers
Stand-alone systems and utility-interactive (U-I) systems with battery banks will also have charge controllers that regulate the state-of-charge to the battery bank. Charge controllers come in many sizes, shapes, and colors (see photos 6, 7 and 8). When properly adjusted, they protect the batteries from being overcharged. The installer is responsible for adjusting these devices
Photo 6. 40 A PV charge controller with remote display
properly. Inspectors should verify good field terminations, proper conductor sizes, and appropriate overcurrent devices protecting those conductors. For example, if a charge controller has a continuous 60-amp rating, then the connected conductors should be rated at least at 75 amps (1.25 x 60) and have appropriate overcurrent protection.
Inverters
Inverters are found in both stand-alone systems and U-I systems. They essentially convert direct current (dc) energy from the PV system (and the dc energy stored in batteries) to alternating current (ac) energy for use by local loads or for feeding into the utility system. Some U-I inverters have the capability to power
Photo 7. 60 A PV charge controller
standby load circuits from batteries when the utility is down (see photos 9, 10, and 11). Unfortunately installation manuals for these complex inverters (particularly the stand-alone types) can be several hundred pages long. The inspector should verify the proper dc and ac conductor sizes and overcurrent protection. Both are based on the rated ac power output of the inverter. [See 690.8 and 690.9 in the NEC Handbook.]
The last, somewhat unique, piece of equipment found in PV systems is the NEC 690.5 required ground-fault protection device.
Ground-Fault Protection Devices
Section 690.5, Ground-Fault Protection, of the 1987 NEC added new requirements for
Photo 8. 60 A max power tracking PV charge controller
photovoltaic (PV) systems mounted on the roofs of dwellings. The requirements are intended to reduce fire hazards resulting from ground faults in PV systems mounted on the roofs of dwellings. There is no intent to provide any shock protection, and the requirement is not to be associated with a direct current (dc) GFCI. The ground-fault protection device (GFPD) is intended to deal only with ground faults and not line-to-line faults.
The requirements for the ground-fault protection device have been modified in subsequent revisions of the Code and the current requirements for the device are as follows.
1. Detect a ground fault
2. Interrupt the fault current
3. Indicate that there was a ground fault
4. Open the ungrounded PV conductors
To understand how these GFPDs work, it must be understood that nearly all currently available inverters, both stand-alone and utility-interactive, employ a transformer that isolates the dc grounded circuit conductor (usually the negative) from the ac grounded circuit conductor (usually the neutral). With this transformer isolation, the dc side of a PV system may be considered to be similar to a separately derived system and, as such, must have a single dc bonding connection (jumper) that connects the dc grounded circuit conductor to a common grounding point where the dc equipment-grounding conductors and the dc grounding electrode are connected. Like grounded ac systems, only a single dc bonding connection is allowed. If more than one bonding connection were allowed on either the ac side of the system or on the dc side of the system, unwanted currents would circulate in the equipment-grounding conductors and would violate NEC 250.6.
Photo 9. Stand-alone 4 kW inverter
GFPDs are available as separate devices for adding to stand-alone PV systems and as internal circuits in most utility-interactive inverters. These devices contain and serve as the dc bonding connection.
Figure 1. Ground-fault paths
In any ground-fault scenario on the dc side of the PV system, ground-fault currents from any source (PV modules or batteries in stand-alone systems) must eventually flow through the dc bonding connection on their way from the energy source through the fault and back to the energy source. This includes single ground faults involving the positive conductor faulting to ground or in the negative conductor faulting to ground. In ground faults involving the negative conductor (a grounded conductor), the fault creates unwanted parallel paths for the negative currents and the fault currents will also flow through the dc bonding connection. The diagram in figure 1 shows both positive (red) and negative (blue) ground faults and the paths that the fault currents take. As noted above, all ground-fault currents must pass through the dc bonding connection where the GFPD sensing device is located.
Photo 10. Utility-interactive 2.5 kW inverter
To meet the NEC 690.5 requirements, a typical GFPD has a 1/2 amp to 1 amp and sometimes 5 amp overcurrent device installed in the dc bonding connection. When the dc ground-fault currents exceed the current rating of the device, it opens. By opening, the overcurrent device interrupts the ground-fault current as required in 690.5. If a circuit breaker is employed as the overcurrent device, the tripped position of the breaker handle provides the indicating function. When a fuse is used, an additional electronic monitoring circuit in the inverter provides an indication that there has been a ground-fault. The indication function is also a 690.5 requirement. There is no automatic resetting of these devices.
In the GFPD using a circuit breaker as the sensing device, an additional circuit breaker is mechanically connected (common handle/common trip) to the sensing circuit breaker (see photo 12). These types of GFPDs may be found in both stand-alone and 48-volt utility-interactive systems. This additional circuit breaker (usually rated at 100 amps and used as a switch rather than an overcurrent device) is connected in series with the ungrounded circuit conductor from the PV array. In this manner, when a ground fault is sensed and interrupted, the added circuit breaker disconnects the PV array from the rest of the circuit providing an additional indication that something has happened that needs attention.
Photo 11. Utility-interactive 3.5 kW inverter
Even though the GFPD uses a 100-amp circuit breaker in the ungrounded PV conductor, the 100-amp circuit breaker should not be used as the PV disconnect because in normal use of the system, turning off this breaker would unground the system and this is undesirable in non-fault situations.
Photo 12. Stand-alone PV ground-fault protection device
In the GFPD installed in utility-interactive inverters using a fuse as the sensing element, the electronic controls in the inverter that indicate that there has been a fault, also turn the inverter off and open the internal connections to the ac line. The inverters in photos 10 and 11 have internal fuses as part of the required ground-fault protection device. In listing these inverters, UL has indicated that this method of turning off the inverter to provide an additional indication of trouble meets the requirements of 690.5(B) for disconnecting the ungrounded PV conductor.
It should be noted that the dc GFPD detects and interrupts ground faults anywhere in the dc wiring and the GFPD may be located anywhere in the dc system. GFPDs installed in the utility-interactive inverters or installed in dc power centers on stand-alone systems are the most logical places for these devices. There is no requirement to install them at the PV module location. Installing them at the modules would significantly increase the length of the dc grounding electrode conductor and complicate the routing of that conductor. To achieve significant additional safety enhancements would require a GFPD at each and every module. Equipment to do this does not exist and there are no requirements for such equipment.
These devices are fully capable of interrupting ground faults occurring anywhere in the dc system including faults at the PV array or anywhere in the dc wiring from the PV module to the inverter and even to the battery in stand-alone systems. All of this can be done from any location on the dc circuit. Fire reduction and increased safety are achieved by having these GFPD on residential PV systems.
Yes, during a ground fault, the dc bonding connection is opened, and if the ground fault cures itself for some reason, the dc system remains ungrounded until the system is reset. A positive-to-ground fault may allow the negative conductor (now ungrounded) to go to the open-circuit voltage with respect to ground. This is addressed by the marking requirements of 690.5(C). A very high value resistance is usually built into the GFPD and this resistance bleeds off static electric charges and keeps the PV system loosely referenced to ground (but not solidly grounded) during ground-fault actions. The resistance is selected so that any fault currents still flowing are only a few milliamps—far too low to be a fire hazard.
PV equipment may look a little strange. However, most, if not all, of it is listed and can be installed safely according to the requirements established by theNational Electrical Code. Jump in, inspect away, the water’s fine, and the PV industry needs all the help it can get.
For Additional Information
If this article has raised questions, do not hesitate to contact the author by phone or e-mail. E-mail: jwiles@nmsu.edu Phone: 505-646-6105
A PV Systems Inspector/Installer Checklist will be sent via e-mail to those requesting it. A copy of the 100-page Photovoltaic Power Systems and the National Electrical Code: Suggested Practices, published by Sandia National Laboratories and written by the author, is available on the SWTDI web site or can be mailed at no charge to those requesting a copy with their address by e-mail. The Southwest Technology Development web site (http://www.nmsu.edu/~tdi) maintains all copies of the “Code Corner Columns” written by the author and published in Home Power Magazine over the last 10 years.
The author makes 6–8 hour presentations on “”PV Systems and the NEC”” to groups of 40 or more inspectors, electricians, electrical contractors, and PV professionals for a very nominal cost on an as-requested basis. Call for more information.
Find Us on Socials