With the rapidly growing commercial use of 3D printers to make parts, manufacturers still unfamiliar with this technology need to know its advantages and drawbacks compared to injection molding. The two processes form parts in very different ways, and understanding those differences is critical when evaluating which method is best for a manufacturing project.
Injection Molding
In traditional injection molding, plastic resin is heated to a point it will flow and fill a cooled metal mold using very high pressure. This mold can be used repeatedly at a high speed, with parts made only seconds apart, for mass production of that single part. This ensures all parts are consistent, accurate and fully dense.
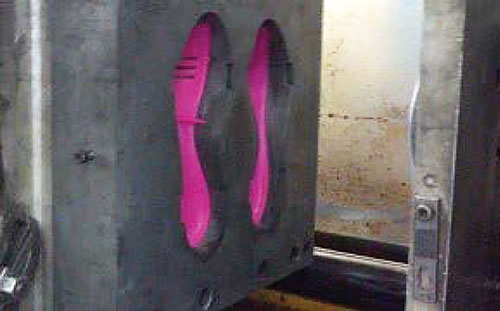
These products’ properties consistently meet performance characteristics set by the design engineer. The choices of resins used in injection molding are wide-ranging, with an established industry record for plastic part production. A long lead time is needed to build the necessary tooling, so this process is best suited for less complex designs and high-volume production.
3D Printing
3D printing works in a much different way. The 3D printing process does not use metal molds or pressure. 3D printed parts are built in thin layers, or cross-sections, based on a 3D design file. The 3D printer precisely forms each new layer on top of the last one to create a finished part.
The layering process makes it ideal for more complex designs and the process is more cost-effective than injection molding. By printing each item one at a time, the process takes longer per part than injection molding, making it better suited to low-volume production.
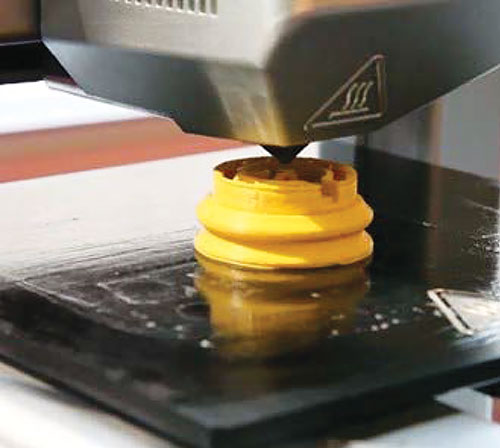
Some smaller designs can print in 30 minutes or less. Larger parts can take several hours to print. Printed layers can vary in thickness depending on the 3D printing technology. Thicker layers will improve the total time, but the surface finish, quality of detail, and accuracy will diminish.
In 3D printing, no mold holds the part in shape as the layers are formed and no pressure is used to ensure density, so the predictability of the finished part is sometimes less consistent. Typically, the parts are not fully dense, which can make them weaker than from an injection molded process.
3D printing, as it is presently understood, is not always suitable to replace most uses of traditional injection molding, which has benefitted as well from technological advances
High-strength and flame-resistant pieces, in particular, are better served by an injection molding process, and the resin selections available far outnumber those for 3D printing.
However, the recent expansion of 3D printer use in smaller businesses and homes points to where this technology might see more initial success. 3D printing is ideal for creating highly detailed, customizable parts in low volumes. Without the need for expensive molds, 3D printing offers the flexibility of implementing new designs cheaply and quickly. 3D printing is a growth industry, so the gap in the selection of resins and metals should shrink as economy-of-scale principles make more varieties marketable.
What about electronics?
Today, electronics are limited to mostly 2D/flat formats. These flat circuit boards and cables are often inserted into injection molded parts. However, designers are continuing to innovate. An example includes using over-molding to help protect these electronics against extreme conditions.
In 3D printing, the ability to effectively and consistently print electronics is still in its infancy. Systems are available to print basic conductive materials, both as final parts or as part of an enclosure. There are also methods of applying conductive materials after a part has been printed, utilizing an aerosol system to apply the material in a very precise manner. What the future holds is still a big question, but the concept of printing a fully functional cell phone with the battery, wires, circuit board and screen is a real possibility.
Summary
The future has arrived for this 30-year-old technology. 3D printing gives established manufacturers a clear alternative to injection molding for certain production needs while offering small-scale businesses and amateur modelers a cost-effective way to compete commercially when creating specialized, design-intensive parts.
Paul’s Points:
Injection Molding
- Longer lead time required to build necessary tooling
- Parts are consistent, accurate and fully dense
- Best suited for less complex designs and high volume production
3D Printing
- No molds needed; enables flexibility to implement complex designs faster with less expense
- Predictability of part is often less consistent
- Ideal for highly detailed, customizable parts in low volumes
Find Us on Socials