“Codes” are regulations to protect the safety of the public that are recommended by knowledgeable experts to be written into law by municipalities. The earliest building code in the U.S. was passed in Baltimore in 1859, but it wasn’t until the mid-20th Century that general building codes were published and adopted by large regions of the country. The most fundamental additions to today’s International Code Council (ICC) are the recently added Energy Conservation Codes, which were created to preserve our natural resources.
How does this relate to lighting? Lighting and energy codes are adopted for buildings by cities, states and other government bodies based upon standards written by technical experts that are listed by the American National Standards Association (ANSI) and then are enforced by the building departments of those municipalities. The penalties vary, but the strongest one is the withholding of a Certificate of Occupancy to the owner when a building is completed, keeping it from being occupied.
These building and energy codes are upgraded on a timely basis to keep up with field experience and new developments in the technical improvements of lighting devices. Inspection and compliance varies widely by municipalities, but once a code document is adopted into law, the owner or contractor is liable for its proper implementation. From a technical viewpoint, the important guide is the adoption of “What’s New” and “How to Do It.” Historically, these codes originated in the population centers in the east and spread westward across the country, being modified where necessary due to local conditions like weather and coastal humidity. Recently, however, with our recognition of the importance of conserving energy and non-renewable resources, the state of California—with the widest spread of geographical latitudes and climate variation in the continental U.S.—has been the most aggressive in increasing the severity of energy conserving measures, and these regulations have been spreading eastward across the country.
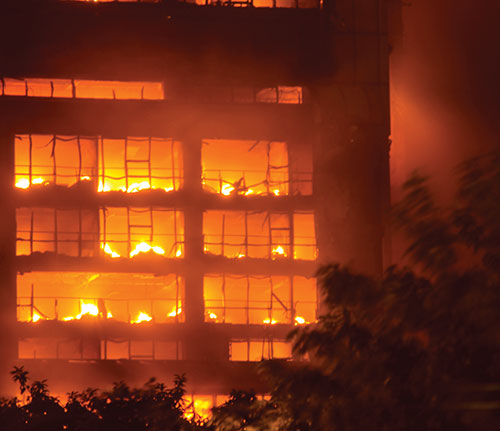
What is missing from today’s codes?
We have been a little slow in responding to the lessons learned from catastrophic events like fires and explosions. Jake Pauls, the nation’s leading expert on building failures due to fires, explains that it is impossible to interview people who have just escaped from a burning building because the trauma is so severe that they just want help and are too frightened to give accurate details about their escape. For example, there has always been the common belief that people die in fires from asphyxiation, not poisoning from the combustion of toxic materials. This was true in the first attack on NYC’s twin towers in 1993 when six people died this way. But now, after the destruction of both towers on 9/11/01, we know that many of the rescuers and many first responders were poisoned by products of combustion and are dying slowly. So we have established that the nature of the materials in a building are important; and we have not responded to the threat from toxic fumes emanating from new products used in buildings, lighting included.
Secondly, there has been a recent evolution in lighting caused by the use of solid state devices like light emitting diodes (LEDs), with the promise of more to come. While this has meant that the initial cost of the luminaires has increased, fewer units are required, or if upgrading buildings, the wattage of existing units has been significantly reduced. For example, we have become entranced by advanced methods of control of lighting without the recognition that as we get closer to the accomplishment of reaching Net Zero Energy (NZE) in the next 15 years, the return on investment (ROI) period increases dramatically. Specifically, lighting power density (LPD) in new and upgraded buildings is 0.5 watts/sq. ft. or less, and professional lighting designers are now able to get to as low as half of that level. A major manufacturer of lighting equipment and controls just announced the introduction of a sophisticated day-lighting control system that will cut lighting load another 15%. If the LPD is 0.5 w and the use of a new (and expensive) control device saves 0.075 w/sf annually, at a utility rate of $0.15/kWh with use of 3000 hours annually, the savings will be $0.03/sf. Most of these control systems are limited to a maximum LED load of 600 watts, which limits the savings to a room of 1200 sf maximum. The maximum possible annual savings for a 1200 sf room at $.03/sf are $36. If the LPD gets down to 0.3 w/sf, the ROI period for the material and installation may exceed an uneconomical 20 years. The manufacturers of lighting control equipment have to adapt to the realities of the age of NZE when the usage of energy will not exceed that which is site-generated.
What lessons have we missed in lighting codes?
Most high-rise buildings post a floor plan in every elevator lobby showing the location of the stairways, and a warning not to use the elevator in the event of a fire, but go to the nearest stairway shown on the floor plan. The ANSI 101 Life Safety Code prescribes the requirement for emergency lighting in stairways and landings in the path of egress, and most municipalities have adapted to it with bi-level lighting. However, it may not always be possible to read the sign or the map on the wall in the elevator lobby with the existing emergency lighting, if there is any. And while bi-level lighting is useful in emergency egress areas, we’ll see below how bi-level lighting units for the reduction of 24/7 load usage have also come up against poorly-worded municipal or state codes.
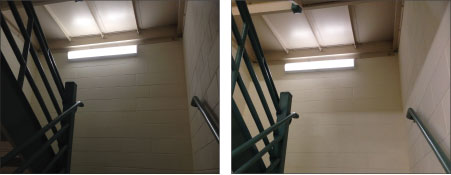
With regard to safety, the US Consumer Products Safety Commission through the National Electronic Injury Surveillance System (NEISS) keeps records of emergency room hospital visits by people who have suffered accidents of all types. For 2011 and 2013— the latest years for which there is data—there were1,651 national injury estimates for product code 4063–Panelboards, Circuit Breakers, GFCIs or Fuses. For 2013, there were 1,278 injuries for the same code 4063.
According to the Bureau of Labor Statistics, U.S. Department of Labor, January 2015, workers who sustained injuries and illnesses involving ladders require three times the recuperation time than for all workers at 24 median days away from work.
Too many electricians or maintenance people are injured by trying to service lighting equipment that is located over machinery of one sort or another and they reach too far and either get a shock, or fall off the ladder, or both. This could be seen as an example of how and why building codes originate. Statistics show overexertion, which includes overreaching, is the #1 cause of workplace accidents.
Lighting codes and a ‘high’ rise
The first major upgrade using bi-level lighting occurred in 1997 at a large housing development adjacent to JFK airport in New York City, comprised of 46 high-rise apartment buildings. 20,000 surface mounted “Occusmart” units, invented by Lamar, containing two 13W CFL lamps in each, were used to replace an equal number of 32/40w circline lamp units in the corridors and stairways of the buildings, which at the time were home to more than 14,000 people. In these bi-level fixtures, one lamp remained lit 24/7 while the other was controlled by an occupancy sensor that turned it on when anyone walked the stairs or occupied a corridor. Because frequent switching of a fluorescent lamp severely reduces the life of both the lamp and ballast, the controlled lamp was kept on for 30 minutes after the last person left the space.
Bi-level lighting was first adopted by the State of California in the 1978 Title 24 Energy Code for use in offices, but the 30 minute “dwell” time was considered a waste of energy, especially when a person’s momentary entrance would trigger the light, setting it ‘on’ for a half hour. Consequently, Title 24 was changed in 1992 to require “occupancy” sensors that had to be turned on manually, so the lights would not be turned on for 30 minutes if the visitor was just dropping off mail. Today, LEDs are used to reduce the energy consumed in those same spaces, which can be switched on and off often with no loss of lamp life. Unfortunately, most of the occupancy sensors installed after the last code change cannot be reprogrammed to stay on only very briefly after a room is vacated. Furthermore, most of the occupancy sensors only use a line-of-sight infrared signal to detect occupancy. A more effective signaling system employs ultrasonic waves, which detect people without necessarily “seeing” them: if a person enters a stairway, they can be detected by the bouncing ultrasonic waves on the floor below and the floor above to make their passage more secure and safe, whether going up or down.
Police and security personnel at the NYC housing complex found that a number of young occupants would go into a stairway and remove the lamps from the bi-level fixtures to smoke pot unseen, thus allowing them some time to flee in the dark and not be caught. With ultrasonic technology sensors, anyone ascending or descending would know immediately that if the lamps, which should be triggered by the ultrasonic waves on the landings above and below do not go on, it is not safe to proceed any further.
The safest, most efficient solution is to change the Title 24 code to allow a shorter illumination time, instead of 30 minutes, and require tamper-resistant or solid-state LED technology where bulbs cannot easily be removed.
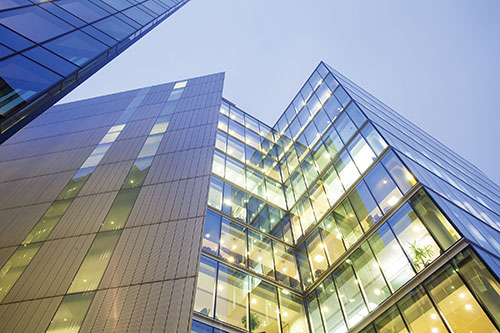
Energy Codes vs. the NEC
In the past, the only control used to turn on or off incandescent or fluorescent lights was a wall switch, so the control wire could be brought down from the “home run” in an outlet box in, or on, the ceiling, without a neutral wire. Now, energy codes are requiring step dimming for fluorescent units and continuous dimming for LED units which is difficult, because it can be an NEC code violation not to have a neutral in an outlet box used for dimming. The National Electric Code (NEC) should require a neutral in all switch boxes.
The NEC acknowledges the existence of energy codes by allowing an exception to the requirement that all buildings now require the electrical system to allow for the capacity to serve 3.5 Watts/sf of lighting to reduce it to 1.5 w/sf, if they segregate the lighting to its own panels and monitor it, which saves thousands of dollars in the cost of the service entry, risers, panels and home runs. But the energy codes now limit lighting power density (LPD) to less than 1 Watt/sf, and many professionals, anticipating the arrival of Net Zero Energy buildings in 15 years, are using occupancy, daylight harvesting technology and site generated solar or wind power to provide the necessary IES recommended lighting levels with only 0.5 w/sf. And soon, with the development of more efficient energy storage devices, it will be possible to get by with only 0.2 to 0.3 w/sf for lighting.
Some cynics collect phrases that are considered a contradiction in terms like “giant shrimp” or “military intelligence” and lately have added “creative bureaucracy” to the list. Let’s hope that we can keep pace in our codes with the rapidly changing technological advances made by our industry. And if we have to change those codes based on field experience, as in California, “it’s a far better thing we do” for safety’s sake.
Find Us on Socials