From 1972 until 1980, in the wake of the EC grade aluminum fire saga that began in the mid-1960s as a result of the response of the construction industry to record-high copper prices, US residential builders installed copper-clad aluminum (CCA) building wire for residential branch circuits in tens of thousands (perhaps even hundreds of thousands) of single family homes, condominiums and apartments. In the United States, the decades of the 1960s and the 1970s were plagued by record-high copper prices, the war in Vietnam, gasoline shortages, trade embargos, a deep-rooted cultural paradigm-shift, presidential impeachment proceedings, and a severe economic recession. Radicalism, conflict, and unorthodoxy defined the age.
With the increase in the number of automobiles, as well as the fear of the increase of inner city crime, the nation as a whole continued to suburbanize, accelerating a migration to newly constructed neighborhoods miles from the large regional cities where once stood farmland, forest, and plains. Cheap power abounded thanks to mass hydro and nuclear projects spread throughout the nation contributing to this growth. But, at the dawning of the seventies, with commodity prices at record highs, the need to economize new construction was evident. Millions of new suburban homes needed to be built.
To wire these new homes for cheap electricity with high-priced, foreign-sourced copper defeated the point, and chaffed the ideals of American ingenuity and national sovereignty. Cheap EC grade aluminum building wire was no longer an option. Due in large part to thermal creep and galvanic corrosion issues as the primary causes of its lethal shortcomings, solid EC grade aluminum building wire had been ushered out of the US market by 1972, and essentially all municipalities within the nation had banned it for use in all branch circuit building wire (BCBW) soon thereafter.
Nevertheless, the US residential construction industry and its advocates continued to search for a lower cost alternative to solid copper. As a result of five years of testing and vetting by accrediting agencies such as UL and the NEC, as well as by a handful of inventors and building wire manufacturers, a solution came in the form of copper-clad aluminum THHN and NM-B.
Trickling into the US market by 1971, CCA was seen as the most promising material for use in residential BCBW.
First and foremost, it was safe and affordable. Even though it was slightly more expensive than the cheaper EC grade aluminum building wire, which was on the way out anyway, CCA still offered considerable savings over expensive solid copper.
Second, it was nearly three times lighter than copper diameter per diameter, making hand-toting heavy coils less of a chore, and pulling wire at the job-site a breeze. It was flexible, but yet sufficiently strong to pull through studs.
Third, it was not brittle like solid EC grade aluminum building wire that caused the fires during the 1960s, and peeling the insulation to make connections was no different than with copper wire.
Finally, because of the thick copper cladding covering the surface of the bare conductor, there was no fear of galvanic corrosion nor creep over decades of use in the circuit. The same copper connectors and devices could be used regardless if a contractor installed solid copper or CCA.
According to UL, dovetailing the two metals – CCA to Solid Copper – was a permissible installation technique as the surfaces of each wire were copper, and the thermal properties practically identical. In short, the construction industry had finally found a low-cost, technically feasible alternative to solid copper for BCBW. Residential builders cheered. A new way to cut construction costs as the suburban building boom rumbled on!
The run for CCA as a solution for BCBW, however, proved to be short-lived. But not for the same reasons that halted the EC grade aluminum building wire a decade before. This time, it was the change in the economy that suspended the business. By 1976, the nagging US recession brought about by the Mideast oil embargo began to bite the residential construction business hard in the form of stagflation, sending copper prices to the floor for the better part of two years. Purchasing a new home during this period became nearly impossible as finance rates hit double-digits. In the wake of the economic turmoil of 1976, CCA for BCBW became non-competitive against solid copper building wire. Production of CCA building wire ground to a halt and distribution programs were suspended indefinitely.
The manufacturers of CCA were few, so the available capacity had not developed to near the size required to service the entire US residential construction industry. From 1972 through 1976, due to record high copper prices, demand for CCA building wire far outweighed the ability to produce and distribute. These five short years were the golden years for CCA for BCBW. The factories could not keep up. The product was flying off the shelves. Those contractors lucky enough to find a supplier could not get enough of it. Everyone on the inside of the CCA BCBW business was either making money or saving money. Even homeowners benefited! They enjoyed safe electrical service while paying less for their new homes.
By 1978, the economy shifted once again, and the “Good Ole Days” for CCA seemed to have returned. Almost like a swan song at the end of a stellar performance, CCA for BCBW became competitive again vs. copper. From 1978 to the summer of 1980, copper prices had rebounded just enough to allow distributors time enough to sell their excess inventories of CCA building wire accumulated before 1977. Although the rebound of copper prices was much needed for copper producers, it came too little too late for CCA producers. Actual production of CCA building wire never resumed after 1977, and by the fall of 1980, copper prices dropped out of sight once again to record lows.
For the next two decades, until January 2003, copper prices operated within a sublime climate of unprecedented low values and nonvolatility. For copper miners and commodity traders, this long period of economic doldrums was despised, akin to Purgatory, and became known as such within certain circles in the mining community. But this too was about to change. Just like some metallurgical remake of the movie Back to the Future, CCA for BCBW returned to competitiveness in October 2005. At the time of this writing, July 2016, with copper cathode trading in a range of US$ 2.08 – 2.25 / lb., CCA remains both the most economically feasible, as well the most technically feasible, building wire conductor on the market for branch-circuit wiring.
The following pages will drill deeper into the details of CCA for residential BCBW. The goal is to provide a reference for those searching for information about the product, or, at the very least, to provide a starting place for one’s research. The intent is to integrate as many sources and voices as possible in the delivery of this information. In Part One of the paper, I will deal largely with history, economics, and standards. I hope to recount the story of CCA from the players and the various companies involved in its development to the demographic and economic trends of the era that allowed it to emerge. I will explain how CCA is manufactured, its mechanical and electrical characteristics, as well as what makes it remarkably suitable for applications like BCBW. And finally, I will discuss CCA’s presence in the NEC, as well as its standard in both ASTM and UL.
The Great Suburbanization of the 1970s
In the face of inflation and general social uneasiness, for millions of Americans, the decade that started in January 1970 saw a deurbanization towards greener pastures. Most large urban areas in the nation saw their population wane. According to Mousumi Sarkar, a researcher for the Demographic Directorate of the US Census Bureau, the number of homes built in the suburbs in the decade of the 1970s rose from 43% to nearly 60% of new homes, whereas new homes in urban areas fell from 30% to almost 20% in the same period.* In fact, “in the decade of the 1970s, some 11.05 million homes were built including single family, apartments and mobile homes.” 1 This figure amounted to nearly 20% of the total residences in the country before 1970, according to the Historic Census for Housing Tables of the US Census Bureau. By 1980, a full 70% of new residential construction was built either in the South or Western regions of the country, the regions that saw the majority of the suburban growth. But even the larger northeastern cities such as New York, Boston, and Washington DC experienced their own share of suburban flight to semi-rural communities with names like Amityville, Marshfield-Duxbury, and Alexandria. By 1980, a full 44% of the US population resided somewhere in the suburbs.
By 1969, the residential construction business, and the nation as a whole became increasingly aware of a new problem plaguing suburban homes: Fires caused by solid aluminum electrical wiring. Few understood the problem, nor were able to gauge the severity of it. The idea to use EC Grade aluminum for residential BCBW arose from a nagging copper shortage which started in the early 1960s. According to Daniel Edelstein of the US Geological Survey, prices of copper cathode, the heavily-traded base form of copper, began to climb in the years of 1963 and 1964 due to voluntary production cuts by producers as well as excessive demand in support of the war in Vietnam. From 1964 to 1968, copper prices spiked to record highs as miners began to strike in South America and Africa.1 During this time, due in part to the high domestic production capacity of aluminum wire in the USA, a push was made by industry to substitute aluminum for copper for BCBW, the single largest market for copper at the time. This push, so thought industry leaders and regulators of the time, would help to relieve the copper shortages, and perhaps bring down the cost of building new suburban homes. Regulators hastily allowed the product to enter the market without demanding a systematic change of the termination and device systems already in the market and designed to work with only solid copper. EC Grade Aluminum failed miserably, ushering in a dark era of American history that resonates even louder today than back then.
Emergence of CCA as a Power Conductor
Certain non-ferrous industrial metals exhibit excellent thermo-electrical properties. Copper and aluminum are two of these metals. Both Copper and aluminum are very efficient conductors of power and are widely used in industry for this reason. Copper is more thermally stable than solid EC grade aluminum (which is 99.5% pure aluminum by grade, and the most efficient conductor of electrical power of all aluminum grades). Thus copper has been traditionally considered for use where electrical connections must maintain their integrity over long periods of service life with little-to-no direct observation. As a result, most low-tension conductor applications popular in the country today, such as THHN and NM-B, utilize copper as the base metal. Where aluminum-friendly connection systems and/or external observation of connections are available, aluminum is generally the conductor metal of choice. Aluminum is much less expensive. Further, in relation to copper, aluminum is lighter. Therefore, many applications in the high and medium tension conductor world can utilize EC grades of aluminum as the base metal. Being lighter, it can airily span distances. EC grade aluminum is also excellent when reinforced against creep by a steel core like with ACSR strands, for example. Aluminum is also found in abundance within our economy, much more so than copper.
The Copper Alliance, a trade group dedicated to the healthy proliferation of copper, indicates that copper is found predominately in Chile, where 31% of copper originates. The United States Geologic Survey reports that in 2015, 18.7 million metric tons of copper were produced world-wide, of which Chile produced nearly 6 million metric tons of this total. Peru and China are the next largest producers of copper, each at 1.7 million metric tons. The United States is the 4th largest producer of copper in the world at 1.25 metric tons per year in 2015.
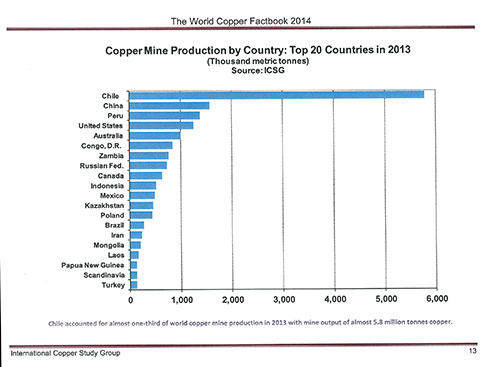
Aluminum, on the other hand, dwarfs the copper industry in as far as metric tons produced. In the United States alone, 2015 saw a production of aluminum of nearly 18 million metric tons by itself—the same tonnage of copper produced globally in 2015. In short, when comparing the two industries, aluminum is perhaps 6 X the size of the copper industry in terms of metric tons produced. Aluminum is also dispersed widely throughout the world, and not concentrated in the hands of few producers or countries. In terms of feet of wire produced vs. copper wire, given that aluminum is 3 X lighter than copper, to say that the aluminum wire industry is 10 X the size of that of copper is a very conservative statement. In short, aluminum is much less subject to shortages and allocations.
But what if out of necessity there came a need to marry the lightweight and economic advantages of aluminum, with the thermal characteristics and connectability of solid copper? In Germany during the war years of the late 1930s and 1940s, such a need did in fact arise! The German government instituted a copper rationing campaign in support of its war effort, giving rise to the first CCA.
It was actually developed in Germany to alleviate copper shortages in the 1930s. 2 Several methods of producing CCA were initially attempted including spraying, dipping, electroplating, and cladding. The spray and electroplating techniques were inconsistent, too thin, and not uniform enough for the desired performance. The technique utilizing heat and pressure became the dominate method for cladding bimetal products. Many advances to the cladding process and the metal alloys themselves have been made over the decades since the introduction of the product to the marketplace. 2
Initial development of Copper Cladded Aluminum took the form of rolled sheets. Pressed coinage, medals, cookware, industrial stampings, plumbing pipes and architectural cladding tiles were its first applications. CCA in the form of wire came later. The first wire products to develop were strand and cable components of antenna communications systems, due to CCA’s lightweight and excellent high-frequency data conduction properties.
Kabelmetal (KM) takes the credit for first developing CCA in the wire form. Founded in Hanover, Germany, in 1900 as Hackethal Wire Works, this proud company eventually evolved into two of the most important companies in the modern nonferrous wire industry. Nexans, a global giant in power conductors, and RFS, a global leader in coaxial and wireless data communication systems, can both trace their roots to Hackethal. Hackethal began researching its CCA process in the late 1950s due to copper shortages caused by the Korean war, 3 and by 1965, patented key elements of a cold-bonding process upon which the modern copper/aluminum bimetallic industry is based. By 1966, Hackethal had changed its name to Kabelmetal according to historical documents from RFS. Many evolutions of the elemental copper cladding process followed, as did technology patents and protection measures, to keep the technology on the cutting edge, as well as out of the hands of competitors. Heavy on R&D, however, Kabelmetal lacked the marketing prowess in the USA to fully capitalize on their invention in the early years.
In 1972, Dr. Gerhard Ziemek, a young Ph.D. engineer employed by Kabelmetal, accepted an award from the Wire Association International (WAI) at their annual meeting in Chicago for the finest technical paper of the year for work in the Electrical Track of the wire industry. The paper’s title: “A New Continuous Process for the Manufacture of Copper Clad Aluminum Conductors.” The Kabelmetal cladding technology was being staged to service not only the US coaxial data-cable market but also the power cable market. But the theory behind this award-winning paper would not become reality until the sun had already set on CCA for power conductors.
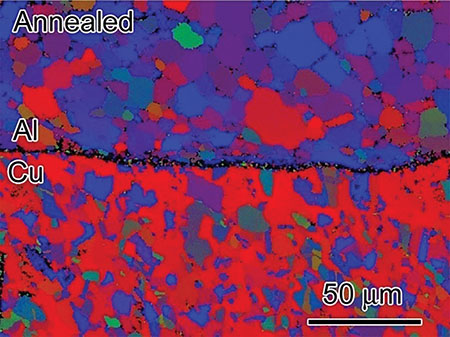
However, there was an American company also interested in the virtues of CCA wire, and armed with a stronger marketing staff than KM. In the late 1950s, Texas Instruments (TI), based in Dallas, TX, forecasted the coming global shortage of copper, which could mean considerable new business if they could develop an alternative. TI quickly recognized that it needed to develop an in-house alternative to solid copper wire. TI had much ground to make up on the Germans, however. In July 1959, TI bought a company called Metals & Controls, an American business dedicated to metals cladding. Over the next half decade, TI labored to develop a heat-bond process as efficient as Dr. Ziemek’s KM cold-bond process, but unique enough to skirt any international patents. By 1963, the prototype process was complete, and field trials ensued (to include standard residential building wire), as is described by an internal TI document from that year entitled: “M&C’s clad-metal expertise was quickly applied to other products.” The article describes the evolution of its CCA wire, and how it would be applied to low-tension building wire as well as coaxial cables. In October 1966, TI finally officially announced to its shareholders that its Attleboro, Massachusetts, facility had developed a copper-cladded wire product with “wide usage possible.”
With its new product, TI made it possible for a wire manufacturer to meet his production commitments within present copper allocations, and particularly without having to buy copper at premium prices. Currently, 1.5 billion pounds of copper are used in the production of pure copper wire each year. This represents about one-third of the country’s annual copper supply. In recent months the shortage of copper has become acute because of the step-up of US military commitments and labor strife in Chile and Zambia, two leading copper producing countries.” 4
As the two companies, Kabelmetal (KM) and Texas Instruments (TI), raced the other to assume the position as the world’s dominate supplier of CCA wire, still in 1969, the application of CCA for use in BCBW was out of reach. When pitted against solid EC grade aluminum, CCA still could not compete. But in the true sense of the word providence, the regulatory climate by 1970 was beginning to turn in their favor, promising more business than the two companies could ever hope to handle.
The Aluminum Wire Troubles of the 1960s
The opportunity for copper-clad aluminum (CCA) for residential branch-circuit building wire (BCBW) came in the wake of an American tragedy. Solid EC grade aluminum was originally supposed to save the residential construction contractor from the shortages and high cost of copper, but as is well documented, it failed miserably to uphold this promise. One single paragraph from Publication 516 of the US Consumer Product Safety Commission (CPSC) sums it up: “The CPSC staff and other government officials have investigated numerous hazardous incidents and fires throughout the nation involving aluminum branch circuit wiring. A national survey conducted by Franklin Research Institute for the CPSC showed that homes built before 1972, and wired with aluminum, are 55 times more likely to have one or more wire connections at outlets reach ‘Fire Hazard Condition’ than homes wired with copper.” That survey encompassed only the wire connections at outlets. It did not address other types of aluminum wire connections and splices in homes that are also prone to fail. No information was developed for aluminum-wired homes build after 1972.” 5
The same publication goes on to state: “A shortage of copper in the mid-1960s caused builders to increase the use of aluminum wire in residential electrical distribution systems from the few large-power circuits to general purpose 15- and 20-ampere-rated circuits. Homes built before 1965 are unlikely to have aluminum branch circuit wiring. On April 28, 1974, two people died in Hampton Bays, NY. Fire officials determined that the fire was caused by an overheating aluminum wire connection at a wall receptacle.” 5
It is obvious in hindsight that EC grade aluminum should have never been applied to BCBW. As a metallurgical solution, EC Grade Aluminum was never a good fit for it. For one, solid EC grade aluminum wire will creep after a few months in the circuit, causing its connection to an electrical device to loosen. Technically speaking, its thermal expansion rate at 90 degrees C is 25% higher than that of solid copper, while its ultimate tensile strength is more than 2X lower. These two factors allow the material to move (or creep) during cycles of power-on and power-off.
Second, a Branch Circuit is a complete system, meaning, all parts must work together to reach a favorable outcome. The terminations in the branch circuit system are as important as the wire itself. Nearly all devices and connectors for residential use in the decades of 1960 and 1970 were designed for use with solid copper wire, not EC grade aluminum, and thus could not deal effectively with the creep or galvanic corrosion inherent in EC grade aluminum. Galvanic corrosion given time, like creep, can easily fail a connection. But perhaps the most unsuitable characteristic of solid EC grade aluminum for BCBW is its brittleness. Solid EC grade aluminum is an unforgiving material if twisted too hard. It breaks twice as easily as solid copper of the same diameter. This breaking gives rise to the potential for hazards caused by poor workmanship.
Forming of the Ad-Hoc Committee by UL
In June of 1972, an Ad Hoc Committee on Aluminum Terminations was formed with the membership from industry and UL. Its purpose was to study and recommend procedures for improving the connectability of larger sizes (AWG #12 and larger) of aluminum conductors.6
The Ad Hoc Committee on Aluminum Terminations had the unenviable job of quietly ushering EC grade aluminum out of the building wire business, while simultaneously not levying wholesale bankruptcy upon the US aluminum industry. There were 11 member-organizations of the Ad Hoc committee, including Underwriters Laboratories, and all were very influential voices in the electrical industry. The Ad Hoc Committee agreed to instruct those manufacturers producing EC grade aluminum building wire to cease all production, so as not to escalate the problem. Then, for those homes already wired with it, the Committee came up with a procedural fix in the form of a 7-page pamphlet. The Committee distributed the pamphlet throughout the country via electrical distribution houses and electrical inspectors. Concerned homeowners were encouraged to call the Committee directly. And finally, the Committee encouraged local municipalities to ban solid EC grade aluminum from use in BCBW, rather than attempt to amend the standards at a national level. There was still some question on whether more suitable aluminum grades could be developed for use in commercial building wire.
However, many municipalities had already acted against solid aluminum of any type for BCBW: in January 1971, at least ten jurisdictions in Orange County, California, had imposed a ban on all direct connections of aluminum wire to devices in sizes 8, 10 and 12.7 Further, “the US CPSC estimated that approximately two million homes were wired with aluminum between 1965 and 1974.” 8
Even though records are not officially kept for fires caused by aluminum wiring, some 53,000 electrical fires nationwide are thought to have started as a result of using EC grade aluminum building wire, or, nearly 3% of the homes wired with solid aluminum. Despite this horror, the truth of the matter is that this number represents less than ¼ of 1% of the homes, condominiums, and apartments built during the period in question: 1965 – 1974. Without question, even one death to an electrical fire is too much. But in its defense, the industry itself quickly recognized that EC grade aluminum was a problem, and thus began regulating itself well before 1972 when UL formed the Ad Hoc Committee on Aluminum Terminations. With the enormous available production capacity of aluminum wire in the United States during the decade of the 1960s, and in light of the overwhelming economic advantage aluminum held over solid copper during that time, easily half of the BCBW business could have shifted to aluminum had the EC grade aluminum product worked as planned. Concerned and conscience-driven individuals in the aluminum wire business recognized that EC grade aluminum was failing. Without this common-sense approach and subsequent self-policing, the disaster could have been much worse.
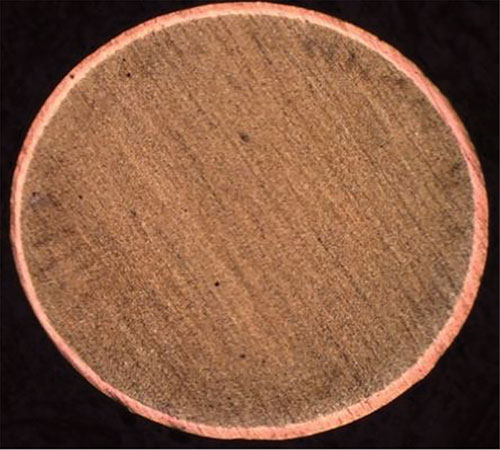
How Is CCA Different than EC grade Aluminum? How is it manufactured?
Copper clad aluminum wire is very different from solid EC grade aluminum wire. For one, CCA belongs to a species of metals known as “Bimetallics,” whereas EC grade aluminum is known as an alloy. A bimetal is not an alloy. An alloy is defined as a mixture of at least two different metals through a molten process. A bimetal is a physical bonding of two separate distinct metals aimed to maintain the best properties of each. A true bimetal is not subject to galvanic corrosion due to the stability of its bond. In other words, it will not corrode itself. A clean bond eliminates the medium for the electro-locomotion of ions, as there is no space or electrical potential in which a corrosion cell can operate. This being the case, a bimetal can be designed to maximize the advantages of both metals for the job it aims to do. In the case of CCA for BCBW, as stated in the introduction, the advantages of using a bimetal are numerous. When set next to solid EC grade aluminum, CCA gains the advantage of being able to connect to devices as if it were copper due to its copper skin and enhanced thermal characteristics. It also maintains 90% of the weight advantage of solid aluminum. Finally, CCA retains a good portion of the economic advantages of solid EC grade aluminum, which makes the consumer happy.
At this writing, there is only one proven bonding process for CCA wire that is good enough to create a bond to call itself a bimetal. The pressure method originally designed by Kabelmetal and brought into the market by Dr. Gerhard Ziemek, or the KM Process, is the benchmark of the industry. The Texas Instruments process (TI Process) uses the very same principals as that of Dr. Ziemek, with slight cosmetic modifications, and the introduction of heat bonding, so it too can be considered a true bimetallic process. A true bimetallic process creates hyper-clean surfaces on the metals before uniting them within an atmosphere of zero oxygen. The work piece then undergoes a measured and precise mechanical pressure while travelling through a sealed zone to prevent oxidation within the bond. The two metals are physically pressed together at precise loads creating a metallurgical bond at an atomic level. In both the KM and TI processes, quality control is built into the system, as every inch of CCA is examined in-line for pinholes, cracks and surface irregularities. Each finished coil is sampled, where a rigorous torsion test is performed to verify the bond. A torsion test will twist the bimetal a few dozen times in one direction, then reverse the direction to torsion a few more dozen times in the other. If the bond is true, under this extreme procedure, the two metals will not separate. The number of processes in the world that can produce industrial grade CCA is only two, and the technology is very closely held.
In short, CCA is a material very well suited for BCBW. In addition to the advantages stated previously, one of the most understated advantages is that the copper and the aluminum bonded by the KM or TI processes cannot be easily separated. According to the Copper Alliance, “Separation of the Two Metals in Copper-clad aluminum: The outer coating of copper-clad aluminum wire cannot be easily stripped away from its aluminum core. At present, the copper and aluminum content in copper-clad aluminum cannot be separated thoroughly by fire refining due to their affinity. Also, there is no developed hydrometallurgical refining technology to completely separate the two metals. CCA cannot be recycled…” 9
The Copper Alliance statement is both true and false. It is true in the sense that the copper and aluminum cannot be easily separated once a true metallurgical bond is accomplished. This is by design, and a testament to legitimate CCA technology. It is also true that one cannot easily find a scrap dealer that will accept CCA, and, in fact, most scrap dealers will reject it if they know that it’s CCA. The aluminum core of CCA can contaminate copper scrap causing problems for re-melters aiming for pure copper at the end of their process. Herein lays an advantage, however. A copper thief will tend not to steal CCA if he’s aware. Not being universally accepted by just any scrap dealer eliminates the demand-side of the theft-incentive equation. Not just any scrap dealer will buy it. But here is where the truth of the Copper Alliance statement ends: CCA scrap is quite recyclable. In fact, it is recycled most every day. Modern producers of CCA, such as Copperweld Bimetallics and Engineered Material Solutions, have developed reliable networks of niche recyclers for their CCA scrap. Niche applications for CCA scrap include re-melt for aluminum-killed steels, weathering steels, certain stainless steels, bronze and even certain aluminum alloys.
Standardization of CCA Began in the Late 1960s: CCA Is Not New
That CCA building wire for branch circuits is a new product is a common misconception. It is nearly ½ century old. The modern form of CCA building wire is a reincarnation of the CCA building wire first introduced and standardized in the early 1970s by the NEC, UL and ASTM. CCA building wire has improved from where it was 45 years ago. Just as the aluminum and copper industries have advanced their quality systems and metallurgical abilities over the last half century, so too has the copper bimetals industry. For example, today’s solid aluminum building wire, although still widely banned for use in residential branch-circuit wiring due to the legitimate fears of galvanic corrosion when installed improperly, uses a specific grade of aluminum designed to have the same thermal coefficient as solid copper, eliminating thermal creep.
Creep was a major cause of the problems during the 1960s with EC grade aluminum building wire, but modern 8000 series aluminum puts this fear to rest, and is quite useful for SEU conductors, for example. Also, the copper industry now offers an oxygen free product that is infinitely cleaner than that of the 1960s and 1970s, allowing for better corrosion resistance, cleaner surfaces, higher ductility and more-efficient electrical properties. Oxygen free copper is the grade currently used to make CCA by the TI and KM processes. Also, the aluminum used today to make CCA for building wire is the modern 8000 series grade, which carries the enhanced thermal characteristics. Both the TI Process and the KM Process utilize the modern aluminum for its product. In short, these are a few poignant examples of how the metals industries have advanced to make safer products.
Regarding updating the standards for CCA to keep pace with the evolution of the materials, work has been constant since the early 1970s regarding the process standard of ASTM, but less so with the NEC and UL. CCA can be found in ASTM as ASTM – B566, which was first published in March 1972. ASTM governs the production of the base bimetal conductor itself, not necessarily the complete insulated conductor. The latest edition of ASTM for CCA was published in 2011. There is a yearly review of the standard by the conductor committee of the ASTM to suggest adjustments to the standard based upon new materials or advances in the process. For decades, CCA wire has been a heavily used material within the coaxial cable industry, thus the reason for ASTM’s continuity in keeping the standard up-to-date.
In the late 1960s and early 1970s, with the global copper shortage worsening, a great deal of work took place at the NEC and UL in standardizing CCA. Copper-clad aluminum (CCA) building wire first appeared in the NEC in 1971 in Article 310 on Conductors. Table 310-14, Allowable Ampacities of Insulated Aluminum and Copper Clad Aluminum Conductors, clearly defines the electrical characteristics of the material. As with solid aluminum, CCA must be sized up for equal ampacity when substituting for copper. For example, a 12 AWG copper conductor is equivalent to a 10 AWG CCA. With the 1976 edition of the NEC, CCA is given a complete definition. “Copper-Clad Aluminum Conductors: Conductors drawn from a copper clad aluminum rod with the copper metallurgically bonded to an aluminum core. The copper forms a minimum of 10 percent of the cross-sectional area of a solid conductor or each strand of a stranded conductor.” Since 1976, the year that CCA building wire for BCBW began to fade from the market due to economic reasons, no significant changes in wording have happened in the code.
The copper-clad aluminum conductor material and physical requirements established by UL in 1971 can be found in the UL building wire standards. UL 44 (Rubber Insulated Wire), UL 83 (Thermoplastic Insulated Wire), and UL 719 (Non-Metallic Sheathed Cable). The years of 1965 – 1976 were quite busy for the electrical systems staff at UL. During this period, not only did UL deal with the hundreds if not thousands of complaints of overheating and/or fires in outlets from EC grade aluminum, but also, it still had to run the business of standardizing new products. As previously mentioned, UL set up the Ad Hoc Committee of Aluminum Terminations in 1972. The mission of the Ad Hoc committee was clear: Educate those affected, and Assist with a remedy. According to Thomas J. D’Agostino, Secretary of the Ad Hoc Committee and UL Senior Project Engineer at the time, he “took hundreds and hundreds of calls from March of 1973 through about 1981 from concerned homeowners throughout the country about solid aluminum wiring.”10 But in addition to the valuable contribution of Mr. D’Agostino to the effort of quelling the chaos, he also kept one eye upon the future. He continued to do the work of UL, a job he began in 1969, in testing promising new products for gaining UL listings. In the late 1960s, Mr. D’Agostino began testing a new conductor product for UL at the behest of a new client, Texas Instruments (TI). The conductor material was CCA. After the lessons learned from solid EC grade aluminum building wire, UL made sure that the CCA product was put through the most extreme testing available at the time for electrical systems connections, namely UL 486C. They took a system-wide approach, meaning they considered the wire as part of an electrical system. If it failed at any point in the system, it would not be granted a listing. According to Mr. D’Agostino, “The test methodology was based on long time heat cycling that was previously performed by the BICC in England who earlier evaluated aluminum wire performance in connection systems. The emphasis for the testing was to determine how copper (sizes 14–12) vs copper-clad conductor (sizes 12–10) performed in wiring devices only intended for use with solid copper building wire.”10 It came as a surprise to the UL staff that the CCA produced by the TI Process performed extremely well. The thermal characteristics and mechanical properties of the wire were night and day from those of EC grade aluminum, and thus worthy of being included in the standard. In April 1971, UL recognized Texas Instrument’s CCA conductor as a suitable alternate conductor material for use in building wire such as NM-B and THHN. As a result, the material and physical requirements for CCA conductor were put into the UL building wire standards. Shortly thereafter, General Cable, A.I.W., and Triangle obtained UL Listings of their insulated building wire with CCA conductor.
Texas Instruments Reaches the BCBW Market First
So as the residential construction industry began to recover from the bite of EC grade aluminum, it still saw little relief from the high cost of copper BCBW. Not only was building wire extremely expensive in 1970, but also, to find to buy it in a pinch was out of the question. Long lead times and allocation became normal. Given this economic environment, TI could not have been better poised to jump into the market now that its CCA was in code. The only obstacle they faced was the fear in the marketplace caused by EC grade aluminum. But in that construction in the suburbs was booming, and solid copper building wire was increasingly difficult to find, a small number of contractors were willing to take a chance on the new product just as long as it was listed by UL, and proven safe. By 1972, TI was fully engaged in the business. To take advantage of established brand names, TI developed commercial relationships with three well-known conductor manufacturers located near their manufacturing facility in Attleboro, MA: General Cable, Collyer Insulated Wire, and American Insulated Wire. Together these companies serviced the residential building wire market from New York to Tennessee with their own brands of CCA NM-B and THHN for BCBW. The business boomed until 1976 when the recession hit. By 1980, as a result of the ensuing global glut of copper cathode, the run of CCA building wire had come to an abrupt and unceremonious end.
Kabelmetal, despite having a head start over TI in the development of its cladding technology, delayed the introduction of CCA into the US market. By 1973, Kabelmetal had finally made a strategic alliance with Copperweld Company, a well-known bimetallics business located in Glassport, PA and famous for inventing Copperweld ground rods. The deal would allow Copperweld to buy a KM line to sell its own brand of CCA wire. Copperweld was interested in diversifying its product portfolio as a result of the success of the Copperweld ground rod campaign; and because they understood in-line cladding processes, Copperweld resolved to make CCA. Through KM’s influence, Copperweld came to realize that CCA could be applied to two emerging markets: residential building wire and coaxial data cables. Copperweld then got busy planning to build a new production facility for CCA in Fayetteville, Tennessee, to service both markets. By the fall of 1975, the plant was ready, and the production team itched to begin production. Unfortunately, while in the midst of its initial trials, the recession of 1976 entered the scene, while copper prices began to fall. These two variables proved deadly for power conductor applications, including BCBW. Luckily for Copperweld, the coaxial cable application for CCA allowed for a one-to-one diameter substitution with solid copper, which meant that it could compete against solid copper even when copper prices dropped to record lows as they did in 1976. This was not the case with CCA for power cables, because the NEC had already established that CCA must be sized up against Cu (copper) for equal ampacity. Copperweld enjoyed fantastic growth in CCA for coaxial cable applications throughout the decades of the 1980s and 1990s, while CCA for power applications hibernated awaiting the rise of copper prices.
Bibliography:
- Working Paper. “How American Homes Vary by the Year They Were Built.” US Census Bureau. June. 2011.
- “History of Copper Clad Aluminum: The Synergy of Aluminum and Copper.” Pete Burd. 2011. Sub-reference: Metal Industry, July – December. 1952
- Personal Interview, Dr. Gerhard Ziemek. July 15, 2016
- “Texas Instruments Historical Document: New Clad Metal Wire Helps Stretch Copper Supply.” Attleboro, MA, October 1966.
- “Repairing Aluminum Wiring,” Publication 516, US Consumer Product Safety Commission
- “Hazard Assessment of Aluminum Electrical Wiring in Residential Use”; Elaine D. Runden, John L. Donaldson, Eugene C. McDowell. Product Systems Analysis Division. National Bureau of Standards. Final Report. December 1974.
- “Aluminum Wiring in Housing.” E-local. Electrician Forum. August 22, 2011
- “The 1970s: 1970 – 1979,” Ellen Parson. June 1, 2001.
- Copper Alliance Website.
- Personal Interview with Thomas J. D’Agostino, Tuesday, June 7th, 2016
Find Us on Socials