Based on this series of articles and presentations that I make to groups of inspectors around the country, I get several calls and e-mails a week and sometimes several calls a day from inspectors looking at PV plans or inspecting PV systems. The questions that they pose are always challenging because most of the inspectors have done their homework and found the Code lacking in clear concise answers. I usually gain new insights on the Code from these calls. Here are some of the more common questions and the best answers that I have. I encourage these calls so that everyone involved can help to ensure that the numerous PV systems being installed are as safe as possible.
Location of main dc PV disconnect
Question: Where should the main dc PV disconnect be located? NEC Section 690.14 says either inside or outside at the point of first penetration of the PV source or output conductors in a readily accessible location. Is there a preference between inside and outside locations?
Answer: The dc PV disconnect resembles the ac service-entrance disconnect in function, although it is not required to be rated as service-entrance equipment. The location of this dc PV disconnect should take into account the local requirements for locating the ac service
Photo 1. DC PV disconnect grouped with ac service disconnect
disconnect since they more than likely take into account emergency response requirements. If the ac service disconnect for the house or structure is outside, it seems reasonable to put the dc PV disconnect outside in the same vicinity. In a similar manner, an inside ac service disconnect would seem to point to an inside location for the dc PV disconnect. Both ac and PV disconnects should be “grouped” (as defined by the AHJ) since they both shut off power to the building (see photo 1). In a few cases it has been argued that the PV system is a second supply to the house and may have the main dc PV disconnect remotely located from the ac service disconnect if all disconnects are properly placarded.
Many jurisdictions allow an inside ac service disconnect, although a locked house may not be readily accessible. If an inside disconnect is allowed, then many locations for the dc PV disconnect are possible including on the exterior wall of an upstairs bedroom for example. Some installers would like to put the disconnect in an attic to eliminate the wiring on the outside of the building, but an attic would not be considered readily accessible unless permanent, fixed stairs were available to the attic.
Location of ac PV disconnect
Question: Where should the ac PV disconnect be located?
Answer: In the smaller residential systems, the ac PV disconnect is usually a backfed breaker in the load ac center and, if the inverter is close to the load center containing the backfed breaker,
Photo 2. AC and dc disconnects grouped at the inverter
no additional ac disconnect is required. The ac circuit between the inverter and the load center is very similar to any ac branch circuit. If there is some distance between the inverter and the backfed breaker, then an additional disconnect should be located at the inverter to allow safe servicing of that product (see photo 2). The AHJ determines how far apart the inverter and the disconnect may be. Some require a spread-arms’ distance between the ac and dc disconnects at the inverter, and other AHJs allow the disconnect to be some distance apart as long as they are both visible from the inverter.
Inverters with internal ac and/or dc disconnects
Question: I am seeing inverters with ac and dc or just dc disconnects built into them. Do these inverters meet code requirements when installed without external ac and dc disconnects?
Answer: The NEC provides little guidance in this area. The inverters have been listed to UL
Photo 3. Internal ac and dc disconnects
Standard 1741 and are considered to be safe in operation. They do have the internal disconnects that allow the unqualified user to safely turn them on and off during normal operations (see photo 3). The AHJ or the jurisdiction should decide on the safety requirements for servicing these electronic devices. Section 690.18 suggests that the PV array be covered before servicing the system and that blocking the light from the modules would de-energize the output circuits if done properly. However, on large roof-mounted arrays, covering the entire array is not a common or easy practice. If the AHJ or jurisdiction judges that qualified people are going to be disconnecting those energized dc input conductors from the PV array in the inverter, then the internal disconnect is probably OK. However, if there is a possibility that the inverter will be removed for service by unqualified people, they probably should not be handling those energized PV input conductors, and at least an external dc disconnect should be required (see photo 4). Hopefully, anyone servicing one of these inverters would know enough to open the backfed ac breaker to remove ac power from the inverter before disconnecting the ac circuits.
Several older inverters (out of production) and some newer inverters have an electronics section that can be removed for service from a lower input/output circuit section. The AHJ should evaluate the difficulty of the removal process. Some units can require that energized conductors be pulled through conduit knockouts. The input/output power section remaining attached to the wall should be examined to ensure that it is safe for contact by unqualified people and that it is somewhat weather resistant if the inverter is mounted outside. If these conditions are not met, the AHJ might consider requiring external disconnects.
Location of manual disconnect
Question: The local utility requires a manual safety switch (disconnect) between the inverter and the utility point of connection. What are the Code requirements pertaining to the installation of this disconnect?
Answer: This safety switch is a common requirement imposed by many, but not all, utilities. The utility wants to ensure that there is no possibility of a PV system “islanding” and energizing a feeder that a lineman has disconnected from the utility. The listed, utility-interactive inverter will sense a turned off grid and shut down. This automatic action plus the lineman’s safety procedures of measuring, shorting, and grounding the line to be serviced plus wearing protective gear are sufficient to allow some utilities to not require the safety switch. Other utilities will require the safety switch and will dictate its location—usually near the utility meter. However, this safety switch is being installed on the premises wiring and must follow the general Code requirements as far as rating, conductors, wiring methods, grounding, height, and clearances. In this position on the dedicated branch circuit serving the PV inverter, the safety switch would not have to be rated as service-entrance equipment.
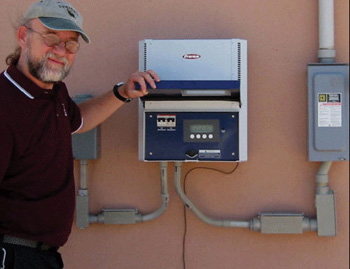
If the inverter is adjacent to the utility-required disconnect on the outside of the house, in many cases, it can also be used as the inverter ac disconnect. In a situation where the PV utility connection is made on the supply side of the service disconnect, this utility-required disconnect may also serve as the PV ac inverter disconnect if it were rated as service-entrance equipment.
Aluminum lay-in lugs
Question: I have a PV system where aluminum lay-in lugs have been attached to the narrow sides of the modules for equipment grounding. These modules are marked for grounding points only on the long side of the modules. Does this comply with the Code?
Answer: There will be a couple of things that the installer must verify. First, aluminum lay-in
Photo 5. Dry-location lug rusting outdoors
lugs are generally not listed for outdoor/wet applications because the setscrew is typically plated steel and will rust quickly (see photo 5). The correct lay-in lug for these applications is a tin-plated, solid-copper lug that has a stainless-steel screw (see photo 6). These lugs are listed for underground, direct-burial applications and have been found to be suitable for wet/outdoor applications. While they are not listed for use with aluminum conductors, the tin plating allows them to be bolted to aluminum surfaces (like aluminum bus bars and aluminum module frames). The aluminum module frame should be scraped to remove the invisible oxidation and an anti-oxidation compound like Burndy PENETROX A-13 should be applied between the lug and the aluminum module frame at the contact point. A solid-copper lug without the tin plating should not be used since copper should not come into contact with aluminum (see photo 7). Drilling the module on the short side away from the marked grounding points may violate both the listing and the warranty on the module. The module manufacturer should be contacted before any modification of the module is undertaken that deviates from the instructions supplied with the module or the markings on the module.
Photo 6. Direct burial lug with stainless-steel screw
Unbalanced PV array and inverter ratings
Question: I have a PV system where the PV array is rated at 3000 watts, but the inverter connected to the array is rated at only 2500 watts. Won’t this arrangement damage the inverter, make the system unsafe, and be non-code-compliant?
Answer: The rating (3000 watts in this case) of a PV array is normally expressed at a set of standard test conditions (STC) of 1000 watts per square meter of irradiance (sunlight intensity) and a module temperature of 25°C (77°F). These laboratory test conditions are infrequently met in the installed PV array. At an outdoor temperature of 35°C (95°F), the PV modules will be operating at a temperature of about 65°C (149°F) and the array will only be putting out about 2350 watts when the irradiance is 1000 watts per square meter. The lower power output is due to the fact that PV modules lose
Photo 7. Copper direct burial lug, not suited for aluminum contact
power at the rate of about 0.5 percent per degree Centigrade as the temperature increases. At lower temperatures, higher power levels from the array can be expected, but the inverter simply limits the input current from the array and/or the output power to the utility grid to keep the output from exceeding the inverter rated power. Sizing the array slightly larger than the inverter rating is normal and allows more energy to be delivered to the grid during hot sunny days and during cloudy periods. The inverter protects itself; there is no safety issue, and no Code violation.
For Additional Information
If this article has raised questions, do not hesitate to contact the author by phone or e-mail. E-mail: jwiles@nmsu.edu Phone: 505-646-6105
A color copy of the 143-page, 2005 edition of the Photovoltaic Power Systems and the National Electrical Code: Suggested Practices, published by Sandia National Laboratories and written by the author, may be downloaded from this web site: (http://www.nmsu.edu/~tdi/roswell-8opt.pdf.) The Southwest Technology Development Institute web site (http://www.nmsu.edu/~tdi/Photovoltaics/Codes-Stds/Codes-Stds.html) maintains a PV Systems Inspector/Installer Checklist and all copies of the previous “Perspectives on PV” articles for easy downloading. Copies of “Code Corner,” written by the author and published in Home Power Magazine over the last 10 years, are also available on this web site.
Proposals for the 2008 NEC that were submitted by the PV Industry Forum may be downloaded from this web site:
http://www.nmsu.edu/~tdi/pdf-resources/2008NECproposals2.pdf
The author makes 6–8 hour presentations on “PV Systems and the NEC” to groups of 40 or more inspectors, electricians, electrical contractors, and PV professionals for a very nominal cost on an as-requested basis. A schedule of future presentations can be found on the SWTDI web site.
Find Us on Socials