For years, manufacturers and users alike have struggled with the selection of ground rod electrode coating alternatives, striving to select the most effective alternative that provides the longest service life. This process is a noble goal, as grounding all too often is looked upon as a step-child and once in the ground that is often the last time any thought is given to effectiveness and reliability of the overall grounding electrode system.
Any number of charts, graphs and allied information available offer suggestions in ground rod coating selection but in the most general of terms. Some national studies have arrived at conclusions using an inconclusive basis for coating selection, leading one to select a product without performing any soil analysis. One does have to be extremely careful of the “agenda” in use of this information when considering this rod coating, for the number of variables involved, in reality, is too pervasive for even the best soils engineer to draw a single conclusion. One of the main reasons for this is that soil conditions often vary widely within a close area to where the soil sample may have been taken, the point of installation. Note that whatever the rod steel core coating is (copper-plating, zinc-coating and stainless in the case of cladding) is there to protect deterioration of the steel core, not for strength or conductive purposes.
Yet how often is soil analysis of the specific site actually employed? The cost is often prohibitive and, instead, general conclusions are made for overall economic purposes. The most common statement is, “We have used this type of rod coating for decades, and it seems to work and we are not changing it under my watch.” While not always the most technically sound way to arrive at an engineering conclusion, it more often than not is the justification and probably is not too far off target. Moreover, a single soil analysis can often result in opposing views based upon the engineer conducting the analysis.
In reality, the cost of time and/or money to do otherwise is usually not acceptable due to a variety of reasons. There are many electrical and non-electrical components buried in the earth, and one component may cause the other to corrode via an anodic/cathodic cell. Years ago we experienced galvanized screw anchor failures due to copper-coated rods and other materials buried nearby, and we saw the solution as isolating the cell by one of several means.
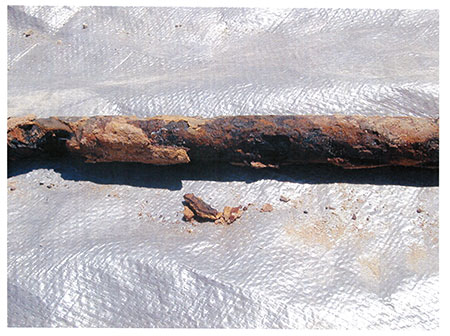
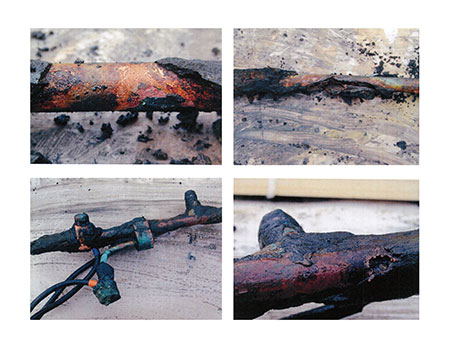
On the other hand, engineers are now looking at buried steel poles as a means of grounding versus a driven ground rod electrode adjacent to the pole. What about life of the uncoated steel pole with the material at grade level often in the ³16 to ¼ inch thickness range? And the story continues to include buried gas pipe lines, to above ground pipe lines to include the Alaskan Pipeline where corrosion conditions are taken very seriously.
The following table provides a general guide for the selection of zinc-coated steel, copper-coated steel, or solid 304-stainless-steel ground rod electrodes in soil conditions identified by the ground rod resistance measured during site testing. This guide is NOT intended to be conclusive, but a fundamental guideline often used in rod type coating selection.
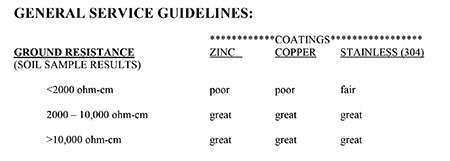
Ground resistance is only one measurement criteria to be used in the selection of a coating, but it is generally considered one of the prime factors. Soil pH is another critical factor to be considered, as are several other parameters mentioned below in the comment section. These two factors, combined, have been used as an economic, yet technically supported, basis for rod coating selection. This basis is NOT the most thorough technique to follow, but it is supported by many engineers as to an economical approach to addressing what could be a costly effort.
From the the general service guidelines chart, one might conclude that when faced with low resistance soil conditions most rod coatings are subject to more aggressive unfavorable conditions. On the other hand, under higher ground resistance conditions one might conclude that most coating types are acceptable. So let’s consider adding another parameter, soil pH.
The most comprehensive selection method to assure the highest degree of confidence in system reliability is to enlist a soils engineer and accurately identify soil characteristics at the exact location where each grounding electrode(s) is to be installed. Anything less is highly subjective and based upon incomplete technical support in the critical area of electrical service to residential, commercial, and industrial or power utility installations. How many installations are ever re-inspected unless faced with an upgrade where then current electrical codes must often be complied with? Moreover, what about changes to the site at a later date including chemical contamination, other buried installed components, and so forth?
SOIL
Soil pH at or below 4 is particularly harmful to any of the above alternatives. The higher the pH number, the more likely system life reliability will be enhanced, whereas the lower the number, the more critical the soil conditions may be on any ground rod electrode.
pH…
<4 trends poorer (acidic)
4 threshold (neutral)
>4 trends better (basic)
From this information, one might conclude that the makeup of the soil from a chemical perspective is very critical, which of course it is. However, using resistivity and pH together will result in what is used in most cases without having the complete site analysis of soil by a qualified firm.
Well-aerated soils with a neutral or slightly basic pH are likely to cause only limited corrosion of a ground rod electrode.
While the above information based upon ground soil resistivity and pH alone does provide a basic guideline; however, other factors that should be considered in a thorough evaluation include
- Soil resistivity
- Soil pH
- Moisture and drainage
- Aeration
- Stray current (ac and/or dc)
- Permeability
- Soil bacteria and/or acids
- Temperature
- Chlorides
- Sulfates
- Dissimilar metals buried nearby
- Soil make-up characteristics (rock, gravel, etcwhere the rod electrode is being driven inflicting potential damage to the coating resulting in premature degradation of electrode life due to surface degradation
- Certain soil enhancement materials
- Degradation of rod coating to rod steel core
- Common sense!
HISTORY
Copper-coated, zinc-coated or solid 304 stainless-steel ground rod electrodes will generally provide a service life of 30–40 years (or more) in certain soil conditions, but not all! This statement is further supported by the history of RUS who have used hot-dip galvanized rods since the early 1930s; Investor Owned Utilities have used copper-coated rods for decades; and industrial facilities who have used stainless-steel ground rods for years, each with great success.
Salts are particularly adverse to zinc coatings, and as a result, galvanized ground rods should not be considered when near coastal areas where salts are prevalent. This situation is where common sense comes to play. Some conditions become quite obvious.
Hardness of the coating should also be considered as a factor in rod selection, as should the electromotive-series-of-metals should the coating ever be compromised. By nature, copper-coated rods are more inclined to be vulnerable to surface coating damage during installation, whereas hot-dip galvanized (not electro-plated) coatings are extremely hard and resist most coating damage resulting from being driven into the ground, similar to solid stainless-steel.
While no one method of rod selection may be considered “better” based upon continually changing soil conditions (moisture, freezing, etc.) this information is intended to offer suggestions on the most effective coating selection based upon what information may be available to the individual responsible for this selection.
Most errors in establishment and interpretation of corrosion protection for copper-coated, zinc-coated or solid stainless steel ground rod electrodes include one or more of the following issues:
- Basic assumptions made about coating protection
- Mechanics of corrosion characteristics
- Assumptions used to predict ground rod service life.
CONCLUSION
So what does all this mean for those who are responsible for a system which will provide equipment protection, system reliability and personal safety? Maybe a headache would be a good place to start. However, every day decisions must be made that have consequences of one sort or another. Often the decision is to remain with what has worked in the past and not make any changes for fear of failure.
But to look forward and incorporate the technical information available today does allow decisions to be made with a degree of confidence. Using soil resistivity and pH does allow a reasonable conclusion to be made. But for one to say that one type of coating is much better than another is pure minutia. And do not overlook the likelihood of coating damage during the driving process in rocky soil as previously mentioned which opens up a completely new concern. That is, in a galvanized ground rod the zinc-coating then “sacrifices” to protect an exposed steel core; whereas in the copper-coated ground rod, the steel core “sacrifices” to protect the copper coating! Think about this!
If you are able find a ground rod manufacturer who offers a 30–40 year “life guarantee in most soil conditions” without conducting due-diligence, including all factors involved with corrosion of zinc, steel and/or copper at a particular site, you should be the first one to get that warranty in writing! If you disagree with this, ask an investor-owned utility firm in the domestic US if they have been offered such a warranty, as they would be the entity most interested in receiving such a guarantee due simply to the number of copper-coated and/or zinc-coated ground rod electrodes installed!
Do not be led by sales or marketing influences when the number of variables that need to be considered for a technically sound installation is too pervasive for any one chart or opinion, this one included! A sound engineering soil analysis is the only way to make a technically sound analysis and decision. Anything less is technically unsound and unsubstantiated!
Find Us on Socials